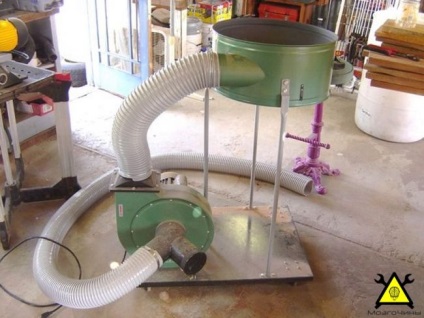
Складно уявити собі столярну майстерню без таких речей як верстак, токарний верстат, різні пилки, рубанки та інші інструменти. Це природно, тому що за допомогою цих інструментів виробляються основні роботи в майстерні, але мало хто замислюється над тим, що як під час роботи, так і після роботи залишається дуже багато сміття у вигляді стружки. Тому пилосос для збору стружки так само є одним з найбільш важливих атрибутів столярній майстерні. Завдяки використанню пилососа приміщення майстерні не тільки буде виглядати чистіше і придбає порядок, але і захистить легені від шкідливої деревного пилу, що може бути в повітрі.
Різнорідність величини деревного сміття сильно варіюється від дрібного пилу до великих стружок, тому фільтр пилососа використовуваного в столярній майстерні часто забивається і знижує ефективність використання. Замість того щоб постійно чистити або міняти фільтри, можна зібрати якийсь проміжний екран, який буде відділяти великі стружки і інші частинки сміття від дрібного пилу, тим самим дозволивши фільтру більш довго служити без чистки, допомагаючи йому ефективно очищати пропускається повітря набагато довше.
матеріали:
- два листа МДФ товщиною 12.5 мм
- наждачний папір
- порохотяг
- пластмасові бочки
- ОСБ товщиною 15 мм
Детальний опис самостійного створення сепаратора стружки для пилососа в столярній майстерні.
Крок перший: Пилозбірник
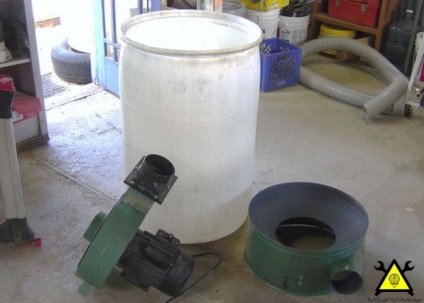
Крок третій: Розбирання пилососа.
По суті, вся конструкція збирається заново, тому наявний пилосос був розібраний, щоб дістати необхідні для використання деталі: двигун, центральне кільце, шланги з фітингами і вентилятор, і звільнитися від зайвих деталей.
Крок четвертий: Концепція перегородки
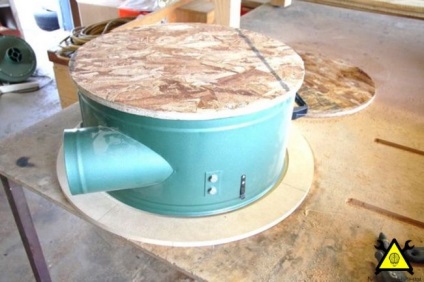
Подальша ідея полягала в тому, щоб виготовити диск, який буде знаходитися на вершині сміттєвого бака, а центральне кільце буде розташовуватися зверху. У диску буде вирізаний канал довжиною приблизно 2/3 від окружності. Другий диск буде встановлений на верхній частині центрального кільця, а вентилятор буде встановлений зверху.
Крок п'ятий: Виготовлення нижнього диска
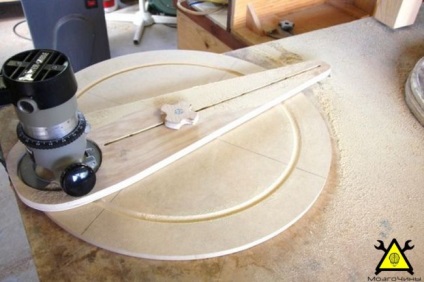
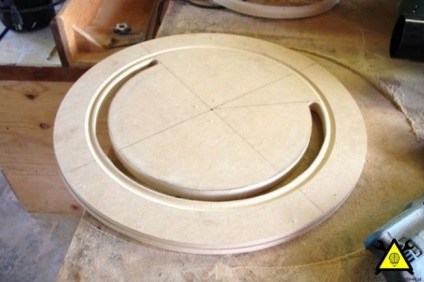
Для виготовлення підстави були взяті листи МДФ товщиною 12.5 мм в кількості двох штук. Скріпивши їх разом отримав один лист товщиною 25 мм. Потім за допомогою фрезера був виконаний паз для дефлектора.
Після чого були відміряно 2 \ 3 від окружності диска і просвердлені отвори 31 мм діаметром в кінцях каналу для дефлектора. Потім за допомогою лобзика були вирізані напрямні.
Крок шостий: Виготовлення верхнього диска
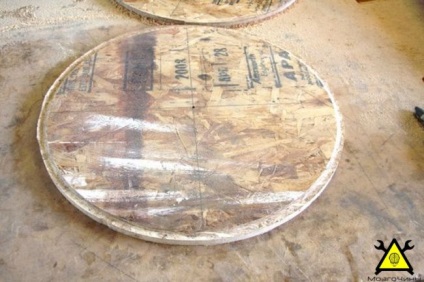
Верхній диск виготовлявся з листа ОСБ товщиною 15 мм. Він так само складається з двох частин склеєних разом для надання більшої міцності виробу, тобто загальна товщина вийшла 30 мм. Точно так же, як і при виготовленні першого диска, за допомогою фрези був зроблений паз, де буде розташована верхня частина центрального кільця. Для того щоб закріпити патрубок щільніше до вентилятора, частина нижнього диска була надрізана. Потім верхня частина диска була щільно прикріплена до вентилятора за допомогою будівельного клею, отримавши таким чином герметичне ущільнення.
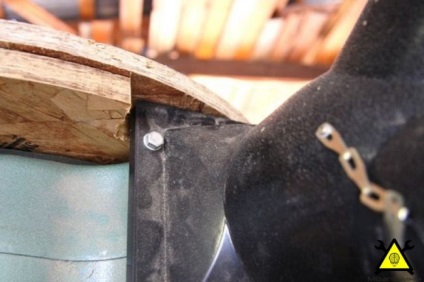
Крок сьомий: Ущільнювальна прокладка
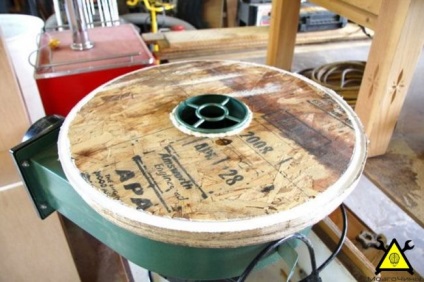
Важливо розуміти, що пластмасова бочка, як і центральне кільце не є ідеальними колами, тому будуть щілини. Але для ефективної роботи конструкції цей елемент повинен бути герметичний, тому всі цілі були рясно промазати силіконовим герметиком.
На повне охолодження герметика знадобилося 24 години.
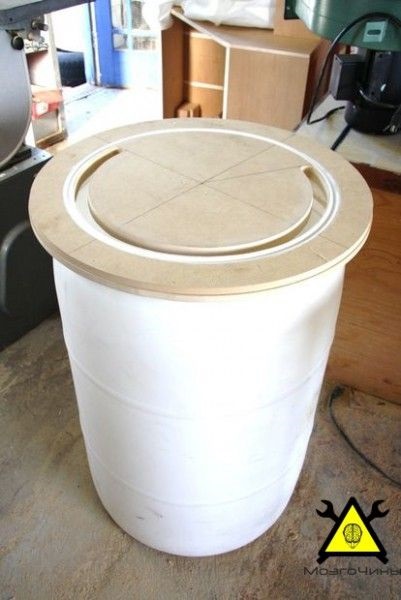
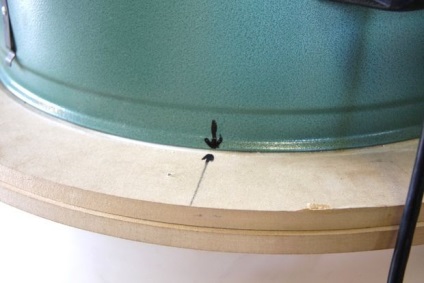
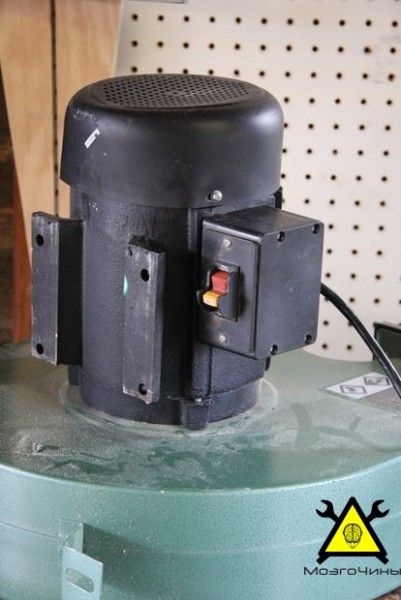
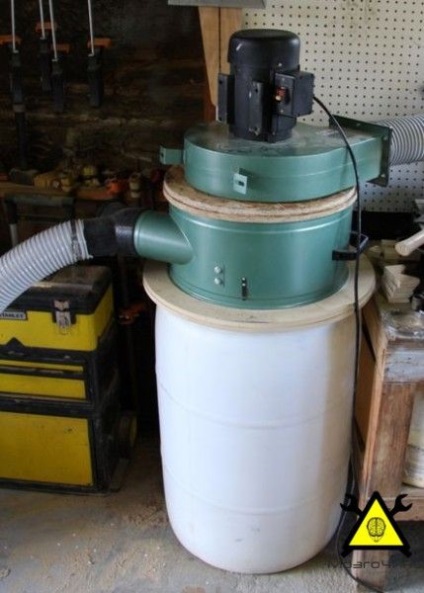
Крок дев'ятий: Перевертаємо вимикач
Крок десятий: Тестування пристрою
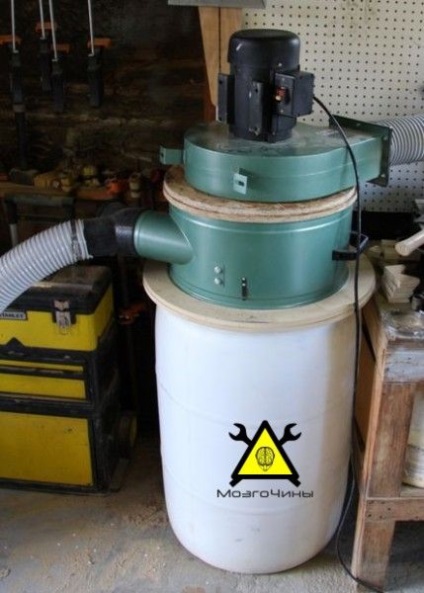