Монтаж сталевих трубопроводів
Сталеві трубопроводи, що прокладаються в траншеях, піддаються корозії і впливу блукаючих струмів (в міських умовах), що скорочує їх термін служби. Для захисту сталевих трубопроводів від корозії їх покривають ізоляцією, а при небезпеці наявності блукаючих струмів додатково застосовують методи електротехнічної захисту (дренажна, катодний, проекторна).
Роботи по ізоляції сталевих труб можуть виконуватися:
- на стаціонарній базі з подальшою ізоляцією місць зварних з'єднань в польових умовах;
- безпосередньо на трасі (магістральні трубопроводи).
Як ізоляційних матеріалів застосовують: нафтові бітуми, пластмасові покриття з полімерних липких стрічок та ін. Покриття з полімерних липких стрічок відзначаються високою захисною здатністю і можливістю механізації їх нанесення.
Безпосередньою ізоляції трубопроводу передує очищення поверхні від бруду, окалини, іржі, пилу та ін. Виконувана механізованим способом. Ізоляційні покриття складаються з грунтовки. одного або декілька шарів ізоляційного матеріалу (мастика, липка стрічка), армуючого (стеклохолст) і обгорткового шару (крафт-папір, брізол, гідроізол).
Особлива увага при ізоляції трубопроводів слід приділяти техніці безпеки (бітумну мастику наносять з температурою 160-180 ° на висохлу ґрунтовку!). Не можна наносити ізоляційні покриття на вологу поверхню, при снігопаді, дощі, сильний вітер і ін.!
Вплив блукаючих струмів на сталевий трубопровід полягає в тому, що в місцях дефектів ізоляції струми виходять з трубопроводу, який стає анодом (+) і активно руйнується в цих місцях. Завдання електротехнічної захисту перетворити трубопровід з анода в катод (принцип анодування - іони рухаються від анода до катода).
Основний спосіб з'єднання сталевих труб - зварювання, яка може бути електрична і газова. Фланцеве з'єднання!
Електричне зварювання стиків може бути ручна і автоматична (під шаром флюсу або в середовищі захищеного газу).
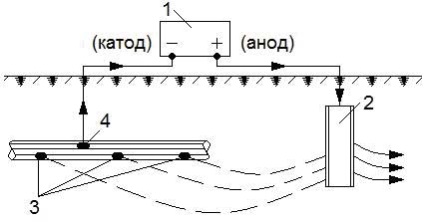
Схема дії катодного захисту:
1 - джерело постійного струму;
2 - заземлення;
3 - місця пошкодження ізоляції;
4 - під'єднання дренажу.
Перед зварюванням труби очищають від бруду (до металевого блиску очищають кромки (фаски) і докладають до них внутрішню і зовнішню поверхні на ширину не менше 10мм), перевіряють форму крайок, збіг торцевих поверхонь і т.д.
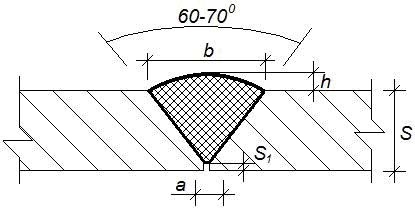
Зварювані труби (секції) укладають на лежання. Після редагування та очисти їх центрують з фіксацією необхідного зазору за допомогою центратору (зовнішнього або внутрішнього), виконують прихватку, а потім зварювання стиків (зварювання з поворотом або без повороту труб).
Міцність зварювальних стиків перевіряють механічними і фізичними методами, що природно простіше проводити в умовах заготівельної бази при складанні секцій (довжиною до 36м).
Доставка труб і секцій на трасу здійснюється автомобільними або тракторними трубопроводами та плетевозамі, які забезпечують збереження захисного покриття.
Вибір технології монтажу сталевого трубопроводу залежить від того ізольовані або неізольовані труби (секції) доставляються на трасу, які монтажні механізми є в розпорядженні будівельної організації.
Монтаж ізольованого трубопроводу може вестися:
- окремими трубами або секціями зі зварюванням і ізоляцією стиків в траншеї;
- збірка безперервної нитки трубопроводів з окремих труб або секцій (батогів) укладаються на підкладки над траншеєю;
- збірка безперервної нитки трубопроводу з окремих труб або секцій (батогів) на бермі.
В останньому випадку монтаж ведеться 3-4 кранами-трубоукладачами, розміщеними вздовж трубопроводу на відстані 20-40м один від одного (в залежності від діаметра труб) щоб не пошкодити трубопровід і його ізоляцію, захоплення трубопроводу здійснюють за допомогою м'яких рушників; підйом, переміщення і опускання трубопроводу із забезпеченням синхронної роботи кранів, що виключає ривки, удари, додаткові вигини.
При прокладанні магістральних трубопроводів раціонально роботи виконувати поєднаним методом, при якому очищення, ізоляція і укладання трубопроводу виконується однією комплексною бригадою, оснащеної кранами-трубоукладачами, самохідними очисними і ізоляційними машинами (ОМ та ІМ):
- трубопровід на бермі зварюється в безперервну нитку;
- на трубопровід встановлюються очисна і ізоляційна машини, його піднімають трубоукладачами за допомогою тролейних підвісок і починається рух всієї колони з виконанням всього комплексно-механізованого процесу.
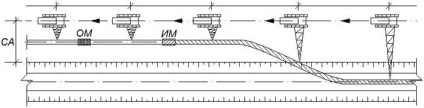
Фланцеве з'єднання сталевих труб застосовується при необхідності їх з'єднання з вузлами арматури (засувки, насоси та ін.) Або при виконанні робіт в умовах обмеженого простору і ін.
Застосування газового зварювання обмежена трубопроводами низького тиску, тому що при її виробництві відбувається вигоряння вуглецю, марганцю і кремнію з металу, що погіршує механічні, хімічні та фізичні властивості труб.
З групи лопатевих насосів насосів найбільш широке застосування знайшов відцентровий насос, що володіє багатьма цінними якостями. Він використовується практично у всіх галузях промисловості - водопостачанні, каналізації, системах опалення, будівництві, транспортуванні нафти по потужним трубопроводах, і особливо часто - в хімічній промисловості.
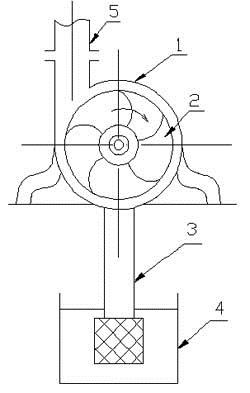
- Корпус спіральної форми (равлик);
- Робоче колесо з криволінійними лопатками;
- Всмоктуючий трубопровід з прийомним клапаном;
- Поживний резервуар;
- Нагнітальний трубопровід.
Передача енергії потоку рідини від електродвигуна здійснюється за допомогою робочого колеса 2. При обертанні робочого колеса рідина, що заповнює простір між лопатками, також приходить в обертання. Під впливом відцентрових сил, що розвиваються при цьому, рідина переміщається до периферії колеса. Одночасно збільшується окружна швидкість (пропорційна радіусу обертання). Далі рідина викидається в спіральний канал корпусу (равлика), в центрі робочого колеса при цьому виникає розрідження. Під дією утворився перепаду тисків (між атмосферним, чинним на вільну поверхню рідини в живильному резервуарі 4, і розрядження в центрі робочого колеса) рідина піднімається по всмоктуючому трубопроводу 3 і заповнює робоче колесо. Робоче колесо обертається безперервно з постійною частотою, тому рідина безперервно підсмоктується в робоче колесо і викидається з нього. Приріст енергії рідини в робочому колесі відбувається, в основному, за рахунок збільшення окружної швидкості (кінетичної енергії). Надалі кінетична енергія, отримана рідиною, частково перетвориться в потенційну (енергію тиску) в спіральному каналі корпусу (равлику), поперечний переріз якого поступово збільшується до вихідного патрубка. При цьому швидкість рідини знижується, а тиск зростає (відповідно до рівняння Бернуллі). Якщо швидкість рідини не знижувати, то це призведе до великих втрат напору в нагнітальному трубопроводі 5 (згадаємо, що втрати напору по довжині і в місцевих опорах при турбулентному русі пропорційні квадрату швидкості потоку), і отримана рідиною енергія в насосі буде витрачена на безцільні нагрів трубопроводів .
Відцентрові насоси перед пуском необхідно заповнювати рідиною, що перекачується. Для того, щоб рідина не йшла в живильний резервуар при заповненні насоса і всмоктуючого трубопроводу, на нижньому кінці всмоктувального трубопроводу встановлюють приймальний клапан, який пропускає рідину тільки в одному напрямку - до насоса. Якщо заповнення робочого колеса рідиною не проведено, атмосферне повітря, що має малу щільність у порівнянні з крапельної рідиною, не може бути викинутий з робочого колеса, в ньому не виникає розрядження, а значить і перепаду тисків, необхідного для процесу всмоктування.
Переваги та недоліки відцентрових насосів
Відцентрові насоси набули широкого поширення у всіх галузях промисловості, а в багатьох хімічних виробництвах повністю витіснили поршневі насоси. Це пояснюється їх великими чеснотами. до яких відносяться:
- Висока продуктивність і рівномірна подача.
- Простота конструкції, компактність, легкість з'єднання з приводом (відсутність передавальних механізмів - редукторів, варіаторів і т.д.)
- Простота регулювання і обслуговування.
- Можливість роботи на забруднених рідинах (відсутність клапанів, досить великі зазори між робочим колесом і корпусом).
- Відсутність інерційних сил при роботі насоса (робоче колесо обертається рівномірно), тому не потрібні важкі фундаменти.
- Висока надійність в роботі і довговічність.
Недоліками відцентрових насосів є:
- Малий створюваний напір (в одноступінчастої конструкції зазвичай не перевищує 50 м). Для створення найбільш високих напорів застосовують багатоступінчасті насоси, що мають кілька однакових коліс, що обертаються на загальному валу. Рідина, послідовно проходячи через всі колеса, отримує натиск, теоретично дорівнює сумі напорів, створюваних кожним робочим колесом. Однак, при переході з одного ступеня до іншої, рідина багаторазово змінює напрямок швидкості, тому відбуваються втрати енергії на місцеві опори і, як наслідок, зниження ККД. Крім того, конструкції багатоступеневих насосів набагато складніше одноступінчатих.
- Насоси не володіють властивістю самовсасиваемості (вимагають заливки рідиною, що перекачується перед пуском).
- Подача насоса залежить від опору мережі і в разі підключення додаткового споживача рідини і (або) збільшення загального опору мережі подача насоса зменшується.