Визначення операції було дано вище. Операція містить одну або кілька установок.
Установка - частина операції, яка виконується при одному незмінному закріпленні оброблюваної заготовки.
Перехід - частина операції, що характеризується постійністю оброблюваної поверхні, робочого інструменту і режиму роботи верстата. Одночасну обробку декількох поверхонь деталі декількома інструментами прийнято вважати за один перехід. Переходи підрозділяються на проходи.
Прохід - частина переходу, яка здійснюється при одному робочому переміщенні інструменту в напрямку подачі. За один прохід знімають один шар металу.
Технологічний процес виготовлення якого-небудь виробу оформляється спеціальними документами. В СРСР введена Єдина система технологічної документації (ЕСТД), яка встановлює основні види технологічних документів. Основна мета ЕСТД - встановити на всіх підприємствах єдині правила оформлення, виконання та звернення технологічної документації. До технологічної документації відносяться маршрутні, операційні карти, карти ескізів і інші документи.
Маршрутна карта містить опис технологічного процесу виготовлення виробу по всіх операціях в технологічній послідовності із зазначенням даних про обладнання, оснащення, матеріальних і трудових нормативах. Операційна карта містить опис операцій технологічного процесу виготовлення виробу з розчленуванням їх по переходах, із зазначенням режимів роботи і даних про засоби технологічного оснащення.
Карта ескізів містить ескізи, схеми, таблиці, необхідні для виконання технологічного процесу, операції, переходу. Для виконання вимог, що пред'являються до обробленої деталі, призначається послідовність операцій виходячи з таких міркувань.
1. Обробку заготовки починають з операцій чорнової обробки, при виконанні яких знімаються найбільші шари металу. Це дозволяє, по-перше, відразу виявити дефекти заготовки. По-друге, при знятті найбільших зовнішніх шарів металу заготівля звільняється від внутрішніх напружень, що викликають деформації. При чорновій обробці потрібні значні сили різання, які можуть вплинути на точність остаточної обробки поверхні.
2. Обробку поверхонь, на яких можливі дефекти заготовок неприпустимі, слід вести на початку технологічного процесу при виконанні чорнових операцій.
3. Слід в першу чергу обробляти поверхні, при видаленні припуску з яких в найменшій мірі знижується жорсткість заготовки.
4. Чистові операції треба виконувати до кінця обробки, так як при цьому зменшується можливість пошкодження вже оброблених поверхонь.
5. Поверхні, у яких задана точність відносного розташування, необхідно обробляти в одній установці і однієї позиції.
6. Слід прагнути застосовувати метод концентрації операцій технологічного процесу, т. Е. Одночасного виконання більшого числа переходів, і використовувати комбіновані інструменти.
Порядок обробки валів залежно від необхідного квалитета вказано в табл. 14.
Таблиця 14 Порядок обробки валів різної точності
Квалітети по СТ РЕВ 144-75
Чорнове і чистове обточування з подальшим шліфуванням підвищеної точності або тонке точіння
Як настановних баз для валів використовуються центрові отвори на торцях валів, службовці для установки їх в центрах. На рис. 27 зображені дві форми центрових отворів. Отвори форми (рис. 27, а) роблять в деталях, які піддаються попередній обробці зі зниженою точністю розмірів. Отвори форми (рис. 27, б) застосовують для деталей, багаторазово встановлюються при обробці на верстаті, і деталей, які в процесі експлуатації піддаються ремонту шліфуванням і т. Д. Запобіжний конус з кутом 120 ° служить для захисту основного конуса від забоїн і полегшує підрізування торців. Центрові отвори роблять однаковими з обох кінців заготовки, навіть якщо діаметри кінцевих шийок різні. Такі отвори можуть виконуватися циліндричним свердлом діаметром d і зенковкой або спеціальними комбінованими свердлами. Центрування проводиться на спеціальних центровочних верстатах, на токарному верстаті в трикулачні патроні або на токарному верстаті з опорою заготовки на задній центр.
Перед установкою деталі на верстат центровий отвір заднього центру заповнюється мастилом, деталь встановлюється іншим центровим отвором на передній Центр, задня бабка посувається до упору заднього центру в центровий отвір деталі і закріплюється нерухомо. Потім маховичком піноль бабки посувається вліво, підтискає центр до необхідної величини і закріплюється рукояткою щоб уникнути довільного відходу.
Обертання деталі при обробці в центрах повідомляється диску приводу різних конструкцій. Патрони нагвинчуються на шпиндель токарного верстата і мають пристрої для захоплення деталі.
Мал. 27. Форми центрових отворів. а - без запобіжного конуса, б - із запобіжним конусом
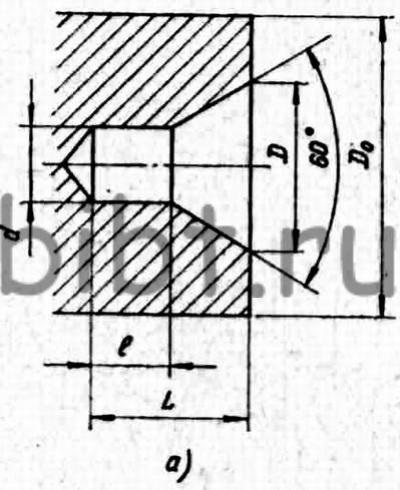
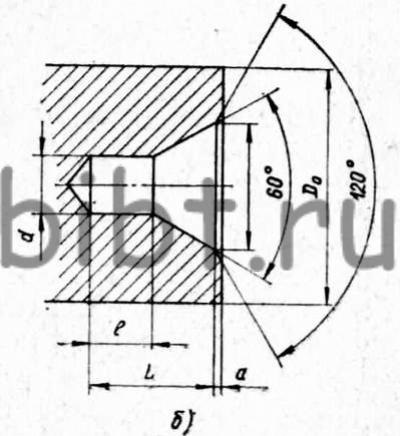
Мал. 28. Люнети. а - з кулачками, б - з підшипниками
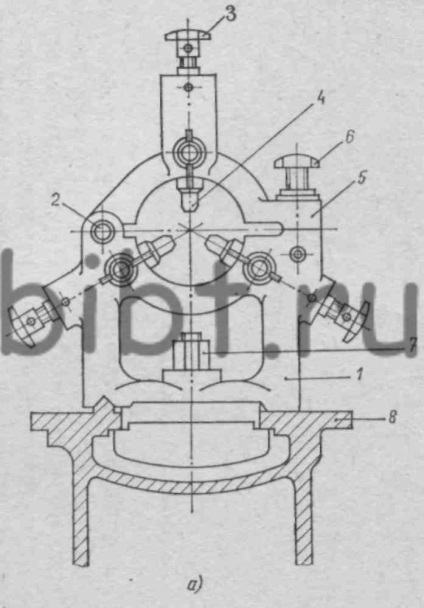
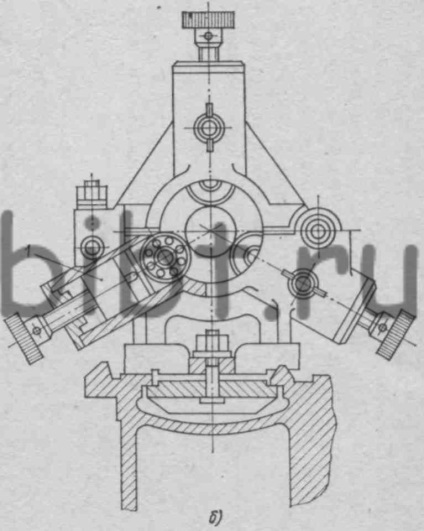
При обробці нежорстких валів, довжина яких в 10- 12 разів перевищує їх діаметр, для посилення жорсткості оброблюваного вала вводиться додаткова опора, яка називається люнетом (рис. 28 і рис. 29). При обточування довгих деталей рекомендується наступний порядок обробки: начорно обточити деталь до середини; переставити і обточити іншу половину; обробити начисто до середини; переставити і обробити начисто іншу половину.
Мал. 29. Рухомий люнет
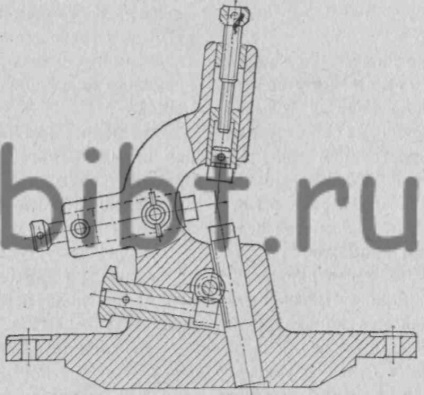
Деталі типу східчастих валиків виходять, як правило, гострінням з прокату. При цьому діаметр заготовки перевищує (на величину припуску) діаметр найбільшої ступені деталі. Обробку деталі можна вести різними способами:
а) обточувати всю заготовку по діаметру найбільшої ступені, потім цю заготовку за вирахуванням довжини найбільшою мірою по діаметру другого ступеня і т. д. до повної обробки всієї деталі. При такому методі шлях і час виходять найбільшими;
б) обточувати (якщо допустима така глибина різання) всю деталь, виключаючи найбільшу ступінь, по діаметру другого ступеня, потім найбільшу ступінь.
Найвища продуктивність виходить в тому випадку, коли весь припуск на обробку можна зняти за один прохід, т. Е. Спочатку обточується найменший діаметр, потім наступний і так до повної обробки. Обмеженням є допустима глибина різання.
Обточування виробів типу коротких втулок і дисків проводиться зазвичай при закріпленні їх в патронах різних конструкцій або на оправках, якщо вироби мають попередньо оброблене центральний отвір. Для цієї мети найбільш часто застосовується трикулачні самоцентруються патрон. У патроні можна затискати деталі як по зовнішній поверхні, так і по внутрішній. Патрон має велику універсальністю. При поздовжньому точінні в патроні треба стежити за тим, щоб виріб виступало з патрона якомога менше, щоб головний кут в плані різця був досить великим, а глибина різання і подання не були надмірно великими. Невиконання цих умов приведе до вигину виробу і до поломки різця.
Кріплення деталей, поверхня яких може бути пошкоджена розжареними кулачками патрона, повинно проводитися за допомогою розрізної втулки. При кріпленні диска, вужчого, ніж виступ кулачка, необхідно підкладати під деталь плоскопараллельное кільце.
Для обробки торцевих поверхонь і уступів заготовки закріплюють тими ж способами, що і при обробці зовнішніх циліндричних поверхонь.
Для підрізання торців і уступів застосовують різці: прохідний прямий, прохідний відігнутий, прохідний завзятий, а також спеціальний підрізної (торцевий).
Невеликі уступи підрізають прохідним завзятим різцем при поздовжньої подачі, причому підрізання уступу зазвичай поєднують з обточування зовнішньої поверхні.
Торець підрізають завзятим різцем при поперечної подачі з установкою ріжучої кромки під невеликим кутом (5-10 °) до торцевої поверхні.
При підрізання торця заготовки для закріплення її в патроні з підтиском заднім центром центровий отвір виконують за типом показаного на рис. 27, б або застосовують спеціальний зрізаний опорний нерухомий центр.
На зовнішніх поверхнях деталей часто протачивают канавки в кінці нарізного ділянки для виходу резьбонарезного інструменту, для установки стопорів, для розміщення кілець і т. Д. Канавки протачивают прорізними (Канавочні) різцями, а відрізання виконують відрізними різцями. Відрізними різцями або відрізають готову деталь, або розрізають заготовку на частини. Ширина ріжучої кромки відрізного різця залежить від діаметра оброблюваної заготовки і становить 3-8 мм. При виконанні відрізних робіт необхідно різець встановлювати точніше по осі заготовки.
В деталях типу втулок і дисків отвори циліндричної форми бувають гладкі, ступінчасті і з канавкою; отвори також можуть бути наскрізними і глухими.
Свердління забезпечує невисоку точність розміру (12 квалітет) і шорсткість тільки до Rz 80.
При свердлінні на токарному верстаті свердло, закріплене в пінолі задньої бабки, подають вручну, тільки обертанням маховичка. Максимальний діаметр повалення, що допускається верстатами 1К62 і 16К20, - 25 мм по сталі і 28 мм по чавуну. Щоб свердло не йшло від горизонтальної осі на початку свердління, торець заготовки попередньо засверливают коротким свердлом меншого діаметру, ніж просвердлюють отвір.
При свердлінні глибоких отворів (довжина яких перевищує діаметр в п'ять і більше разів) застосовують спеціальні «гарматні» свердла з прямою стружкової канавкою. Охолоджуюча рідина надходить від насоса до ріжучої кромці через наскрізний канал в свердлі, охолоджує ріжучу кромку і видаляє стружку.
Для підвищення точності і продуктивності при обробці отворів застосовують багатолезовий розточний інструмент - зенкер. Зенкером обробляють попередньо засверленние отвори. Припуск на зенкерование отворів залишають 0,5- 2 мм на сторону в залежності від діаметра отворів.
Для обробки отворів великого діаметра застосовують комбінований інструмент - свердло-зенкер. Фаски і конічні отвори під головки гвинтів обробляють зенковкой.
Попередньо просвердлені отвори або отвори в заготовках, отриманих литтям або куванням, з метою збільшення діаметра часто піддають розточування. Розточування - найбільш універсальний спосіб обробки отворів на токарному верстаті.
Розточувальні різці бувають прохідними - для наскрізних отворів і наполегливими - для глухих отворів. Розточувальний різець закріплюють у різцетримачі паралельно осі заготовки.
Отвори діаметром 80- 100 мм і більше зазвичай растачивают розточувальними різцями, які закріплюють в оправках.
Для точної чистової обробки отворів застосовують багатолезові розмірні інструменти - розгортки. Розгортка забезпечує 9-7 квалітети точності і шорсткості поверхні (середнє арифметичне відхилення профілю Ra = 6,3 мкм).
Технологічний процес виготовлення втулки в умовах одиничного виробництва виконується в одну операцію, яка складається з двох установок: спочатку заготовку обробляють з одного боку - обточують зовнішню поверхню, свердлять і розточують отвір, потім деталь закріплюють у кулачках за оброблену поверхню, обточують зовнішню поверхню, підрізають торець , знімають фаски і т. д.
В умовах серійного виробництва таку втулку доцільно виготовляти з штучних заготовок, попередньо відрізаних від прутка. В іншому технологічний процес обробки той же, що і в умовах одиничного виробництва.