Коротко описана концепція, на основі якої побудовані практичні підходи TPS і TOC і вказані умови для вибору інструменту управління виробництвом
Передісторія
Керівникам проектів, бізнес-аналітикам і всім, хто цікавиться організацією роботи виробництва.
Приклади ефективного управління виробництвом (дуже коротко)
Стабільність завантаження устаткування замовленнями
Обробка становить 10% від часу знаходження у виробництві
Сама концепція організації ефективного виробництва була розроблена Генрі Фордом на початку 20 століття. Суть концепції полягала в тому, щоб організувати безперервний виробничий потік і усунути на всьому шляху збірки обмеження, які б негативно впливали на час створення автомобіля. Форд впровадив механізм балансування потоку - обмежив площі між ділянками для складування незавершеного виробництва. Цей крок дозволив методом спостереження швидко виявити перевиробництво деталей і виникають проблеми в потоці. Для руху автомобіля від початку збирання до виходу з заводу використовували конвеєр (який, виявляється, придумав не Форд - ідею застосування конвеєра у боєнь запропонував перейняти директор з виробництва Форда). Найцікавіше, що спочатку конвеєр був механічним і робочі вручну переміщали автомобілі від дільниці до дільниці. Уже згодом, конвеєр зробили механізованим, і з'єднали їм все ділянки. За рахунок поділу етапів зборки на 84 операції, вдалося скоротити час складання автомобіля, що складається з 5 тис. Деталей, з 14 годин до 1,5 години. А механізм управління потоком дозволив домогтися фантастичною (до сих пір неперевершеною в масовому виробництві автомобілів) швидкості - через 81 годину після видобутку руди, автомобіль був готовий до відправки покупцеві. В результаті ефективного управління потоком і зниження операційних витрат, ціна автомобіля Форд-Т впала за три роки з 950 до 360 доларів.
У компанії Тойота зайнялися виробництвом автомобілів в середині 20 століття. Тайіті Воно уважно ознайомився з успішним досвідом Генрі Форда. Після того, як Воно почув про ідею роботи супермаркетів в Америці, прийшло рішення яким чином має бути організовано виробництво автомобілів в Тойота. Відмінність виробничої середовища Форда від Тойота полягало в тому, що Форд масово виробляв одну модель автомобіля, а в Тойота одночасно проводилися кілька моделей невеликими кількостями. Для управління потоком, довелося відмовитися від ідеї Форда по обмеженню простору між ділянками і перейти до ідеї обмеження кількості деталей між ділянками. В результаті, між двома ділянками виробництва, розташовувалися контейнери з деталями для кожної моделі автомобіля. Практичним механізмом обмеження виробленого кількості стала Канбан (по-японськи Канбан перекладається як Картка). Коли закінчувалися деталі в контейнері, канбан з спустошеним контейнером передавалися на попередній ділянку, що означало необхідність провести очерь д ву партію деталей. І так само як у Форда, Тайіті Воно впровадив конвеєр, що в ті часи для виробництва малих партій було просто немислимо. За 50 років роботи, TPS перетворилася в фантастичне конкурентну перевагу Toyota. Низька собівартість автомобілів, високий рівень прибутковості Toyota укупі з відмінною якістю вже 30 років не дають спокійно жити іншим автовиробникам.
Теорія обмежень (T heory Of Constraints - TOC або ще 1 назва ББК - Барабан-Буфер-Канат) була розроблена Еліяху Голдраттом для виробництв з незначним часом обробки (менше 10%) у порівнянні з поточним часом виробничого циклу. TOC також відмінно працює в виробництві з будь-якою кількістю продукції, що випускається. Чому багато виробників терпіли невдачі з впровадженням у себе Виробничої Системи Тойота. Необхідно добре розуміти, що Тайіті Воно розробив практичний механізм організації виробництва саме для Тойота. базуючись на концепціях ефективного виробництва Форда. Для Тойота характерно виробництво незначного асортименту автомобілів, модельний ряд змінюється не частіше ніж один раз на рік і надходження замовлень від покупців вирівняні таким чином, щоб не зірвати встановлені терміни їх виконання. Однак, більшість підприємств працює в іншій виробниче середовище: широкий асортимент, який змінюється частіше, ніж 1 раз в рік і супроводжується нестабільним надходженням замовлень від покупців. В результаті, застосування механізму обмеження від перевиробництва Тойота - Канбан, стає неможливим. Адже за умови виробництва широкого асортименту виробів, не вийде тримати між двома ділянками контейнери з деталями для кожного виду продукції. Виходячи із зазначеного характеру виробничого середовища, Голдратт пропонує відійти від обмеження перевиробництва по площі, як у Форда, і за кількістю, як у Тойота, і використовувати механізм обмеження за часом запуску у виробництво. Управління потоком слід організувати за пріоритетами, наприклад, виділити деталі, які знаходяться менше 30% у виробництві зеленим кольором, більш 70% - жовтим і інші червоним кольором. І вибудувати порядок обробки деталей строго згідно квітам червоний-жовтий-зелений.
Власне кажучи, це все. Була мета познайомити з таким несподіваним відкриттям. Хоча концепції ефективного виробництва єдині, але практичні рішення побудовані виходячи з умов конкретної виробничої середовища. Тому, перш ніж взятися за застосування практичних підходів в своєму виробництві, необхідно чітко уявляти собі для якої виробничого середовища розроблялося конкретне рішення.
Всі подробиці по цій темі можете знайти в джерелах інформації, зазначених в кінці статті.
Мої знання по темі представлені в карті пам'яті (відкривається після клацання в новому вікні)
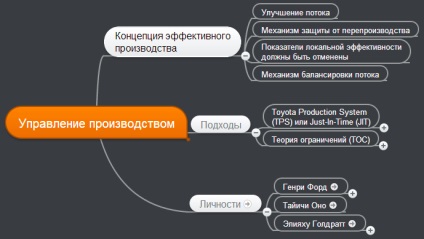