Приймання нововведених в експлуатацію електроприводів
Знову змонтовані і налагоджені електроприводи і пускорегулюючі апаратуру під час приймання в експлуатацію оглядають, перевіряють роботу механічної частини відповідно до заводських і монтажними інструкціями і піддають приймально-здавальним випробуванням відповідно до вимог ПУЕ.
При огляді приймальна комісія повинна переконатися в тому, що: електродвигуни та апарати доступні для огляду і ремонту на місці установки; електропроводка має захист в місцях можливих пошкоджень. Обертові частини, розташовані на доступній висоті, мають огородження від випадкового дотику; лінія валів змонтованих агрегатів плавна; висота установки рукояток і маховиків знаходиться на рівні 1,05-1,1 м від підлоги; вмикання і вимикання апаратів виробляються легко, без заїдань; контактні частини контакторів у включеному положенні не мають просвітів по всій ширині. Поверхні колекторів і контактних кілець не мають задирок або забоїн і добре відполіровані; щітки не зміщені за край колектора або контактних кілець, не мають перекосів, ретельно прітерти і легко переміщуються в обіймах щіткотримачів. Підшипники ковзання наповнені маслом до заводської позначки, а підшипники кочення заправлені мастилом до 2/3 обсягу гнізда підшипника; на електродвигунах і приводних механізмах нанесені стрілки, що вказують нормальне напрямок обертання.
При огляді знову змонтованих заземлюючих пристроїв в силових установках приймальна комісія перевіряє і встановлює, що: заземлюючі провідники, прокладені в приміщеннях, доступні для огляду і мають відмінне забарвлення (чорний колір), що дозволяє легко їх виявити; в тих місцях, де заземлюючі провідники можуть піддаватися хімічних впливів, так як вони мають відповідні захисні покриття, з'єднання заземлюючих провідників виконані за допомогою зварювання, що забезпечує найбільшу надійність. Заземлюючих пристроїв не містить послідовного включення кількох заземлюючих частин установки; відсутні і незадовільні контакти в проводці, що з'єднує апаратуру з контуром заземлення. У місцях ймовірних механічних пошкоджень заземлюючі провідники мають захист (наприклад, в місцях перетину каналів); прохід заземлюючих провідників через стіни виконаний у відкритих отворах, трубах або коробах. Беручи заземлюючих пристроїв, приймальна комісія перевіряє його елементи, що знаходяться в землі, з вибірковим розкриттям ґрунту, а решта - в межах доступності огляду. Кількість заземлювачів і глибина їх закладення повинні відповідати проекту.
Технічне обслуговування електроприводів
Технічне обслуговування обмоток електричних машин
При експлуатації електричних машин поступово руйнується ізоляція обмоток в результаті її нагрівання, впливу механічних зусиль від вібрації, динамічних сил при пусках і перехідних процесах, відцентрових сил при обертанні, впливу вологи і агресивних середовищ, забруднення різної пилом.
Незворотні зміни структури і хімічного складу ізоляції називають старінням, а процес погіршення властивостей ізоляції в результаті старіння - зносом.
Головною причиною виходу з ладу ізоляції машин низької напруги є температурні впливи. При температурному розширенні ізоляційних матеріалів послаблюється їх структура, виникають внутрішні механічні напруги. Теплове старіння ізоляції робить її вразливою для механічних впливів. При втраті механічної міцності і еластичності ізоляція не здатна протистояти звичайним умовам вібрації або ударів, проникнення вологи і неоднаковим теплових розширень міді, сталі та ізоляційних матеріалів. Усадка ізоляції від впливу теплоти призводить до ослаблення кріплень котушок, клинів, пазових прокладок і інших кріпильних конструкційних деталей, що сприяє пошкодження обмотки при відносно слабких механічних впливах. У початковий період експлуатації просочувальний лак добре цементує обмотку, але внаслідок теплового старіння лаку цементація погіршується і дію вібрації стає більш відчутним.
В процесі експлуатації обмотка може забруднюватися пилом з навколишнього повітря, маслом з підшипників, вугільним пилом при роботі щіток. У робочих приміщеннях металургійних і вугільних підприємств, прокатних, коксових та інших цехів пил настільки мілка і легка, що проникає всередину машини, в такі місця, куди потрапляння її, здавалося б, неможливо. Вона утворює провідні містки, які можуть викликати перекриття або пробою на корпус.
Зовнішню поверхню машини і доступні внутрішні частини в процесі технічного обслуговування очищають від пилу сухою серветкою, волосяною щіткою або пилососом.
При поточному ремонті обмоток машину розбирають. Обмотки оглядають, продувають сухим стисненим повітрям і при необхідності протирають серветками, змоченими в бензині. При огляді перевіряють надійність кріплення лобових частин, клинів та бандажів. Усувають виявлені несправності. Ослаблені або обірвані бандажі на лобових частинах статорних обмоток з круглого дроти зрізають і замінюють їх новими зі скляних або лавсанових шнурів або стрічок.
Якщо покриття обмотки знаходиться в незадовільному стані, то обмотку сушать і покривають шаром емалі. Покривати обмотку товстим шаром емалі не рекомендується, так як потовщений шар погіршує охолодження машини. Якість проведеного ремонту перевіряють виміром опору ізоляції до і після ремонту.
Короткозамкнені обмотки асинхронних двигунів при поточному ремонті, як правило, не ремонтують, а тільки оглядають. При виявленні несправностей ротори відправляють в капітальний ремонт.
Технічне обслуговування щітково-колекторного вузла
Щітково-колекторний вузол в машинах постійного струму та інших машинах є найменш надійним вузлом і вимагає ретельного технічного обслуговування. Для забезпечення безіскрової роботи необхідно виконання ряду умов, які б забезпечували надійний контакт між щіткою і колектором і рівномірну допустиме навантаження струмом робочої поверхні щітки.
Справність щітково-колекторного вузла перевіряють при огляді і необхідних вимірах. У справних колекторів поверхня гладка, без виступаючої слюди або окремих пластин, вм'ятин, подгара, ексцентриситету або биття. Щітки вільно ковзають в обіймах щіткотримачів, без качки і з достатньою силою притискаються до колектора. Болти, траверси, пальці, на яких кріпляться щеткодержатели, досить жорсткі і не мають вібрацій, качки і т.п. Якір машини збалансований і обертається без вібрацій. Щітки повинні бути однієї марки, необхідного розміру і притертими до колектора.
При технічному обслуговуванні пил з колектора і щіткового механізму видаляють пилососом або продувкою стисненим повітрям; колектор протирають серветкою, змоченою спиртом. Перевіряють легкість переміщення щітки 2 (рис. 1) в щіткотримачі 1. Якщо щітка переміщається туго, необхідно почистити щіткотримач і щітку. Зазор між щіткотримачем і колектором повинен бути в машинах великої потужності 2 - 4 мм, в машинах малої потужності 1-2,5 мм. Люфт щітки в гнізді щіткотримача в напрямку обертання колектора не повинен перевищувати 0,1-0,2 мм при товщині щітки 8-16 мм і 0,15 - 0,25 мм при товщині понад 16 мм. Великий зазор призводить до нахилу щітки через сили тертя об колектор, що захоплюється за собою нижній край щітки, і ускладнює її переміщення в гнізді. Великий люфт особливо проявляється в реверсивних машинах, так як при зміні напрямку обертання щітка
нахиляється в протилежну сторону, що зменшує поверхню її прилягання до колектора. Уздовж осі колектора допускається люфт в гнізді від 0,2 до 0,5 мм.
Вимірюють також тиск щітки на колектор. Під щітку підкладають аркуш паперу 6, а динамометр 3 кріплять до щітки 2. Показання динамометра, при якому папір легко витягується з-під щітки, дозволяє визначити тиск щітки на колектор. Недостатній тиск щітки призводить до сильного іскріння і прискореного зносу колектора і щіток. Занадто сильний тиск збільшує силу тертя в ковзному контакті, а також знос. Тиск повинен бути мінімальним, при якому іскріння не перевищує значення, допустимого за технічною документацією, і однаковим на все щітки для рівномірного розподілу струму між ними. Тиск пальця 4 на середину щітки регулюється пружиною 5.
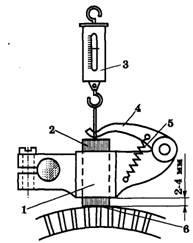
Мал. 1. Пристрій для вимірювання динамометром тиску щітки на колектор
Крім того, перевіряється правильність розташування щіток на колекторі. Для рівномірного навантаження щіток струмом на кожному щеткодержателе їх розміщують строго по осі колектора (рис. 2, а). Для рівномірного зносу колектора щітки рядів в осьовому напрямків повинні бути зрушені (рис. 2, б). Відстань між щіткотримачами однаково (рис. 2, в).
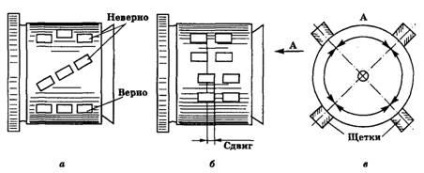
Мал. 2. Розстановка щіток на колекторі
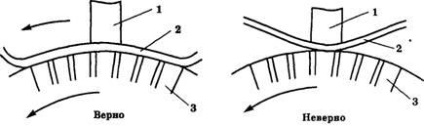
Мал. 3. Схема притирання щіток до колектора: 1 - щітки; 2 - скляна шкурка; 3 - колектор
Биття робочої поверхні колектора перевіряють індикатором годинникового типу. Для того щоб поглиблення між колекторними пластинами спотворювали вимірювань, на кінець стрижня індикатора надягають плоский наконечник. Биття перевіряють в декількох місцях при повільному провертанні якоря. Допустиме биття в швидкохідних машинах з окружною швидкістю колектора до 50 м / с не повинно перевищувати 0,02-0,03 мм; в тихохідних машинах без шкоди для роботи машини допускається значно більше биття.
Мал. 4. Колодка для шліфування колектора: а - з однією ручкою; б - з двома ручками; 1 - дерев'яна колодка; 2 - скляна шкурка
При виробленні щіток їх замінюють. Величина допустимої вироблення вказується в технічній документації на кожну машину. Після установки нових щіток виробляють їх притирання і прішліфовкой. Для притирання між щіткою і колектором встановлюють скляну шкурку з дрібним зерном і простягають її в напрямку обертання колектора (рис. 3). Робоча поверхня шкурки надає щітці попередній радіус, близький радіусу колектора. Потім щітковий апарат продувають стисненим повітрям для очищення від пилу і щітки прішліфовивать при обертається на холостому ходу машини. Прішліфовкой можна вважати закінченою, коли не менше половини поверхні щітки прилягає до колектора. При цьому на колекторі повинна бути політура. Якщо колектор має подряпини, незначні подгара, то їх видаляють шліфуванням колектора (рис. 4). Після шліфування колектора необхідно створити на ньому політуру, обертаючи машину на холостому ходу.