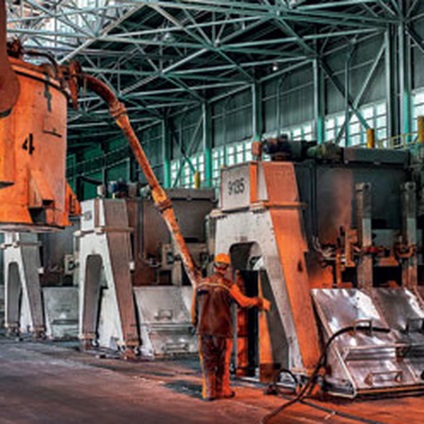
Від Плінія до наших днів
Пліній Старший згадує легенду про те, що одного разу римському імператору Тиберію піднесли чашу з металу, схожого на срібло, але дуже легкого. Майстер, який виготовив чашу, стверджував, що метал отриманий з глини, і Тіберій, побоюючись, що цей метал знецінить всі його срібло, наказав стратити винахідника, щоб зберегти секрет. Невідомо, наскільки правдива ця легенда, але з'єднання алюмінію знайомі людям з найдавніших часів, адже глинозем (біла глина) - це не що інше, як оксид алюмінію (Al2 O3). Алюміній - третій за поширеністю елемент в земній корі (після кисню і кремнію). Своє ім'я він отримав від латинської назви алюмінієвих солей, квасцов (подвійних сульфатів трьох- і одновалентних металів) - alum, - які протягом багатьох століть використовувалися для фарбування тканин і шкіри.
Металевий алюміній вперше отримав в 1825 році датський фізик Ганс Християн Ерстед відновленням з хлориду алюмінію за допомогою амальгами калію. Двома роками пізніше німецький хімік Фрідріх Велер використовував для цієї мети металевий калій. А в 1846 році Анрі Сент-Клер Девілль допрацював метод Велера з використанням металевого натрію, що дозволило отримувати хоч і малі, але вже не мікроскопічні кількості металу. Проте алюміній ще довгий час залишався дуже рідкісним і дорогим металом. Про це свідчить той факт, що на одному з прийомів, організованих французьким імператором Наполеоном III, багатство монархії символізували алюмінієві столові прибори господарів і почесних гостей, а решта гостей обходилися «звичайними» - золотими - ложками і виделками.
концентрований електрику
У електролізному цеху алюмінієвого заводу встановлені сотні електролізерів. Кожен з них влаштований досить просто: сталева ванна, яка представляє собою катод (негативний електрод), наповнена розплавом кріоліту з температурою близько 950 ° C, в якому розчинений оксид алюмінію (глинозем). У розплав занурюється анод (позитивний електрод). Через електролізер пропускається струм, на аноді виділяється кисень, на катоді - алюміній, який в рідкому вигляді покриває дно ванни (температура його плавлення 660 ° С). «Наші інженери жартують, що алюміній - це концентроване електрику, - пояснює Віктор Манн, технічний директор ОК« РУСАЛ ». - Отримання кілограма металу вимагає витрати 13 кВт • год електроенергії. Колись цей показник був істотно вище, але в міру вдосконалення технологій його вдалося знизити - і я сподіваюся, що вдасться знизити ще. Власне, це один із напрямів наших розробок - домогтися зниження споживання електроенергії за рахунок оптимізації конструкції анодів, електролізера, зменшення розсіювання тепла та інших факторів ».
Використання електроенергії породжує і ще одну проблему. У електролізному цеху сотні електролізерів з'єднані послідовно, падіння напруги на кожному зовсім невелике - всього близько 4 В. А ось ток вимірюється в сотнях кілоампер (зокрема, на ХАЗі це 320 кА, а в новіших електролізерах - 550 кА). Такі струми, поточні по поруч розташованим провідникам, викликають появу сили Ампера, в результаті чого на струмопідведення починають діяти сили, які обчислюються сотнями і тисячами кілограм-сил. «Щоб мінімізувати вплив сили Ампера, конструкцію токоподводов і самих електродів доводиться розраховувати за допомогою комп'ютерних моделей, - каже Віктор Манн. - Конфігурація виходить складна - потрібно розподілити струмопідведення до анодам по висоті і довжині, врахувати розміри електричних шин довжиною в десятки метрів, щоб магнітні поля не деформовані всю конструкцію. Сили впливають і на розплавлений алюміній, який шаром товщиною 20-50 см покриває дно ванни і теж є провідником електричного струму ».
Аноди і катоди
В процесі виробництва алюмінію витрачається не тільки електроенергія, але і вуглецеві аноди. Оскільки матеріал анода повинен протистояти електричної ерозії (розчиненню в електроліті і в алюмінії), зараз в цій якості використовується вуглець. Але під дією кисню, що виділяється він досить швидко вигоряє з утворенням чадного і вуглекислого газів: для отримання однієї тонни алюмінію витрачається приблизно півтонни вуглецевих анодів.
Існує два основних типи вуглецевих анодів. Безперервні самообжігающіеся аноди Содерберга є брикети з коксосмоляной пасти, які завантажуються в сталевий кожух електрода зверху. У міру вигоряння нижній частині брикети опускаються вниз і обпікаються до того, як досягають ванни з розплавом. До складу брикетів входять різні сполучні смоли, які вносять свою частку в продукти згоряння. Другий тип - заздалегідь обпалені аноди - дає менше викидів в процесі електролізу. Вони формуються з вуглецю з різними сполучними і обпікаються в спеціальних печах. Готовий електрод кріпиться в анододержателе і опускається в розплав. У міру вигоряння анод замінюють, а «недогарки» переробляють, виготовляючи із залишків нові аноди.
інертні аноди
Витрата електродів породжує безліч проблем. Крім того, що заміна електродів ускладнює процес і збільшує вартість алюмінію, це ще призводить до серйозних викидів вуглекислого та чадного газів. За словами Віктора Манна, інертний анод, яка б не витрачався в процесі електролізу, що не вигоряв, що не розчинявся в розплавленому кріоліті і не забруднював б отриманий алюміній, - мабуть, головна мрія розробників електролізного обладнання. Це можуть бути керамічні аноди на основі оксидів різних металів (заліза, нікелю, міді та ін.), Повністю інертні по відношенню до електроліту і алюмінію, але складно зварюються (тому до них досить складно зробити токоподвод). Інший підхід - спеціальні металеві сплави (залізо, мідь і ін.), Вони більш технологічні, але можуть реагувати з алюмінієм, вносячи в нього частку домішок. «Ми вже досить близькі до цього, зараз такі аноди проходять випробування, і сподіваюся, що протягом декількох найближчих років почнуть впроваджуватися у виробництво на заводах« РУСАЛ », - каже Віктор Манн. - Інертні аноди не вимагають заміни вже наявних електролізерів з горизонтальними анодами. Але якщо говорити про майбутнє і конструкції, яка спеціально розрахована на інертні аноди, то можна очікувати переходу до іншої схеми - набору з безлічі чергуються вертикальних анодів і катодів. Така конфігурація дозволить істотно збільшити продуктивність і ефективність процесу електролізу. Хоча, звичайно, там будуть потрібні нові рішення. Скажімо, в звичайній схемі з горизонтальними анодами регулювання зазору між електродами відбувається просто за рахунок опускання анода. Регулювати ж зазор між вертикальними електродами конструктивно складніше. Крім того, ускладнюється і утилізація тепла. Але переваги, звичайно, того варті. Авіаційна, автомобільна, будівельна та електротехнічна промисловість вимагають все більше алюмінієвих сплавів, так що за цим металом майбутнє ».
Від сировини до чушки
I. Для отримання 1 т алюмінію потрібно приблизно 2 т глинозему. А до того, як потрапити в електролізер, глинозем виконує ще одну важливу функцію - служить абсорбентом в газоуловітелях, поглинаючи гази, що утворюються в процесі електролізу.
II. Старі технології виробництва алюмінію передбачали невелика витрата кріоліту, вугільний пил приводила до утворення піни (шлаку), який час від часу потрібно було видаляти. Сучасні технології в цьому відношенні набагато чистіші - кріоліт не тільки не витрачається, але навіть напрацьовується за рахунок домішок натрію в глиноземі, який в процесі електролізу реагує з утворюється фтором.
III. Алюміній опускається на дно електролізера, а потім витягується вакуумним ковшем. З ковша він зливається в міксер, де готуються потрібні сплави.
IV. Основні домішки в отриманому алюмінії - це залізо і кремній (зазвичай менше 1%). Чим їх менше, тим вищим вважається сорт металу. Джерела домішок - це аноди, ванна, інструменти, струмопідведення і інші елементи електролізера.
виробництво алюмінію
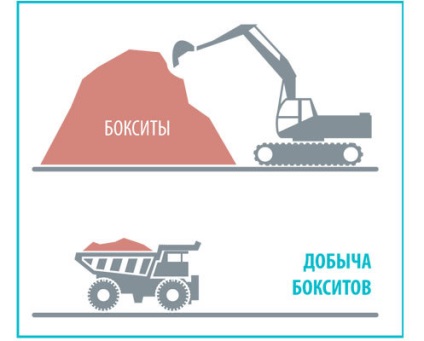
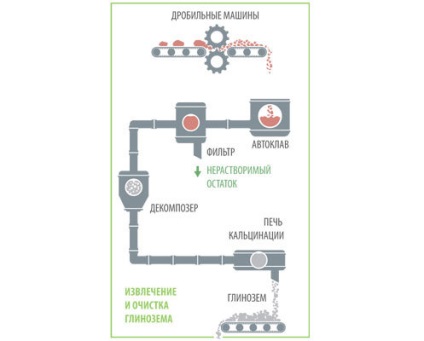