Оснащення зубів пластинами твердого сплаву - найефективніший засіб підвищення стійкості дереворізального інструменту. Інструмент з твердосплавними пластинами особливо незамінний при обробці ДСтП, ДВП і інших клеєних матеріалів.
Пластини твердого сплаву кріплять на зубах ріжучого інструменту ме
тодом пайки. На кафедрі верстатів та інструментів УГЛТУ цей спосіб практично реалізований А. І. Шевченко.
Якість паяних з'єднання залежить від правильності вибору мате- ріалу для корпусу інструменту, підготовки корпусу і пластин твердого сплаву до Паяні, вибору припоїв і флюсу, методу і режиму нагріву.
Пайка - процес створення нероз'ємного з'єднання різних ма-
ріалів в твердому стані шляхом заповнення капілярного зазору між-
ду ними проміжним металом або сплавом в рідкому стані, на-
Матеріалкорпусаінструмента. За ГОСТ 9769-79 "Пили диско ші з твердосплавними пластинами для обробки деревних матеріалів. Технічні умови" корпус пилки рекомендується робити зі сталі марки
50ХФА. Це більш пластична сталь, ніж сталь марки 9ХФ. Вона не закалі-
ється на повітрі після пайки латунними припоями.
При організації виробництва пив з твердосплавними пластинами на деревообробному підприємстві допускається для корпуса пилки ис
використовувати сталь марки 9ХФ. Ця сталь має температуру гарту 840 ° С.
Після Пайк і п р ип про ям і, що мають температуру плавлення я вище 840 ° С.
про н а гартується н а повітрі. Тому п про сл е Пайк і зуби пив и піддають
від пу ску п ри температурі 450. 500 ° С. так як загартовані зуби занадто
Корпуси фрез і ножів виготовляють з конструкційної сталі марки 45.
Твердосплавниепластіни. Найбільш часто дереворізальний инст- румент оснащують твердосплавними пластинами з карбідів вольфраму на кобальтової зв'язці марок ВК8, ВК15.
Форма і розміри пластин твердого сплаву стандартизовані ГОСТ 13833-77 і 13834-77. Наприклад, пластини О1Д (ширина 5,5 мм, довжина 10 мм, товщина 3 мм) застосовуються для зубів поздовжнього пиляння, а пластини О2Д - для зубів поперечного пиляння; пластини О5Д (ширина 15 мм, довжина 110 мм, товщина 3 мм) - для ножів і фрез.
Припій. Обов'язковою властивістю припою, що дозволяє отримувати міцне паяні з'єднання, є його здатність змочувати основний метал. При змочуванні атоми припою вступають в енергетичне взаємодію з поверхневими атомами основного металу. При цьому атоми припою і основного металу зближуються на таку відстань, на якому знаходяться атоми в кристалічній решітці металу.
Змочування залежить від властивостей припою і основного металу. його ха-
рактер і з у ют величин ой крайового кут а змочування θ. При хорошому смачі-
вані і θ → 0, п ри пл охом змочуванні θ> 90 ° (р і с. 13).
Рекомендовані для паяння та п р ип ої (ГО С Т 231377-78) наведені в
Подготовкакпайке. Підготовка до пайки пластин включає ви-
ня наступних операцій.
Припої у вигляді фольги або стрічки поділяють на смужки шириною
1. 1,5 мм і знежирюють в бензині або іншому розчиннику. Для пайки можна використовувати припій у вигляді дроту діаметром 0,3. 0,4 мм.
Опорниеповерхності пластінтвердогосплава очищають від ока- лин і окисної плівки. Для цього їх шліфують по задній поверхні на пласко верстаті з магнітним столом алмазним шліфоваль- ним кругом. Перед паянням прошліфовані пластини знежирюють бен- Зіном.
На корпусі ріжучого інструменту формують зуби з кутом заост-
ре ні я н е менше 50 °. При менших кута х загострення жорсткість зуба стан про -
вітся недостатньою, і п ри роботі в пластин е твердого сплаву можуть обра-
На кожному зубі паз під пластину формують методом фрезерування або шліфування абразивним кругом паз. Глибина паза 1. 2 мм. довжина паза менше довжини пластини на 1,0. 1,5 мм і становить близько 2/3 висоти зу- ба.
Для ножів глибина паза на 0,3. 0,5 мм менше товщини пластини.
Шорсткість поверхні паза Ra = 6,3. 3,2 мкм, поверхня повинна бути прямолінійна і знежирена.
Подготовкакомпенсаторов проводиться з тонкої мідної або сталевої фольги товщиною 0,2. 0,3 мм.
Коефіцієнти лінійного розширення твердих сплавів приблизно в два рази менше, ніж для сталі. Тому в паяних шві утворюються внут- ренніе напруги: стискають з боку твердосплавних пластини і розтягують з боку корпусу. З метою запобігання утворенню тріщин у шві між пластиною і корпусом поміщають компенсатор.
Пайкатвердосплавнихпластін назубья пив. Для пайки корпус пилки з підготовленими зубами кріплять у фланцях нагрівальної уста- новки (рис. 14). Фланці підключені до одного з електродів трансформа- тора (часто використовують зварювальні трансформатори).
Мал. 14. Схема електроконтактні пайки
Пластину твердого сплаву кла- дуть на рухливий мідний електрод, заводять в паз і притискають до корпусу зуба із зусиллям 5. 50 Н. Між зубом і пластиною можна покласти компен-
Сатор (іноді паяють без нього). На місце пайки насипають флюс і включають трансформатор. Зону пайки нагрівають, наприклад, до жовтого кольору побе- жалості. Флюс плавиться і розтікається. У зону пайки вручну підводять смужку припою, який плавиться і розтікається на поверхні паза. Трансформатор відключають, і зуб остигає на повітрі. Остиглий припій повинен утворити жолобник по всьому периметру з'єднання.
Після пайки всіх зубів виробляють їх відпустку при температурі
Поряд з механізмами, які тривалий час працюють при постійній потужності, у багатьох механізмів в процесі тривалої роботи навантаження на валу, будучи функцією часу, змінюється в досить широких межах. Такий режим навантаження на валу визначається характером роботи, що виконується виконавчим механізмом в ході відповідного технологічного процесу.
Якщо при тривалій незмінному навантаженні методика вибору електродвигуна виявляється досить простий і зводиться до вибору потужності по каталогу, то при тривалій змінному навантаженні завдання вибору потужності електродвигуна істотно ускладнюється, оскільки зі зміною навантаження виробничого механізму змінюється і момент навантаження на валу електродвигуна. Подібний характер навантаження буде приводити до зміни величини струму, споживаного двигуном з мережі, і, отже, до зміни гріють втрат в ньому, що, в свою чергу, призведе до зміни його нагрівання в часі. З цього випливає, що при тривалій змінному навантаженні температура електродвигуна в процесі роботи безупинно змінюється.
При роботі електродвигуна зі змінним навантаженням в тривалому режимі навантаження в часі в загальному випадку може змінюватися за довільним законом. Зміна навантаження на валу характеризує зміну моменту, а отже, потужності або струму, споживаних електродвигуном з мережі.
При змінному навантаженні температура електродвигуна безперервно змінюється внаслідок зміни потужності і струму. У цьому випадку визначення потужності електродвигуна для заданих умов роботи може бути вироблено за методом середніх втрат. При застосуванні цього методу передбачається, що при заданому графіку навантаження кількість тепла, що виділяється в електродвигуні при роботі, а отже, і його температура при середніх втратах, будуть такими ж, як і при роботі електродвигуна з номінальним навантаженням. У більшості практичних випадків метод середніх втрат дає результати з достатньою для практики точністю, хоча і не враховує максимальної температури електродвигуна в процесі роботи при змінному графіку навантаження. Однак метод середніх втрат пов'язаний з досить трудомісткими розрахунками.
Точне встановлення потужності електродвигуна при роботі в заданих умовах представляє значні труднощі. Тому при практичних розрахунках використовуються інші, більш прості і зручні, хоча і дещо менш точні методи розрахунку.
До них відноситься метод еквівалентного струму, метод еквівалентного моменту і метод еквівалентної потужності.
Вибір електродвигуна за методом еквівалентного струму при змінному навантаженні заснований на заміні дійсного, що змінюється за величиною в часі значення струму I, споживаного двигуном, еквівалентним струмом Iе, при якому втрати в електродвигуні при тривалій незмінному навантаженні відповідають середнім втратам при змінному режимі роботи. Метод еквівалентного струму дає можливість вибрати електродвигун при наявності графіка зміни струму в часі. При виборі потужності електродвигуна за методом середньоквадратичного (еквівалентного) струму необхідно враховувати умови охолодження його в процесі роботи, що особливо важливо для двигунів з самовентиляцією. Це пояснюється тим, що при пуску і гальмуванні внаслідок зміни частоти обертання змінюються і умови охолодження електродвигуна, так як під час пуску і при зупинці його постійна часу нагріву матиме інше (менше) значення, ніж при нормальній роботі.
Розглянутий метод не застосуємо у випадках, коли необхідно враховувати зміну втрат в сталі і втрат на тертя в процесі роботи, а також при значному коливанні напруги і швидкості обертання двигуна. Методом еквівалентного струму не слід користуватися також при наявності значної зміни активного опору обмоток в процесі роботи електродвигуна (асинхронні електродвигуни з глибоким пазом і з подвійною кліткою в пускових і гальмівних режимах). У цих випадках слід застосовувати методи, засновані на безпосередньому визначенні втрат в електродвигуні.
При вирішенні завдань з вибору потужності електродвигуна на практиці частіше доводиться оперувати з навантажувальні моментами. У цьому випадку зручно використовувати метод еквівалентного моменту, який випливає безпосередньо з методу еквівалентного струму, якщо існує пропорційна залежність між струмом і моментом електродвигуна.
Як і в разі вибору електродвигуна за методом еквівалентного струму, обраний таким чином електродвигун перевіряється по допустимої перевантаження. Метод еквівалентного моменту не рекомендується застосовувати для тих же випадків, що і метод еквівалентного струму. Він непридатний для двигунів постійного струму послідовного збудження, асинхронних короткозамкнених двигунів при роботі в гальмівних і пускових режимах, а також в інших випадках, коли магнітний потік електродвигуна в процесі роботи не залишається постійним, так як при цьому між струмом і моментом електродвигуна порушується пропорційна залежність.
У багатьох випадках більш зручним при виборі потужності електродвигуна виявляється метод еквівалентної потужності, який передбачає в процесі роботи сталість ККД, а для двигунів змінного струму та коефіцієнта потужності. Цей метод особливо зручний при виборі потужності електродвигуна при наявності навантажувальної діаграми виконавчого механізму по потужності.
Якщо електродвигун не задовольняє умовам пуску або перевантаження, то його потужність у всіх випадках повинна бути відповідно збільшена. Метод еквівалентної потужності має ті ж обмеження, що і метод середньоквадратичного моменту.
Він непридатний при виборі електродвигунів, у яких швидкість в процесі роботи значно змінюється, а також при частих пусках і зупинках двигуна.
4. Правила проектування литих деталей
Розглянемо основні правила конструювання литих деталей.
При конструюванні литих деталей насамперед потрібно забезпечити необхідну розрахункову міцність при мінімальній масі виливка. Крім того, слід прагнути до спрощення конфігурації виливки. Чим простіше конфігурація виливки, тим менше трудомісткість і вартість виготовлення оснастки і форми, а отже, і виливки. Ускладнення конфігурації виливки, як правило, призводить до ускладнення її усадки
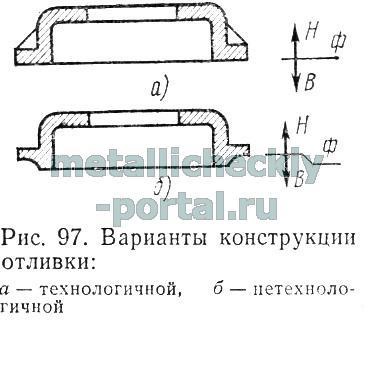
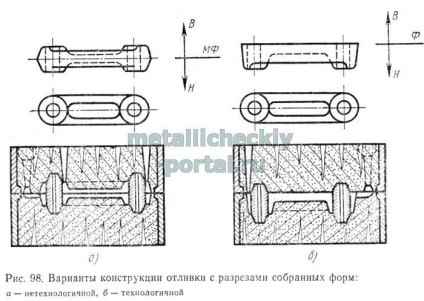
5. Нормування при многостаночной роботі.
Багатоверстатне обслуговування є однією з форм кооперації праці. Можливість такої роботи обумовлена збігом часу виконання ручних прийомів на одному верстаті (машині) з часом машинної роботи на інших верстатах (машинах). Причому можливості багатоверстатногообслуговування можуть бути розширені за рахунок підвищення технічної оснащеності виробництва, комплексної механізації і автоматизації, перепланування обладнання з метою скорочення шляху переміщення робочого від одного верстата до іншого і інших організаційно-технічних заходів.
На практиці зустрічаються різні види багатоверстатногообслуговування, і чим більше робочих опановують суміжними професіями, тим ширше можливості для багатоверстатного обслуговування. Тому ефективність многостаночной роботи значно вище, якщо вона поєднується з суміщенням професій. Найбільш сприятливі умови для суміщення професій створюються в умовах бригадної організації праці.
Головною умовою організації багатоверстатного обслуговування є наявність машино-вільного часу на кожному з верстатів, рівного сумі ручного часу роботи на всіх інших, що обслуговуються одним робочим верстатах.