З феритних сталей виготовляють обладнання азотно-кислотних заводів (ємності, труби).
Для підвищення механічних властивостей феритних хромистих сталей в них додають 2 ... 3% нікелю. Стали 10Х13Н3, 12Х17Н2 використовуються для виготовлення важко навантажених деталей, що працюють в агресивних середовищах.
Після гарту від температурі 1000 o C і відпустки при 700 ... 750 o С межа плинності сталей становить 1000 МПа.
Термічну обробку для феритних сталей проводять для отримання структури більш однорідного твердого розчину, що збільшує корозійну стійкість.
Стали аустенітного класу - високолеговані хромонікелеві стали.
Нікель - аустенітообразующій елемент, сильно знижує критичні точки перетворення. Після охолодження на повітрі до кімнатної температури має структуру аустеніту.
Нержавіючі сталі аустенітного класу 04Х18Н10, 12Х18Н9Т мають більш високу корозійну стійкість, кращі технологічні властивості в порівнянні з хромисті нержавіючими сталями, краще зварюються. Вони зберігають міцність до більш високих температур, менш схильні до зростання зерна при нагріванні і не втрачають пластичності при низьких температурах.
Хромонікелеві стали корозійностійкої в окислювальних середовищах. Основним елементом є хром, нікель тільки підвищує корозійну стійкість.
Для більшої гомогенності хромонікелеві стали піддають загартуванню з температури 1050 ... 1100 o C в воді. При нагріванні відбувається розчинення карбідів хрому в аустените. Виділення їх з аустеніту при загартуванню виключено, так як швидкість охолодження велика. Отримують межа міцності = 500 ... 600 МПа, і високі характеристики пластичності, відносне подовження = 35 ... 45%.
Упрочняют аустенітні стали холодною пластичною деформацією, що викликає ефект наклепу. Межа плинності при цьому може досягти значень 1000 ... 1200 МПа, а межа міцності - 1200 ... 1400 МПа.
Для зменшення дефіцитного нікелю частина його замінюють марганцем (сталь 40Х14Г14Н3Т) або азотом (сталь 10Х20Н4АГ11).
Аустенітно-ферритні стали 12Х21Н5Т, 08Х22Н6Т є замінниками хромонікелевих сталей з метою економії нікелю.
Властивості сталей залежать від співвідношення феритної і аустенітної фаз (оптимальні властивості отримують при співвідношенні - Ф: А = 1: 1). Термічна обробка сталей включає загартування від температури 1100 ... 1150 o C і відпустку-старіння при температурі 500 ... 750 o C.
Аустенітно-ферритні стали не схильні до корозійного розтріскування під напругою: тріщини можуть виникати тільки на аустенітних ділянках, але ферритні ділянки затримують їх розвиток. При кімнатних температурах аустенитно-ферритні стали мають твердість і міцність вище, а пластичність і ударну в'язкість нижче, ніж сталі аустенітного класу.
Жаростійкість, жаростійкі сталі і сплави.
Жаростійкість (окалиностойкость) - це здатність металів і сплавів чинити опір газової корозії при високих температурах протягом тривалого часу.
Якщо виріб працює в окислювальному газовому середовищі при температурі 500..550 o C без великих навантажень, то досить, щоб вони були тільки жаростійкими (наприклад, деталі нагрівальних печей).
Сплави на основі заліза при температурах вище 570 o C інтенсивно окислюються, так як утворюється в цих умовах на поверхні металу оксид заліза (вюстит) з простою гратами, що має дефіцит атомів кисню (твердий розчин віднімання), не перешкоджає дифузії кисню і металу. Відбувається інтенсивне утворення тендітної окалини.
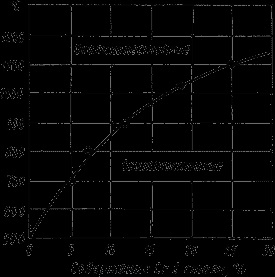
Мал. 20.2. Вплив хрому на жаростійкість хромової сталі
Для підвищення жаростійкості до складу стали вводять елементи, які утворюють з киснем оксиди з щільним будовою кристалічної решітки (хром, кремній, алюміній).
Ступінь легування стали, для запобігання окислення, залежить від температури. Вплив хрому на жаростійкість хромової сталі показано на ріс.20.2.
Високої жаростойкостью мають сільхроми, сплави на основі нікелю - ніхроми, стали 08Х17Т, 36Х18Н25С2, 15Х6СЮ.
Жароміцність, жароміцні стали і сплави
Жароміцність - це здатність металу чинити опір пластичної деформації і руйнування при високих температурах.
Жароміцні матеріали використовуються для виготовлення деталей, що працюють при високих температурах, коли має місце явище повзучості.
Критеріями оцінки жароміцності є короткочасна і тривала міцності, повзучість.
Короткочасна міцність визначається за допомогою випробувань на розтяг розривних зразків. Зразки поміщають в піч і відчувають при заданій температурі. Позначають короткочасну міцність =, напрімер300oС = 300МПа.
Міцність залежить від тривалості випробувань.
Межею тривалої міцності називається максимальна напруга, яке викликає руйнування зразка при заданій температурі за певний час.
Наприклад = 200 МПа, верхній індекс означає температуру випробувань, а нижній - задану тривалість випробування в годинниках. Для котельних установок потрібно невисоке значення міцності, але протягом декількох років.
Повзучість - властивість металу повільно пластично деформуватися під дією постійного навантаження при постійній температурі.
При випробуваннях зразки поміщають в піч із заданою температурою і прикладають постійне навантаження. Вимірюють деформацію індикаторами.
При звичайній температурі і напружених вище межі пружності повзучість не спостерігається, а при температурі вище 0,6Тпл. коли протікають процеси знеміцнення, і при напружених вище межі упругостінаблюдается повзучість.
Залежно від температури швидкість деформації при постійному навантаженні виражається кривою складається з трьох ділянок (рис. 20.3):
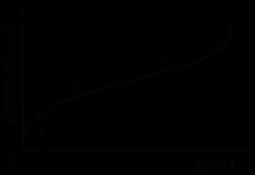
Мал. 20.3. крива повзучості
ОА - пружна деформація зразка в момент прикладання навантаження;
АВ - ділянка, відповідний початкової швидкості повзучості;
ВС - ділянку сталої швидкості повзучості, коли подовження має постійну швидкість.
Якщо напруги досить великі, то протікає третя стадія (ділянка СД), пов'язана з початком руйнування зразка (утворення шийки).
Для вуглецевих сталей повзучість спостерігається при нагріванні вище 400 o С.
Межа повзучості - напруга, яке за певний час при заданій температурі викликає задане сумарне подовження або задану швидкість деформації.
НапрімерМПа, де верхній індекс - температура випробування в o С, перший нижній індекс - задане сумарне подовження у відсотках, другий - задана тривалість випробування в годинниках.
Класифікація жароміцних сталей і сплавів
При температурах до 300 o C звичайні конструкційні стали мають високу міцність, немає необхідності використовувати високолеговані стали.
Перлітні жароміцні стали. До цієї групи належать котельні стали і сільхроми. Ці стали застосовуються для виготовлення деталей котельних агрегатів, парових турбін, двигунів внутрішнього згоряння. Стали містять відносно мало вуглецю. Легування сталей хромом, молібденом і ванадієм виробляється для підвищення температури рекристалізації (марки 12Х1МФ, 20Х3МФ). Використовуються в загартованому і високоотпущенном стані. Іноді загартування заміняють нормалізацією. В результаті цього утворюються пластинчасті продукти перетворення аустеніту, які забезпечують більш високу жароміцність. Межа повзучості цих сталей повинен забезпечити залишкову деформацію в межах 1% за час 10000 ... 100000 ч роботи.
Перлітні стали володіють задовільною зварюваністю, тому використовуються для зварних конструкцій (наприклад, труби пароперегрівачів).
Для виготовлення жароміцних деталей, які не потребують зварювання (клапани двигунів внутрішнього згоряння), застосовуються хромокремністие стали - сільхроми: 40Х10С2М, 40Х9С2, Х6С.
Жароміцні властивості зростають зі збільшенням ступеня легування. Сільхроми піддаються загартуванню від температури близько 1000 o С і відпуску при температурі 720 ... 780 o С.
При робочих температурах 500 ... 700 o C застосовуються сталіаустенітного класу. З цих сталей виготовляють клапани двигунів, лопатки газових турбін, соплові апарати реактивних двигунів і т.д.
Основними жароміцними аустенітних сталей є хромонікелеві стали, додатково леговані вольфрамом, молібденом, ванадієм і іншими елементами. Стали містять 15 ... 20% хрому і 10 ... 20% нікелю. Мають жароміцністю і жаростійкістю, пластичні, добре зварюються, але ускладнена обробка різанням і тиском, охрупчиваются в інтервалі температур близько 600 o С, через виділення по границях різних фаз.
За структурою стали поділяються на дві групи:
2. Аустенітні стали з гетерогенною структурою 37Х12Н8Г8МФБ, 10Х11Н20Т3Р.
Термічна обробка сталей включає загартування з 1050 ... 1100 o С. Після гарту старіння при температурі вище експлуатаційної (600 ... 750 o С). В процесі витримки при цих температурах в дисперсному вигляді виділяються карбіди, карбонітриди, внаслідок чого міцність стали підвищується.
Деталі, що працюють при температурах 700 ... 900 o C, виготовляють з сплавів на основі нікелю і кобальту (наприклад, турбіни реактивних двигунів).
Нікелеві сплави переважно застосовують в деформованому вигляді. Вони містять більше 55% нікелю і мінімальна кількість вуглецю (0,06 ... 0,12%). За жароміцним властивостями перевершують кращі жароміцні стали.
За структурою нікелеві сплави поділяють на гомогенні (ніхроми) і гетерогенні (німонік).
Ніхроми. Основою цих сплавів є нікель, а основним легуючим елементом - хром (ХН60Ю, ХН78Т).
Ніхроми не володіють високу жароміцних, але вони дуже жаростойки. Їх застосовують для малонавантажених деталей, що працюють в окисних середовищах, в тому числі і для нагрівальних елементів.
Німонік є четвертними сплавами нікель - хром (близько 20%) - титан (близько 2%) - алюміній (близько 1%) (ХН77ТЮ, ХН70МВТЮБ, ХН55ВМТФКЮ). Використовуються тільки в термічно обробленому стані. Термічна обробка складається з гарту з 1050 ... 1150 o С на повітрі і відпустки - старіння при 600 ... 800 o С.
Збільшення жароміцності сложнолегірованних нікелевих сплавів досягається зміцненням твердого розчину введенням кобальту, молібдену, вольфраму.
Основними матеріалами, які можуть працювати при температурах вище 900 o C (до 2500 o С), являютсясплави на основі тугоплавких металів - вольфраму, молібдену, ніобію та інших.
Температури плавлення основних тугоплавких металів: вольфрам - 3400 o С, тантал - 3000 o С, молібден - 2640 o С, ніобій - 2415 o С, хром - 1900 o С.
Висока жароміцність таких металів обумовлена великими силами міжатомних зв'язків в кристалічній решітці і високими температурами рекристалізації.
Найбільш часто застосовують сплави на основі молібдену. Як легуючі добавок в сплави вводять титан, цирконій, ніобій. З метою захисту від окислення проводять силицирование, на поверхні сплавів утворюється шар MoSi2 товщиною 0,03 ... 0,04 мм. При температурі 1700 o С Силіційованний деталі можуть працювати 30 годин.
Вольфрам - найбільш тугоплавкий метал. Його використовують як легуючий елемент в сталях і сплавах різного призначення, в електротехніці і електроніці (нитки розжарення, нагрівачі в вакуумних приладах).
Як легуючі елементів до вольфраму додають молібден, реній, тантал. Сплави вольфраму з ренієм зберігають пластичність до -196 o С і мають межу міцності 150 МПа при температурі 1800 o С.
Для сплавів на основі вольфраму характерна низька жаростійкість, плівки утворюються оксидів перевищують обсяг металу більш, ніж в три рази, тому вони розтріскуються і відшаровуються Виготовляють вироби, що працюють в вакуумі).