Металізація. Методи нанесення металевих покриттів.
Металізація. покриття поверхні виробу металами і сплавами для повідомлення фізико-хімічних і механічних властивостей, відмінних від властивостей металізуюча (вихідного) матеріалу. Металлизацию застосовують для захисту виробів від корозії, зносу, ерозії, в декоративних і ін. Цілях. За принципом взаємодії металізуюча поверхні (підкладки) з наноситься металом розрізняють металлизацию, при якій зчеплення покриття з основою (підкладкою) здійснюється механічно - силами адгезії (див. Табл. Група 1), і металлизацию, при якій зчеплення забезпечується силами металевого зв'язку (група 2 ): з утворенням дифузійної зони на кордоні сполучаються поверхонь, за межами якої покриття складається з накладеного шару металу або сплаву (підгрупа 2а), і з освітою дифузійної зони в межах всього шару п окритія (підгрупа 2б).
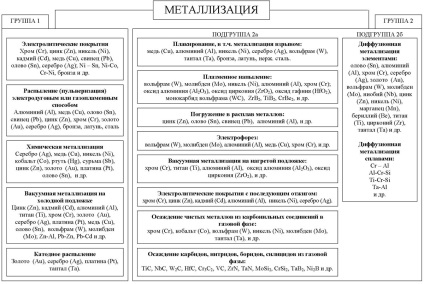
У цих процесах металлизация супроводжується зміною геометрії і розмірів виробу відповідно товщині шару наноситься металу або сплаву. Технологія металлизация за типом 2б передбачає дифузійне насичення металевими елементами поверхні деталей, нагрітих до високих температур, в результаті якого в зоні дифузії елементу утворюється сплав (Диффузионная металлизация). В цьому випадку геометрія і розміри металізуюча деталі практично не змінюються.
Металізація виробів за типом 1 виробляється в декоративних цілях, для підвищення твердості і зносостійкості, для захисту від корозії. Через слабкий зчеплення покриття з підкладкою цей вид металізації недоцільно застосовувати для деталей, що працюють в умовах великих навантажень і температур. Металізація деталей по типу 2 надає їм високу твердість і зносостійкість, високу корозійну і ерозійну стійкість, жаростійкість, необхідні теплофізичні і електричні властивості. Металізація за типом 2б застосовується для деталей, що зазнають дію значних механічних напружень (статичних, динамічних, знакозмінних) при низьких і високих температурах. Ці види металізації, за деяким винятком, використовуються для нанесення захисного шару на підкладки з різних металів, сплавів і неметалічних матеріалів (пластмаси, скла, кераміка, папір, тканини та ін.). Металізація знаходить застосування в електротехніці, радіоелектроніці, оптиці, ракетній техніці, автомобільної промисловості, суднобудуванні, літакобудуванні та ін. Областях техніки.
Гальванотехніка (гальваніка) - область прикладної електрохімії, що охоплює процеси електролітичного осадження металів на поверхню металевих і неметалевих виробів. Гальванотехніка включає: гальваностегію - отримання на поверхні виробів міцно зчеплених з нею тонких металевих покриттів; гальванопластику - отримання легко відділяються, щодо товстих, точних копій з різних предметів, т. н. матриць.
Суть методу полягає в зануренні покриваються виробів в водний розчин електроліту, головним компонентом якого є солі або інші розчинні сполуки - металопокриття. Покриваються вироби контактують з негативним полюсом джерела постійного струму, тобто є катодами. Анодами зазвичай служать пластини або прутки з того металу, якими покривають вироби. Вони контактують з позитивним полюсом джерела постійного струму і при проходженні електричного струму розчиняються, компенсуючи спад іонів, розряджається на покриваються виробах. Поряд з електрохімічним методом катодного осадження металів широке застосування знаходять і анодні методи електрохімічної обробки поверхні металів. До них слід віднести електрохімічне оксидування, травлення, полірування та ін. У всіх анодних процесах відбувається або розчинення металу, або перетворення поверхневого шару металу в оксидний або інший шар.
Всі процеси як гальванопластики, так і гальваностегії протікають в гальванічних ваннах. Часто гальванічної ванній називають також склад знаходиться в ній електроліту. Матеріалом ванни в залежності від її розмірів і ступеня агресивності електроліту можуть служити: кераміка, емальований чавун, сталь, футерованная свинцем або вініпласт, органічне скло та ін. Ємність ванн коливається від часток м (для золочення) до 10 м і більше. Розрізняють ванни: стаціонарні (покриваються вироби в яких нерухомі), напівавтоматичні (вироби обертаються або переміщаються по колу або подковообразно) і агрегати, в яких автоматично здійснюються завантаження, вивантаження і транспортування виробів уздовж ряду ванн. Постійний струм для електролізу отримують головним чином від селенових і кремнієвих випрямлячів, щільність струму регулюється за допомогою багатоступінчастого трансформатора.
Гальваностегія застосовується ширше, ніж гальванопластика; її мета надати готовим виробам або напівфабрикатів певні властивості: підвищену корозійну стійкість (цинкуванням, кадміюванням, лудінням, Свинцювання), зносостійкість поверхонь тертя (хромуванням, залізненням). Гальваностегія застосовується для захисно-декоративної обробки поверхні (досягається никелированием, хромуванням, покриттям дорогоцінними металами). Всі покриття в гальваностегії повинні бути міцно зчеплені з покриваються виробами; для багатьох видів покриттів це вимога повинна бути задоволена при будь-якого ступеня деформації основного металу. Міцність зчеплення між покриттям і основою забезпечується належною підготовкою поверхні покриваються виробів, яка зводиться до повного видалення оксидів і жирових забруднень шляхом травлення або знежирення. При нанесенні захисно-декоративних покриттів (срібних, золотих і т. П.) Необхідно видалити з поверхні виробів що залишилася від попередніх операцій шорсткість шліфуванням і поліруванням.
Гальванопластика полягає в процесі отримання металевих опадів бажаного виду і форми за допомогою електричного струму, через розкладання їм металевих розчинів. Гальванопластика переслідує дві мети: 1) отримання точних металевих копій з медалей, барельєфів, статуй і т. П. Предметів, а також і покривання тонким шаром металу - дерева, гіпсу, порцеляни й іншого. 2) осадження тонкого шару металів на поверхні інших металів з метою надати останнім більш красивий вигляд, захистити їх від окислення або, нарешті, зробити їх більш міцними.
Для отримання гальванопластіческіх виробів, що представляють копії з даних оригіналів, майже виключно користуються розчинами солей міді, рідше застосовується залізо. Мідь досить легко виділяється з її розчинів у вигляді рівного, щільного дрібнозернистого осаду, що зберігає найтонші відбитки форми; при цьому мідь повільно окислюється, і очищення її поверхні проводиться дуже легко. Гальванічний струм, проходячи через розчин солей міді, виділяє мідь на катоді, причому осад її дає точну копію (негативну) катода. Гальванопластичне осадження міді проводиться:
а) на металеві форми;
б) на предмети, що не проводять струму, які: гіпс, дерево, фарфор, скло і т. п .; поверхня робить їх проводять струм за допомогою металізації
в) точні копії з міді отримують, роблячи осадження на металізовані форми, відлиті з оригіналу з стеарину, гутаперчі і т. п. речовин.
При гальванопластичного осадженні міді на металеві оригінали останні попередньо очищаються і натираються м'якою щіткою графітом або будь-яким жирним речовиною майже насухо; операція ця має на меті полегшити відставання осаду міді від металевої форми.
Металізація поверхонь не проводять струм виробляється різними способами. Натирають м'якою щіткою подрібненим графітом або порошком для бронзування (поталу), поки поверхня не стане зовсім рівною і блискучою. Покривають форми розчином 1 частини білого фосфору і 4 частин сірчистого вуглецю і потім пензлем наносять розчин азотносеребряной солі (ляпіс); з останнього виділяється на поверхні тонкий шар металевого срібла. Іноді форму покривають (пензлем) розчином ляпісу і тримають її над чашкою, на водяній бані, - в чашці поміщений шматочок білого фосфору і налитий алкоголь; в цьому випадку, як і в попередньому, на поверхні виділяється тонка плівка металевого срібла. Предмети зі скла та порцеляни металлизируют іноді прямо сріблення мокрим шляхом (як дзеркала). Найчастіше гальванічне відтворення копій проводиться осадженням міді на негативні форми з непровідних струм речовин, які: гіпс, стеарин з воском, легкоплавкі металеві сплави, гутаперча і інші.
Метод хімічної металізації полягає в забезпеченні умов, при яких протікають окислювально-відновні реакції, що супроводжуються виділенням атомів металу, що мають більш високий стандартний окислювально-відновний потенціал. До хімічної металізації можна віднести методи отримання металевого шару шляхом термічного розкладання органічних сполук металів на поверхні полімерів.
Напилення. нанесення речовини в дисперсному стані на поверхню виробів і напівфабрикатів для повідомлення їм спеціальних фізико-хімічних, механічних, декоративних властивостей або для відновлення дефектної поверхні. Напиляним покриття утримується на поверхні в основному силами адгезії. Залежно від вихідного стану напилюються матеріалів і устаткування Напилювана пристроїв розрізняють наступним методи напилення. Газополум'яний, електродугової, порошковий, рідинний, парофазовий, плазмовий, лазерний, автотермоіонноеміссіонний. Зазначеними методами наносять метали (Ni, Zn, Al, Ag, Cr, Cu, Au, Pt та ін.), Сплави (сталь, бронзу та ін.), Хімічні сполуки (силіциди, бориди, карбіди, оксиди і ін.), неметалеві матеріали (пластмаси). Товщина напилюваного шару залежить від методу і режиму напилення і необхідних властивостей. Крім того, напиленням отримують тонкі епітаксіальні плівки, наприклад напівпровідникових матеріалів.
Плакірованіе (механо-термічний). Спосіб плакирования або облицювання полягає в тому, що на матрицю основного металу накладають з обох сторін (або з одного боку) листи іншого металу, потім весь пакет піддають гарячої прокатки, отримуючи в результаті дифузії на межах поділу металів міцне зчеплення між шарами. Таким способом сталь плакируют міддю, латунню, нікелем, міднонікелевого сплавами, алюмінієм, нержавіючою сталлю, отримуючи біметалічні матеріали. Товщина плакіровочного шару зазвичай становить 8-20% загальної товщини листа.
Термодіффузіонного покриття. Ці покриття мають порівняно високу корозійну стійкість і високу адгезію. Дифузійні покриття виходять в результаті насичення поверхневих шарів захищається металу атомами захищає металу і дифузії останніх у глибину захищається металу при високих температурах. У поверхневих шарах покривається металу зазвичай спостерігається утворення нових фаз хімічних сполук або твердих розчинів.
З дифузійних покриттів. що володіють високу корозійну стійкість і особливо жаростойкостью, представляють інтерес покриття алюмінієм (алитирование), кремнієм (термосіліцірованіе), хромом (термохромірованіе). Спостережуване при цьому значне підвищення жаростійкості виробів зумовлено утворенням на їх поверхні оксидів Al2O3, Cr2O3, SiO2 або змішаних оксидів, що володіють підвищеними захисними властивостями і перешкоджають подальшому окисленню металу.
Металізація зануренням в розплавлені метали (Гарячі покриття). Спосіб гарячого нанесення покриттів полягає в зануренні виробів у розплавлений метал. Можливості отримання покриття гарячим способом визначаються здатністю покривається металу смачиваться розплавленим металом покриття. Покриває метал, як правило, повинен мати нижчу температуру плавлення, ніж покриваються метал. До числа недоліків цього способу відноситься: велика витрата наноситься металу, нерівномірність покриття по товщині на виробах складної форми і т.д. Найбільш широко цей метод застосовується в промисловості для нанесення на вуглецеву сталь цинку, олова, свинцю.
При копіюванні інформації, прохання посилатися на джерело.