При виготовленні меблів не обійтися без криволінійних деталей. Отримати їх можна двома способами - випилювання і гнуттям. Технологічно, здавалося б, легше випиляти криволінійну деталь, ніж відпарювати, гнути а потім протягом певного часу витримувати її до повної готовності. Але у випилювання є ряд негативних наслідків.
Гнуття дозволяє уникнути всіх цих недоліків. Звичайно, гнуття передбачає наявність спеціального обладнання і пристосувань, а це не завжди можливо. Проте, гнуття можливо і в домашній майстерні. Отже, яка ж технологія процесу гнуття?
Технологічний процес виготовлення гнутих деталей включає в себе гідротермічної обробки, гнуття заготовок і їх сушку після гнуття.
Гідротермічної обробкою досягається поліпшення пластичних властивостей деревини. Під пластичністю розуміють властивості матеріалу змінювати свою форму без руйнування під дією зовнішніх сил і зберігати її після того, як дія сил буде усунуто. Найкращі пластичні властивості деревина набуває при вологості 25 - 30% і температурі в центрі заготовки до моменту гнуття приблизно 100 ° С.
Гідротермічної обробки деревини виконують пропарюванням в котлах насиченою парою низького тиску 0,02 - 0,05 МПа при температурі 102 - 105 ° С.
Так як тривалість пропарювання визначається часом досягнення заданої температури в центрі пропарюють заготовки, то час пропарювання збільшується зі збільшенням товщини заготовки. Наприклад, для пропарювання заготовки (з початковою вологістю 30% і початковою температурою 25 ° С) товщиною 25 мм з досягненням температури в центрі заготовки 100 ° С необхідно 1 ч. Товщиною 35 мм - 1 ч.50 хв.
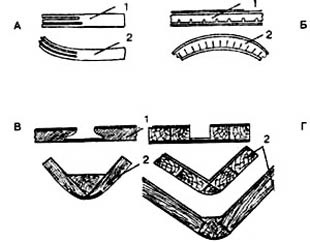
Рис.1. Шина з упорами для гнуття заготовки. 1 - упори; 2 - заготовка; 3 - гвинт; 4 - шина
Мал. 2. Гнутопропільние заготовки. А - з поздовжніми пропилами на кінцях деталей; Б - з пропилами в плитах; В, Г - з пазами в плитах; 1 заготовки; 2 - готові вузли
При гнуття заготовку кладуть на шину з упорами (рис.1), потім в механічному або гідравлічному пресі заготовку разом з шиною згинають на заданий контур, в пресах, як правило, згинають одночасно декілька заготовок. Після закінчення гнуття кінці шин стягують стяжкою. Зігнуті заготовки надходять на сушку разом з шинами.
Сушать заготовки 6 - 8 ч. Під час сушіння стабілізується форма заготовок. Після сушіння заготовки звільняють від шаблонів і шин і витримують не менше 24 год. Після витримки відхилення розмірів гнутих заготовок від початкових зазвичай становить ± 3 мм. Далі заготовки обробляють.
Для гнутих заготовок застосовуються лущений шпон, карбамідоформальдегідні смоли КФ-БЖ, КФ-Ж, КФ-МГ, М-70, деревостружкові плити П-1 і П-2. Товщина заготовки може бути від 4 до 30 мм. Заготовки можуть мати найрізноманітніші профілі: уголковие, дугоподібні, сферичні, П-образні, трапецієподібні і коритоподібні (див. Рис.2). Такі заготовки виходять шляхом одночасного згину і склеювання між собою змазаних клеєм листів шпону, які сформовані в пакети (рис. 3). Така технологія дозволяє отримати вироби найрізноманітніших архітектурних форм. До того ж виготовлення гнутоклеєних деталей з шпону економічно доцільно через малої витрати лісоматеріалів і порівняно невеликих трудовитрат.
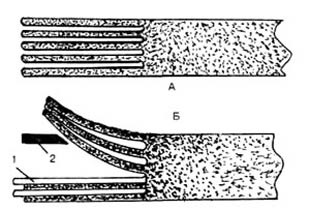
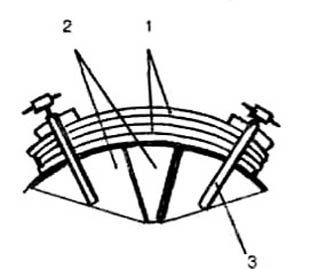
Мал. 3. Гнутопропільние заготовки. А - заготівля з пропилами; Б - закладка шпону в пропили; 1 - закладаються смужки шпону; 2 - ніж
Мал. 4. Фіксація на жорсткому шаблоні за допомогою струбцин. 1 - Склеєні пласти; 2 -жесктій шаблон; 3 - струбцина
Пласти ділянок намазують клеєм, закладають в шаблон і запресовують (рис. 4). Після витримки під пресом до повного затвердіння клею вузол зберігає надану йому форму. Гнутоклеєні вузли виготовляють з шпони, з пластин листяних і хвойних порід, з фанери. У гнутоклеєних елементах зі шпону напрямок волокон в шарах шпони може бути як взаємно перпендикулярним, так і однаковим. Вигин шпону, при якому волокна деревини залишаються прямолінійними, називається вигином поперек волокон, а при якому волокна згинаються - вигином уздовж волокон.
При конструюванні гнутоклеєних вузлів зі шпону, несучих при експлуатації значні навантаження (ніжки стільців, корпусних виробів), найбільш раціональні конструкції з вигином уздовж волокон у всіх шарах. Жорсткість таких вузлів значно вище, ніж вузлів з взаємно перпендикулярним напрямком волокон деревини. З взаємно перпендикулярним напрямком волокон шпону в шарах конструюють гнутоклеєні вузли товщиною до 10 мм, що не несуть великих навантажень при експлуатації (стінки ящиків і т. П.). У цьому випадку вони менше схильні до формоізменяемості. Зовнішній шар таких вузлів повинен мати пайову напрям волокон (вигин уздовж волокон), так як при вигині поперек волокон в місцях вигину з'являються дрібні часткові тріщини, які виключають хорошу обробку вироби.
Допустимі (радіуси кривизни гнутоклеєних елементів з шпону залежать від наступних конструктивних параметрів: товщини шпону, кількості шарів шпону в пакеті, конструкції пакета, кута вигину заготовки, конструкції прес-форми.
При виготовленні гнутопрофільних вузлів з поздовжніми пропилами необхідно враховувати залежність товщини елементів, що згинаються від породи деревини і товщини згинається деталі.
У таблицях залишилися після розрізання елементи названі крайніми, інші - проміжними. Мінімальна відстань між пропилами, яке можна отримати, становить близько 1,5 мм.
Зі збільшенням радіуса вигину плити відстань між пропилами зменшується (рис. 5). Ширина пропила залежить від радіуса вигину плити і кількості пропилів. Для отримання закруглених вузлів, в плиті після її фанерування і шліфування вибирають паз в тому місці, де буде вигин. Паз може бути прямокутним або типу «ластівчин хвіст». Товщина залишилася фанерною перемички (дна паза) повинна бути дорівнює товщині облицювальної фанери з припуском 1-1,5 мм. У прямокутний паз вставляють на клею закруглений брусок, а в паз "ластівчин хвіст» - смугу шпону. Потім плиту згинають і витримують в шаблоні до затвердіння клею. Для додання кутку більшої міцності в нього з внутрішньої сторони можна поставити дерев'яний кутник.
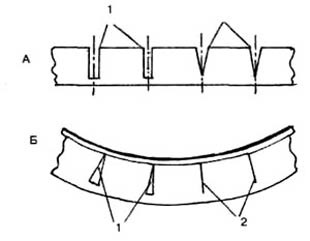
Мал. 5. Прямокутні і конічні пропили в плитах. А - до вигину; Б - після вигину; 1 - пропили прямокутної форми; 2 - пропили конічної форми.