Для успішного ведення процесу прокатки дуже важливо мати правильний вхід і вихід смуги з валків. Це забезпечує валковая арматура. Сюди слід віднести всі види обладнання та пристроїв, які необхідні для направлення і утримання прокочується смуги як при подачі до валянням, так і при виході її з валків. У зв'язку з цим арматуру прокатних станів можна поділити на три основні види:
- Вступну арматуру, що забезпечує правильну подачу смуги в валки і утримання її в потрібному положенні під час прокатки. До таких деталей і пристосуванням ставляться лінійки, воронки, коробки, пропуски і ін.
- Вивідні арматуру, що забезпечує правильний вихід смуги з валків і відповідний напрям при подальшому русі. Сюди слід віднести лінійки, які зберігають необхідне положення смуги в горизонтальній площині, і проводки в вертикальній площині, що оберігають від оковиванія (окільцьовування) валків металом.
- Передавальні пристрої, які передають смугу від однієї кліті до іншої або в межах однієї кліті, з кантуванням або без кантування смуги. До цього виду пристроїв відносять різні трубки, пристосування для кантування виходить з валків смуги (спіральні проводки. Кантуються ролики); обвідну арматуру, що забезпечує автоматичну передачу смуги з однієї кліті в іншу і застосовується на лінійних дротових, дрібносортних, а в деяких випадках і на середньосортних станах.
Вибір і установка арматури істотно впливають на продуктивність прокатного стану, на отримання точних розмірів і якісної поверхні прокату. Тому конструювання, підготовки та встановлення арматури в прокатних цехах приділяють серйозну увагу.
Деталі валковой арматури в процесі роботи відчувають значні динамічні впливу з боку смуги. Тому їх роблять досить міцними і надійно закріплюють. При цьому кріплення не повинно ускладнювати успішної регулювання і швидкої заміни в разі потреби. На сортових станах арматуру встановлюють на опорних брусах, закріплених в спеціальних пазах по обидва боки валків паралельно їх осі.
Блюмінги, слябінги і деякі інші стани часто не мають спеціальної арматури, так як подача металу у валки і його вихід з валків забезпечуються рельгангамі і лінійками-маніпуляторами, а поперечні розміри смуг, прокочуються на цих станах, практично виключають таке явище, як оковиваніе валків.
До валковой арматурі, яка встановлюється в сторону кліті, відносяться, зокрема, напрямні лінійки, які є нерухомим продовженням буртов струмка. Вони забезпечують спрямовану подачу смуги в валки. Якщо немає необхідності безперервно утримувати смугу при її подачі та прокатки, наприклад в прямокутних або ромбічних калібрах, то окремі лінійки замінюють литим столом з постійними лінійками, які мають у своєму розпорядженні відповідно до кожного калібру. З вихідний боку при прокатці, наприклад, овалу в круглому калібрі смугу доводиться безперервно утримувати від звалювання і скручування. Лінійки при цьому виготовляють з відповідною профилировкой, причому їх дуже ретельно встановлюють за калібром в приймальні коробці. Такі профільовані лінійки називають пропусками. В даному випадку спостерігаються особливо важкі умови служби направляє арматури, так як пропуски при роботі стикаються з гарячим металом і відчувають високі швидкості ковзання. Все це призводить до інтенсивного зносу робочих поверхонь пропусків, а при прокатці стали (особливо нержавіючої, жаротривкої і ін.) Можна спостерігати значне наварювання (налипання) металу на контактну поверхню пропусків, що призводить до утворення на прокочується металі рисок і задирок, а в кінцевому підсумку до шлюбу.
Тривалий час пропуски виготовляли з вибіленого або сірого чавуну. Хоча згодом пропуски почали виготовляти з легованої сталі з подальшою термічною обробкою, стійкість їх проти стирання і налипання металу на робочу поверхню не може вважатися задовільною. Успішно вирішується питання заміною тертя ковзання тертям кочення, т. Е. Заміною звичайних пропусків роликовими.
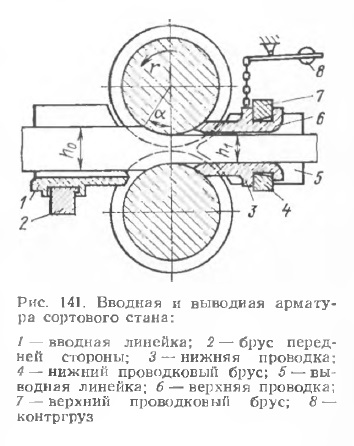
Дуже великий вплив на успішну роботу прокатної кліті надає вивідні арматура (рис. 141,5, 5, 6). Різниця в діаметрах робочих валків і їх окружних швидкостей (за однакової кількості частоти їх обертання) викликає вигин смуги по виході в бік валка з меншим діаметром. Крім того, неправильна установка валків, нерівномірний прогрів металу перед прокаткою, нерівномірна деформація, що викликається формою калібру або формою заготовки, неправильна подача смуги в валки можуть привести до появи вигину смуги у вертикальній або горизонтальній площинах або закручування її навколо своєї осі при виході металу з валків . Щоб запобігти цьому, на виході смуги з валків встановлюють вивідну арматуру - лінійки, а також нижню і, де необхідно, верхню проводки, які зберігають правильний вихід смуги у вертикальній площині. Проведення оберігають валки від оковиванія прокочується смуги під час виходу переднього кінця. При значних перетинах смуги проводки сприймають великі навантаження. Тому їх, як правило, виготовляють кованими зі сталі.
Проводки, як це видно з рис. 141, 3, 6, встановлюють заостроенним кінцем на валок і п'ятою на Проводковая брус. Носок проводки повинен постійно щільно притискатися до валку, інакше виходить смуга буде вибивати проводку, що може привести до аварії на стані. Нижня проводка притискається до валку своєю масою, щільне ж прилягання верхньої проводки до валку забезпечується пружинами або контрвантажем (див. Рис. 141,5).
Найбільшого поширення набула валковая арматура ковзання, що обумовлено простотою конструкції і надійністю в експлуатації. Валковая арматура ковзання складається з вступних і вивідних лінійок або профільних проводок, які кріплять на Проводковая брусі. Для підвищення жорсткості валковой арматури ковзання фасонні проводки встановлюють в жорсткій закритій коробці. Залежно від розташування профільні проводки ділять на нижні і верхні. Вони спираються на валок і притискаються до коробки стяжними болтами. Профільні проводки виготовляють зі сталі для станів гарячої прокатки і з бронзи для станів холодної прокатки.
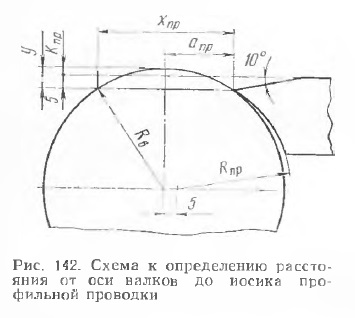
Велике значення для запобігання оковиванія валків має ретельна підгонка вивідний арматури. Носик профільних проводок повинен щільно прилягати до струмка калібру по всьому контуру (рис. 142). Розміри профільних проводок визначають наступними залежностями:
де R в - радіуси валка і проводки; aпр - відстань від осі валка до носика проводки; Хпр - хорда (береться в залежності від діаметра валка); Кпр - відстань від дна проводки до дна калібру (менше значення для холодної прокатки і більше для гарячої).
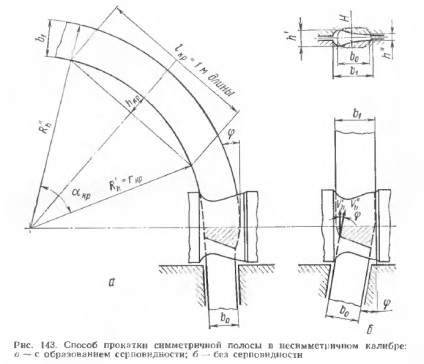
Вперше питання вигину смуги в горизонтальній площині розглянув І. М. Павлов. Користуючись поняттям природних витяжок, він встановив, що довжини країв смуги після прокатки обернено пропорційні їх толщинам. Надалі В. І. Видрін показав, що вигин смуги в горизонтальній площині при виході з валків є результатом відмінності в витяжці крайок смуги не в усьому осередку деформації, а тільки в зоні випередження. Це пояснюється тим, що в площині виходу смуги з осередку деформації швидкості лівої (товстої) V'h і правої (тонкої) V »h крайок різні (рис. 143). Виходячи з цих уявлень, можна написати
де l'h. h ', R'h. S'h. ε '- відповідно довжина, товщина, радіуса кривизни, швидкість випередження і відносне обтиснення з боку лівої (товстої) кромки смуги; l »h. h », R» h. S''h. ε »- то ж з боку правої (тонкої) кромки смуги; b1 - ширина смуги після прокатки.
Зазвичай випередження значно менше одиниці; в таких випадках можна використовувати спрощену залежність, отриману В. І. Вибріним:
Таким чином, різні подовження волокон смуги, викликають різний розподіл внутрішніх силових факторів (напруг по перетину, зване вигином), призводять до утворення серповидно. Смуга буде виходити з валків прямий, якщо швидкості її точок по ширині дорівнюватимуть.
Для визначення значення серповидно (рис. 143) маємо
де αкр - кут серповидно між двома точками на колі радіуса Rкр на відстані lкр. рівному 1 м, який визначається за формулою αкр = 57,3lкр / Rкр = 57300 / Rкр.
Для усунення гвинтоподібно профілю у ВНИИМЕТМАШ розроблений новий спосіб прокатки, що включає дві операції в одному безперервному процесі; подачу смуги в валки під потрібним кутом до осі прокатки і згинання в осередку деформації до необхідної величини.
Існуючий процес поздовжньої прокатки складних фасонних профілів вимагає суворого дотримання технологічного режиму і високої культури виробництва. Незначна зміна хоча б одного або декількох технологічних параметрів, наприклад нерівномірні нагрів по ширині смуги і знос валків, призводить до утворення серповидно і, як наслідок, до Гвинтоподібне. Зазначеного явища при прокатці можна уникнути, якщо задається смугу піддати попередньому вигину, т. Е. Змусити одні шари подовжиться більше інших. У цьому випадку попередній вигин задається смуги компенсує різницю подовжень між товстої і тонкої крайками при нерівномірному висотної деформації. Для здійснення попереднього вигину задається смуги встановлюють вступні проводки під потрібним кутом φ до осі прокатки. Різниця подовжень товстої і тонкої крайок смуги тим більше, чим більше різниця обтиснень, а отже, різниця витяжок і швидкостей переміщення. Однак арматура ковзання по стійкості поступається арматурі кочення. Швидкий знос арматури ковзання негативно позначається на продуктивності станів, так як заміна арматури та подальша настройка вимагають великих витрат часу.
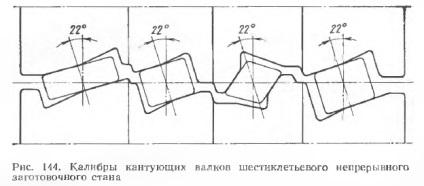
Найбільш радикальним способом підвищення стійкості арматури є заміна ковзання смуги коченням по її робочих поверхонь. У цьому випадку використання для тіл кочення навіть звичайної конструкційної сталі дозволяє досягти набагато більшої стійкості арматури в порівнянні зі стійкістю арматури ковзання, виготовленої з високолегованої сталі.
Позитивними сторонами застосування арматури кочення є майже повна відсутність ковзання між роликами і смугою; відсутність налипання частинок гарячого металу на поверхню роликів; поліпшення якості готової продукції; скорочення простоїв стану, що обумовлено високою стійкістю роликового арматури; зниження витрати енергії при прокатці, оскільки відсутнє тертя ковзання між смугою і арматурою, на подолання якого потрібна значне зусилля.
Діаметр і довжина бочки Канта валків приблизно ті ж, що і робітників. Шейки Канта валків встановлюють в подушках, укріплених в станині робочої кліті. Калібри Канта валків (рис. 144) відповідають кантуемой смузі. Кут скручування смуги визначають за рівнянням
де ак - відстань від осі робочих валків до осі Канта валків; хξ - відстань між осями робочих клітей; αξ - кут кантування (зазвичай 90 або 45 °).
Ширина Канта пасків повинна становити 0,3-0,4 ширини смуги. Кут кантування регулюють зміною відстані між Канто валками або зміщенням одного з них в осьовому напрямку. Стійкість Канта валків вище стійкості Канта проводок в кілька сотень разів і характеризується наступним:
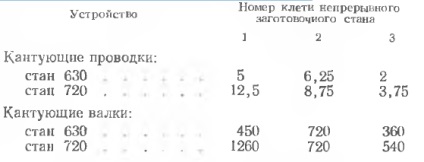
Основним робочим елементом, властивим будь-яким конструкціям валковой арматури кочення, є ролик, за яким смуга котиться під час її руху через арматуру.
Конструкція роликів і спосіб їх установки в арматурі багато в чому визначають її експлуатаційні якості. Для кращого утримання високих смуг ролики вступної арматури повинні бути максимально наближені до валянням. Збільшення діаметра роликів призводить до збільшення відстані від них до валків. При прокатці круглих (квадратних) профілів діаметр роликів можна визначити за емпіричною формулою
де dmax. dmin - найбільший і найменший діаметри прокочуються кіл.
Висоту ролика зазвичай вибирають рівній
де h к - ширина врізу калібру в ролик.
Ролики виготовляють з матеріалів, добре працюють на знос при високих температурах (чавуну з добавками хрому, нікелю, вольфраму та інших елементів, а також стали марок ШХ15, 40Х, Х10С2М і ін.). Найкращі результати отримані при виготовленні роликів зі сталі марки Х10С2М. В якості замінників цієї порівняно дорогої стали можуть бути застосовані стали 35Г2С і 38ХМОА, однак стійкість виготовлених з них роликів трохи нижче.
Для обробки поверхні каліброваних роликів застосовують копіювально-шліфувальні і шліфувальні верстати. Поверхня каліброваних роликів повинна бути чистою; це попереджає налипання на ролики частинок металу.