Ресорне підвішування тепловоза призначене для зменшення динамічного впливу коліс на рейки при русі по нерівностях шляху, забезпечення плавності ходу тепловоза і передачі ваги кузова і візків на колісні пари. З іншого боку, рессорное підвішування полегшує завдання правильного розподілу навантаження від ваги тепловоза між колісними парами, а також забезпечує часткову передачу горизонтальних сил з боку коліс на раму візка.
Підвішування тепловоза виконано одноступінчастим, одинарним (тільки пружини) і індивідуальним для кожного буксового вузла колісної пари. Воно складається з 12 однакових груп (по шість груп для кожного візка), що мають по два однакових пружинних комплекту, встановлених між опорними кронштейнами корпусу букси і кронштейнами рами візка. Паралельно з кожною групою ресорного підвішування встановлюють фрикційний гаситель коливань.
Пружинний комплект (рис. 91) складають три пружини: зовнішня 2, середня 4, внутрішня 3, дві опорні плити 1 і 5 й регулювальні прокладки 6. Для виключення торкання і заскакуючи витків однієї пружини між витками іншої при їх концентричному розташуванні внутрішню пружину розміщують в зовнішньої з зазором не менше 5 мм на сторону, причому пружини повинні бути навито в різні боки. Пружини ресорного підвішування виготовляють з круглого каліброваного прокату гарячекатаної пружинної стали 60С2А діаметром: для- зовнішніх пружин 36 мм, для середніх 23 мм, для внутрішніх 16 мм. Твердість пружин в термообробленому стані повинна бути 1ЖС 40-47. Після термообробки пружини упрочняют наклепом дробом.
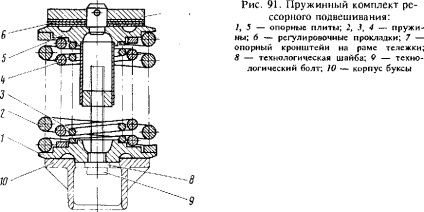
Зовнішня пружина сприймає «65% навантаження на пружинний комплект, середня -« 23% і внутрішня - «12%. Граничне навантаження з урахуванням перевантаження і динамічного прогину становить для зовнішньої пружини 40 кН (4 тс), середньої - 15 кН (1,5 тс), внутрішньої - 8 кН (0,8 тс). При дії цих навантажень у витках при їх повному змиканні напруги не перевищують межі текучості матеріалу пружин при крученні, рівного 750 МПа (7500 кгс / см2).
При індивідуальному підвішуванні значення жорсткості і висоти у вільному стані пружин різних комплектів не повинні значно відрізнятися, інакше виникає нерівність статичних навантажень, що передаються колесами на рейки. З огляду на це пружини поділяють на три групи. Номер групи для пружинного комплекту визначають за номером групи зовнішньої пружини. Формують комплекти наступним чином: якщо зовнішня пружина I групи, то внутрішні - I або II; якщо Зовнішня пружина
II групи, то внутрішні - I, II або III; якщо зовнішня пружина
III групи, то внутрішні - II або III. Перед установкою на візок пружинні комплекти збирають і стягують спеціальними технологічними болтами 9, які після остаточного складання візка знімають. На одному візку встановлюють пружинні комплекти тільки однієї з груп.
Демпфіруючі властивості гасителя оцінюють за значенням сили тертя, яке становить 4,65-5,2 кН (0,465-0,52 тс), або 5_5,5% підресореного ваги, що припадає на буксових вузол. Це відповідає коефіцієнту демпфірування 4-5, який представляє собою відношення роботи сил тертя гасителів до роботи пружних сил системи ресорного підвішування при зміні прогину від нуля до статичного.
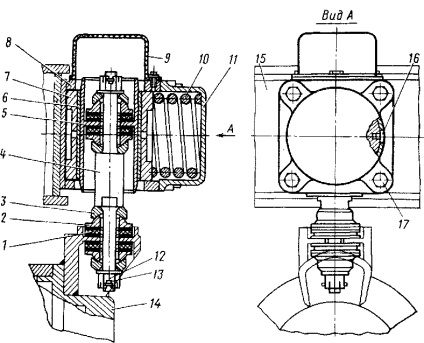
Фрикційні гасителі мають симетричну характеристику (однакова при русі вгору і вниз), не гасять вібрації (коливання з високою частотою і невеликими амплітудами). Вони застосовуються на тепловозі для гасіння вертикальних коливань, які можуть мати амплітуду ± 30 мм і частоту до 2 Гц, і бічний качки підресорених мас. Гасителі встановлюють в першій ступені підвішування між підресореними (рама візка) та непідресореної (букса) елементами ходових частин екіпажу. Гасіння коливань силою сухого тертя, природно, супроводжується інтенсивним зносом (близько 0,05 мм / год) поршня гасителя і фрикційних накладок. Тому експлуатаційний ресурс цих швидкозношуваних елементів гасителя не більше 400 тис. Км пробігу тепловоза.
Роботи з підвищення довговічності гасителів коливань ведуться в напрямку зменшення сили тертя спокою, вдосконалення кінематики приводу гасителів, застосування більш зносостійких фрикційних матеріалів і, нарешті, створення гідравлічних гасителів коливань об'ємного типу і рідинного в'язкісно тертя. В останніх опір створюється силою рідинного тертя поліметаллсілоксановой рідини марки ПМС-800000, що має кінематичну в'язкість 0,8 м2 / с (800 000 сСт) і знаходиться в щелевом з радіальним зазором 0,20-0,65 мм че-тирехкамерном лабіринтовому просторі, утвореному ротором і статором гасителя. Сила опору пропорційна ширині зазору і змінюється від швидкості нелінійно (регресивна характеристика). Привід ротора гасителя здійснюється кривошип-но-шатунним пружним механізмом від буксового вузла ходової частини екіпажу. Ротаційні рідинного тертя, а також гідравлічні об'ємного типу гасителі коливань проходять стендової-екс-експлуатаційного ресурсні випробування.