Методи виявлення тріщин і прихованих дефектів в деталях і вузлах машин і устаткування
Мета роботи.
1. Вивчити методи виявлення тріщин і прихованих дефектів в деталях машин.
2. Дати висновок про можливість подальшого використання деталі або призначити спосіб усунення виявленого дефекту.
Завдання.
1. Ознайомитися з пристроєм устаткування, стендів, приладів і пристосувань.
2. Вивчити послідовність виконання операцій по виявленню поверхневих і внутрішніх тріщин в деталях машин.
3. Придбати практичні навички виявлення прихованих дефектів в деталях, що мають різні конфігурацію, матеріал і умови роботи.
4. Дати короткий опис способу усунення дефекту або висновок про придатність деталі.
На практиці застосовують такі методи:
1) магнітний;
2) флуоресцентний;
3) травлення деталі кислотою;
4) змочування поверхні деталі гасом з подальшою крейдяний обмазкою;
5) гідравлічний;
6) пневматичний;
7) нагрівання деталі;
8) перевірки електричної міцності деталі;
9) ультразвукової.
Вибір того чи іншого методу дефектів обумовлюється конфігурацією і матеріалом деталі, а також вірогідним розташуванням дефекту.
Магнітний метод застосовується для контролю деталей будь-якої конфігурації і розмірів, виготовлених з феромагнітних сплавів (сталь, чавун). Він відрізняється досить високою точністю, швидкістю виконання операцій, простотою пристрої апаратури.
При намагнічуванні деталі в місцях, де є дефект, магнітні силові лінії утворюють потік розсіювання. На кордонах дефекту виникають магнітні полюси, і величина магнітного потоку змінюється. Після короткочасного занурення деталі в суспензію з порошку і масла легко виявити місця розташування дефекту по осілим частинкам порошку. Дефект в деталі можна виявити також за допомогою вишукувальних котушок і вимірювальних приладів.
Деталі, виготовлені з термічно оброблених або легованих сталей, перевіряють за залишковим магнетизму, занурюючи в суспензію після відключення намагнічує апарату.
Деталі з невисокою твердістю, а також мають поверхневі тріщини відчувають під час їх намагнічування. Перед установкою на намагнічує прилад деталі, що має наскрізний отвір (пружини, втулки, підшипники кочення і ін.), Необхідно вставити в нього мідний стержень.
Розрізняють циркулярний, поздовжнє і комбіноване намагнічнва-ня деталей.
При циркулярному намагничивании виявляють поздовжні і косо розташовані тріщини (кут між напрямком магнітного потоку і тріщиною повинна бути не менше 20 °).
Величину намагнічує струму при циркулярному намагничивании вибирають, виходячи з співвідношень:
а) при контролі на залишкової намагніченості
б) при контролі в магнітному полі
При поздовжньому намагнічуванні напруженість магнітного поля повинна бути в півтора рази більше, ніж при циркулярному намагничивании.
Для визначення дефектів при циркулярному намагничивании деталь встановлюють між мідної плитою і контактної пластиною і затискають рукояткою приладу. Включають трансформатор або спеціальний акумулятор, при цьому напруга повинна становити 4-8 В, а величина струму залежить від поперечного перерізу та матеріалу перевіряється деталі. Деталь намагничивают протягом 1-2 с, потім відключають джерело струму і звільняють її. Занурюють деталь на 1-2 хв в ванну з суспензією, що складається з дрібнодисперсного порошку прокаленной окису заліза (крокусу) і трансформаторного масла (співвідношення обсягів порошку і масла 1. 40). Зовнішнім оглядом поверхні деталі по концентрації порошку уздовж тріщини визначають місце розташування і характер дефекту, промивають її в чистому трансформаторному маслі і проводять розмагнічування, поміщаючи деталь всередину котушки соленоїда, що живиться від мережі змінного струму, або на індукційному апараті типу ППЯ (модель 533).
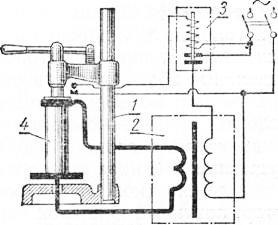
Мал. 12. Схема магнітної дефектоскопічної установки:
1 - прилад для циркулярного намагнічування; 2 - трансформатор; 3 - магнітний пускач; 4 - деталь.
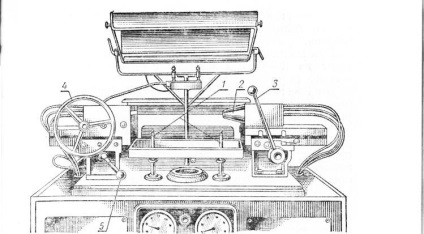
Мал. 13. Універсальний магнітний дефектоскоп типу МДВ:
1 - призми; 2 - полюсний наконечник; 3 - рукоятка; 4 - маховик; 5 - затискний механізм.
Внутрішні пошкодження будь-якого напрямку в деталях виявляють на універсальному магнітному дефектоскопі МДВ (рис. 13).
При контролі на цьому приладі деталь кладуть на призми, ножною педаллю піднімають її до рівня полюсних наконечників електромагніту і рукояткою притискають до них. Затискним механізмом забезпечують щільність контакту деталі з наконечниками. Під час випробування повертають деталь маховиком.
Розмагнічують деталь в спеціальній камері магнітного дефектоскопа.
Флуоресцентний метод застосовують для контролю деталей зі сплавів кольорових металів і інструменту з пластинками з твердого сплаву. використовують його
і для контролю деталей з чорних металів, але в цьому випадку він більш складний і вимагає значних витрат часу.
При контролі очищену і знежирену деталь занурюють на 10-15 хв у ванну з флуоресцентної рідиною.
Ця рідина являє собою суміш 0,25 л трансформаторного масла, 0,5 л гасу, 0,25 л бензину і 0,25 г порошку дефектол.
Якщо флуоресцентну рідину наносять на поверхню деталі пензлем, то деталь також витримують, перш ніж приступити до наступної операції. Потім струменем холодної води під тиском приблизно 0,2 МПа видаляють з поверхні флуоресцентний розчин і просушують деталь. На контрольовану поверхню наносять дрібний сухий порошок силикагеля (Si02), витримують деталь на повітрі протягом 5-30 хв і потім видаляють надлишки порошку. Опромінюють перевіряється поверхню деталі ртутно-кварцовою лампою через світлофільтр УФС-3. Дефекти виявляють по яскравій зелено-жовтому світіння порошку силикагеля, просоченого флуоресцентним розчином, який розташовується по тріщині.
Метод виявлення тріщин травленням полягає в тому, що попередньо очищену і знежирену деталь протягом 3-5 хв протруюють в 10-20% -ному розчині сірчаної кислоти. За допомогою лупи 10-20-кратного збільшення або мікроскопа виявляють тріщину по слідах корозії на краях тріщини.
Метод виявлення тріщин за допомогою гасу і млявий обмазки включає наступні операції.
Очищену поверхню контрольованої деталі злегка змочують гасом і після 5-10 хв витримки протирають ганчір'ям. На перевіряється поверхню наносять крейдяне обмазку (крейда, розведений у воді до кашкоподібного стану) і сушать. Ударами дерев'яного молотка по суміжних ділянках деталі видавлюють залишки гасу з тріщини і по жовтій плямі на крейдяній обмазці виявляють прихований дефект.
Гідравлічний метод (опресовування) застосовують для визначення пошкоджень в корпусних деталях (блоці і голівці циліндрів, впускний і випускний трубі колектора) і в окремих вузлах машини (водяному радіаторі і ін.).
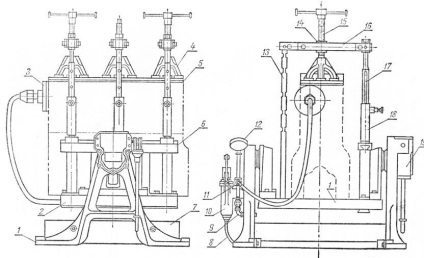
Мал. 14. Гідравлічне випробування блоку циліндрів на стенді КП-0406 J
1 - кронштейн; 2 - стіл; 3 - фланець з прокладкою і штуцером; 4 - натискний кронштейн; 5 - плита з гумовою прокладкою; 6 - паралелі столу; 7 - ванна; 8 - для огорожі трубка; 9 - зливна трубка з краном; 10 - поршневий насос; 11 - нагнітальна трубка з шлангом; 12 - манометр; 13 - розтяжка; 14-гайка; 15 - затискний гвинт; 16 - брус; 17 - висувна стійка кронштейна; 18 - кронштейн; 19 - поворотний механізм з рукояткою.
Блоки і головки циліндрів обпресовують на стендах КП-0406 (рис. 14). Для випробування колектора використовують спеціальні плити (рис. 15).
При установці деталей на стенд зовнішні отвори закривають кришками і заглушками. Стендовим насосом заповнюють сорочку блоку і внутрішні порожнини головки водою і створюють тиск 0,4-0,5 МПа. Тиск контролюють за манометром. Випробування проводять протягом 5 хв.
Постійність тиску і відсутність течі - ознака хорошої герметичності стінок сорочки блоку циліндрів і головки.
Пошкодження тракторного радіатора визначають на спеціальному стенді. Отвори баків радіатора заглушають пробками, плитами і фланцями з гумовими прокладками. Заповнюють радіатор водою і створюють в ньому тиск до 0,1 0,15 МПа. Випробування проводять протягом 1 хв. Виявлені місця пошкоджень відзначають фарбою, крейдою або чертилкой.
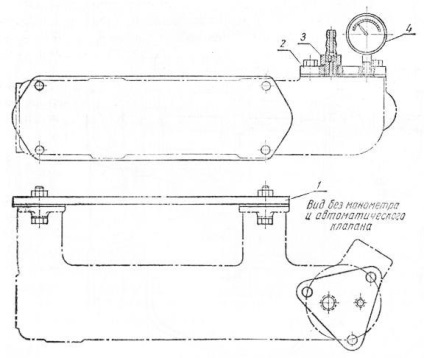
Мал. 15. Пристосування для гідравлічного випробування випускного колектора:
1 і 2 плити з гумовими прокладками; 3 = ш автоматичний клапан; 4 - манометр.
Пневматичний метод використовують для визначення пошкоджень в автомобільних радіаторах, шинах і паливних баках. Повітря під тиском 0,05-0,1 МПа подають всередину радіатора, зануреного в ванну з водою. За бульбашок повітря, що виходить виявляють дефекти.
Пошкодження паливного бака знаходять так. Ручним повітряним насосом всередину бака нагнітають повітря до тиску приблизно 0,1 МПа. На ділянки можливих тріщин (зварні шви, з'єднання штуцера з баком) наносять мильний розчин. Порушення герметичності виявляють по виступаючим в місцях пошкоджень бульбашок мильного розчину.
Метод нагріву деталі використовують для виявлення тріщин в тонкостінних герметично закритих деталях (наприклад, латунних поплавців карбюраторів). При цьому деталь поміщають в гарячу (^ = 80ч-90 ° С) воду. За виходять бульбашок нагрітого повітря встановлюють місце розташування тріщин.
Метод перевірки електричної міцності деталей використовують для виявлення тріщин в ізоляційних деталях електрообладнання і баках акумуляторів. Перевірку проводять за схемою, показаної на малюнку 16. Припинення іскроутворення в трьохелектродну розряднику стенду свідчить про наявність тріщини.
Ультразвуковий метод контролю заснований на здатності ультразвукових коливань (УЗК) поширюватися в металі на великі відстані у вигляді спрямованих пучків і відбиватися від дефектного ділянки деталі внаслідок різкої зміни щільності середовища, а отже, і акустичного опору (твір щільності середовища на швидкість УЗ К).
Звіт про роботу.
1. Обгрунтовують обраний метод контролю заданих деталей і в технологічній послідовності перераховують операції з виявлення прихованих дефектів.
2. Складають гідравлічну або електричну схему однієї з установок.
3. Призначають спосіб відновлення або дають висновок про придатність деталі.
Мал. 16. Перевірка бака акумулятора на наявність тріщини:
1 - бак акумулятора; 2 - іскровий розрядник; 3 - контакти.
До атегорія: - Практика ремонту машин