Кокс-сіре, трохи сріблясте, пористе і дуже тверда речовина, більш ніж на 96% складається з вуглецю і отримується при на-прогрівання кам'яного вугілля або нафтових пеков без доступу повітря при 950-1050 ° С. Процес полученія- коксу в результаті переробки природних палив називається коксуванням.
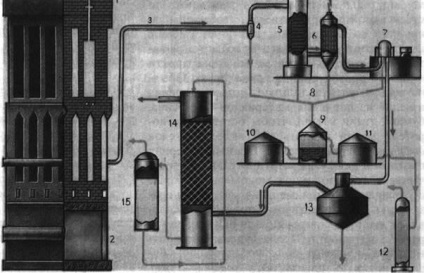
Схема коксування: 1. - коксову батарею; 2. - збірний канал продуктів горіння; 3. - газопровід; 4. - відділювач конденсату; 5. - газовий холодильник; 6. - електрофільтр; 7. - газодувки; 8. - трубопровід для відведення конденсату; 9. - відстійник; 10. - сховище смоли; 11. - сховище аміачної води; 12. - аміачна колона; 13. - сатуратор; 14. - бензоловий скруббер; 15. - бензолова колонка.
Кокс застосовують для виготовлення елек-Трод, для фільтрування, очищення рідин і, найголовніше, для відновлення заліза із залізних руд і концентратів в доменному процесі виплавки чавуну. У доменній печі кокс згоряє і утворюється оксид вуглецю (IV):
який взаємодіє з розпеченим кок-сом з утворенням оксиду вуглецю (II):
Оксид вуглецю (II) і є відновите-лем заліза, причому спочатку з оксиду заліза (III) утворюється оксид заліза (II, III), потім оксид заліза (II) і, нарешті, залізо:
В результаті доменного процесу отримують рідкий чавун-сплав заліза з домішками, з-тримаються в залізній руді і кам'яно-вугільному коксі, - вуглецем, кремнієм, мар-ганцем, фосфором і сіркою.
Коксування виникло в XVIII в. коли ис-споживання лісів для отримання деревного вугілля, що використовувався при виплавці желе-за, стало загрозливим і потрібно було заме-нить це вугілля іншим паливом. У 1735 р в Англії була проведена перша доменна плавка на коксі.
У наш час 10% видобутого в світі ка-ного вугілля перетворюють на кокс. Коксування проводять в камерах коксової печі, обігр ваемих зовні палаючим газом. При пови-шеніі температури в кам'яному вугіллі від-ходять різноманітні процеси. При 250 0 Сиз нього випаровується волога, виділяються СО і СО2; при 350 0 С вугілля розм'якшується, перехо-дить в тістоподібне, пластичне стан, з нього виділяються вуглеводні-газо-бразние і низкокипящие, а також азотисті і фосфористий з'єднання. Важкі уг-листові залишки спікається при 500 0 С, даючи напівкокс. А при 700 0 С і вище напівкокс ті-ряется залишкові леткі речовини, головним чином водень, і перетворюється в кокс.
Всі летючі продукти надходять в газо-збірник, а залишився розпечений кокс ви-талківают в так званий гасильний ва-гон, де його охолоджують (гасять) водою або інертним газом. Летючі речовини при кон-денсаціі утворюють аміачну воду і смолу. Частина неконденсірующаяся газу використовують для нагрівання вугілля в камерах печі; залишок га-за, аміачна вода і смола йдуть на пере-лення. З них отримують різноманітні неорганізованому-ганическое і органічні (головним чином ароматичні) з'єднання. З 1 т кам'яного вугілля отримують приблизно 800 кг коксу, 150 кг газу і 50 кг інших продуктів.
Важливим джерелом промислового отримання ароматичних вуглеводнів поряд з переробкою нафти є коксування кам'яного вугілля.
Процес коксування можна провести в лабораторії. Якщо кам'яне вугілля сильно нагрівати в залізній трубці без доступу повітря, то через деякий час можна буде спостерігати виділення газів і парів. В U-образ-ой трубці конденсується смола, що має неприємний запах, і над нею вода, що містить аміак. Проходив далі гази збираються в посудині над водою. У залізної трубці після досвіду залишається кокс. Зібраний газ добре горить, його називають коксівним газом.
Таким чином, при нагріванні кам'яного вугілля без доступу повітря утворюються чотири основні продукти: кокс, кам'яновугільна смола, аміачна вода, коксовий газ.
Коксохімічне виробництво в основі своїй має багато спільного з лабораторним досвідом коксування вугілля, воно як би відтворює його в великих масштабах.
При нагріванні вугілля без доступу повітря до 900-1050 о С призводить до його термічного розкладання з утворенням летючих продуктів і твердого залишку-коксу.
Процес коксування триває близько 14 годин. Після того як він закінчиться, що утворився кокс- «коксовий пиріг» -вигружают з камери в вагон і потім гасять водою або інертним газом; в камеру завантажують нову партію вугілля, і процес коксування починається знову. Коксування вугілля-періодичний процес. Основні продукти: кокс-96-98% вуглецю; коксовий газ-60% водню, 25% метану, 7% оксиду вуглецю (II) і ін. Побічні продукти: кам'яновугільна смола (бензол, толуол), аміак (з коксового газу) і ін.
Після охолодження кокс сортують і направляють на металургійні заводи для доменних печей.
Летючі продукти виводяться через отвори вгорі камер і надходять до загального газосборнік, де з них, як в нашому досвіді, конденсується смола і аміачна вода.
З неконденсірующаяся газу витягують аміак і легкі ароматичні вуглеці (головним чином бензол). З метою вилучення аміаку газ пропускають через розчин сірчаної кислоти; утворюється сульфат амонію використовується як азотне добриво.
Ароматичні вуглеводи виходять шляхом поглинання їх розчинником і подальшої відгону з утворюється розчину.
З кам'яновугільної смоли шляхом фракціонування отримують гомологи бензолу, фенол (карболової кислоти), нафталін і ін.
Коксовий газ після отчистки застосовується в якості палива в промислових печах, так як містить багато горючих речовин. Він використовується і як хімічна сировина. Наприклад, з коксового газу виділяють водень для різних синтезів.
Проблеми використання вуглеводневої сировини:
До недавнього часу в паливному балансі країни величезна частка припадала на нафту. У зв'язку з розвитком енергопостачання здійснюється переведення енергетики з використанням нафти і нафтопродуктів в якості палива на широке застосування в цих цілях природного газу, вугілля, на використання атомної енергії. Це означає, що важкі залишки переробки нафти-мазути будуть більш повно перероблятися в світлі нафтопродукти, необхідні для сучасного органічного синтезу. Хімічній науці належить завдання вишукати більш ефективні шляхи переробки нафти, природного і попутних газів, вугілля, сланців, а також удосконалити існуючі з метою більш повного і комплексного використання природного вуглеводневої сировини.
Отримання штучного рідкого палива не є новою проблемою. Установка гідрування вугілля була введена в Німеччині ще в 1923 році, а в 1943 цим шляхом в Німеччині було отримано 2 мільйони тонн бензину і 800000 тонн дизельного палива. Процес отримання штучного рідкого палива був дуже дорогим і проходив при тиску 70 МПа і температурі 180 о С. У післявоєнні роки гідрування вугілля практично втратило промислове значення.
В даний час вченими розробляються інші економічно вигідніші методи гідрування вугілля з використанням ефективних каталізаторів, що дасть можливість знизити температуру і тиск.
Іншим перспективним шляхом отримання синтетичного рідкого палива є його синтез з оксиду вуглецю (II) і водню.