Разом зі словом «каменоломня» виникає асоціація зі словом «каторга» і уява відразу малює в голові моторошні картинки про непосильну працю катованих втоми і хворобами людей. Насправді це мало чим відображає реальність. Сучасна видобуток блочного каменю процес хоч і дуже трудомісткий, але цілком посильний для професіоналів. Про те, як і для чого видобувається такий камінь я постараюся розповісти на прикладі одного гранітного кар'єру на півночі Ленінградської області.
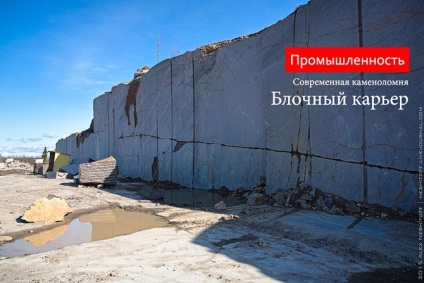
Кар'єр прихований від сторонніх очей, сховавшись в глухих місцях майже на кордоні з Фінляндією. Дорога є, але назвати це дорогий досить складно. Швидше за напрямок. Вибоїста грунтовка протяжністю близько сорока кілометрів від Каменногорск до кар'єра відняла у нас більше години. Кожен новий кілометр був гіршим за попередній, поки нарешті дорога не перетворилася на суцільне піщано-глиниста місиво. Вірний знак. Значить ми майже на місці.
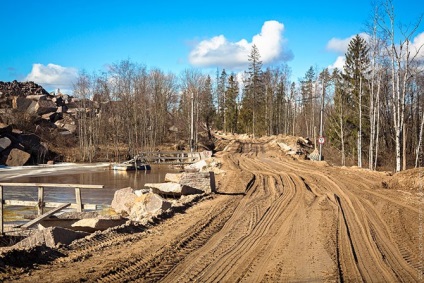
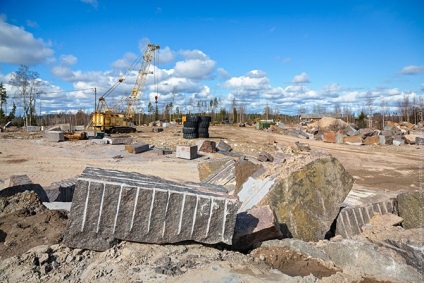
Побутові умови тут спартанські. Електрики немає. Все електропостачання здійснюється за допомогою дизельного електрогенератора. Все інше як у селі. Вода в колодязі, туалет на вулиці, душ там же. Опалення пічне. Суворий побут суворих камнетесов.
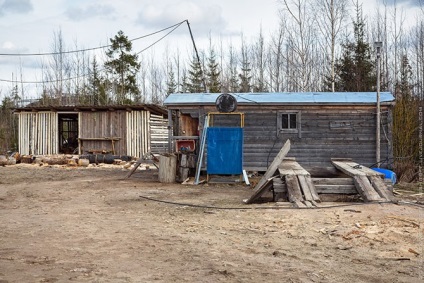
Картину брутальності доповнює пошарпаний бульдозер вітчизняного виробництва, як монумент дремлящій близько побутового містечка. Для нього тут не дуже багато роботи.
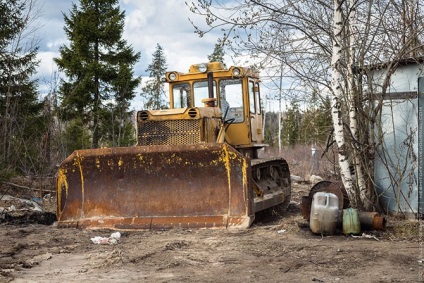
Про кар'єру і про аспектах роботи нам розповів старший поточної зміни, люб'язно погодився на проведення невеликої екскурсії по своєму господарству. У зміні всього 5-7 чоловік. Практично всі працівники мають універсальні навичками і поєднують кілька посад. Рентабельність виробництва при існуючих обсягах тут намагаються підвищити зниженням собівартості, в тому числі і економією на штаті. Гірничий майстер тут виступає і як начальник ділянки, і як енергетик. Оператор навантажувача може бути і кольщик, і оператором пив, і механіком.
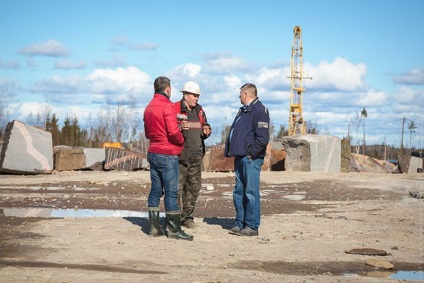
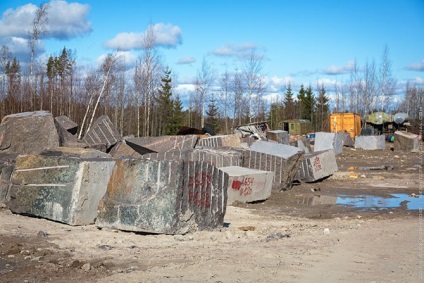
Однак, не дивлячись на більш дорогу вартість, великі блоки видобувати не надто вигідно. Основним попитом користуються блоки II і III групи. Такі як наприклад цей. Це класичний приклад найбільш затребуваного на цьому кар'єрі блоку. Його розмір приблизно 1х1х2,5 метра.
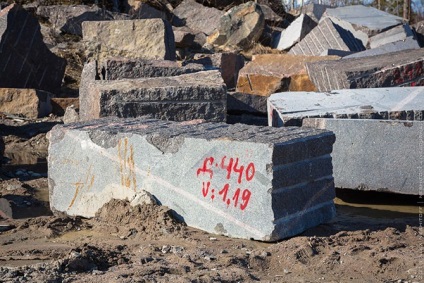
Однак серед готових блоків знаходяться і такі гіганти. Невідомо скільки такий блок буде чекати свого покупця, але рано чи пізно це станеться і це буде вигідний продаж. Такі групние блоки зазвичай беруть для подальшої розпилювання на слябів - пластини, з яких потім виготовляють, наприклад, стільниці або підвіконня. Але ця продукція не надто ходова. Набагато більш часто з граніту виготовляють облицювальну плитку, бордюрний камінь або плити для мощення мостових і тротуарів. Для цих виробів такий розмір сировинних блоків просто не потрібен.
Тому в більшості випадків здобуті великі блоки пасерують для додання їм більш затребуваних габаритів і правильної форми. Для цього використовується спеціальне бурильне обладнання, яке способоності дуже швидко, а головне точно пробурити рядок з паралельних отворів, через які пізніше блок буде розколотий на частини. Існує і більш технологічний спосіб - розпилювання, але в плані мобільності бурілка виграє, хоча і помітно поступається в швидкості і якості. Після дискової пили краю блоку набувають гладкі рівні поверхні, що позитивно впливає на його товарні якості.
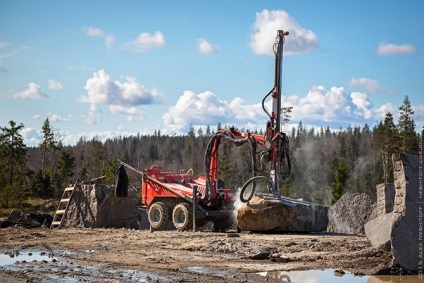
Технології видобутку блоків існують різні. Найпоширеніший видобутку в нашій країні ще недавно був спосіб слабких вибухів. Але у нього є безліч недоліків. При такому способі видобутку виходить величезна кількість відходів, що досягає 80% від отриманої гірничої маси. Крім того, неправильний розрахунок потужності вибуху може привести до появи тріщин через що такий камінь буде просто нікому не потрібен. Таким чином можна взагалі занапастити родовище і єдиним продуктом, який можна буде отримати залишиться тільки щебінь. Тому все більшого поширення набуває спосіб канатного пиляння. Конструкція канатної пили дуже проста. Фактично це електромотор, який простягає канат, віддалено схожий на велосипедну ланцюг з ріжучими алмазними елементами.
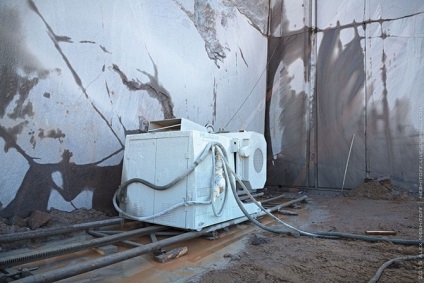
Саме після її роботи залишаються такі ідеально рівні і гладкі стіни. Але не все так просто як здається на перший погляд. Якщо в процесі пиляння нічого складного - пила пиляє самостійно, поступово в міру пропіліванія зміщується по рейках, то процес підготовки куди більш трудомісткий.
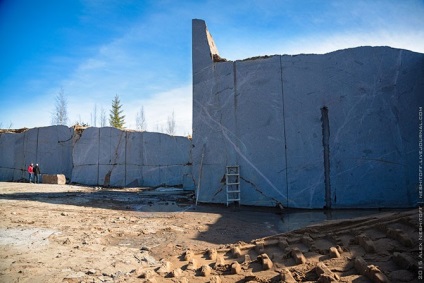
Для того щоб завести канат необхідно попередньо пробурити в скелі два отвори. Одне вертикально, а друге горизонтально. причому їх потрібно пробурити таким чином, щоб вони перетнулися в одній точці. Найменший перекіс бура і буріння піде нанівець. Для цієї операції в світі розроблено безліч пристроїв, що спрощують життя гірникам, але на цьому кар'єрі традиційно довіряють ручної переносний бурової установки з пневмоприводом.
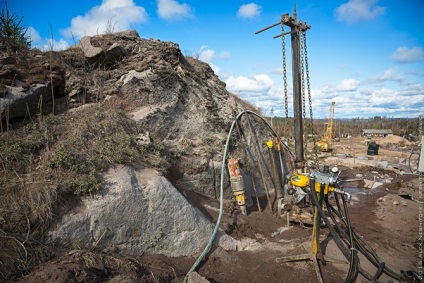
Бурить вона гранітну породу дуже ефективно, але має свої особливості. Для роботи їй потрібен компресор. Добре якщо є дизельний компресор. Він може працювати автономно. А якщо компресор електричний, то до нього доведеться або тягнути дроти з електроживленням, або живити від дизельного генератора. Така схема якраз і застосовується на кар'єрі. Як ви пам'ятаєте зовнішнього електропостачання тут немає. У міру буріння довжину бура доводиться нарощувати. Це робиться за допомогою бурильних труб, які крім подовження забезпечують також подачу повітря.
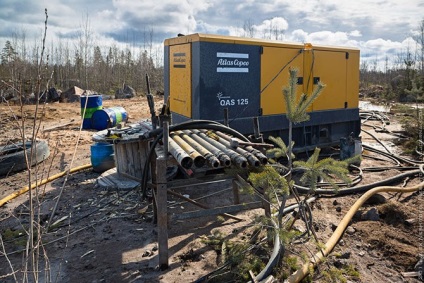
Мабуть головним недоліком такого бурового інструменту є його неточність. За словами самих робітників, найскладніше в канатному пилянні це точно пробурити свердловини. Це виходить, на жаль, не завжди. Іноді доводиться перебурівать, часто не один раз. Якщо все пройшло гладко в отримані отвори заводиться ріжучий канат і далі досить доглядати за пилкою, поки вона відпилює шматок скелі.
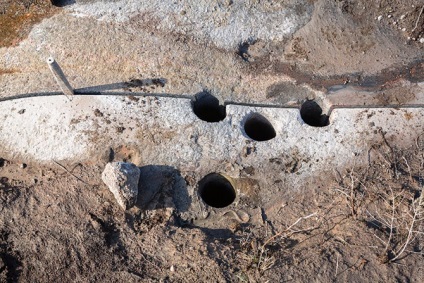
Пиляють вертикальними скибками, званими панелями. Після того як пропив закінчений панель завалюють. Від удару об землю вона як правило розколюється по природним тріщинах. Після цього отримані блоки сортують і надають їм товарну форму.
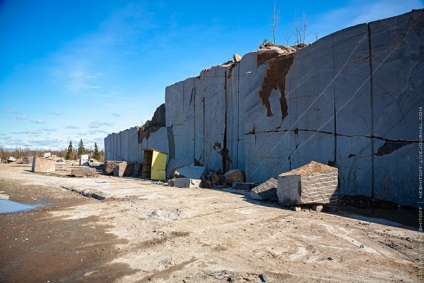
Завалювання панелі, мабуть, найнебезпечніша процедура у всьому процесі видобутку блоків. Чим вище горизонт, тим небезпечніше. Панель завалюється за допомогою навантажувача. У розпил зверху вставляється сапа - сталевий гак. До нього кріпиться трос, на іншому кінці зачіпається навантажувач і повільно починає тягнути. У якийсь момент скеля не витримує і завлівается. Не хотів би я в цей момент знаходитися поруч. До речі ризик мимовільного самостійного завалювання відпиляної панелі теж існує. Тому треба бути гранично обережним і уникати потенційно небезпечних зон.
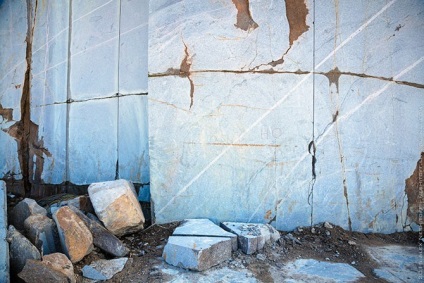
Тріщинуватість - головний ворог видобувачів. Якщо тріщин багато, то відповідно збільшується відсоток відходів. У відходи йдуть уламки неправильної форми, з неправильним напрямком шаруватості каменю, занадто строкатим малюнком і т.п. Втім поняття відходи в даному випадку досить абстрактне. При бажанні, практично весь цей відхід можна відповідним чином переробити. Наприклад, розколоти його на дрібні вироби, такі як бруківка. Інше питання наскільки це доцільно. Тут кожен кар'єр вирішує цю задачу самостійно.
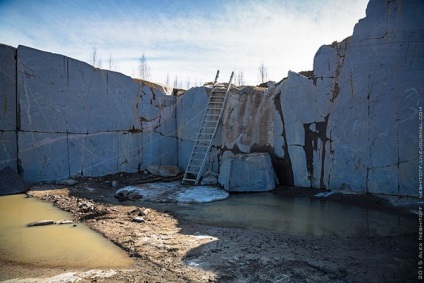
Головною машиною на блочному кар'єрі безперечно є величезний фронтальний навантажувач. Саме він виконує всю важку роботу на кар'єрі. Завдяки його силі і вазі, він є незамінним помічником людини практично у всіх операціях, від розчищення забою від відходів, транспортування блоків, до завалювання панелей. Найпоширенішим навантажувачем для роботи на подібних кар'єрах є CAT 988. Це величезна махина вагою 50 тонн, неймовірно сильна і надійна. Такий агрегат має просто космічну вартість - близько 800 000 доларів. Одна тільки шина від такого навантажувача коштує близько 10 000 доларів.
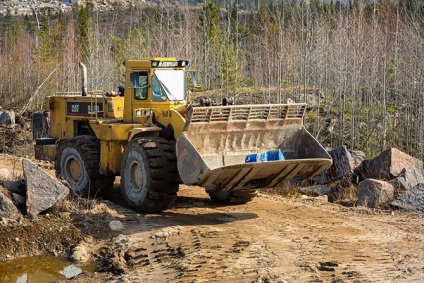
Як я вже сказав. Ця машина робить абсолютно все. З її допомогою готові блоки переміщаються на склад, забій очищається від уламків, проводиться доставка палива до установок в будь-якій точці кар'єра, здійснюється навантаження на автотранспорт, відсипаються і рівняються под'езние шляху, проводиться прибирання снігу.
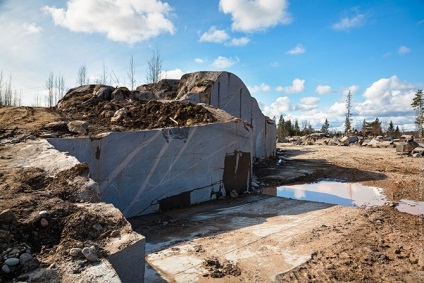
Для переміщення і навантаження блоків навантажувач не використовує ківш. Для цих операцій є інше пристосування - вила. Навантажувач обладнаний швидкознімним пристроєм, що дозволяє оперативно змінювати навісне устаткування. Досить пари хвилин, щоб ковшовий фронтальний навантажувач перетворився в навантажувач вилковий на подобу того, що ми часто зустрічаємо в великих магазинах будівельних товарів. Тільки більше, набагато більше.
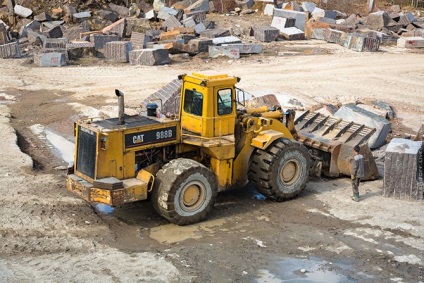
Вила, до речі, теж солідні. Під стать самій машині. Їм доводиться піднімати вагу до 20 тонн. Але іноді блоки важать і більше. Для їх транспортування стандартні вантажні напівпричепи не підходять. Їх перевозять на посилених платформах, на таких зазвичай транспортують важку будівельну техніку, а навантаження здійснюється вже за допомогою крана.
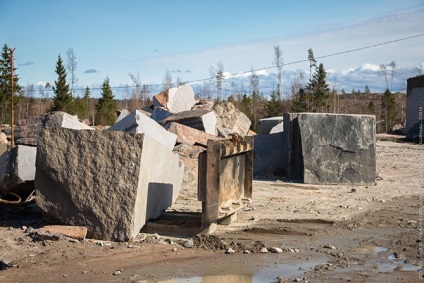
А так виглядають ті самі відходи від виробництва блоків: уламки, осколки і обрізки, за своєю формою і розмірами не потрапляють ні під одну групу. Вітчизняні кар'єри традиційно не піклуються про переробку своїх відходів, які насправді є прекрасною сировиною. Але для цього потрібне відповідне обладнання, яке дуже дороге. Крім того це вже соврешенно інший профіль і інший ринок збуту. Самим кар'єрів це просто не вигідно, а переработчкам каменю в свою чергу невигідно транспортувати уламки до своїх виробництв. Через це відвали давно працюють кар'єрів досягають неймовірних розмірів. Часом в них накопичується по кілька мільйонів кубічних метрів породи.
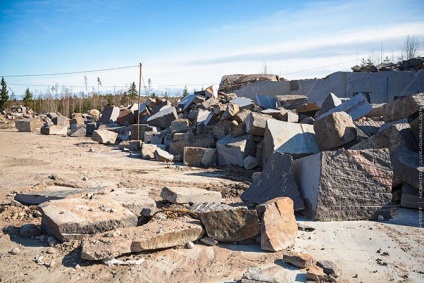
Каменедобувних бізнес в Росії тільки зараз починає виходити на шлях високих технологій. Все частіше застосовується високотехнологічна техніка та обладнання, використовуються більш ефективні технології, з'являються додаткові цеху по переробці каменю. Зрозуміло такий розвиток безпосередньо залежить від керівництва і, на жаль, у нас поки частіше буває так, що існуючий стан справ багатьох влаштовує. Втім ця ситуація не тільки в гірничодобувній промисловості.
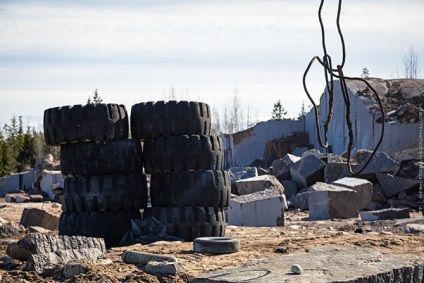