Проблема утилізації деревних відходів стоїть перед багатьма дачниками. Розповідаємо, як її вирішити, на досвіді користувачів FORUMHOUSE
Верстат для подрібнення деревини (садові дробарка) дозволяє назавжди забути про необхідність розпалювати вогонь з метою утилізації деревних відходів. Це пристрій здатний переробляти вихідний матеріал в тирсу, які завжди можна використовувати для обробки грунту або для виготовлення будівельних матеріалів.
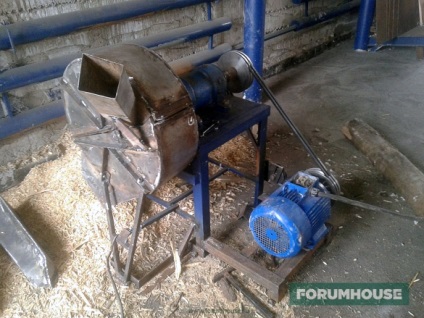
Практичний господар ніколи не дозволить безслідно згоріти у вогні ценнейшему удобрення - тирсі. Правильно організована компостна купа за короткий час перетворить це добро в екологічне і насичене добриво.
Став застосовувати злегка лежані тирсу і розкладати їх за допомогою азотфіксуючих бактерій (в повітрі 78% азоту). Обов'язково розпушування. Саджу прям в тирсу.
Що стосується виготовлення будівельних матеріалів на основі деревної тріски: якщо ви чули про таке поняття, як «арболит». то напевно зрозумієте - про що йде мова.
І, до речі, деякі котли опалення успішно працюють на паливі, виготовленому з деревної тирси. Отже, сфера застосування матеріалу, отриманого з деревини, що відслужила свій вік, велика. А тому, виготовлення машини для подрібнення деревини є заняттям виправданим.
Схема садової дробарки
Вивчення конструкції будь-якого механізму починається з вивчення схеми і принципу його дії. Почнемо зі схеми.
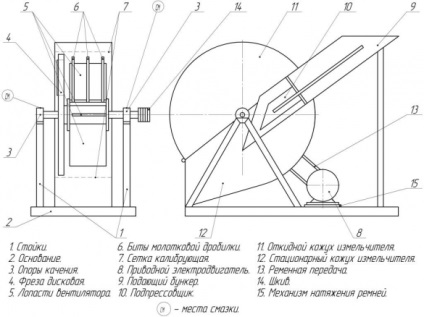
На цьому зображенні представлена наочна схема садової дробарки. Перерахуємо її основні елементи:
- Рама - складається зі стійок (1) і підстави (2).
- Механізм приводу - механізм натягу ременів (15), двигун (8), ремінь (13) і приводний шків (14).
- Вал з вентилятором і ріжучими елементами (поз. 4,5,6).
- Приймаючий пристрій - подає бункер (9), подпрессовщік (10).
- Захисний кожух (поз. 11 і 12).
- Калібрує сітка (поз. 7).
Якщо всі вузли машини зібрані правильно, якщо зварювальні шви надійні, а ріжучі елементи міцні, то верстат буде довговічний і зручний в експлуатації. Він забезпечить хороший захоплення переробляється деревини, а на виході ви отримаєте тирса необхідної величини.
Принцип дії механізму наступний:
З огляду на, що дробарка є громіздким механізм (до того ж схильний до вібрацій), її рама повинна бути виготовлена з міцної металевої труби (з товщиною стінки від 4 мм) або з жорсткого металевого куточка.
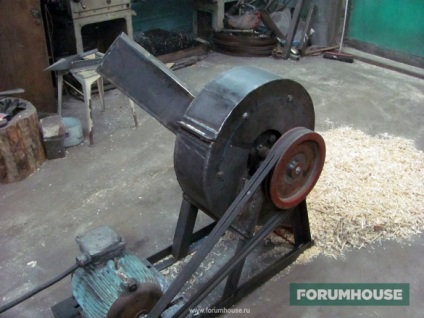
Пересувний варіант подрібнювача буде непогано оснастити парочкою коліс.
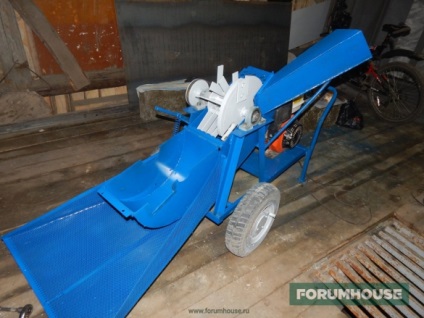
Розміри і інші особливості рами повністю залежать від габаритів навішується на неї обладнання та від продуктивності верстата.
Конструкція приводу, по суті, проста: механізм натягу, шківи і ремені - все це можна без особливих проблем виготовити або купити. Ключовим завданням, яку нам належить вирішити, розробляючи конструкцію приводу, є вибір відповідного двигуна.
Двигун можна використовувати як електричний, так і бензиновий. Верстати з бензиновим двигуном мають більш складну конструкцію. Верстати з двигуном електричним, навпаки, більш компактні і прості в управлінні. Для стаціонарних подрібнювачів деревини краще використовувати електродвигун. Для мобільних верстатів більше підходить бензиновий двигун. Серед вдалих моделей, які користувачі FORUMHOUSE змогли зібрати самостійно, переважають машини з електричним приводом. Тому їх ми і будемо розглядати в цій статті.
Двигун слід вибирати, виходячи з його потужності. Потужність двигуна повинна бути не менше 4-х кВт. Цього показника досить для подрібнення садових гілок діаметром до 4-х см. При цьому оптимальні обороти на валу подрібнювача повинні відповідати показнику 1500 об / хв.
Значне зниження оборотів (1000 об / хв і менше) на робочому валу дробарки призводить до зменшення сили повітряного потоку, який виштовхує подрібнену масу з дробарки. А це може спричинити за собою цілком передбачувані наслідки: забивання барабана тирсою, падіння потужності і т. Д.
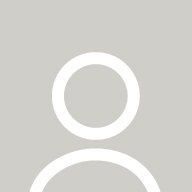
Ana789Пользователь FORUMHOUSE
В обговоренні подрібнювачів є інформація, що кількість обертів ротора має бути в межах 1500 об / хв.
Якщо крім подрібнення садових гілок ви перед собою ставите інші цілі (наприклад, підготовка сировини для виробництва арболітових плит), то вашому верстата неодмінно знадобиться запас потужності. Також при цьому може бути змінено і кількість обертів на робочому валу дробарки (як в більшу, так і в меншу сторону).
Volodaris Користувач FORUMHOUSE
Двигун 5.5 кВт виявився слабким. При такій подачі брус 50х50 він не долає. Мабуть, це пов'язано з хорошим самозахопленням деревини. Тому і почалися переробки верстата (щоб не купувати потужний двигун, а він потрібен був би як мінімум 11 кВт).
Оптимальна кількість обертів на валу дробарки можна отримати, змінюючи діаметри приводних шківів.
Двигуни на перших верстатах застосовував трехтисячніков - тільки тому, що не було 1500 об / хв.
Вал подрібнювача з ріжучими елементами
Мабуть, найскладнішою частиною нашого верстата є подрібнювач - вал дробарки (на підшипниках), з подрібнювальної фрезою і молотками (бітами). Його розгляд почнемо з подрібнювальної фрези, що складається з маховика (диска) з ножами.
Ключовим параметром диска, який безпосередньо впливає на продуктивність дробарки, є його діаметр (від 350 до 600 мм). Менше робити не варто.
На мій погляд - це тупиковий рішення (я маю на увазі диск 200 мм). По-перше, які ножі туди можна поставити? По центру вал, скажімо, 50 мм. Що залишиться від диска? У моєму випадку мій верстат не дозволив мені зробити диск більше (350 мм при товщині в 15 мм - це був край). Все, що було зроблено, зроблено, не виходячи з дому. Але нічого страшного немає в тому, щоб замовити диск у будь-якого токаря.
В даному випадку до диска в процесі виготовлення була приварена металева втулка. Після того як диск був насаджений на вал, втулку приварили до самого валу. Таким чином фреза була надійно зафіксована на валу.
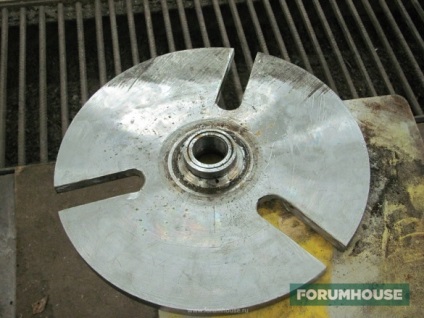
Як бачимо, 350 мм - це мінімум. При цьому користувач «Kirasir» пішов далі, виготовивши диск діаметром 600 мм і товщиною 33 мм, беручи за основу розміри деталей від китайської дробарки. На диск було встановлено 3 ножа. Подрібнювач приводиться в дію двигуном потужністю 18,5 кВт.
На окрему увагу заслуговують ножі, що встановлюються на диск фрези. Сталь для ножів повинна бути міцною, тому користувачі FORUMHOUSE рекомендують в якості вихідного матеріалу для ножів використовувати автомобільні ресори.
Ножі - це звичайна ресора (думаю, що від ГАЗ-52). Ніякого попереднього відпустки не робив (так само, як і загартування). Самі ножі були зібрані в пакет і оброблялися до потрібного розміру на наждаку.
Свердління ресори - заняття трудомістке. І для того, щоб домогтися позитивного результату, свердлити заготовку слід на верстаті (токарному або свердлильному), що дозволяє виставити досить низькі обороти шпинделя (щоб свердел не згорали).
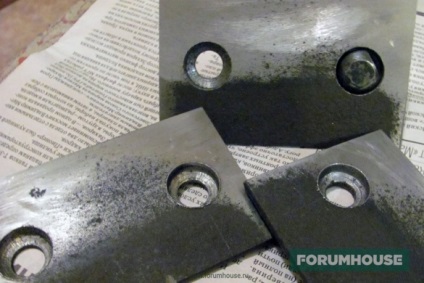
Довжина ножа повинна відповідати довжині робочої прорізи на диску.
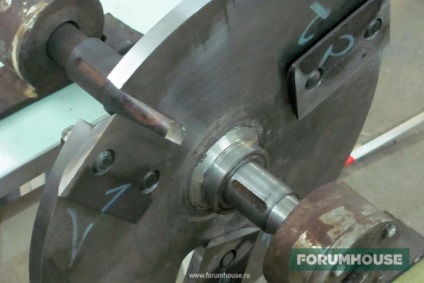
Від того, наскільки правильно заточені ножі, буде залежати продуктивність дробарки і її здатність до самостійного захоплення подається деревини. При хорошому захопленні деревина провалюється в верстат без сторонньої допомоги.
Кут заточування ножа (кут самозаточкі) повинен дорівнювати 30 °.
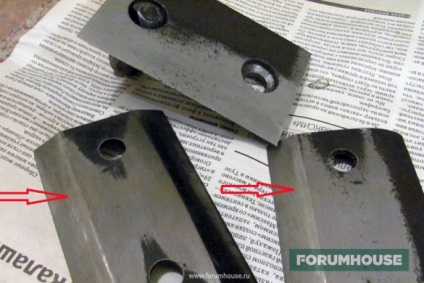
При цьому, заточуючи ріжучий елемент, необхідно створити затиловку (скіс на задній поверхні ножа - під кутом 2 ° ... 3 °). Затиловка потрібна для забезпечення гарного самозахоплення подається деревини.
За науці зворотний кут повинен бути близько 3-5 градусів.
Молоточки (біти) для подальшого подрібнення тріски необхідно робити знімними. На даному етапі складнощів виникнути не повинно. Адже конструкція знімного механізму досить проста, і якщо в її основі будуть використані болтові з'єднання, то вийшли з ладу деталі можна при необхідності швидко замінити.
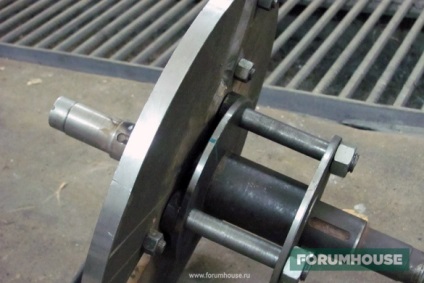
Ось, що говорить про конструкцію молоточків користувач нашого порталу.
Volodaris Користувач FORUMHOUSE
Самі молотки я виготовляв з простої листової сталі товщиною 4 мм. Якщо дробити тільки дерево, то їх міцності буде досить. Щодо заточки: не бачу в цьому сенсу - все працює і так прекрасно.

Диски котушки, зображеної на фото, зроблені зі сталевого листа товщиною 6 мм. Лопаті вентилятора можна виготовити з того ж матеріалу, з якого були зроблені біти.
Балансування робочого вала - завдання непросте, але якщо є така можливість, то її слід виконати. По-перше, це позбавить верстат від зайвих вібрацій, по-друге, значно подовжить термін його експлуатації.
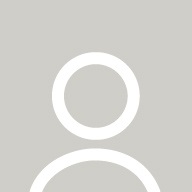
Kyper777Пользователь FORUMHOUSE
Сам диск я балансував спочатку на центрах (попередньо зібрав все, крім молотків). Це була перша груба балансування. Потім балансував на ножах (думаю, дисбалансу же не бути має). Коли буду збирати молотки, їх теж подгоню за вагою.
Вал дробарки найкраще монтувати на дворядні самоустановлювальні підшипники. При роботі в умовах вібрацій і нерівномірних навантажень переваги цих виробів є безсумнівні.
Якщо дробарка робиться для банального подрібнення гілок, і розмір тріски на виході з неї вам не важливий, то молотковий механізм (втім, як і калібровану сітку) включати в конструкцію верстата необов'язково.
Захисний кожух і приймаючий пристрій
Конструкцію кожуха краще розглядати в комплекті з пристроєм одержувача. Розміри кожуха залежать від продуктивності верстата, а точніше - від розмірів його робочих органів (фреза, молоточки і т.д.). Товщина стінок кожуха повинна бути достатньою для того, щоб витримувати інтенсивні навантаження, по можливості, граючи роль протиріжучими елемента. Кожух доцільно робити з відкидною кришкою (для зручності обслуговування верстата), як показано на малюнку.
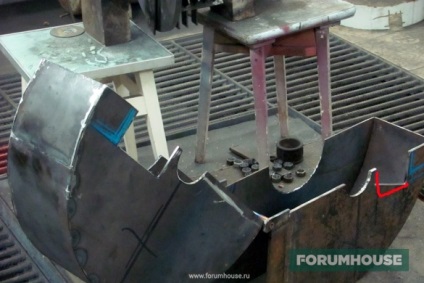
Конструкція представленого кожуха є повністю робочої. Єдине, що було доопрацьовано в процесі настройки верстата - це вікно під завантажувальний бункер (змінився нахил завантажувального пристрою, а, отже, була змінена конфігурація вхідного отвору).
Користувач Volodaris виготовив два верстати з кожухами різної товщини: 6 мм і 12 мм. У конструкції другого верстата роль протиріжучими елемента грає стінка кожуха товщиною 12 мм. Верстат повністю робочий, але для збільшення надійності кожух слід оснастити контрножем (в ідеалі - знімним). Це можна реалізувати наступним чином: до кожуха приварити жорстку пластину, до якої за допомогою болтів і буде кріпитися знімний контрніж.
Протирізальний елемент повинен бути не менш міцним, ніж ріжучий ніж. Тому виготовляти ці деталі краще з одного і того ж матеріалу. Що ж стосується кута заточування контрножем, то він повинен бути прямим.
Сандугач Користувач FORUMHOUSE
Я вважаю, що потрібен міцний метал, т. К. Навантаження чимала, а кут потрібен чіткий - 90 градусів. Якщо я не правий - буду радий прочитати інші версії. 90 градусів - це кут заточки контрножем.
Чим менше зазор між ріжучим і протиріжучими ножем, тим коротше буде виходити тріска. Отже, вказане яку можна звести до мінімуму (головне, щоб ножі не чіпляє один за одного).
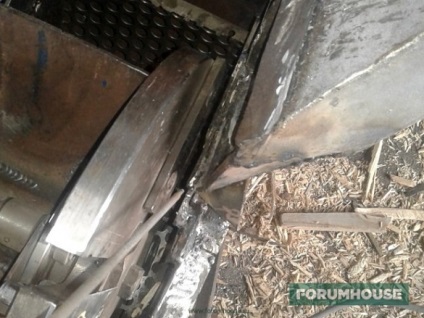
В принципі, зазор між ріжучим і протиріжучими елементом верстата можна відрегулювати в процесі роботи. Це дозволить отримати оптимальну ступінь подрібнення деревини. Наприклад, користувач нашого порталу, зареєстрований під ніком Phoenix83, здійснює регулювання, пересуваючи фрезу уздовж осі обертання. Але можна зробити простіше, підкладаючи шайби різної товщини під контрніж.
Завантажувальний бункер можна виготовити з того ж матеріалу, що і сам кожух. При цьому, з огляду на порівняно невисоку навантаження на даний вузол, його стінки можна зробити трохи тонше. Конструкція завантажувального бункера гранично проста, і якщо ножі дробарки заточені правильно, то необхідність включення подпрессовщіка в конструкцію подає пристрої відпадає сама собою (самозахоплення деревини в цьому випадку і так буде на вищому рівні).
Монтуючи завантажувальний пристрій, найважче вибрати правильний кут його установки.
Багато з цим кутом граються: чим він крутіший, тим краще самозахоплення. Я його роблю величиною приблизно 120-130 градусів. Робота верстата при цьому мене цілком влаштовує.
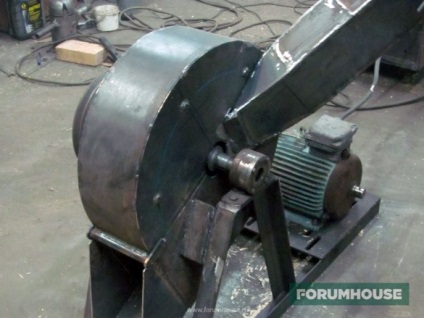
Металеве решето (сито), встановлене по внутрішньому колу кожуха, допомагає відсівати тирса необхідної фракції. Розмір отворів в полотні решета залежить від того, яку саме фракцію тріски ви бажаєте отримати. Визначається він частіше дослідним шляхом. Так, користувач Volodaris зробив отвори діаметром 20 мм, будучи заздалегідь готовим, при необхідності, змінити вказаний розмір.
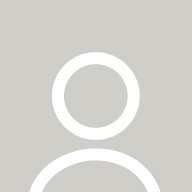
Патріот 777Пользователь FORUMHOUSE
Використовував сито з довгастими отворами - 10 * 50 мм.
Встановлюючи решето, обов'язково слід звернути увагу на величину робочих зазорів: між решетом і кожухом, а також між молоточками і ситом.
Що стосується просвіту між решетом і кожухом, то він повинен забезпечувати безперешкодний рух подрібненої маси, не допускаючи забивання дробарки тирсою. За його користувачів FORUMHOUSE, зазору величиною 10 см цілком достатньо для безперебійної роботи пристрою.
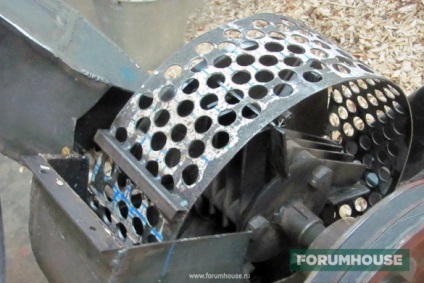
Що ж стосується зазору між бітами і решетом, то він повинен бути мінімальним. При цьому бажано, щоб молоточки по своїй довжині на пару сантиметрів виходили за діаметр подрібнювальної фрези.
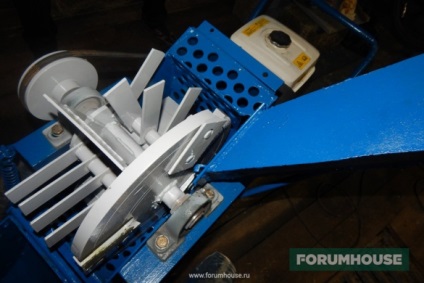
Пропонуємо вашій увазі простий і надійний спосіб кріплення решета до кожуха верстата.
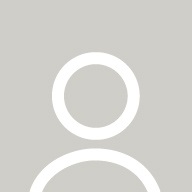
Volodaris Користувач FORUMHOUSE
По діаметру кожуха уварені болти, на які сито і лягає. Верхня частина кожуха точно такими ж болтами притискає сито. До ситу приварений обмежувач, який, спираючись в болти, не дозволяє решето обертатися.
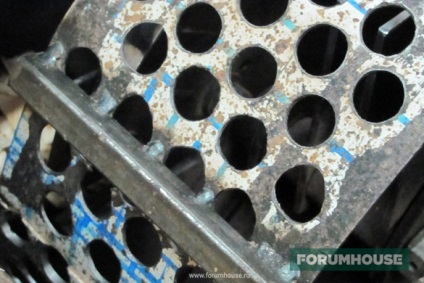
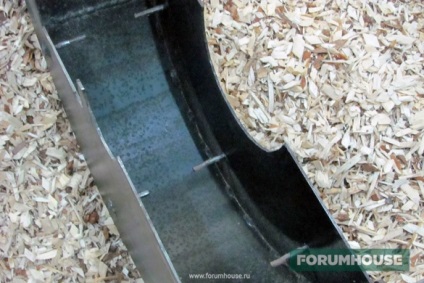