Відомо, що найчастіше першим критерієм вибору нової запчастини є ціна. Ціни на вторинному ринку дуже різноманітні, але не вони повинні визначати переваги. Існує кілька основних аспектів, на які і слід звернути увагу, вибираючи нове обладнання.
Параметри, що визначають якість
На ефективність придушення шуму і безпеку використання всієї вихлопної системи впливають в першу чергу такі фактори, як конструкція глушника, діаметр внутрішніх труб, надійність і спосіб кріплення елементів системи до шасі. Також надзвичайно важливим є якість швів і ущільнень, які використовуються в з'єднаннях і деталях системи.
Глушники, що поставляються на вторинний ринок, часто відрізняються від оригінальних конструкцій, що встановлюються автовиробником при випуску автомобіля. Навіть великі компанії, що виробляють глушники, спрощують оригінальну конструкцію, якщо вона виявляється занадто, на їх погляд, нетехнологічною. Існують і такі постачальники запчастин, які навмисне гранично спрощують заводські конструкції випускних систем. Знижуючи власні витрати, вони мають можливість запропонувати покупцеві дуже дешеві, порівняно з оригінальними конструкціями, продуктові лінійки.
Зміна конструкції глушника, при збереженні його оригінальних параметрів і, головне, характеристик, вимагає проведення ряду тестів і досліджень. Виробники, що змінюють конструкції без будь-яких погоджень і тестів своїх виробів, часто реалізують їх на ринку, а потім їх продукція порушує нормальну роботу всієї вихлопної системи автомобіля.
Ще одним важливим фактором, що визначає вибір вихлопної системи, є використання відповідних діаметрів труб в глушнику. Адже можна сконструювати глушник, використовуючи труби заниженого, від оригіналу, діаметра, і він буде істотно знижувати шумовий фон. Але подібне «дросселирование» потоку вихлопних газів обов'язково відіб'ється на зниженні ефективності роботи двигуна.
Не можна не зупинитися на проблемі матеріалів, використовуваних в глушники. На вихлопну систему діють такі шкідливі зовнішні фактори, як різкі зміни температури, наприклад при їзді під час дощу. Несприятливо впливає на елементи системи випуску відпрацьованих газів і експлуатація в зимовий період, коли на деталі діють низькі температури; контакт зі снігом, сіллю викликає утворення вогнищ корозії. А якщо врахувати, що і внутрішня поверхня елементів глушника піддається впливу кислих середовищ, то стає зрозуміло, чому вибір матеріалу глушника впливає не останнім чином на термін його служби.
Глушники, що встановлюються на автозаводі, як правило, виготовлені з листів і труб, матеріалом яких є нержавіючі і жароміцні стали. Через високу ціну цих матеріалів деталі системи випуску газів, призначені для реалізації на вторинному ринку, роблять з рядовий стали, але обробляють з обох сторін антикорозійним покриттям, головним чином на основі алюмінію. Покриття наноситься шаром 80 ... 120 г / м 2. товщина визначає стійкість поверхні до корозії. Якість покриття можна оцінити візуально: якщо шар завдано тонкий, то поверхні деталей не блищать, а мають матовий алюмінієвий відтінок.
Еластичне з'єднання між випускним колектором і каталізатором Ford Mondeo
Важлива, безумовно, для продовження терміну служби системи випуску газів товщина самого металу глушника, оскільки чим він товстіший, тим довше виріб прослужить.
Крім стали в конструкції глушника використовуються матеріали, які поглинають або ж відображають звуки. З функціями шумозаглушення добре справляється скловолокно. Матеріал характеризується відмінними характеристиками глушіння шуму і, в порівнянні з іншими звукоізоляційні технологіями, не завдає шкоди навколишньому середовищу. Скловолокно не поглинає конденсат, але сприяє його випаровуванню з глушника. Цей матеріал не змінює своїх властивостей навіть при температурі + 900 ° С. Технологія текстурирования скловолокна дозволяє ретельно заповнити «кишені» глушника.
Важливо пам'ятати, що всі елементи системи випуску відпрацьованих газів слід монтувати в суворій відповідності з призначеними для них місцями на днище кузова.
Вихлопна система повинна бути закріплена без напружень, її розташування повинно забезпечувати можливість вільного зсуву під дією зміни навколишнього і внутрішньої температури. При заміні відпрацювала свій ресурс вихлопної системи на нову еластичні гумові елементи також змінюються.
Необхідно також додати, що при установці нового глушника треба звернути увагу на естетичний вигляд і антикорозійний захист зварних швів, на кронштейни кріплення, розташовані на трубах і резонаторах. Метал кріплень повинен бути певної товщини, а самі кріплення повинні бути приварені звареними швами достатньої довжини. Сварка частин системи є найважливішим фактором, що впливає на надійність всієї вихлопної системи, якій доводиться постійно сприймати динамічні навантаження різної сили.
Каталізатори на сторожі чистоти «вихлопу»
Як відомо, призначенням вихлопної системи є відведення з двигуна відпрацьованих газів, а також зниження шумового ефекту, що виникає в результаті пульсації тиску вихідних газів. Однак в сучасних авто вихлопна система виконує також важливу роль і з очищення відпрацьованих газів. З цією метою в вихлопні системи вводяться такі компоненти, як каталітичні нейтралізатори, кисневі датчики, сажові фільтри і деякі інші пристрої.
У зв'язку з відмінностями в технологіях очищення шкідливих викидів каталітичні реактори, призначені для «дизелів», не можна використовувати в бензинових двигунах, і навпаки. У дизельних двигунах завданням очисних пристроїв є зниження викидів окису вуглецю, яка утворюється при роботі на збідненої суміші. Зниження викидів оксиду азоту в значній мірі забезпечує дію використовуваної в двигунах системи рециркуляції відпрацьованих газів (EGR), а також застосування системи селективної каталітичної нейтралізації (SCR). Хоча в Росії дана технологія, в зв'язку з цілою низкою недоліків, а саме високою ціною, низькою температурою замерзання одного з головних компонентів даної технології, всього -11,5 ° С, підвищеними вимогами до якості дизпалива, використовується досить рідко.
Завданням каталітичного нейтралізатора, більше відомого в народі під назвою каталізатор, є перетворення шкідливих сполук, що утворюються в процесі згоряння палива в двигуні, в дещо менш шкідливі для екології речовини. У двигунах з іскровий системою запалювання каталізатори окислюють і знижують шкідливість трьох з'єднань. NOx. або оксид азоту, перетворюється в N2 або нейтральний азот, вуглеводень CH перетворюється в H2 O, а окис вуглецю CO стає вуглекислим газом CO2. Тому в бензинових двигунах каталітичний нейтралізатор називають трикомпонентним.
Хімічні реакції відбуваються при робочій температурі каталізатора 350 ... 800 ° С. Для оптимального здійснення процесу згоряння палива необхідно збереження стехіометричного складу горючої суміші. Для такої суміші встановлюється спеціальний коефіцієнт надлишку повітря λ = 1. Це означає, що для згоряння 1 кг палива без освіти залишкового кисню потрібно 14,7 кг повітря. До речі, при використанні в якості палива пропану співвідношення повітря / паливо змінюється і дорівнюватиме 15,6: 1.
Як матеріали, що прискорюють проходження реакцій в каталізаторах, використовують метали - паладій, платину, родій, рутеній. Ці матеріали напилюється на монолітний блок, що знаходиться всередині реактора і нагадує своїм зовнішнім будовою бджолині стільники.
Звичайно, згорання відбувається і при λ <1 или λ> 1, однак тільки при λ = 1 рівень викидів шкідливих сполук мінімальний. Треба сказати, що уприскування точно дозованим суміші можуть забезпечити тільки інжекторні пристрої, контрольовані і керовані бортовим комп'ютером. Тому каталізатори працюють в основному в автомобілях з інжекторної системою подачі палива, а в машинах, де горючу суміш готує карбюратор, використовуються дуже рідко.
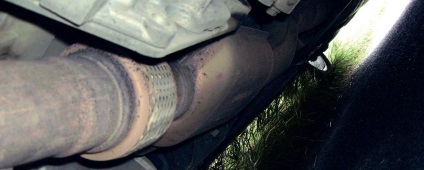
Каталітичні блоки бувають керамічними та металевими. Керамічна конструкція характеризується поділом на квадратні, в перерізі, стільники, з товщиною стінок між каналами 0,05 ... 0,15 мм. У сталевих блоках стінки значно тонше, всього 0,03 ... 0,07 мм. Така будова дозволяє сталевим блокам пропускати більший потік вихлопних газів. Металеві блоки значно частіше керамічних встановлюють на нові автомобілі, вони відрізняються великим тепловим опором, тому, наприклад, тільки сталеві каталітичні решітки використовують в двигунах, що працюють на газі.
До переваг керамічних блоків можна віднести більш милозвучна для людського вуха звук, видаваний ними під час роботи, ніж утворюється при проходженні вихлопних газів через металеві «стільники». Однак керамічний блок відрізняється набагато менш міцною структурою, ніж металевий, стійкість його до механічних пошкоджень низька, і дуже часто вони виходять з ладу через появу тріщин, які утворилися від ударів. Також керамічні блоки гірше металевих переносять перепади температур, тому, як писалося вище, «кераміку" не застосовують у двигунах, що працюють на газі.
Експлуатація каталізатора - в жорстких рамках
Однак симптоми «втрати працездатності» каталізатора можна виявити в процесі експлуатації автомобіля. Втрата потужності, проблеми з запуском, галаслива робота двигуна - все це може бути ознакою того, що каталізатор пошкоджений. Також слід перевірити, в якому стані знаходиться закінчення вихлопної труби. Якщо воно сильно закопчено, вкрите сажею, це вірний знак того, що вихлопна система, і особливо каталізатор, може мати серйозні дефекти.
Робочий ресурс сучасних каталізаторів постійно збільшується, проте більшість виробників рекомендують міняти каталізатор після 120 ... 150 тис. Км пробігу. Бувають, звичайно, випадки, коли каталізатори виходжують і по 250 тис. Км, але це відноситься до розряду винятків.
Для продовження «життя» каталізатора необхідно ретельно стежити за тим, що потрапляє в заправний бак машини. Навіть незначна кількість етилованого бензину може необоротно пошкодити каталізатор. Тому особливо небезпечно заправляти автомобіль десь на трасі, набуваючи вже розлите в каністри пальне.
Крім того, використання палива низької якості, забрудненого, призводить до того, що за рахунок високої температури вихлопних газів внутрішня частина каталізатора може розплавитися. Нормальна робота каталізатора відбувається приблизно при 600 ° С, а неякісне паливо може підвищити температуру до 900 ° С.
Необхідно також систематично контролювати стан свічок запалювання. Відсутність іскри в одному з циліндрів буде приводити до стікання незгорілого бензину в вихлопну систему, що негативно відіб'ється на стані каталізатора.
Каталітичний нейтралізатор може бути зруйнований одним ударом об бордюр або виступаючий камінь, при русі по пересіченій місцевості. Слід також побоюватися різкого охолодження каталізатора, яке може статися, наприклад, при перетині автомобілем глибокої калюжі.
Скорочення шкідливих викидів у вихлопних газах в значній мірі залежить від кисневого датчика, або лямбда-зонда. Конструкція цих пристроїв зазнала з роками значні зміни: якщо спочатку це були звичайні датчики, то сьогодні це вже мікропроцесорні системи.
Кисневий датчик: 1 - електрораз'ем, 2 - кабель, 3 - корпус, 4 - різьблення на корпусі для кріплення, 5 - захисний кожух датчика
Очищення вихлопних газів спочатку проводилася тільки з використанням каталітичних нейтралізаторів. У їх функції входило прискорення хімічної реакції, в результаті якої шкідливі сполуки повинні були перетворитися в менш шкідливі. У 70-х рр. минулого століття був винайдений кисневий датчик. З'єднання цього приладу з каталізатором дозволило значно підняти рівень очищення відпрацьованих газів. Лямбда-зонд нагрівається швидше каталізатора, а значить, система управління двигуном швидше починає отримувати сигнали про зміни вмісту кисню у вихлопних газах, яке, як відомо, визначає оптимальний для згоряння склад паливно-повітряної суміші.
Важливим параметром є температура кисневого датчика: при низькій температурі датчик не функціонує, а при дуже високій або при частих значних температурних перепадах можуть виникати поломки датчика, знижується його термін служби.
Щоб стабілізувати температурний режим роботи кисневих датчиків, зробити їх незалежними від температури відпрацьованих газів, сучасні лямбда-зонди оснащують електричними підігрівниками. Постійна робоча температура дозволяє отримувати сигнали від датчика в більшому діапазоні режимів роботи двигуна, що збільшує в цілому чистоту вихлопних газів автомобіля. Завдяки появі незалежних від навколишньої температури підігріваються датчиків стали застосовувати монтаж відразу двох кисневих датчиків - до і після каталізатора. У цьому випадку контроль кількості кисню в суміші значно більш точний, а функціонування всієї вихлопної системи більш надійно. Крім того, таким чином легко контролювати ефективність роботи каталізатора.
Один з найбільш відомих виробників кисневих датчиків - японська компанія Denso. Перші датчики компанія випустила в 1977 р і за минулі роки Denso поставила сотні мільйонів своїх датчиків виробникам автотехніки по всьому світу. Сьогодні високотехнологічні конструкції Denso доступні покупцям вторинного ринку, причому якість продукції не поступається якості датчиків, що йдуть на конвеєри провідних автобудівників.
Програма випуску Denso охоплює 277 позицій і 1700 модифікацій. Велика їх частина - унікальні розробки інженерів компанії. Серед таких розробок - датчики цирконієво-оксидні, циліндричного або плоского виконання, з підігрівом і без такого, титанові датчики, лямбда-зонди для збіднених сумішей, лінійні A / F і інші.
Не менш відома продукція фірми NGK. За останні 30 років компанія реалізувала більше 600 млн кисневих датчиків марки NTK. Протягом останнього десятиліття підприємство стало одним з основних постачальників подібних компонентів, як на вторинному ринку, так і при комплектації нових машин.
Збільшенню попиту на лямбда-датчики сприяють все більш і більш жорсткі екологічні норми, що вводяться в світі. Наприклад, на початку нинішнього століття, перед введенням OBD II (On-Board-Diagnosis II), вимогами передбачалася установка одного регулювального кисневого датчика, але з введенням OBD II кожен знову зареєстрований автомобіль повинен мати, крім регулюючого датчика, ще й діагностичний. Автомобілі з двома вихлопними трубами повинні бути обладнані сьогодні не менш як двома датчиками кожного виду.
Ще одним фактором, що обумовлює зростання продажів датчиків, стала поява двигунів зі зниженою витратою палива, зростає число реєстрованих мотоциклів, які в Європі сьогодні оснащуються трикомпонентними катализаторную нейтрализаторами і кисневими датчиками.
Лямбда-зонди теж ламаються
Однією з причин значних обсягів продажів кисневих датчиків є те, що пошкоджений датчик ремонту не підлягає, а змінюється на новий.
Однак лямбда-зонди, виготовлені відомими виробниками, як правило, не ламаються протягом всього терміну експлуатації транспортного засобу, якщо, звичайно, на них не впливають зовнішні причини, наприклад механічні удари, що призводять до появи тріщин в керамічних елементах або до обриву з'єднання корпусу і кабелю. Забруднення датчика осідаючими на нього твердими частинками, що вилітають разом з вихлопними газами, призводить до затримки його реагування на зміни в складі вихлопних газів і, як наслідок, викликає невірні дії електронного модуля, який керує роботою двигуна. Також і вплив вологи, що потрапляє в місця електроз'єднань, поява корозії на металевих поверхнях контактів відображаються на якості сигналів, які передаються датчиком.
Отже, як ми бачимо, якщо врахувати при виборі елементів системи випуску відпрацьованих газів всі необхідні для довгої і надійної роботи чинники, то можна дійсно отримати якісно і надійно працюючу систему, а досить висока ціна її буде цілком виправдана.