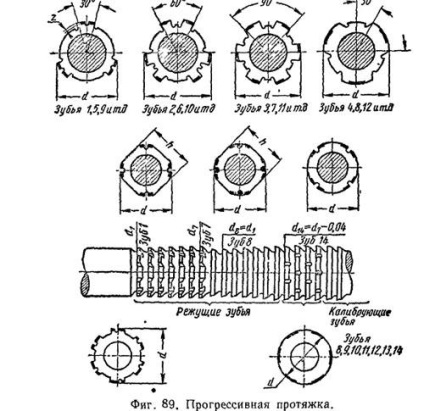
Протягування отворів. Протягуванням називається обробка поверхонь інструментами - протяжками, забезпеченими зубами, розташованими перпендикулярно осі інструменту; кожен з зубів знімає певний шар металу, так як висота зубів різна. Зняття металу з поверхні при обробці отворів відбувається при переміщенні протягання в напрямі осі оброблюваної деталі.
Найбільш поширені протягання для обробки раніше просвердлених або марнування отворів складаються з хвостовика 1 (фіг. 88) з замком для кріплення інструменту; шийки 2, поперечний переріз якої вибирається так, щоб при перевантаженні протягання її розрив стався в цьому, а не в будь-якому іншому місці, де було б важко знову зварити розірвані частини інструменту; направляючої частини 3, необхідної для попередньої орієнтування протягання в оброблюваному отворі; робочої частини 4 (ріжучі зуби); калібрує 5 (для стандартизації цих величин зуби); підтримуючої частини 6.
Відстань між ріжучими крайками двох сусідніх зубів, зване кроком зубів (, по-різному у ріжучих і калібрів зубів. Для перших воно вибирається в залежності від довжини оброблюваного отвору, для других - зазвичай в середньому приймається рівним половині кроку ріжучих зубів.
Умовою правильної роботи протягання є одночасне різання не менше ніж трьома зубцями. Проте, щоб уникнути появи надмірних зусиль і розриву протяжки в роботі повинно знаходитися не більше 6-8 зубів. Для отримання після обробки більш рівною і чистою поверхні крок зубів повинен бути неоднаковий (відмінність в кроці 0,2-0,3 мм).
Висота зубів робочої частини поступово збільшується від хвостовика до калібрує, в залежності від оброблюваного матеріалу і розмірів отвору, що простягається, на 0,01-0,2 мм.
Зазвичай робочу і калібруючу частини протягання виготовляють зі швидкорізальної сталі, інші частини роблять з конструкційної сталі і зварюють з частинами, виготовленими зі швидкорізальної сталі.
Для зменшення довжини протягання застосовують прогресивні протягання (фіг. 89), у яких ріжуча частина більшості ців Зуби зрізають метал не по всьому колу отвори, а в окремих її частинах ( «прогресивне різання»). Тільки останніми калібрують круглими зубами отвору надається циліндрична форма
В результаті зменшення ширини стружки можна збільшити її товщину і, отже, зменшити кількість ріжучих зубів протягання, скоротивши її довжину майже вдвічі, і зменшити зусилля різання, що діють на інструмент.
Кількість зубів в секції 3-6 кожною секцією знімається шар металу товщиною 0,1-0,4 мм. На кінці протягання розташовані круглі чистові і калібрів зуби.
Протягування необроблених поверхонь ускладнюється значними коливаннями в їх формі і розмірах. У цих випадках застосовують прогресивні протягання з зубами чотирьох- або шестигранної форми, а також з шліцеобразнимі зубами.
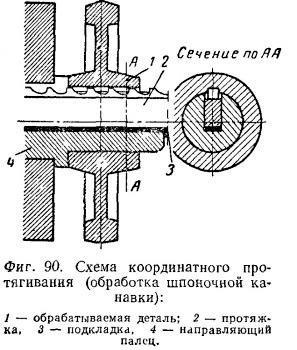
При координатному протягуванні потрібно забезпечити певну координацію обробленої протяжкой поверхні щодо інших поверхонь, наприклад, положення шпоночно канавки щодо осі раніше обробленого отвору (фіг. 90). В цьому випадку обробляється деталь не орієнтується в просторі самої протяжкой, як при вільному протягуванні: деталі надається певне положення на верстаті. Протяжка також перемішається по відповідним напрямних або по поверхні деталі, щодо якої має бути координована простягнута поверхню.
Дуже часто обробку отворів виробляють інструментом, подібним звичайної протяжке (але коротшим), проштовхуючи його на пресі через обробляється отвір При цьому інструмент працює на стиск на відміну від протягання, що працює на розтяг. Цей процес називають прбшіваніем отвори, г застосовувані інструменти - прошивками.
Прошивання отворів застосовується зазвичай для їх калібрування найчастіше після термічної обробки деталей, при якій порушується правильне і, форми отворів.
При протягуванні і прошивці руху подачі не потрібно, так як зняття послідовно окремих шарів металу здійснюється внаслідок різниці в розмірах зубів протягання.
Протягування застосовується при обробці різних внутрішніх поверхонь (круглих і фасонних отворів діаметром 6-100 мм), площин і зовнішніх фасонних поверхонь. Деякі види поверхонь (наприклад, шліцьові отвори) в даний час обробляють тільки протягуванням внаслідок великих труднощів, що виникають при обробці таких поверхонь іншими способами.
Широке застосування протягування поверхонь (особливо в великосерійному і масовому виробництвах) пояснюється наступними перевагами цього процесу:
1) високою продуктивністю обробки;
2) високою точністю (до 2-го класу) і високою чистотою обробки (до 9-го класу);
3) простотою обслуговування верстата і можливістю автоматизації процесів;
4) спрощенням технологічного процесу обробки деталі в результаті заміни протягуванням послідовної обробки поверхні кількома інструментами (зенкером і рядків або розточувальним різцем і рядків і т. Д);
5) можливістю забезпечити потрібну точність протягуванням деяких поверхонь (наприклад, шліцьових отворів), які важко точно обробити іншими способами.
Застосування протягування обмежується наступними причинами:
1) виникненням при протягуванні значних зусиль різання, які можуть викликати деформації оброблюваних (особливо тонкостінних коробчатих) деталей;
2) неможливістю протягування поверхонь деталей великих розмірів;
3) неможливістю протягування глухих отворів;
4) високою вартістю протяжок;
5) неможливістю протягування поверхонь при такій твердості поверхні, при якій непридатний лезовий інструмент;
6) труднощами точно координувати положення осі оброблюваного отвору щодо інших поверхонь деталі (т. Е. Трудність виправити становище цього отвору).
Протяжні верстати для обробки отворів поділяють на такі види:
а) з одним повзуном;
б) з двома повзунами;
2) вертикальні з одним повзуном;
3) вертикальні напівавтомати:
а) з одним повзуном;
б) з декількома повзунами.
Зазвичай верстати, забезпечені повзунами для додання протяжка прямолінійного руху, мають гідравлічний привід.
Найбільш універсальними і широко поширеними в усіх видах виробництва є горизонтально-протяжні верстати, призначені для обробки отворів. Для вертикально-протяжних верстатів потрібно менше площі.
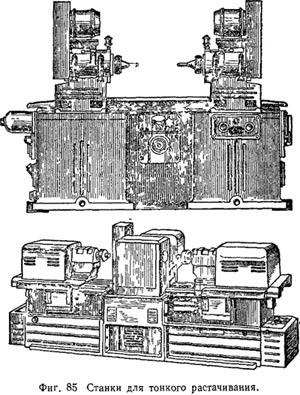
Тонке розточування отворів. При виготовленні багатьох деталей потрібно забезпечити високу точність і чистоту обробки отворів при високій точності координації осей.
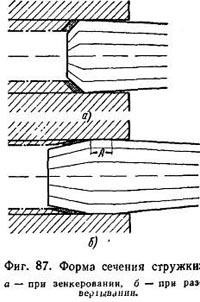
Розгортання отворів. Отвори 2-го і 3-го класів точності після свердління або розточування іноді остаточно обробляють розгортанням. Отвори обробляють розгортанням на таких.
Обробки отворів деталей із застосуванням абразивів. Існують наступні способи обробки отворів абразивами: 1) шліфування; 2) хонингование; 3) притирання; 4) суперфінішірованіе; 5) полірування.
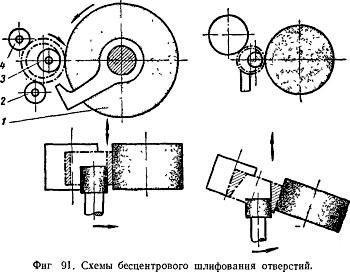
Шліфування отворів у виробничих цехах застосовують в дуже обмеженій формі, так як цей спосіб малопродуктивний і дорогий. Внутрішнім шліфуванням обробляють.