Пайка в вакуумі і в відновлювальної атмосфері
При нагріванні металу до високих температур в звичайних умовах кисень повітря окисляє його поверхню, утворюючи окалину. Наявність оксидів ускладнює ведення процесу пайки. Для їх видалення і очищення поверхні при пайку на повітрі доводиться застосовувати спеціальні флюси. Однак пайка з флюсами, дозволяючи отримувати міцне з'єднання, не забезпечує захисту всієї поверхні деталі від окислення; тому після пайки доводиться піддавати деталі очищення від флюсу і окалини. Щоб уникнути цього, застосовують способи ізоляції нагрівається вироби від повітряного середовища, що дозволяють вести безокіслітельние процеси пайки. До них відносяться пайка в вакуумі і пайка в відновлювальної атмосфері.
Пайка в вакуумі. Як зазначалося вище, одним з достоїнств високочастотної пайки є можливість паяти в вакуумі. Перевага вакуумної пайки полягає в тому, що при нагріванні в середовищі, де відсутній кисень, не відбувається окислення металу, і для отримання якісної пайки немає необхідності користуватися флюсом. При правильному режимі нагріву в вакуумі партії деталей і строго визначеної витримці часу можна бути впевненим, що якість пайки буде у всіх деталей абсолютно однаковим.
Перший пристрій для пайки в вакуумі представляло собою круглий мідний стіл з відшліфованою поверхнею, на який могла встановлюватися підготовлена до пайки деталь. Деталь накривалася скляним ковпачком, щільно прилеглими своїми відшліфованими краями до поверхні столу. Для кращого ущільнення поверхню столу змащувалася технічним вазеліном. Через отвір в столі з-під ковпачка відкачувався повітря. При розрядці близько Ю-3 мм рт. ст. яке досягалося через кілька секунд, деталь була готова до пайки.
Розташований над скляним ковпачком індуктор при включенні генератора передавав енергію високої частоти в споюють деталь так само інтенсивно, як і при пайку на повітрі. На такому примітивному пристрої в лабораторії проф. В. П. Вологдина проводилися перші досліди по пайку у вакуумі деталей і ріжучого інструменту міддю і срібними припоями.
Трохи пізніше там же був створений верстат-автомат для пайки свічок запалювання двигунів внутрішнього згоряння (рис. 1). У спеціальних гніздах на масивному мідному поворотному столі, охлаждаемом водою, встановлювалися спаюється деталі, які зверху закривалися скляними ковпачками. При повороті столу простір, що знаходиться під знову встановленим ковпачком, поєднувалося за допомогою спеціальної системи каналів з вакуумним насосами, які і забезпечували там спочатку попередньо а датем і глибокий вакуум. Стіл з деталями за допомогою спеціальної приводної системи здійснював обертальний рух, періодично, через певні проміжки часу, повертаючись на деякий кут. У певному положенні ковпачок накривався кільцевим індуктором і в той же момент включався генератор. Деталь миттєво починала грітися. Після нагріву до необхідної температури і розплавлення припою індуктор підводився, нагрів вимикався і стіл пересувався на наступну позицію, після чого починався нагрів наступної деталі. Таким чином, деталі по черзі підходили до індуктора, де отримували порцію енергії, необхідну для розплавлення припою і отримання пайки. Після нагріву деталі охолоджувалися, передаючи тепло в мідний стіл, інтенсивно охолоджується водою. Після закінчення пайки простір під ковпачком ще якийсь час не поєднувалося з навколишнім повітрям, так як, якщо зняти ковпачок раніше, ніж деталь охолоне до температури 100-150 ° С, поверхня її окислиться і потемніє. Деталі ж, охолоджені в вакуумі, мають блискучу поверхню, як ніби вони тільки що пройшли полірування. Якість пайки деталей у вакуумі виходить виключно високим.
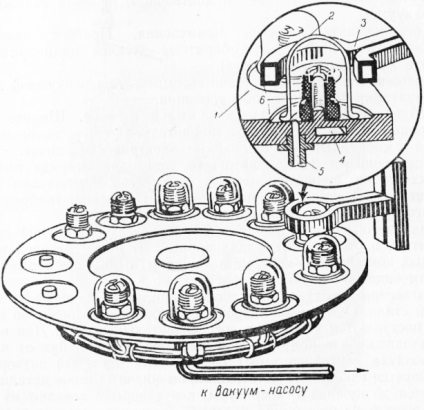
Мал. 1. Схема верстата-автомата для пайки деталей у вакуумі: 1 - мідний стіл; 2 - скляний ковпачок; 3 - індуктор; 4 - канал для водяного охолодження столу; 5 - канал для відкачування повітря; в - спаюється деталі
Незважаючи на ряд позитивних сторін процесу високочастотної пайки в вакуумі, область його застосування до теперішнього часу ще дуже обмежена.
До причин, що перешкоджає широкому використанню його в промисловості, слід віднести:
1) відносно низьку продуктивність процесу внаслідок штучного нагріву деталей і тривалого періоду охолодження їх у вакуумі;
2) обмежену сферу застосування. Процес придатний, в основному, для пайки малогабаритних деталей циліндричної форми в масовому виробництві;
3) складність створення верстатів-автоматів для вакуумної пайки і експлуатації вакуумного обладнання.
Пайка в відновної середовищі. Широко відомий процес пайки міддю в відновної середовищі, який проводиться в спеціально обладнаних електричних печах.
Істотними недоліками його, при наявності ряду позитивних сторін, є висока вартість обладнання та його дефіцитність. Печі, в яких проводиться паяння, вимагають тривалого часу нагрівання та охолодження.
З огляду на те, що спеціальні печі з відновлювальної середовищем дефіцитні, в окремих випадках роблять пайку деталей в спеціальних контейнерах, які завантажують у звичайні термічні печі, що мають високу температуру.
Контейнери представляють собою ящики, виготовлені з жаростійкої стали. Вони мають уварені трубки, по яких під час пайки надходять і видаляються відновлювальні гази. Для ізоляції знаходяться в контейнері деталей під час пайки від кисню повітря контейнер має спеціальний піщаний затвор або замазується глиною. Після закінчення часу, за яке деталі прогріваються до потрібної температури, контейнери витягують з печі і охолоджують, не припиняючи подавати відновну середу до тих пір, поки деталі не охолонуть.
Такий спосіб пайки дуже недосконалий, так як вимагає тривалого часу і дозволяє пропускати дуже мала кількість деталей при великій витраті енергії.
Більш продуктивним процесом є пайка в контейнерах з нагріванням струмами високої частоти (рис. 2). Цей різновид пайки лише умовно може називатися високочастотної, так як на відміну від того, що спостерігається при всіх інших способах високочастотного нагріву, тут струми майже не индуктируются в самій деталі, а нагрівають контейнер, який вже, в свою чергу, передає тепло в деталь через теплопровідність відновлювальної середовища. При цьому втрачається одна з переваг високочастотного нагріву - можливість розігрівати тільки потрібну зону деталі.
Цикл пайки деталей в контейнері з високочастотним нагріванням може бути скорочений у порівнянні з циклом пайки в печах в кілька разів. Це дозволяє застосовувати в якості припоїв не тільки мідь, але і латуні. При існуючих же способах пайки в відновної середовищі не можна було застосовувати в якості припою латуні, так як тривале нагрівання негативно позначався на їх властивості.
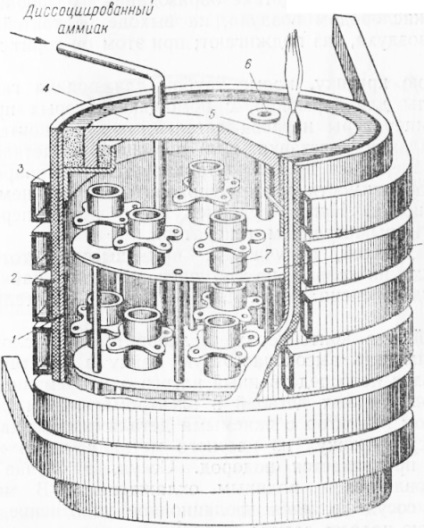
Мал. 2. Схема контейнера для високочастотної пайки в відновної середовищі з непрямим нагріванням деталей: 1 - корпус контейнера; 2 - шар теплоізоляції; 3 - індуктор; 4 кришка контейнера; 5 - трубка для подачі і відведення відновлювальної середовища; 6 - гніздо для термопар; 7 - споювали деталь; 8 - підставка
Контейнер з високочастотним підігрівом виготовляється шляхом зварювання з жароміцної листової сталі у вигляді бочки, який встановлюється на теплоизолирующее підставу. Контейнер поміщається в багатовитковому індуктор. Між індуктором і контейнером прокладається теплоізоляційний шар для зменшення втрат енергії на випромінювання. Дно контейнера роблять з неяк-ними гофрами для запобігання його від руйнування через термічних напружень під час багаторазових нагревов і охолоджень. Через верхню масивну кришку вводять і видаляють відновлювальні гази, в якості яких найкраще використовувати дисоційованому аміак.
Під час нагрівання під пайку і охолодження контейнера в нього повинен безперервно надходити газ. Для виключення можливості вибуху в приміщенні внаслідок утворення вибухонебезпечної суміші водню з киснем повітря, на виході з контейнера, після витіснення повітря, газ підпалюють; при цьому він горить жовтуватим полум'ям.
У верхню кришку, крім трубок для подачі газу, слід вварити чохли для термопар, за допомогою яких проводиться контроль температури нагрівання деталей; на дно контейнера кладеться спеціальна підставка для розміщення деталей. Нагрівання стінок контейнера весь час контролюється термопарою, яка в разі необхідності може управляти включенням і вимиканням установки. Нагрівання найзручніше вести періодичним включенням і вимиканням генератора.
Якість деталей, одержуваних при високочастотної пайку в контейнерах, анітрохи не поступається якості пайки деталей, виготовлених в спеціальних печах з відновлювальної атмосферою.
Крім пайки в контейнерах, в лабораторних условійх легко і просто застосовувати високочастотну пайку в відновної середовищі, використовуючи безпосереднє нагрівання одночасно однієї або декількох однотипних деталей в електромагнітному полі індуктора. При цьому індуктор з паяемимі деталями поміщається в спеціальну посудину - кожух з кольорового металу, через який під час пайки пропускається водень. Посудина, в разі необхідності, виготовляється з водяним охолодженням. У місці введення індуктора в посудину робиться ізоляційне ущільнення, що захищає внутрішню порожнину посудини від проникнення повітря, а індуктор від замикання висновків. Деталі в індуктор завантажуються через отвір, яке перед пропусканням газу герметично закривається кришкою з оглядовим вікном (рис. 3).
Заповнення посудини газом і поводження з ним проводиться так само, як і при застосуванні для пайки контейнерів з відновлювальної середовищем. Нагрівання деталей при пайку слід проводити на відпрацьованому режимі з певною витримкою часу, отриманої експериментальним шляхом. Подача газу припиняється після охолодження деталей до температури нижче 100-120 ° С, після чого вони можуть бути замінені наступними. При цьому процесі може бути застосований водень, одержуваний в умовах лабораторії в апараті кіп дією кислот на цинк з подальшим очищенням і відібранням вологи. Витрата газу і його тиск у посудині можуть бути незначними, проте вони повинні бути достатніми для того, щоб безперервно підтримувати горіння газу на виході. На вихідну трубку слід надіти скляний наконечник, наповнень мідної стружкою. Його призначення - перешкодити спалаху водню в посудині і тим забезпечити безпечні умови роботи. Істотним недоліком водню в якості відновлювальної середовища є його здатність утворювати з киснем повітря вибухові суміші, що вимагає при роботі великої уваги і точного дотримання інструкцій щодо поводження з воднем.
Незважаючи на свою малу продуктивність і обмежені можливості, пайка з безпосереднім нагріванням деталей є значно досконалішим процесом, ніж пайка з нагріванням деталей в контейнерах.
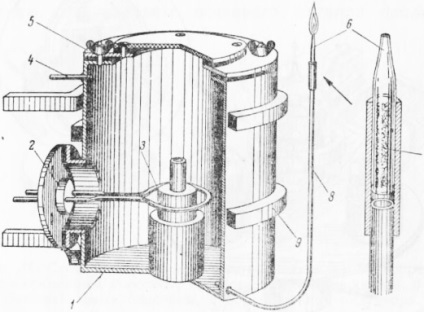
Мал. 3. Схема пристрою для високочасточной пайки в відновної середовищі з безпосереднім нагріванням деталей: 1 - посудина; 2 - ізоляційне ущільнення; 3 - індуктор з споюють деталлю; 4 - трубка для подачі газу; 5 - кришка посудини; 6 - запобіжний наконечник; 7 - мідна стружка; 8 - трубка для відводу газу; 9 - охолоджуюча трубка
На жаль до цього часу високочастотна пайка деталей у вакуумі і відновної середовищі не знайшла собі широкого застосування, хоча ці процеси є прогресивними технологічними процесами, такими, що заслуговують на велику увагу.
У пристроях подібного роду можна також виробляти пайку в середовищі нейтрального газу, наприклад аргону. Аргон захищає деталі під час нагрівання від окислення, створює більш сприятливі умови для змочування припоєм основного металу і затікання його в зазори. Бажано застосовувати аргон, що містить мінімальну кількість домішок, особливо кисню. Пайка в аргоні краще пайки на повітрі, але гірше пайки в водні, так як витрачається певна кількість флюсів і дає менш красиві з'єднання. Аргон щільніше повітря, сам не горить і горіння не підтримує, тому з ним зручно звертатися при пайку. Можна також легко здійснити пайку в аргоні дрібних деталей під скляними ковпачками, подібно до того, як це роблять у випадку пайки в вакуумі (рис. 4). Такий процес доцільно застосувати тоді, коли деталі мають внутрішні порожнини, що вимагають захисту від окислення при пайку. У цьому випадку подача газу може здійснюватися спеціальним розподільним пристроєм, розташованим в поворотному столі, через отвір під паяемой деталлю, з подальшим витіканням газу через носок у верхній частині скляного ковпачка.
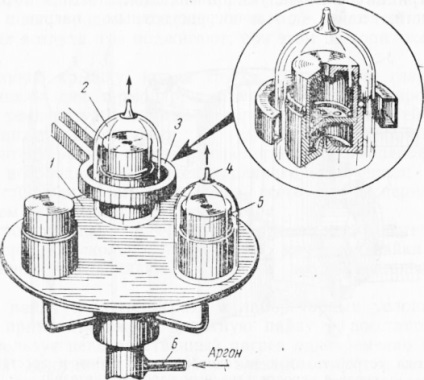
Мал. 4. Схема пристрою для пайки деталей в середовищі аргону: 1 - мідний стіл; 2 - скляний ковпачок; 3 - індуктор; 4 - носок ковпачка з отвором для виходу газу; 5 - спаюється деталі; 6 - трубка для продувки газу
Для тих же цілей при пайку деякого роду деталей на повітрі можна продувати аргон через внутрішні порожнини деталей, наприклад, при високочастотної пайку відповідальних паливних трубок високого тиску. Якщо дозволяють умови роботи і конструкція деталі, при відповідних запобіжних заходів, замість аргону можна застосувати водень, який забезпечує більш надійний захист від окислення внутрішньої поверхні деталі.