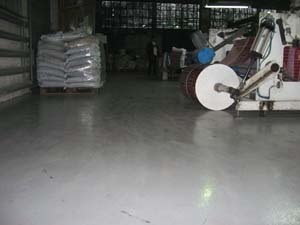
Бетонні покриття набули найбільшого поширення через їх відносно низькій вартості, так як виготовлення зносостійкого покриття об'єднується в одному технологічному циклі з пристроєм несучої монолітної плити.
Конструкція бетонної плити залежить від безлічі факторів - характеристик підстави, навантажень на підлогу, розташування стелажів, типу армування і т.д.
При будівництві нових складів підставою для підлоги служить ущільнений пісок, рідше залізобетонна монолітна плита. При реконструкції будівель підставу часто є старі підлоги з бетонної плитки, монолітного бетону та ін.
На стадії проектування статі необхідно знати основні характеристики підстави, тому його спеціалізоване обстеження обов'язково. При новому будівництві, коли підставою для бетонної підлоги служить ущільнений пісок, замовник повинен контролювати ступінь його ущільнення, не покладаючись на дані підрядника, а залучаючи незалежну спеціалізовану лабораторію, що дозволить виключити надалі просадки статі і утворення тріщин.
У чистому вигляді бетонні покриття для виготовлення підлог складів практично не застосовуються через їх низьку зносостійкості і значного запилення. Для додання бетонній підлозі високих експлуатаційних характеристик використовують технологічні прийоми поверхневого (1 - 3 мм) зміцнення за допомогою рідких або сухих складів на стадії влаштування бетонної підлоги.
Використовуються також спеціальні високоміцні цементнополімерние склади з товщиною шару 5 - 12 мм, які укладають по незатверділому або «старому» бетону. Найбільш широко поширена технологія зміцнення бетонної підлоги сухими сумішами.
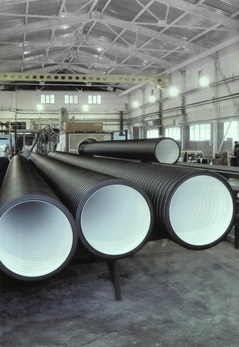
Технологічні операції при влаштуванні бетонного покриття з верхнім зміцненим шаром:
Нівелювання поверхні підстави.
Зйомкою визначається найбільш висока відмітка підстави, після чого уточнюється товщина бетонної плити, яка не повинна бути менше проектної.
Відповідно до рекомендацій ACI302.IR-89 Американського Інституту бетону мінімальна товщина бетонної плити, що влаштовується по монолітному бетонною основою - 100 мм. У разі, якщо бетонне покриття влаштовується з ущільнення грунту, то його товщина складає, як правило, 150 - 250 мм, в залежності від навантажень на підлогу і застосовуваного армування. Слід зазначити, що пристрій бетонної підлоги товщиною 50 - 100 мм, незважаючи на економію коштів за рахунок зменшення витрати бетону, невиправдано, тому що в переважній більшості випадків призводить до значного утворення тріщин і надалі - до руйнування покриття.
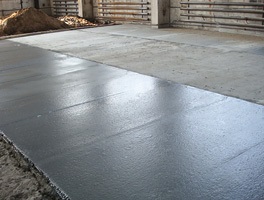
Розбивка площі підлоги на карти (захватки)
У разі, якщо в складі будуть встановлюватися стелажі, краю захваток повинні по можливості розташовуватися між стелажами. Це особливо важливо для висотного складування, оскільки пред'являються підвищені вимоги до рівності статей, а досвід влаштування бетонних покриттів свідчить про те, що найбільша кількість нерівностей виникає по краях захваток. Ширина захваток для «Надплоскі» статей не повинна перевищувати 4 м (в окремих випадках 6 м). Довжина захваток визначається в залежності від денної продуктивності укладання з тим, щоб уникнути зайвих, так званих, «холодних» або «будівельних» швів, що виникають через перерви в бетонуванні.
Як напрямні використовуються спеціальні бетонні вироби, або металеві форми, рідше квадратний металевий порожнистий профіль або швелер. Від якості напрямних безпосередньо залежить рівність статей, тому для «Надплоскі» підлог повинні використовуватися тільки спеціальні форми з підвищеною жорсткістю і рівністю верхньої кромки. Для установки напрямних краще застосовувати оптичні нівеліри, а лазерні використовувати для вибіркового контролю правильності установки.
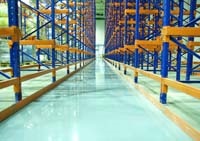
У США і країнах Європи останні два десятиліття широко поширена технологія влаштування бетонної підлоги за допомогою автоматичних бетоноукладочних комплексів, які представляють собою пересувні установки з телескопічним механізмом, на якому закріплено розрівнюють пристрій, оснащений вібраторами (наприклад, компанія Somero, США). Бетоноукладочной комплекси забезпечують автоматичний контроль рівня укладається бетонної суміші - для цього застосовується стаціонарний лазерний випромінювач, що встановлюється в зоні прямої видимості і приймачі, закріплені на самому механізмі. Виконавчий гідравлічний механізм кілька разів на секунду регулює висоту розрівнює пристрою, що дозволяє отримати прийнятну рівність бетонного покриття.
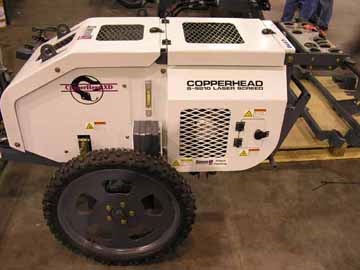
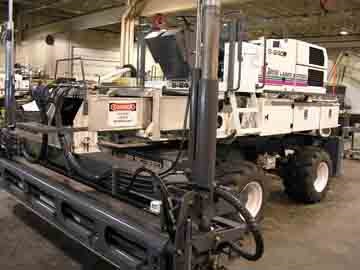
При використанні традиційного армування за допомогою арматурних сіток дуже важливий контроль за їх розташуванням щодо заснування та заданої позначки статі. Як показує досвід вітчизняного та зарубіжного будівництва, від правильності установки арматури залежить тріщиностійкість, а, отже, і довговічність статі.
Особливо це важливо в разі виготовлення бетонного покриття невеликої товщини, армованого однієї сіткою - неправильно покладена сітка (наприклад, укладена безпосередньо на підставу) не тільки не запобігає утворення тріщин, а й часто є його джерелом. Тому при такій конструкції підлоги бажано використовувати комбіноване армування (крім установки арматурної сітки вводити до складу бетону металеву фібру).
Дисперсне армування бетону металевої фіброю (витрата 25 - 40 кг. На куб.м. бетону) дозволяє відмовитися від пристрою традиційних арматурних сіток, різко знизити трудовитрати, використовувати високопродуктивні бетоноукладочной комплекси, проте, пред'являє надзвичайно жорсткі вимоги до якості ущільнення грунтової основи і підбору складу бетонної суміші. На жаль, в даний час вітчизняна нормативна база застосування металевої фібри для влаштування підлог не розвинена, відсутні стандартизовані практичні рекомендації з приготування складів бетонних сумішей.
Осадові шви відокремлюють колони і стіни будівлі від покриття підлоги. Їх влаштовують шляхом установки пенополіетіленовие стрічки товщиною 3 - 5 мм навколо колон і вздовж зовнішніх і внутрішніх стін будівлі.
Дана операція дозволяє запобігти утворенню тріщин в бетонній підлозі через осад стін і колон, викликаних як просадками грунтової основи, так і зміною навантажень на конструкцію будівлі.
Доставка бетонної суміші на будмайданчик і розподіл її по захваткам і ущільнення за допомогою глибинних вібраторів і віброрейок.
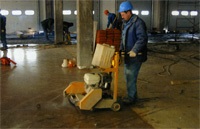
Цей технологічний переділ - організаційно найбільш складний етап у влаштуванні бетонних покриттів підлог. Перерви в доставці бетону навіть на 30 - 40 хв (особливо в літню пору), неоднорідний склад бетону, різна пластичність суміші приводять до необоротного погіршення якості бетонної підлоги - в першу чергу, його рівності і довговічності.
Виробник підлог в даному випадку повністю залежить від обов'язковості та оперативності постачальника товарного бетону, тому вибір бетонозмішувального вузла - найбільш важливий етап планування всієї роботи із влаштування підлог.
Бетонна суміш розподіляється по захваткам і ущільнюється за допомогою віброрейок і глибинних вібраторів. Особливу увагу необхідно приділяти якості ущільнення бетону уздовж напрямних, стін і навколо колон. При влаштуванні «Надплоскі» підлог використовуються спеціальні високоякісні віброрейки, причому їх геометрія (прогин) повинен перевірятися і при необхідності регулюватися після кожної робочої зміни.
Перевірятися повинна і пластичність поставляється бетону. Виробник повинен вимірювати осадку конуса бетонної суміші з кожного автобетонозмішувача ( «міксера») і вимагати від постачальника коригування рецептури. Зміна опади конуса більш ніж на 4 см в партії бетону, що поставляється в одну зміну, може призвести до складнощів при виконанні робіт і знизити якість готової підлоги.
Вирівнювання ущільненої бетонної суміші за допомогою ручних рейок.
При традиційній технології пристрою бетонних підлог (використання напрямних і віброрейок) рівність статей в значній мірі визначається професіоналізмом укладальників бетону. Використання високоякісних напрямних, регульованих віброрейок не є запорукою влаштування покриттів із заданою рівністю.
На жаль, без великої кількості ручної праці отримати якісні і рівні підлоги не представляється можливим. При виготовленні «Надплоскі» підлог для вузькопрохідних штабелеров 20 - 30% всіх трудовитрат припадає на ручне вирівнювання бетонної підлоги.
Використання бетоноукладочних комплексів дозволяє знизити частку трудовитрат з розподілу і ущільнення бетонної суміші, але також не дозволяє відмовитися від ручної праці по вирівнюванню свежеуложенного бетону.
Вирівнювання виробляють за допомогою алюмінієвих і дерев'яних рейок прямокутного перерізу, спеціальних загладжуючих профілів на телескопічних ручках з поворотними шарнірами.
Витримка свежеуложенного бетону.
Час витримки залежить від температури підстави, вологості і температури навколишнього повітря, активності цементу, використаного при приготуванні бетонної суміші. Як правило, бетон до наступних операцій по його обробці витримується протягом 3 - 5 годин. Часто застосовувана технологія вакуумирования бетонної суміші скорочує час витримки до 1 - 2 годин, що спрощує технологію.
Відповідно до рекомендацій Американського інституту бетону (ACI) і більшості фірм-виробників зміцнюючих складів подальшу обробку бетону можна починати тільки після того, як глибина відбитка від взуття на бетоні буде менше 4 - 5 мм. Настільки неформалізована рекомендація свідчить, що технологія бетонної підлоги, і як наслідок - їх якість, в значній мірі залежить від накопиченого досвіду і професіоналізму укладальників.
У разі, якщо на будмайданчик бетонна суміш поставляється неоднорідної якості, витримка різних ділянок укладеного бетону буде різною за часом, тому на даному етапі необхідно уважно стежити за термінами схоплювання бетону.
Нанесення 2/3 загальної кількості упрочняющей композиції на свіжоукладений бетон
Суха упрочняющая суміш наноситься на твердне бетон вручну, або за допомогою спеціальних розподільних візків. Останній метод найкращий, так як дозволяє домогтися контрольованого і рівномірного розподілу зміцнюючої суміші.
Для виготовлення зміцненого бетону використовуються сухі суміші, що відрізняються між собою типом зносостійкого наповнювача. Найбільш поширені -фракціонірованний кварц, корунд, карбід кремнію і метал. Крім наповнювача до складу зміцнюючих сумішей входить портландцемент, водоудерживающие, пластифікуючі і інші полімерні добавки.
Від інтенсивності зносу, якому піддається підлогу, залежить і тип зміцнюючого складу. У складських приміщеннях, де використовуються навантажувачі та візки з монолітними поліуретановими колесами, застосовують зміцнення підлог на кварцовому і корундовому наповнювачі. У приміщеннях, де можливий рух візків на металевих колесах, - тільки металлонаполненние суміші. Для «Надплоскі» підлог деякі фірми випускають зміцнюючі склади, що відрізняються підвищеною пластичністю і збільшеним часом життєздатності і оброблюваності.
Загальний витрата кварцового і корундового упрочнителя 4 - 7 кг на кв.м. металлонаполненного - 8 - 12 кг. на кв.м.
Випускаються і широко використовуються кольорові зміцнюючі склади, проте колір готового покриття через неоднорідність складу бетонної суміші, її товщини, нанесення зміцнюючого складу ніколи не буває рівномірним. Вирівнювання кольору підлоги відбувається протягом 1 - 3 місяців в залежності від товщини бетону і умов його твердіння. Це ж відноситься і до «плямистості» упрочнителя «натурального бетонного» кольору.
Нанесений на бетон сухий упрочнитель загладжують за допомогою ручних рейок, що представляють собою алюмінієвий профіль перетином 50 х 100 або 50 х 150 мм, до якого прикріплена ручка на поворотному шарнірі. Використання ручної рейки дозволяє більш рівномірно розподілити зміцнюючу суміш по поверхні бетону і контролювати її насичення вологою, що надходить з бетону.
Для механізованої затірки використовують самохідні і ручні затирочні машини. Затірку починають одягненими на машини дисками (діаметр 60, 90 або 120 см) при мінімальних обертах. Затірку припиняють після одного - двох проходів по поверхні.
Нанесення залишилася 1/3 частини упрочнителя і остаточна затирка.
Після нанесення решти зміцнюючого складу на поверхню бетону затірку продовжують за допомогою дисків, а в міру твердіння бетону диски з затирочних машин знімають і продовжують обробляти поверхню лопатями. При цьому поступово збільшують кут нахилу лопатей і швидкість обертання роторів.
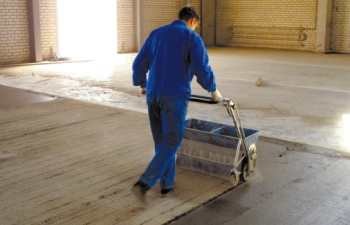
Нанесення захисного Водоутримуюча лаку.
Оскільки бетон, який використовують для підлог, виготовляють на основі портландцементу, він характеризується усадкою при твердінні. Наслідком усадки є тріщини - як поверхневі, так і структурні (на всю глибину бетонного шару). Поверхневі усадочні тріщини згодом можуть розкриватися і привести до лущення поверхні і руйнування підлоги. Щоб запобігти утворення тріщин, необхідно різко знизити випаровування вологи з бетонної поверхні, особливо в ранні стадії твердіння. Для цього використовують спеціальні водоудерживающие лаки - розчини акрилових сополімерів в органічних розчинниках або воді. При рекомендованому витраті лаку 150 - 200 м на кв.м. товщина плівки на бетоні становить 0,07 - 0,12 мм. Цього цілком достатньо, щоб сповільнити випаровування вологи з бетонної плити і запобігти утворення тріщин.
Критичним в даній операції є час нанесення Водоутримуюча лаку - інтервал між завершенням затирання і укладанні лаку повинен бути мінімальним і обчислюватися хвилинами.
При експлуатації підлог водоутримуючий лак стирається.
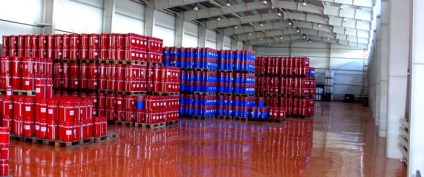
Нарізка проводиться за допомогою спеціальних машин з алмазними або корундовими дисками на глибину 1/3 товщини бетонного покриття, але не менше ніж 2,5 см.
Нарізка швів проводиться не пізніше ніж через 6 - 8 годин після остаточної затірки зміцненого шару, що дозволяє уникнути появи усадочних тріщин.
Крок між швами залежить, в основному, від товщини бетону. За рекомендаціями ACI - крок між швами не повинен перевищувати 30 - 40 товщин бетонної плити. Розташування швів визначається в залежності від місця розташування і кроку колон і конфігурації складу.
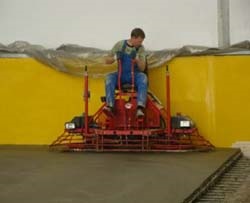
Заповнення усадочних і деформаційних швів.
Оскільки усадка бетону протікає протягом досить тривалого періоду (інтенсивна - перші три місяці), то заповнення швів еластомірними герметиками необхідно проводити якомога пізніше. Для бетонних підлог товщиною (100 - 150 мм) заповнення швів можна починати не раніше 1,5 - 2 місяців після їх влаштування. Для бетонних підлог товщиною 200 - 300 мм цей термін не повинен бути менше 3 місяців. Такі вимоги ускладнюють організацію робіт, так як операції з герметизації швів необхідно виконувати в умовах діючого складу. З іншого боку, заповнення швів раніше зазначеного терміну, як правило, призводить до порушення адгезії між герметиком і краями шва, що неминуче призводить до ремонту швів в умовах діючого складу.
Як показує практика, найбільш ефективним є використання жорстких поліуретанових або епоксидних герметиків з високою твердістю (понад 90 у.о. за Шор А) і невисокою еластичністю (відносне подовження до 150%). Найбільш поширений метод заповнення швів - укладання пенополіетіленовие шнура і заповнення герметиком на глибину 5 - 7 мм не завжди забезпечує довговічність статі. Часто краю швів під впливом інтенсивного руху сколюються, що призводить до подальшого руйнування пошкоджених ділянок. У зарубіжній літературі є рекомендації не використовувати пенополіетіленовие шнур взагалі, а заповнювати герметиком шов на всю глибину. Таким чином, завдання отримати безпильний і довговічний підлогу вимагає від виконавця як значних зусиль по організації виробництва, так і високого професіоналізму інженерів і робітників. З іншого боку, на якість робіт впливає безліч факторів, що не залежать безпосередньо від установника підлог. Це - стабільна температура в приміщенні не нижче 10 ° С, відсутність протягів, протікання води, суміжних будівельних організацій в зоні робіт, наявність ефективного освітлення майданчика.
Замовник і генпідрядник повинні з розумінням ставитися до вимог установника підлог і заздалегідь планувати час його роботи.