Опис схеми. Залишковий сировину змішують з циркулюючим і свіжим ВСГ і через систему теплообмінників і піч подають під розподільну решітку реактора із псевдозрідженим шаром сіро-стійкого каталізатора (АКМ). У цьому шарі, створюваному газорідинним потоком, здійснюється гідрокрекінг. Продукти реакції, виходячи з верху реактора, віддають тепло в теплообмінниках і холодильниках і надходять в сепаратор високого тиску, де від рідкої фази відділяється циркулює ВСГ. Після очищення від сірководню і осушення цей газ повертають компресором на змішання з сировиною. Насичений легкими вуглеводнями каталізата з низу сепаратора після скидання тиску перетікає в наступний сепаратор, де відокремлюються газоподібні вуглеводні і, частково, розчинений сірководень, а потім потрапляє в стабілізаційну колону, для відділення бутанов і залишився сірководню. Стабільний гидрогенизат направляють на ректифікацію в звичайну систему з трубчастої печі і колони перегонки каталізатора. З цієї колони відбирають бензин, дизельного паливо і залишок. Залишок можна повертати насосом на повторний гідрокрекінг, а також використовувати в якості сировини каталітичного крекінгу або як котельне паливо. Рівноважну активність каталізатора в псевдозрідженому шарі підтримують постійною, періодично або безперервно виводячи частину каталізатора і виконуючи її свіжим. Тиск в реакційній зоні 15-20 МПа, температура 425-450 0 С, об'ємна швидкість подачі сировини 1ч -1. кратність циркуляції водню 1000-1200 м 3 на 1 м 3 сировинної суміші.
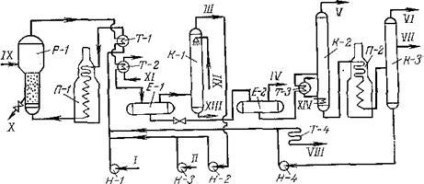
P-1-реактор; П-1, П-2-печі; К-1-колона очищення газу від сірководню; К-2 - стабілізаційна колона; К-З - колона перегонки каталізатора;
Т-1 - теплообмінник; Т-2, Т-4 - холодильники; Т-3 - підігрівач;
Е-1, Е-2 - сепаратори; H-l, Н-4 -насоси; Н-2, Н-3 - компресори.
I -сир; II- водень: III- циркулює газ; IV - вуглеводневий газ (з H2 S); V- бутан (з H2 S); VI-пари бензину; VII- легкий газойль; Vlll - важкий газойль; IX - свіжий каталізатор; Х - каталізатор на реактівірованіе; XI - вода; XII - свіжий розчин моноетаноламіна; XIII - відпрацьований розчин моноетаноламіна; XIV -водяной пар
Виробництво водню. На НПЗ, де є установки каталітичного риформінгу і гідроочищення світлих нафтопродуктів, потреба в водні зазвичай задовольняється його кількістю, що отримуються на установках риформінгу. Якщо на старих установках риформінгу, які працювали на платиновому каталізаторі при м'якому режимі, вихід водню не перевищував 1%, то на сучасних установках з платінореніевих і поліметалічних каталізаторами вихід водню може досягати 2% на сировину і більш. Якщо в схему заводу ввести каталітичний крекінг, то з урахуванням гідроочищення одержуваних при цьому дистилятів потреба в водні зростає, особливо з урахуванням того, що світлі продукти каталітичного крекінгу містять ненасичені вуглеводні і вимагають, тому підвищеного витрати водню в порівнянні з відповідними прямогонного фракціями. Для здійснення такої потокової схеми необхідно спеціальне виробництво додаткового водню. Основний метод виробництва водню - парова каталітична конверсія газового або нафтової сировини. Конверсії можна піддавати як газоподібні вуглеводні, так і рідкі нафтопродукти. Вихід водню буде тим більше, чим вище концентрація його в молекулах сировини. З цієї точки зору, найбільш сприятливе сировину - метан, в молекулі якого 25% (мас.) Водню. Джерелом метану є природні гази з концентрацією 94-99% (об) СН4. Використовують також сухі гази нафтопереробки. На заводі паливного профілю з глибокої переробки нафти отримують сухі гази, які містять водень, метан і етан. Процес протікає з витратою тепла, і термодинамічно йому сприяють високі температури: без каталізаторів необхідна температура 1300-1400 0 С. При цьому йдуть побічні реакції піролітичних перетворень граничних вуглеводнів в граничні і виділення вільного вуглецю. Для зниження температури і забезпечення високої селективності процесу використовують нікелеві каталізатори з промотуючих добавками. Нікель знаходиться на носії (оксиди алюмінію, магнію або кремнію). Для протидії осадження вуглецю застосовують окислювальні добавки. Каталізатори чутливі до сірководню, органічним сірчистим сполукам і галогенів. Застосування каталізатора дозволяє знизити температуру до 700-1000 0 С. Процес проводять як при підвищеному тиску, так і при тиску, близькому до атмосферного. Використання підвищеного тиску змушує кілька збільшувати температуру і тим самим знижувати селективність процесу. Однак якщо вихідний газ надходить на установку під тиском, то неекономічно дросселіровать його, а потім знову компримованого утворився газ. Найбільш широко застосовують тиск 2-4 МПа. Реактор являє собою трубчасту піч з вертикальними трубами. Печі в основному прямокутного перетину; труби в них розміщені в один, два і більше рядів. Їх опалюють газом. Реакційні труби сприймають радіантні тепло, а тепло конвекції використовується для підігріву сировини і виробництва пара. Пальники розташовані в зведенні печі, і димові гази рухаються прямотоком з паро-сировинної сумішшю. Робоча частина труб заповнена каталізатором, насипаним на решітку. Для виготовлення труб зазвичай використовують хромонікелевої сталі.