Дуже важливою частиною технологічного процесу виготовлення зварних або паяних вузлів є заготівельні роботи.
Для зварних виробів в конструкціях літальних апаратів в основному використовуються деталі, отримані у вигляді заготовок з листа, труб або профілів, часто йдуть в масових кількостях.
Заготівельні роботи можна розділити на два основних види: розкрій і формоутворення.
Розкрій займає приблизно 10% всього обсягу заготівельних робіт і формоутворення - 90%, при цьому більше половини пов'язане з формоутворенням деталей з листа.
Якість і способи виконання заготівельних робіт дуже впливають на якість і на кошти виконання наступних операцій зварюванням або паянням, в значній мірі визначають можливість використання спеціалізованої оснастки і засобів автоматизації, а отже, визначають можливість скорочення циклу виробництва і підвищення якості виробів. Тому технолог по заготівельним процесам повинен добре знати специфіку зварювання і пайки і які з неї вимоги до заготовок.
Поверхня деталей, отриманих після заготівельних операцій, особливо після операцій, пов'язаних з формоутворенням, має на собі сліди різних забруднень: масло, фарби, окалина, окисні плівки. Подібні забруднення поверхні деталей, що з'єднуються тягнуть за собою забруднення і зниження якості металу шва, незадовільне формування шва при зварюванні плавленням, зниження стійкості процесу і поява прожогов і виплеск при контактному зварюванні, погане розтікання припоїв і різні дефекти з'єднань при пайку.
Тому для отримання якісного зварного або паяного з'єднання необхідно провести перед зварюванням або паянням спеціальну підготовку поверхні деталей, що входять в вузли, або місць з'єднань. Особливо це істотно при таких способах з'єднання, при яких виключена можливість проведення інтенсивної металургійної обробки металу ванни, т. Е. При точкової і роликового зварювання, зварювання плавленням в захисних газах, безфлю-совою пайку і т. П. Така підготовка в основному полягає в очищенню деталі від забруднень, видалення окалини та поверхневих окисних плівок. При підготовці деталей під пайку, крім того, передбачається створення більш сприятливого мікрорельєфу поверхні, нанесення спеціальних покриттів і ін. Операцій, про що буде сказано нижче.
У загальному вигляді підготовка поверхні місць з'єднання полягає у видаленні з поверхні забруднень, жирових речовин і окисних плівок.
Для знежирення деталі обробляють в спеціальних ваннах з розчинами лугів різного складу, що видаляють жири і масла. Під дією лугів відбувається омилення жирів і їх перехід в розчин. Мінеральні масла з лужними розчинами утворюють легко віддільні від поверхні металу емульсії. Ні-обмилюють жирові плівки видаляються за допомогою органічних розчинників: бензину, трихлоретилена, чотирихлористого вуглецю, дихлоретан та ін. В деяких випадках для цих цілей можуть бути використані і такі процеси, як обробка в ваннах із застосуванням ультразвукових коливань, особливо для невеликих деталей і деталей складної форми, електролітичне знежирення і ін.
Оксидні плівки видаляються або механічним шляхом (металевими щітками, обдування піском, дробом і т. П.), Або хімічним шляхом - травленням.
Спосіб видалення оксидної плівки в першу чергу визначається типом виробництва і конструкцією деталей, що з'єднуються. При великому обсязі продукції, що випускається слід надавати перевагу травлення і піскоструминну обробку.
У масовому і великосерійному виробництві травлення є більш продуктивним процесом, ніж механічна зачистка поверхні. Недолік його полягає в можливості перетравлі-вання поверхні металу і в складності роботи з травильними розчинами. Цей метод заснований на здатності кислот і лугів розчиняти оксиди деяких металів. Для цієї мети зазвичай застосовуються водні розчини таких кислот, як сірчана, азотна, соляна, фтористоводнева, ортофос-Форн, плавикова і їх суміші, водні розчини лугів, а також газові травители.
Поверхня металів, отримана при травленні, у багатьох випадках має більш сприятливий характер для подальшої зварюванням або паянням, ніж поверхня після механічної зачистки.
Для травлення деталей потрібне окреме приміщення, обладнане ваннами, завантажувальними пристроями, сушильними шафами, вентиляцією і стоками для рідин.
Застосовуються два основних способи хімічної очистки: ний - зануренням - і струменевий. Приклад організації ділянки за першим способом наведено на рис. 1. Оброблювані деталі встановлюються у вертикальному положенні, витримуються в кожній ванні певний час, а потім переносяться в наступну ванну до повного завершення циклу.
При струменевому способі обробки пропесс йде значно інтенсивніше, ніж при обробці методом занурення. Струменевий метод дозволяє організувати найбільш продуктивні і механізовані лінії хімічної очистки.
По піскоструминному очищенню деталей від окалини та поверхневих оксидів є вельми універсальним і продуктивним способом, але не відповідає сучасним вимогам промислової санітарії та техніки безпеки, так як при цьому виділяється
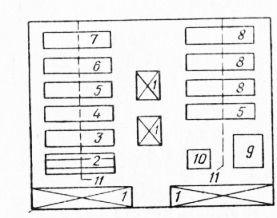
Мал. 1. План ділянки хімічної очистки з використанням ванного способу: 1 - стелажі для зберігання деталей, 2 - стелаж для попереднього очищення поверхні деталей, 3 - ванна знежирення, 4 - ванна промивання гарячою водою, 5 - ванна промивання у холодній воді, 6 - ванна травлення в азотній кислоті. 7 - ванна травлення в розчині їдкого натру, 8 - ванни травлення і пассивирования, 9 - сушильна камера, 10 - установка для контролю електричного опору, 11 - монорельси.
велика кількість кварцового пилу. Тому її замінюють менш шкідливими способами.
Останнім часом все більш широке застосування починає знаходити очищення деталей обдувом металевим піском, які добувають з чавунною дробу. Цей спосіб може використовуватися для різних марок матеріалів, крім алюмінієвих і магнієвих сплавів, для нержавіючих сталей аустенітного класу, жароміцних сталей і сплавів. При цьому відсутня забруднення повітря. Металевий пісок зараз проводиться в промислових масштабах.
Мал. 2. Схема безперервної потокової лінії хімічної очистки струменевим методом: