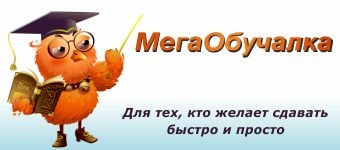
Головна | Про нас | Зворотній зв'язок
Супермаркет на заводі.
Виникнувши в супермаркеті, витягаюча система добре прижилася на виробництві. Це обумовлено тим, що вона дозволяє економити кошти на поповнення запасів. Навіщо купувати зайве і тримати на складі, якщо немає попиту. Коли ж клієнт робить замовлення, лінія створення продукції починає працювати. Отже, виникає потреба у сировину або комплектуючих, і постачальникам подається сигнал. Виявилося вигідніше купувати сировину і комплектуючі невеликими партіями. В цьому випадку вартість комплектуючих підвищується, але вивільняються заморожені кошти, скорочуються витрати на зберігання запасів, а також виробничі площі.
Ця система дозволила японцям, зокрема компанії «Тойота», уникнути багатьох істотних проблем, в тому числі проблему перевиробництва. Є сигнал з ринку - завод працює, немає сигналу - система завмерла в очікуванні. Зрозуміло, в повній мірі тільки на замовлення заводи не можуть працювати. Є прогнозування і попереднє планування, але виробнича система в цілому побудована саме за цим принципом. Причому попереднє планування спрямоване скоріше не на матеріально-технічний ресурс, а на людський: скільки робочих, в який період потрібно буде залучити додатково, якщо буде потрібно розширення виробництва в зв'язку з подальшим розвитком компанії.
Впровадження витягаючої системи передбачає, власне, принцип роботи Jast-in-time (точно вчасно), який спочатку застосовується всередині компанії. Отлаживаются всі процеси, в яких попередній ділянку виробництва - постачальник, а наступний - клієнт. Якщо всередині компанії ця система буде налаштована, це дасть очевидні переваги. Вибудовування потоку скоротить між операційні запаси, що зменшить час виробництва, збільшить оборотність коштів.
Проте, ця витягаюча система повністю не звільняє від запасів. Оскільки необхідно швидко реагувати на сигнал з ринку, на підприємстві все-таки є запас у вигляді незавершеного виробництва. По приходу замовлення потік моментально приводиться в дію, виробляючи потрібну кількість продукції.
В основному всі підприємства, що працюють за традиційною схемою, влаштовані за принципом виштовхує системи. Це звична практика давати графік роботи зверху для кожної виробничої ділянки виходячи із загального плану. Кожен виробнича дільниця прагне сам по собі досягти встановлених показників: потрібен, не потрібен сусідній ділянці на даному етапі часу продукт, він виштовхується на наступний етап обробки. Крім того, якщо не організований потоковий метод (зробив одну деталь - передай по лінії), а продукт обробляється партіями, час на виробництво одиниці продукту, в залежності від величини партії, збільшується в геометричній прогресії.
Для наочності можна провести простий експеримент. Завдання зробити партію з п'яти продуктів. В даному випадку це будуть п'ять листків паперу, на кожному з яких повинні бути написані імена кожного з трьох учасників експерименту. Перший варіант організації нашого експериментального виробництва: першого по черзі учаснику дається п'ять листків. Він повинен на кожному з них написати своє прізвище та тільки після цього передати комплект далі. І так, поки партія не побуває в руках кожного з учасників. Другий варіант: знову ж на п'яти аркушах учасники експерименту пишуть своє ім'я, але передають один одному аркуші по одному (написав прізвище на одному листку - передав його іншому). Час виробництва партії листків паперу з іменами в обох випадках змиритися. Очевидно, що в результаті процес, що відбувається за другою схемою, реалізується в рази швидше.
Незбалансованість обладнання призводить до того, що виникають, з одного боку, простої через брак сировини внаслідок швидкої роботи однієї ділянки, з іншого боку, менш ефективна ділянка не справляється з обробкою продукту, утворюється міжопераційний запас, витрати ресурсів. Зрештою, це призводить до необгрунтованих втрат, про які в більшості випадків навіть не замислюються. Причому кожна ділянка тримає кругову оборону, заявляючи, що з виконанням плану справляється, але підприємство в цілому працює неефективно, несе великі збитки.
Робота з одиницями продукту по витягаючої системі прискорює проходження вироби по потоку. Втрати в часі виробництва, зайвих запасах, які складають партії виробів, крім того, невідомо, а чи потрібна буде ця партія в кінці обробки, чи буде вона затребувана клієнтом.
Kanban і настройка системи
В процесі впровадження витягаючої системи виникло питання: а як повідомити про те, що комплектуючі під кінець і потрібно поповнення запасу. Стало очевидно, що необхідно розробити якусь сигнальну систему, яка б дозволяла стежити за тим, що, на яких ділянках виробництва і в якій кількості потрібно. Тоді і була розроблена система Kanban, що в перекладі з японської означає «картка». (Слово дається в латинській транскрипції). Власне, на японських заводах використовували саме картки, на яких була прописана інформація про поповнення запасів.
Згодом Kanban трансформувався, приймаючи різноманітні форми. Це може бути просто порожній контейнер, місце, окреслене на підлозі, ящичок, куди кладуть відповідні заявки, або рівень, позначений у контейнері або ящику, досягнення цього рівня означає, що пора підвозити комплектуючі або сировину.
Після впровадження Kanban всередині підприємства був розроблений Kanban для постачальника. Сировиною, ні комплектуючими стали поставлятися лише за сигналом з виробництва, що дозволило значно скоротити запаси сировини, а запаси готової продукції на складі звести практично до нуля. Відповідно вивільнилися ресурси, підвищилася ефективність роботи компанії, зросла прибуток. Збільшилася оборотність коштів за рахунок скорочення запасів і часу виконання замовлення, оскільки були виключені простої через брак комплектуючих.
Для того щоб організувати систему Kanban всередині підприємства, необхідно, по-перше, вибудувати якийсь потік, тобто такий стан роботи всіх підрозділів, коли продукція без затримки передається з однієї ділянки на іншу, а по-друге, дотримати баланс роботи обладнання і кожного окремого процесу в цьому потоці. Крім того, слід організувати процес створення продукту таким чином, щоб не накопичувалися між операційні запаси. Зробив одну деталь - передай далі! Це допоможе скоротити час проходження продукту по ділянках в два і більше разів.
Чи не на всіх підприємствах є можливість відразу вибудувати безперервну лінію між ділянками виробництва. Існують проблеми з переналагодження обладнання для виготовлення іншої продукції або використовується старе обладнання, яке не можна часто переналагоджувати.
Деякі потоки залежать від сировини, від плавки в разі металургійного виробництва, де є певні технологічні процеси, що є обмеженням можливості вибудувати потік. Наприклад, виробництво всієї продукції Ярославського шинного заводу залежить від того цеху, де варять гуму по досить складною технологією. На таких ділянках створюється жорстко контрольований склад, умовно званий супермаркет, на якому тримається оптимальний запас сировини, заготовок або незавершеної продукції, щоб система могла працювати без затримок (в нашому випадку така ділянка може бути на етапі упаковки товару, де будуть всі види упаковки). Потік ж вибудовується від того ділянки, де починається виробництво будь-якого продукту.
Є певні обмеження по технологічних особливостях роботи обладнання. Наприклад, якщо ми замовляємо скляну тару, то обладнання може призвести мінімальну партію в 50 тис. Пляшок. Якщо говорити про складальному процесі, безумовно, вибудувати потік можна, і це дасть відчутні результати. Ідеальний приклад організації виробництва на деяких підприємствах компанії «Дженерал Електрик» потік влаштований за допомогою оснастки, яка за формою нагадує підкову. Перший працівник бере таку оснастку, надягає на неї деталь, проводить свою операцію і передає оснащення з деталлю наступному працівникові. Коли деталь проходить весь цикл, виріб знімається і передається на етап упаковки, а оснащення по конвеєру повертається до початку потоку. Жодного зайвого руху. Ящики з деталями стоять на картонних коробках, щоб деталі були на зручному для руки рівні, щоб не відволікатися від процесу і витрачати на нього мінімальний час (це відноситься до ефективної організації робочого місця, про важливість і практичну реалізацію). Підприємство працює за такою системою вже вісім років. Удосконалення виробництва відбувається безперервно. Робочі площі скоротилися на 70%, а обсяг продукції, що випускається при цьому виріс.