Розглянуто також особливості мікроструктури сталевих смуг з захисними покриттями двох видів:
1 _ покриття сплавом Al-Si, що містить 5-11% кремнію, товщина покриття 14-25 мкм;
2 - покриття чистим алюмінієм, товщина покриття
У покриттях обох видів присутній 2-4% заліза від розчиняється у ванні листа і металевих деталей самої ванни.
Реакційна зона містить інтерметаллідним з'єднання і розташовується між сталевою основою і шаром покриття (обох видів). Цей шар товщі у покриття виду 2 і складається, в основному, з Fe, Al5. Інтерметаллідним з'єднання дуже тендітні, тому бажано отримувати зону інтерметаллід- них з'єднань по можливості більш тонкої.
Застосування кремнію сприяє цьому, забезпечуючи мале відміну морфології і структури шару металу.
Легування алюмінієвого розплаву кремні§ / і (6-8%) і застосування відпустки при 400-450 ° С протягом 1-2 год з наступною дресируванням (обтиснення 1-2%) дозволяє отримувати алюмінійовані матеріал з достатньою пластичністю, підвищує стійкість покриття проти корозії і покращує жаростійкість.
Агрегат алюмінування діяв на Карагандинському металургійному комбінаті з нанесенням алюмінієвого покриття на холоднокатані смуги товщиною 0,35 мм. В даний час на цьому агрегаті виробляють цинко-алюмінієве покриття.
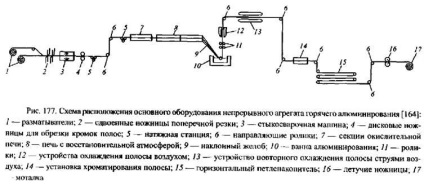
Оригінальна технологія нанесення покриття автомобільного листа алюміній-кремнієвими сплавами розроблена і освоєна фахівцями ДНІІЧермета і працівниками ВАТ «Северсталь». Для реалізації технології проведена реконструкція однієї з ванн для рідкого розплаву. За рахунок використання сверхнізкоуглеродістой IF-сталі вдалося отримати листи з високими для цього процесу фізико-механічними властивостями, практично не поступаються властивостям металу з покриттям цинком.
На ВАТ «Северсталь» випущені промислові партії горячеалюмінірованного листа для бензобаків автомобілів з прямим уприскуванням, а також для вихлопних систем автомобілів. Отримано позитивні результати. Але через відсутність потреби в такому металі в обсягах, що дозволяють організувати рентабельне виробництво, його в даний час в Росії не виробляють.
Світова практика роботи агрегатів гарячого алюмінування показала, що для отримання якісного алюмінієвого покриття необхідно при підготовці поверхні смуги застосовувати електролітичне знежирення в стандартних розчинах з подальшим травленням в 5-10% -ому розчині азотної кислоти з добавкою 10-20 г / л сечовини і мінімальним часом обробки 10-15 с. Як адгезійного шару слід використовувати водний розчин силікатів натрію і калію з концентрацією 3-5 г / л в кількості 4,5-7,5 г / м2, який не погіршує властивостей покриття і дозволяє поліпшити умови прокатки.
Товщина алюмінієвого покриття при нанесенні зануренням в розплав знаходиться в межах 25-50 мкм. У ванну з алюмінієвим розплавом додають флюс, що забезпечує блискучу поверхню покриття.
Електролітичне алюминирование застосовують рідко, так як осадження алюмінію через сильний негативного заряду у водних розчинах не вдається, а осадження з сольових розплавів хоча і можливо, але дорого. Зазвичай для електролітичного алюмінування використовують хлориди алюмінію і лужних металів.
Електрофоретичне алюминирование - нанесення алюмінієвого порошку на сталеву смугу методом електрофорезу або в електростатичному полі. При електрофорезі смуга рухається у вертикальному напрямку через ванну з електролітом, що представляє собою розчин алюмінієвого порошку в етиловому спирті з додаванням хлористого і азотистого нікелю, Аноди виконують з чистого алюмінію. Швидкість руху смуги через ванну становить 1,8-8,2 м / хв, напруга 30-220 В, щільність струму 10-70 А / дм. Отримане покриття сушать і ущільнюють холодної прокаткою. Після прокатки смугу нагрівають до 700 ° С для спікання алюмінієвого порошку з витримкою при 450-500 ° С протягом 2 3 годин. Отримане таким чином покриття має товщину 15-35 мкм, має високу пластичність, зберігає блискучу поверхню при нагріванні до 400 ° С.
Метод нанесення сухого алюмінієвого порошку в електростатичному полі заснований на взаємодії негативно заряджених частинок алюмінієвого порошку. Знежирену і протравлену смугу посипають рівномірним шаром сухого алюмінієвого порошку за допомогою механічного живильника-дозатора і вібраційних сіток. Між сіткою і смугою створюють електричне поле напругою 20 кВ при силі струму 110-115 А. Частинки порошку, потрапляючи в магнітне поле, отримують негативний заряд і в результаті взаємного відштовхування частинок забезпечується підвищена ступінь дисперсії і рівномірна товщина покриття. Покриття сушать, смугу з покриттям прокочують, отжигают в захисній атмосфері при 500-600 ° С. Товщина одержуваного таким способом покриття 50 мкм.
В Японії розроблена технологія нанесення алюмінієвого покриття на сталеву смугу методом порошкової металургії. Перед нанесенням покриття на лист в якості підкладки наносять тонке покриття з цинку, що запобігає здуття на покритті і покращує адгезію алюмінієвої плівки. яка наноситься на смугу з водної суспензії при 180 ° С. Після сушіння смуги прокочують і при термообробці в печі безперервної дії при температурі 600 ° С. Нове покриття товщиною до 60 мкм має чудовий зовнішній вигляд, хороші термостійкість і зчеплення з основою. Крім того, воно має високу корозійну стійкість і штампованих. Порошкове алюмінієве покриття товщиною 20 мкм по корозійної стійкості перевершує покриття, одержувані методом гарячого занурення - цинкове і алюмінієве.
У Великобританії фірмою BISRA розроблений спосіб нанесення алюмінієвого порошку товщиною 25 мкм. Електролітом служить розчин етілал- голя, в який введена суміш порошку алюмінію, хлориду нікелю і нітриду нікелю, катодом - сталева смуга. Надалі BISRA розвинула новий сухий спосіб, який знайшов практичне застосування з 1972 р на заводі «Тіба» (Японія). За цим способом сталеві листи шириною 1350 мм при 90-120сС обробляють в лужному розчині, потім в 5% -ому розчині сердитися кислоти, після чого покривають силікатом натрію або калію, службовцям клейкою основою. Порошок натрію, що подається з бункера, розподіляють на покривається аркуші за допомогою вібратора в електричному полі з напругою між електродами 15-20 кВ. Після цього слід нагрів (350 ° С, 1 хв), прокатка, повторне нагрівання (500-600 ° С при тривалості нагріву 15 с).
У Німеччині з 1971 р діє установка для двостороннього напилення алюмінію продуктивністю 15000 т / рік при максимальній ширині стрічок до 420 мм. Для випаровування алюмінію установка має дві електронні гармати потужністю по 250 кВт. Підігрів стрічки перед напиленням до 250-540 ° С також здійснюється за допомогою двох електронно-променевих гармат. Досвід роботи цієї установки дозволив розробити модель наступного покоління з річною продуктивністю 30000 т при двосторонньому покритті алюмінію на стрічки товщиною 0,1-1 мм при ширині 800 мм. Збільшена потужність підігріву до шести електронно-променевих гармат. У перспективі можна прогнозувати установку напилення стрічок шириною до 1500 мм при річній продуктивності 100 тис.т. Смугу з покриттям дресирують з обтисненням 0,7-1% і лакують. Товщина покриття 1-5,5 мкм на сторону. Зчеплення покриття з основним металом дорівнює 100% і не порушується до руйнування основи.
У 70-х роках минулого століття в ЦНІІЧермете був розроблений технологічний процес нанесення алюмінієвого покриття осадженням порошку в електростатичному полі. До переваг цього процесу слід віднести високу швидкість осадження покриття товщиною 20-60 мкм в поєднанні з корозійними і фізико-механічними властивостями матеріалу. Покриття мають особливо високу стійкість до атмосферної корозії і витримують глибоку холодну штампування без порушення цілісності і відшарування. Технологічний процес передбачає; підготовку поверхні сталевої штаби з подальшим змочуванням рівномірним шаром адгезійного розчину; осадження алюмінієвого порошку в електростатичному полі напруженістю 5-7 кВ / см; висушування вологи з порошкового шару і оксидування поверхні основи при 400-450 ° С і витримка 5-15 с; ущільнення порошкового осаду прокаткою з обтисненням сталевої основи на 3-6% і термообробку в садочних печах при 400-500 ° С при витримці 1-3 ч. В якості вихідного матеріалу для покриття використовували алюмінієвий порошок АСД-1, який наносять на холоднокатану відпалений і дресировану стрічку з низьковуглецевої сталі 08кп [164].
Представлені результати досліджень процесу дифузійного нанесення комбінованих покриттів цинк-мідь-алюміній і цинк-мідь-титан-алюміній, виконаних на дослідній установці. Встановлено, що ці комбіновані покриття зменшують крихкість і пористість цинкового покриття і підвищують корозійну стійкість матеріалу на сталевий основі - СТЗ.
Останнім часом публікацій за новими технологіями алюмінієвих покриттів і реалізації їх у виробництві вкрай мало. Це, ймовірно, пояснюється зазначеними вище недоліками таких покриттів, а також малими обсягами потреби в них.
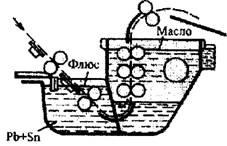
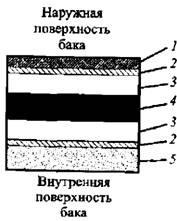
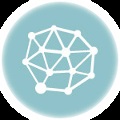
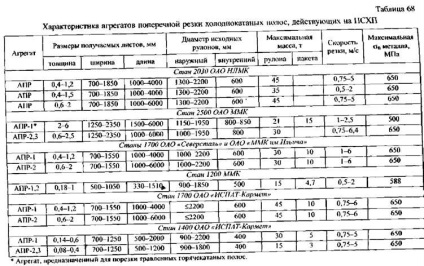