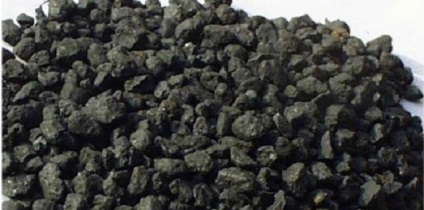
Сировина для отримання нафтового коксу
Якість сировини надає першорядний вплив на характеристики кінцевого продукту - нафтового коксу.
Виробництво коксу в СНД в основному здійснюється на установках сповільненого коксування (УЗК).
Характерною особливістю умов роботи УЗК є використання в якості сировини різноманітних сумішей, що залишаються на заводах в результаті переробки нафти.
Сировиною служать важкі фракції нафти утворюються в результаті атмосферної і вакуумної перегонки нафти (мазути, напівгудрон, гудрони), крекінг-залишки від термічного крекінгу мазуту і гудронів, важкі газойлі каталітичного крекінгу, залишки масляного виробництва (асфальт пропанового деасфальтизації гудрону, екстракти фенольной очищення масел і ін.).
З усіх нафтових залишків, схильних до утворення різних видів структур коксу, найбільш переважними вважаються ароматичні концентрати (дистилятів крекінг-залишок) і деякі інші високомолекулярні вуглеводні.
З цієї причини дистиллятное сировину відносять до перспективних видів сировини.
НПЗ мають різні виробничі умови і працюють на різних нафтах, тому для кожного НПЗ установки сповільненого коксування будувалися з урахуванням конкретних умов.
Серед основних параметрів, що визначають якість нафт, таких як щільність, фракційний та хімічний склад нафтопродуктів, найбільш значущими є щільність і показник сірчистості.
Сірка - одна з найбільш небажаних домішок в складі сирих нафт і кінцевого продукту - коксу.
Залежно від масової частки сірки коксу, так само як і нафти, класифікуються на малосірчисті, сірчисті, високосірчисті.
Сірчисті кокси відрізняються менш сприятливими властивостями, в порівнянні з малосірчистих коксу: викликають корозію обладнання, підвищена кількість тріщин в електродних виробах, руйнування вогнетривкої кладки печей прожарювання, внаслідок чого їх використання обмежене певними областями.
Нафта, що надходить на нафтопереробні заводи, різниться за складом, особливо щодо вмісту сірки.
Для для Росії характерна переробка в основному сірчистої і високосернистої нафти.
В даний час основною сировиною для отримання коксу є сірчисті нафти.
Застосування технологій, що дозволяють отримувати якісний кокс незалежно від складу вихідної нафти, вирішує багато проблем:
забезпечує електродний промисловість якісною сировиною, дозволяє задіяти у виробництві більш широкий діапазон нафт, а також поглибити процес переробки нафти на НПЗ.
З метою знесірчення кінцевого продукту застосовується прожарювання коксу.
Ще один шлях отримання знесірчених нафтового коксу з високосірчистих марок нафти - це попереднє видалення сірки з сирої нафти методом гидрообессеривания, гідрокрекінгу, або деасфальтизації.
Цей варіант вважається більш дієвим, незважаючи на те, що є більш складним і вимагає додаткових витрат.
На російські заводи нафта поставляється, головним чином, за системою магістральних нафтопроводів (МНП) Транснафти, в якій Західно-Сибірська нафту, марки Siberian Light змішується з більш важкої і сірчистої нафтою марки Urals.
Способи отримання сирого і обпаленого нафтового коксу
Коксування нафтової сировини - найбільш жорстка форма термічного крекінгу нафтових залишків.
Здійснюється при низькому тиску і температурі 480-560 ° С, з метою отримання нафтового коксу, а також вуглеводневих газів, бензинів і керосино-газойльових фракцій.
При коксуванні відбувається розщеплення всіх компонентів сировини з утворенням рідких фракцій дистилятів і вуглеводневих газів; деструкція і циклизация вуглеводнів з інтенсивним виділенням керосино-газойльових фракцій; конденсація і поликонденсация вуглеводнів і глибоке ущільнення високомолекулярних сполук з утворенням суцільного коксового залишку.
Промисловий процес коксування здійснюється на установках 3 х типів: періодичне коксування в коксових кубах, уповільнене коксування в камерах, безперервне коксування в псевдозрідженому шарі коксу-носія.
Уповільнене (Напівбезперервне) коксування найбільш широко поширене у світовій практиці.
Сировина, попередньо нагріте в трубчастих печах до 350-380 ° С, безперервно надходить на каскадні тарілки ректифікаційної колони (працює при атмосферному тиску), стікаючи по яким, контактує з піднімаються назустріч парами, які подаються з реакційних апаратів.
В результаті тепло- і масообміну частина парів конденсується, утворюючи з вихідною сировиною так зване вторинну сировину, яке нагрівається в трубчастих печах до 490-510 о С і надходить в коксові камери - порожнисті вертикальні циліндричні апарати діаметром 3-7 м і висотою 22-30 м.
В камеру реакційна маса безперервно подається протягом 24-36 годин і завдяки акумульованої нею теплоті коксується.
Після заповнення камери коксом на 70-90% його видаляють, зазвичай струменем води під високим тиском (до 15 МПа).
Кокс надходить в дробарку, де подрібнюється на шматки розміром не більше 150 мм, після чого подається елеватором на гуркіт, де розділяється на фракції 150-25, 25-6 і 6-0,5 мм.
Камеру, з якої вивантажено кокс, прогрівають гострим водяною парою і парами з працюючих коксових камер і знову заповнюють коксованої масою.
Летючі продукти коксування, що представляють собою парожідкостная суміш, безперервно виводяться з діючих камер і послідовно розділяються в ректифікаційної колоні, водороздільники, газовому блоці і отпарной колоні на гази,
Типові параметри процесу: температура в камерах 450-480 о С, тиск 0,2-0,6 МПа, тривалість до 48 годин.
Переваги сповільненого коксування - високий вихід малозольного коксу.
З одного і того ж кількості сировини цим методом можна отримати в 1,5-1,6 рази більше коксу, ніж при безперервному коксовании.
На російських НПЗ експлуатуються 1-блокові і 2-блокові установки коксування (кожен блок складається з 2 х або 3 х реакторів) декількох типів.
Компонування, проектування установок зроблені за проектами інститутів Гіпронефтезаводи і ВНІПІнефть.
Проводять в горизонтальних циліндричних апаратах діаметром 2-4 м і довжиною 10-13 м.
Сировина в кубі поступово нагрівають знизу відкритим вогнем.
Далі звичайним способом виділяють дистиляти, кокс підсушують і прожарюють (2-3 години).
Після цього температуру в топці під кубом поступово знижують і охолоджують куб спочатку водяною парою, а потім повітрям.
Коли температура коксу знизиться до 150-200 о С, його вивантажують.
Типові параметри процесу: температура в паровій фазі 360-400 о С, тиск атмосферний.
Однак спосіб малопродуктивний, вимагає великої витрати палива, а також значних затрат ручної праці і тому майже не використовується в промисловості.
Безперервне коксування в киплячому шарі (термоконтактним крекінг)
Сировина, попередньо нагріте в теплообміннику, контактує в реакторі з нагрітим і знаходяться в підвішеному стані інертним теплоносієм і коксується на його поверхні протягом 6-12 хвилин.
В якості теплоносія використовується зазвичай порошкоподібний кокс з розміром частинок до 0,3 мм, рідше більші гранули.
Утворився кокс і теплоносій виводять із зони реакції і подають в регенератор (коксонагреватель).
Там шар теплоносія підтримується в підвішеному стані за допомогою повітря, в струмі якого випалюється до 40% коксу, а більша його частина направляється споживачу.
Завдяки теплоті, що виділилася при випалюванні частини коксу, теплоносій нагрівається і повертається в реактор.
Для переміщення теплоносія використовується пневмотранспорт частинок коксу, що захоплюються потоком пари або газу.
Дистилятні фракції і гази виводять з реактора і поділяють так само, як при сповільненому коксовании.
Типові параметри процесу: температура в теплообміннику 300-320 про С. реакторі 510-540 о С і регенераторі 600-620 про С. тиск в реакторі і регенераторі 0,14-0,16 і 0,12-0,16 МПа відповідно, теплоносій - (6,5-8,0)
Коксування в киплячому шарі використовують для збільшення виходу світлих нафтопродуктів. Крім того, поєднання безперервного коксування з газифікацією утворюється коксу може бути застосовано для отримання дизельних і котельних палив.
Перед використанням нафтовий кокс зазвичай піддається облагороджування, що включає кілька процесів.
При прожаренні видаляються леткі речовини і частково гетероатоми (наприклад, сірка і ванадій), знижується питомий електричний опір.
При Графитирование 2-мірні кристалітів перетворюються в кристалічні освіти 3-мірної впорядкованості.
У загальному вигляді стадії облагороджування можна представити наступною схемою: кристаллитами → карбонізує (прожарювання при 500-1000 о С) → 2-мірне впорядкування структури (1000-1400 о С) → предкрісталлізація (трансформація кристаллитов при 1400 о С і вище) → кристалізація, або графітованої (2200-2800 о С).
- алюмінієва промисловість, в якості відновника (анодна маса) при виплавці алюмінію з алюмінієвих руд (бокситів). Питома витрата коксу 550 - 600 кг / т алюмінію.
- сировина для виготовлення електродів, що використовуються в сталеплавильних печах;
- сировина для отримання карбідів (кальцію, кремнію), які застосовуються при отриманні ацетилену;
- виробництво шліфувальних, абразивних матеріалів,
- при виготовленні провідників, вогнетривів і ін.
- в якості відновників і сульфидирующих агентів (серністи1 і високосірчистий),
- для виготовлення хімічної апаратури, що працює в умовах агресивних середовищ, в ракетній техніці і тд (конструкційний матеріал).