Перевірка і відновлення деталей верстатного обладнання з плоскими сполучаються поверхнями
Мета роботи.
1. Вивчити характерні знос основних деталей верстатного обладнання.
2. Освоїти методи і прилади для перевірки стану основних деталей і сполучень.
3. Вивчити технологічні способи відновлення зношених напрямних поверхонь основних деталей верстатів.
Завдання.
1. Ознайомитися з оснащенням робочого місця.
2. Вивчити характерні дефекти і знос токарно-вин-торезного верстата.
3. Перевірити знос і інші дефекти станини, шпинделя і деталей супорта.
4. Вивчити прилади та освоювати методи перевірки станини, шпинделя і кареток супорта.
5. Вибрати методи ремонту зношених поверхонь перевіряються деталей.
Оснащення робочого місця. Токарно-гвинторізний верстат з зносом робочих поверхонь деталей; станина токарного верстата з зношеними напрямними; рівні; косинці; лінійка повірочна; індикатори годинникового типу з державками; щуп-набір; місток універсальний для перевірки напрямних станини; автокалліматор; спеціальні і універсальні пристосування для перевірки напрямних форми «ластівчин хвіст»; контрольний кутник для перевірки перпендикулярності направляючих станини і кареток супорта; пристосування-підставка для контрольного кутника; оправлення для перевірки паралельності осі шпинделя і напрямних станини верстата; пристосування для перевірки паралельності ходових гвинтів і валів і напрямних станини; контрольні валики.
На деталях розібраного верстата виконують такі роботи.
Перевірка направляючої станини. На станині токарного верстата, встановленої на жорстких опорах, перевіряють прямолінійність, паралельність і вивернутися напрямних. Перевірку проводять за допомогою універсального містка або різних спеціальних пристосувань і приладів (лінійки, рівня, індикаторів з державками).
Універсальний місток (рис. 1) складається з підстави Т-подібної форми з регульованими майданчиками і стійки зі спеціальним зеокалом.
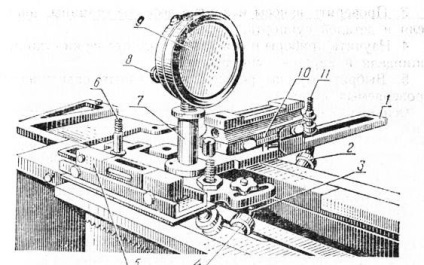
Мал. 1. Універсальний місток:
1 - підстава; 2,4 - подпятники; 3 - опора; 5, 10 - регульовані майданчика; 6, 11 - колонки; 7 - стійка; 8 - регулювальний гвинт; 9 - дзеркало.
Місток базується на п'яти кульових опорах з двома підп'ятниками. Дві з них можна переміщати у вертикальному напрямку за допомогою двох колонок, дві інші опори можна пересувати в горизонтальному напрямку по поздовжніх пазах підстави і закріплювати в необхідному положенні в залежності від ширини направляючих станини. Підп'ятник з колонкою в каналі підстави можна переміщати у вертикальному і горизонтальному напрямках.
Пристосування встановлюють на різні за формою і розмірами напрямні станини.
За допомогою двох рівнів, наявних на пристосуванні (уздовж і поперек станини), одночасно перевіряють прямолінійність і вивернутися напрямних; індикаторами, встановленими на пристосуванні, визначають паралельність поверхонь напрямних. Стійка з дзеркалом 9 і установочними гвинтами 8 використовується при перевірці прямолінійності напрямних станини автокалліматором. Для перевірки на напрямні ставлять місток приблизно в середній частині (по довжині) станини. Положення опор регулюють так, щоб чотири з них розташовувалися на призматической частини напрямних.
За допомогою колонки, що знаходиться на протилежній направляючої, регулюють положення містка в горизонтальній площині. Потім на майданчиках 5і 10 закріплюють рівні з ціною поділки 0,02 мм на 1000 мм довжини і гвинтами регулюють положення рівнів так, щоб бульбашки основної та допоміжної ампул рівнів розташовувалися посередині між шкалами. Далі пристосування зрушують уздовж напрямних і повертають на початкове місце. При цьому бульбашки основних ампул повинні повернутися в початкове положення. В іншому випадку необхідно перевірити кріплення колонок і підп'ятників. Напрямні перевіряють переміщенням містка послідовно від дільниці до дільниці. Довжина ділянки дорівнює відстані між опорами містка. При цьому за рівнем, встановленим вздовж направляючих, визначають непрямолінійність і за рівнем, розташованому перпендикулярно до напрямних, визначають вивернутися поверхонь.
Якщо відображення в мкм, відраховані на окремих ділянках, записують в журнал і потім будують форму профілю напрямних.
Непрямолінійність призматической направляючої як у вертикальній, так і в горизонтальній площинах більш точно можна визначити за допомогою автокалліматора.
В цьому випадку автокалліматор ставлять нерухомо на опорі (переважно на перевіряється станини) навпроти одного з торців станини, а на перевіряються напрямні поміщають місток з дзеркалом. Автокалліматор вивіряють паралельно напрямних і перпендикулярно дзеркалу. Для цього впритул до автокалліматору підводять місток з дзеркалом і регулюють прилад до отримання відбитого перехрестя в середині поля зору окуляра. Потім місток з дзеркалом переміщують, в протилежний кінець станини і гвинтами 8 встановлюють дзеркало перпен-
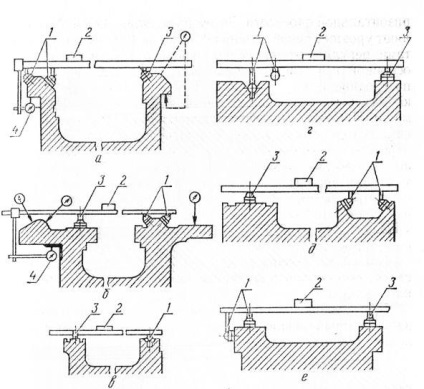
Мал. 2. Схеми налагодження універсального містка для перевірки напрямних станин різного профілю і розмірів: 1,3 - опори; 2 - рівень; 4 - індикатор.
дікулярно візирної осі автокалліматора, домагаючись різкої видимості відбитого зображення. Далі повертають місток в початкове положення і коригують різкість зображення перехрестя додатковим зміщенням приладу; цю операцію повторюють 2-3 рази до отримання однакових показань приладу по обох кінцях поверхонь.
Вимірювання роблять, пересуваючи місток від початкового положення на станині по точно розмічені ділянок (як і при роботі з рівнями). Відраховують по окулярної мікрометра відповідні кути нахилу, за якими будують графік форми напрямних. На малюнку 2 показані приклади налагодження універсального містка для перевірки напрямних станин різного профілю і розмірів за допомогою установки опор рівня і індикаторів.
Паралельність направляючих форми «ластівчин хвіст», а також інших форм зручно перевіряти за допомогою спеціальних та універсальних пристроїв, оснащених індикаторами.
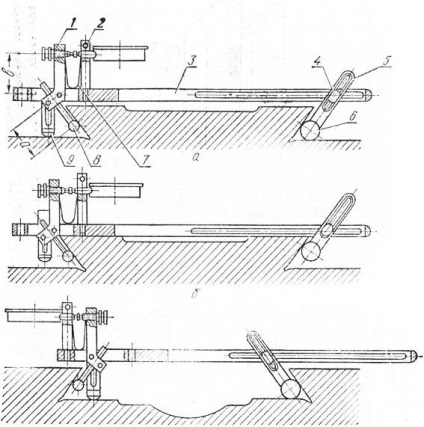
Мал. 3. Перевірка паралельності напрямних форми «ластівчин хвіст» за допомогою пристосування:
1 - важіль; 2 - стійка; 3 - балка; 4 - вісь; 5,9 - опори; 6 - валик; 7 - пружина; 8 - стрижень.
На малюнку 3 (а, б, в) приведена установка пристосування при перевірці паралельності напрямних поверхонь різного розташування. Перевірка проводиться переміщенням пристосування уздовж напрямних; відхилення паралельності визначається індикатором.
Пристрій складається з балки з шарнірно скріпленим важелем і регульованим вимірювальним стрижнем, стійки з індикатором і змінної шарнірної опори з контрольним валиком. При перевірці напрямних з контактами по нижній площині підбирають змінне опору з діаметром валика, що забезпечує контакт приблизно посередині висоти похилій площині (рис. 3, а і в).
Опору регулюють уздовж її паза і також закріплюють болтом. На циліндричній поверхні вимірювального стрижня є шкала, по якій визначають значення поділу індикатора, залежне від різниці відстаней а й в (рис. 3, а). Значення одного ділення шкали індикатора становить 0,005-0,015 мм.
Перевірка перпендикулярності направляючих станини і кареток. У процесі ремонту верстатів необхідно відновлювати взаємну перпендикулярність напрямних кареток, консолей, траверс, плазунів і багатьох інших деталей. Перпендикулярність перевіряють за допомогою контрольних і рамних кутників, кубів, а також іншими пристосуваннями, оснащеними індикаторними головками.
На малюнку 4 представлений контрольний кутник. Він складається з чавунного підстави, ползушки, індикаторів з державками і підставки. Ползушки за допомогою двох пружних притисків регулюється так, щоб її переміщення по напрямних кутника було легким і плавним. Вона не повинна довільно опускатися під дією власної ваги. Ползушки має Т-образні пази для кріплення державки з індикатором, який може бути встановлений під будь-яким кутом.
На малюнку 5 показано пристосування-підставка для контрольного кутника, що забезпечує стійке положення і точну настройку при перевірці перпендикулярності направляючих верстатів в горизонтальній площині. Це пристосування застосовується для перевірки напрямних кареток токарних, фрезерних, розточувальних та інших верстатів. Пристрій складається з підстави 1 і п'яти опор з шарнірно закріпленими підп'ятниками 3.
Для перевірки перпендикулярності направляючих каретки до напрямних станини токарного верстата пристосування (рис. 180) встановлюють на напрямні станини. Регулюють положення опор і контрольного кутника. Потім розташовують каретку на напрямних станини і сполучають поперечні санчата супорта з поперечними напрямними каретки. На санчатах закріплюють стійку з індикатором, вимірювальний штифт якого підводять до базового ребру контрольного кутника. Переміщують санчата по напрямних каретки і спостерігають за відхиленнями стрілки індикатора, що показує неперпендікулярность напрямних кареток до напрямних станини токарного верстата.
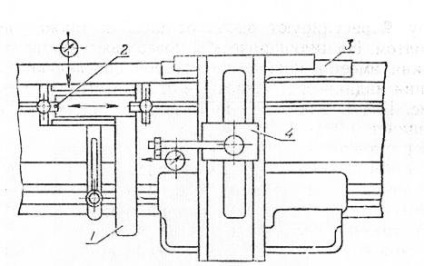
Мал. 4. Схема перевірки перпендикулярності направляючих каретки супорта токарного верстата:
1 - контрольний кутник; 2 - пристосування; 3 - каретка; 4 - поперечні санчата.
Перевірка стану осі шпінде-л я. Для перевірки стану осей шпинделя по відношенню до тих, що направляють станин необхідно визначити вихідну базу. При цьому на шпинделі встановлюють контрольні оправки. Якщо на шпинделі є точна стандартна посадкова поверхня, застосовують стандартні контрольні оправки. За конусної і циліндричної частини цих оправок перевіряють паралельність осі шпинделя напрямних.
Для перевірки ушкоджень на базових поверхнях шпинделів застосовують універсальну оправлення, яка представляє собою порожнистий стрижень з заглушкою і контрольної циліндричної частиною. На одному кінці стрижня є головка з центром, яку обмежує бурти.
Для перевірки полого шпинделя до його торця за допомогою стрижня, пропущеного крізь шпиндель, прикріплюють фланець і совхмещают останній з віссю шпинделя (з точністю 0,01 мм). Поєднання визначають індикатором, вимірювальний штифт якого підводять до зовнішньому діаметру фланця. Потім вістря оправки вставляють в зацентровку фланця і скріплюють за допомогою другого фланця трьома болтами через сферичні шайби, регулюючи положення оправлення з точністю 0,01 мм.
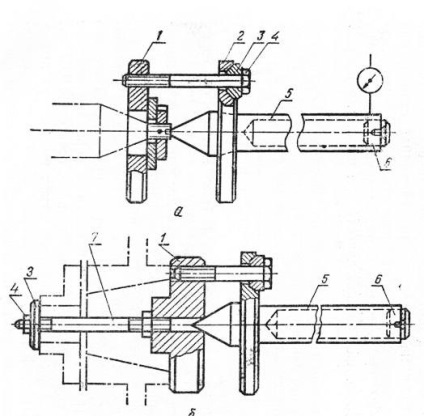
Мал. 5. Універсальна оправлення.
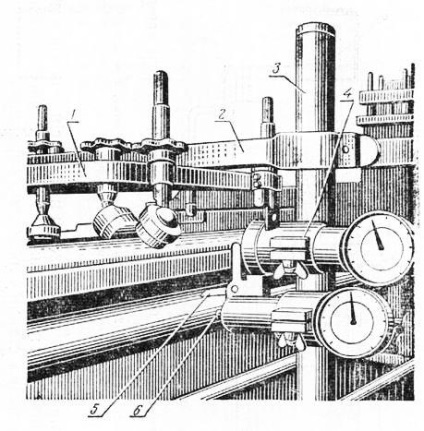
Мал. 6. Пристосування для перевірки паралельності осей ходових гвинтів і валів:
1 - місток; 2 - кронштейн; 3 - ^ стійка; 4 - хомут; 6 - важіль; 6 - вкладиш.
Перевірка паралельності осей ходових гвинтів і валів. Внаслідок зносу напрямних станин окремі вузли і деталі механізмів змінюють своє взаємне положення. Це негативно позначається на роботі механізмів подач і змушує періодично перевіряти правильність установки ходових гвинтів і валів. Пристосування, показане на малюнку 6, дозволяє перевірити паралельність направляючих і співвісність осей гвинтів і валів, що проходять через кілька вузлів.
Перевірку проводять в двох площинах - вертикальної і горизонтальної одночасно. Підставою пристосування служить стійка, закріплена в жорсткому кронштейні ночвоподібної форми. Пристосування може кріпитися на універсальному містку, на спеціальному містку або на підставі задньої бабки токарного верстата. На стійці поміщені два подвійних хомута з обмірними колодками і індикаторами. Хомути встановлюють по висоті станин так, щоб двуплечий важіль був підведений до верхньої твірної валика або гвинта, а підпружинений вкладиш - до бічної твірної. Виліт вимірювального колодок регулюють за місцем, створюючи невеликий натяг пружинами вкладишів, встановлених в вимірювального колодках пристосування.
На малюнку 6 показано застосування цього пристосування при перевірці паралельності осі ходового гвинта токарного верстата. За допомогою цього пристосування також перевіряють непаралельність установки гвинтів столів і супортів, а також непаралельність осей шпинделів напрямних станин.
Напрямні станин, кареток, санчат і інших деталей в залежності від ступеня зносу правлять шабрением, шліфуванням і струганням з подальшим шліфуванням.
Шабрування застосовують при зносі напрямних не більше 0,04 мм; шліфування - у разі спрацювання 0,05-0,1 мм; стругання-при зносі більше 0,1 мм.
Звіт про роботу.
1. Представляють дані по зносу і дефектів напрямних станини і кареток супорта, паралельності ходових гвинтів і валів, биття шпинделя.
2. Вибирають спосіб ремонту направляючих станини і кареток супорта в залежності від їх зносу.
До атегорія: - Практика ремонту машин