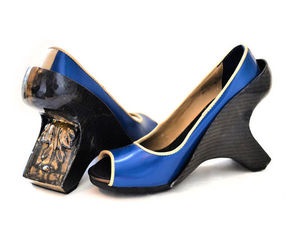
Всім привіт! Ні, це не черговий майстер клас, просто хочу поділитися своїм досвідом роботи з карбоном.
Карбон - це полімерний композиційний матеріал ізпереплетенних ниток вуглецю, розташованих в матриці з полімерних (наприклад, епоксидних) смол.
Основна складова частина вуглепластика це нитки вуглецю (по суті, те ж саме що і, наприклад, стрижень в олівці).
Такі нитки дуже тонкі, зламати їх дуже просто, а ось порвати досить важко.
З цих ниток сплітаються тканини. Вони можуть мати різний малюнок плетіння (ялиночка, рогожа і інш.). Для додання ще більшої міцності дані тканини з ниток вуглецю кладуть шарами, щоразу змінюючи уголнаправленія плетіння. Шари скріплюються за допомогою епоксидних смол.
Застосовується для ізготовленіялёгкіх, але міцних деталей, наприклад: кокліти і обтічники в Формуле1, спінінги, щогли для віндсерфінгу, бампери і пороги на спортивних автомобілях, несучі гвинти вертольотів.
Пару років тому я вирішила, що хочу створити колекцію взуття з карбону або як мінімум з карбоновими деталями (для участі у будь-яких конкурсах і показів). Досвіду в роботі з карбоном у мене не було, зате був знайомий, який цим трошки займався, і обіцяв мені все розповісти, показати і підігнати матеріали (карбонову тканину, смолу, затверджувач).
На жаль, фотографій самого процесу мало, тому спробую пояснити словами.
Використовувалися наступні матеріали.
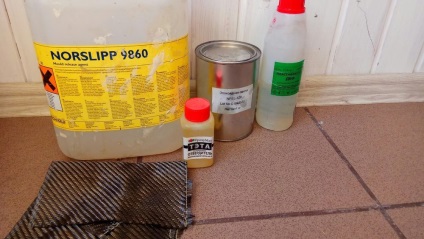
Карбонова тканину (щільність на жаль не знаю, так як купувала з рук) Роздільник NORSLIPP 9860 Епоксидна смола NPEL-128 (пішло десь 2,5 літра) Затверджувач дельта Пластифікатор ДБФ
Перше що потрібно було зробити - це форми, на основі яких будуть робитися карбонові деталі взуття (надалі деталі з форм знімаються, крім підборів).
Форми (або їх частини) для майбутніх карбонових деталей я робила відразу на взуттєвих колодках. Колодку я обклеювала скотчем і тканиною і промазують клеєм ПВА. Що б врахувати товщину матеріалів зверху цієї конструкції я робила шар скульптурного пластиліну товщиною приблизно 8 м. В ідеалі поверхня на яку буде натягатися карбонова тканину повинна бути ідеально рівною, але, відразу скажу, що ідеально-ідеально рівній поверхні у мене не вийшло =)
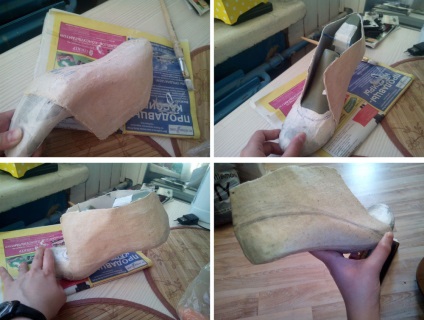
На фото конструкція ще без пластиліну, просто пап'є-маше
Перед приклеюванням тканини, форму промазуйте роздільником і чекала до повного висихання (приблизно 10 хвилин). Промазуйте в два шари, що б уже напевно. Чи не наносила роздільник тільки на готові підбори (окремі або є частиною деталі).
Я змішувала затверджувач, пластифікатор і смолу в пропорціях 1: 1: 8 (1 частина затверджувач, 1 частина пластифікатора і 8 частин смоли). Так як деталі не великі, то замішувала я маленькими порціями, і найзручніше це було робити звичайними шприцами на 10-20 кубиків, і на один прийом вистачало 8-20 мл, в залежності від деталі. Замішувала я в звичайній пластиковому або паперовому стаканчику. В процесі роботи я помітила, що дуже багато (час висихання, прозорість і іноді навіть колір) залежить від температури в приміщенні. У більш жаркі дні я могла змушують в пропорціях 1: 1: 10, в більш холодні 1: 1: 6.
Головне при замішуванні що б смола не була занадто вузький. Я ставила банку зі смолою перед початком роботи в гарячу воду на 5 хвилин, і потім, при необхідності, трохи підігрівала феном вже замішану смолу прямо в склянці.
Я приклеювала тканину на форму тієї ж смолою. Тобто розведену смолу я наносила спочатку на форму, потім приклеювала тканину, і промащувати зверху.
Так як форми не прості, то мені доводилося додатково закріплювати тканину що б вона не відклеюватися.
Надлишки тканини, за які я закріплювала тканину, я зрізала після висихання смоли. В принципі, один два шар карбону легко зрізаються ножицями або ножем, а якщо шарів було більше я використовувала дремель з відрізним диском.
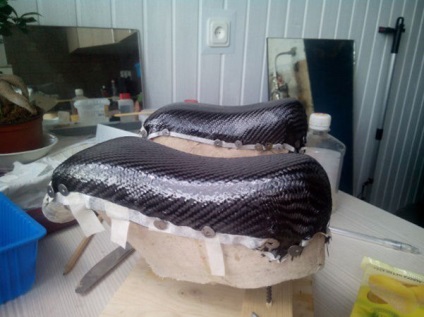
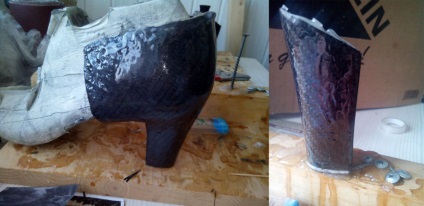
Так як я робила це майже три роки тому, то інформації про роботу з каброном майже не було, тому доводилося імпровізувати на ходу грунтуючись на тій інформації яку мені розповіли перед роботою.
Спочатку я працювала за принципом приклеїла тканину - завдала шар-повністю висушила - зашкурена, приклеїла - завдала - висушила - зашкурена, і потім так само кілька шарів смоли. Надалі я стала робити по іншому: приклеювала тканину, наносила шар, чекала поки він підсохне і перестане нагріватися, і завдавала наступний шар смоли (це вже на останніх шарах тканини, а нові шари карбону я приклеювала на повністю висохлу і зашкуренную смолу). Коли мене задовольняв загальний шар смоли я чекала до повного висихання і вже потім починала шліфувати. Особливою візуальної різниці між цими способами я не помітила, зате робота пішла набагато швидше коли я перестала зачищати кожен шар окремо.
Шліфувати я починала наждачним папером 200 мкм поступово доводячи до 1200 мкм. Так як я робила це вдома, то у мене була можливість шліфувати під струменем води, так було менше пилу і шліфувати було набагато приємніше ніж по сухому. Але деталі на одну модель я зіпсувала, почавши шліфувати під водою. Один з нижніх шарів трохи не досох і від вологи смола помутніла. Скриплячи серцем довелося зафарбувати всю робити.
Що б смола швидше сохла і на неї не падала пил, деталі накривала коробкою з лампочками. Під лампами смола повністю висихала приблизно за годину.
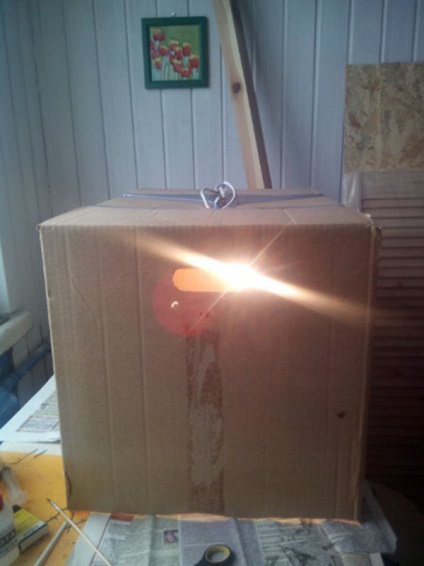
Для створення каблуків на одній з моделей я використовувала консоль з поліуретану, пофарбувала її звичайними акриловими фарбами і залила тієї ж смолою. Вийшов прозорий прямокутник зі скошеним краєм і декором всередині (на жаль окремого фото готового каблука немає). Далі я приклеїла каблук до вже готової карбонової деталі і зверху поклала ще пару шарів тканини що б закріпити каблук і з'єднати його з основною деталлю. В цілому ось у цій деталі у мене вийшло п'ять шарів тканини, в деяких місцях шість. Хочу зауважити, що пластилін, звичайно, не найвдаліший матеріал для створення форм, так як після зняття дуже довго довелося вичищати внутрішню поверхню, хоча в деяких місцях знімалося легко.
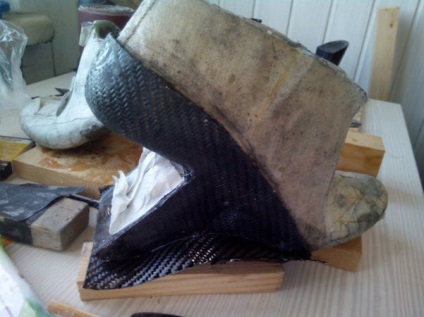
Останній етап роботи - це полірування. Можна звичайно це робити вручну, поступово збільшуючи зернистість шкурки, але я вирішила що з мене вистачить і віднесла спеціально навченим людям. Взуття я сама не затягувала, тільки проектувала, та й то, вирішила робити максимально прості конструкції що б вся увага була зосереджена на підборах. Ось що в результаті вийшло. Каблуки на основі поліуретанових декоративних консолей залитих смолою
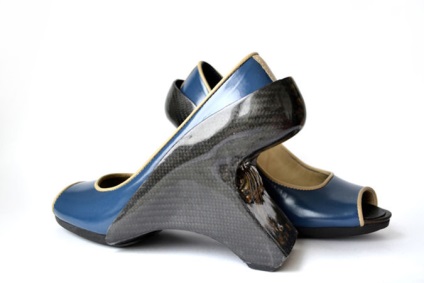
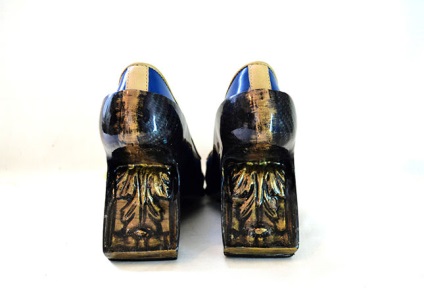
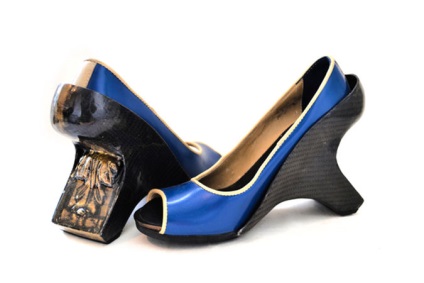
Ці деталі-накладки теж з карбону, тільки їх довелося зафарбувати бо смола помутніла = (
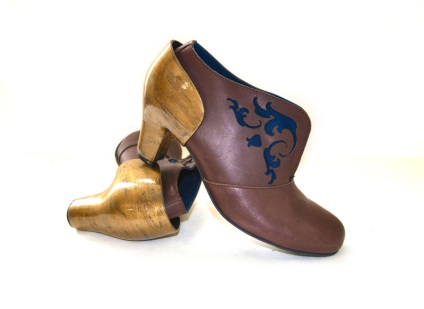
У цій моделі просто підбори обтягнуті карбоном (робила їх першими, для проби) з накладками з ABS пластику, роздруковані на 3D-принтері.
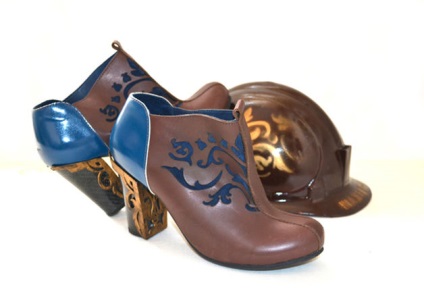
А в цій моделі немає нічого з карбону, просто вирішила показати все колекцію цілком. Тут каблук з дуба, робили на фрезерному верстаті.
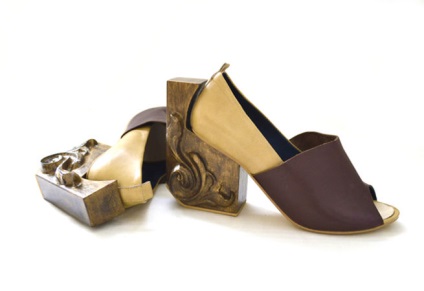
Підсумую: Я так і не змогла вирішити проблему бульбашок повітря в смолі, тому при поліруванні в ці бульбашки природно забивалася поліроль і поверхню подекуди вийшла з білими крапочками, але їх майже не видно.
Якби робила це зараз, то напевно б робила по-іншому, швидше за все з вакуумом, і безумовно приділила більше уваги підготовці (опрацювання ескізів, створення і вирівнюванню! Форм).