Традиційно прийнято вважати, що фланцеве з'єднання є відносно простим видом роз'ємного герметичного з'єднання (РГС) і тому його герметизація - простий і зрозумілий кожному процес. Насправді, як мінімум, друга частина цього твердження є ілюзією, а стереотип уявної простоти в результаті дорого обходиться людям і навколишньому середовищу.
Протягом сотень років конструкція традиційного фланцевого з'єднання (рис.1) залишається практично незмінною - це сукупність двох (як правило, металевих) фланців з ущільнювальною поверхнею, прокладки (найчастіше, з пластичного матеріалу), розміщеної між цими поверхнями і кріпильних елементів, - такий класичний фланцевий «бутерброд». Звичайно, існують і інші конструкції, включаючи бугельні та інші сполуки без звичних кріпильних елементів. Фланцеві з'єднання традиційної конструкції можуть працювати в режимі самоущільнення. Також досить різноманітний і ряд конструктивних рішень фланцевих прокладок. Виключно рідко у фланцевих з'єднаннях застосовуються прокладки сальникового типу, де контактні напруги створюються на циліндричних ущільнюються поверхнях (рис.2). Однак, незважаючи на деяку різноманітність існуючих конструкцій, традиційні фланцеві з'єднання займають домінуюче становище в техніці і ця конструкція принципово не змінюється. Виникає питання - як тоді відбувається «еволюція» фланцевих з'єднань? Відповідь очевидна, - змінюються і удосконалюються використовувані матеріали, розробляються принципово нові конструкції фланцевих прокладок.
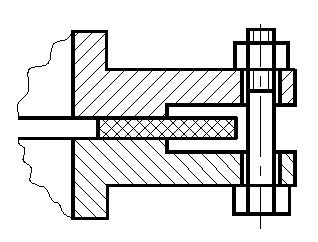
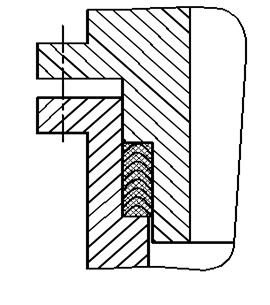
Умови герметизації фланцевих з'єднань: стереотипи і помилки
Мільярди фланцевих з'єднань по всьому світу покликані забезпечувати надійну і безпечну роботу технологічних об'єктів у всіх галузях промисловості, в енергетиці, на транспорті і в житлово-комунальному господарстві. Для цього фланцеві з'єднання повинні зберігати міцність і герметичність протягом певного періоду часу. Фахівці ремонтних і експлуатаційних служб промислових підприємств, що працюють з фланцевими сполуками, як правило, на жаль, не знайомі з основами ущільнювальної техніки. Тому серед них домінує спотворене уявлення про те, що для надійної експлуатації фланцевого з'єднання досить правильно вибрати прокладку і правильно виконати збірку з'єднання. Вони часто дивуються, коли свіже, щойно зібране з'єднання працює з витоками робочого середовища. Це класичний приклад безграмотного підходу до оцінки працездатності фланцевого з'єднання. так як не враховується поточний технічний стан елементів з'єднання. Ці елементи можуть мати «вроджені» (тобто отримані при виготовленні) або «придбані» (тобто отримані в процесі експлуатації) дефекти. Саме ці дефекти - механічні пошкодження і відхилення форми і шорсткості поверхонь ущільнювачів і кріпильних елементів, - досить часто є справжньою причиною розгерметизації і аварій. Придбані дефекти, як правило, обумовлені вродженими дефектами. Тобто, якщо при виготовленні фланців не дотримувалася технологія або був відсутній адекватний контроль якості, то потім, в процесі експлуатації і ремонтів, такі сполуки, очевидно, дуже швидко накопичать дефекти. В наш час, коли при проведенні конкурсів і тендерів досить часто, ключовим, а часом і єдиним критерієм оцінки пропозиції постачальника є низька ціна, досить важко догодити ринку з продукцією високої якості. Але виготовлення фланців - це досить складний технологічний процес, що включає в себе кілька етапів від отримання заготовки (кування, штампування, лиття) до обробки поверхонь. Якість поверхонь ущільнювачів - виключно важливий параметр для забезпечення герметичності фланцевого з'єднання. На жаль, затребуване ринком низька якість (дешеві вироби не можуть бути якісними по визначенню) в результаті дуже дорого обходиться тим, хто прагнув заощадити. Наприклад, майже завжди, для герметизації фланцевого з'єднання з дефектами потрібно більш товста (а значить і дорожча) прокладка. З'єднання з дефектами практично завжди має витоку (іноді невидимі на перший погляд) і означає, процеси корозії в ньому будуть проходити швидше, ніж в кондиционном з'єднанні. Це може привести до того, що, нарешті, ущільнювальні поверхні отримають такі дефекти, при яких з'єднання вже неможливо буде ущільнити без додаткової механічної обробки. Наступний етап - це вже наплавка ущільнювальної поверхні і подальша механічна обробка. Все це, в кінцевому підсумку, виливається в витрати, на порядок і навіть на порядки перевищують економію на закупівлю неякісних фланців або неякісний монтаж обладнання на місці експлуатації. Отже, надійність фланцевого з'єднання визначається не тільки матеріалом, конструкцією і якістю виготовлення прокладки і правильної складанням з'єднання, а й поточним технічним станом всіх елементів з'єднання. Але для оцінки поточного стану з'єднання потрібні спеціально розроблені нормативні документи і технічні засоби контролю і моніторингу стану елементів конструкції з'єднання. На жаль, в переважній більшості випадків, на підприємствах, що експлуатують фланцеві з'єднання, немає ні того, ні іншого.
Вибір прокладки та збирання з'єднання - ахіллесова п'ята і дамоклів меч кінцевих користувачів.
Якщо російські виробники тепломеханічного обладнання, прагнучи використовувати найбільш дешеві ущільнення, хоч якусь увагу приділяють підбору і надійності ущільнення, то кінцеві користувачі, в переважній більшості, все ще знаходяться в кам'яному столітті. Важко знайти яку-небудь іншу технічну сферу, де настільки безграмотно і легковажно підходили б до питання, що вимагає особливої ретельності і підвищеної відповідальності. Але це лише одна сторона медалі або навіть слідство. А причина в тому, що розробники і виробники ущільнювачів і виробів самі сприяють такому стану речей. Досить порівняти технічні дані на випущені прокладки провідних західних і російських виробників. Що ми бачимо, як правило, на сторінках технічних каталогів і інтернет сайтів російських виробників? Правильно, - ми бачимо максимальну температуру і максимальний тиск робочого середовища для даного ущільнювача матеріалу або конкретного конструктивного виконання прокладки. Непосвячений в основи ущільнювальної техніки звичайний обиватель - кінцевий користувач, зрозуміло, сприймає ці рамки як легітимне поле для застосування прокладки. Але! При цьому він не усвідомлює потенційну небезпеку закладеної в такому безвідповідальному підході «міни», - можливого одночасного поєднання (сукупності) максимальної температури і максимального тиску. Технічні дані - як правило, у вигляді Р / Т діаграм (рис.3), що встановлюють межі застосування ущільнювачів з урахуванням поєднання тиску робочого середовища і температури експлуатації, є виключно важливими і необхідними для тих, хто здійснює вибір прокладки для конкретних робочих умов. Типовий приклад з життя - впровадження безасбестового паронита. Багато компаній - кінцеві користувачі «обпеклися» на дешевих прокладках в прямому і переносному сенсі. Вони встановлювали нові прокладки на вузлах з підвищеною температурою, там, де раніше застосовували пароніт ПОН. Але практично 95% всіх марок безасбестового паронита можуть працювати надійно лише при температурі максимум 250 градусів за Цельсієм, решта 5% - в кращому випадку, до 300 градусів. І лише зовсім недавно, менше п'яти років тому, один з провідних світових виробників безазбестових пароніти запропонував ринку дійсно термостійкий і термостабільний матеріал, але навіть у цього матеріалу температура застосування, при якій не потрібні додаткові випробування, не перевищує 400 градусів за Цельсієм. Така ж ситуація іноді виникає і з прокладками з терморозширеного графіту. Відповідальні постачальники чітко обмежують температуру їх застосування величиною 400-450 градусів за Цельсієм. Але при цьому досить часто в технічних каталогах деяких постачальників можна знайти температурний межа в 500 і навіть 550 градусів, але без уточнення, в яких конкретних умовах такі температури допустимі. Продовжуючи цю тему, можна також згадати і про інших не менш важливих технічних параметрах фланцевих прокладок, таких як стисливість і пружне відновлення, щільність, газопроникність, стійкість до циклічних силовим і тепловим навантаженням, схильність до повзучості, стійкість до агресивних робочим середах, теплопровідність і ін .
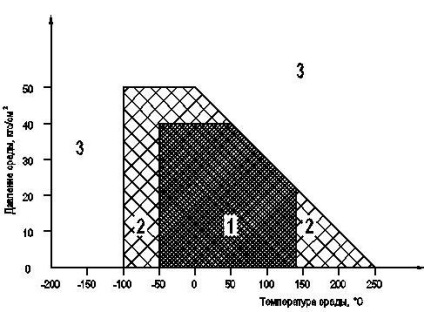
Якщо робочі температура і тиск знаходяться в межах сектора 1, то технічні випробування зазвичай не проводяться, якщо прийнята до уваги стійкість матеріалу до робочого середовища.
Якщо робочі температура і тиск знаходяться в межах сектора 2, рекомендується проведення технічних випробувань.
Якщо робочі температура і тиск знаходяться у відкритому секторі 3, то технічні випробування обов'язкові.
Класична помилка при виборі фланцевої прокладки - недостатня товщина прокладки при її низькій стисливості. Всі чули, що завжди бажано застосовувати більш тонку прокладку, та до того ж вона і дешевше. Так, так воно і є, але за умови, що з'єднання не має дефектів. Наприклад, у паронита стисливість, як правило, не вище 10% (для порівняння - у графітових прокладок до 45%). Якщо таку прокладку поставити в умов не паралельності поверхонь ущільнювачів, то вона, швидше за все, в одному місці буде перетиснута, в іншому буде «висіти». Ще складніша ситуація може скластися в разі складання замкнутого (тобто жорсткого і малорухливого в осьовому напрямку) технологічного контуру або при складанні так званих «калачів» (вигнутих коротких ділянок трубопроводу з двома привареними фланцями). У таких ситуаціях, як правило, на одному фланцевому з'єднанні завжди має місце збільшений зазор між фланцями, і усунути його затягуванням не представляється можливим. Єдиний вихід - застосування прокладки зі збільшеною товщиною або, що найбільш доцільно - виготовлення спеціального проміжного металевого кільця з установкою двох пластичних прокладок. З іншого боку, занадто товста прокладка, в більшій мірі, схильна до ризику повзучості і релаксації напружень. Також негативним моментом є відносно велика площа внутрішньої торцевої поверхні прокладки, що означає і велику пропускну здатність прокладки для витоків, якщо прийняти за основу механізм витоків з теорії фільтрації.
Інший характерний приклад не зовсім коректного вибору розмірів прокладки - орієнтація на розміри поверхонь, що ущільнюються. На жаль, іноді можна зустріти приклади нестандартних фланцевих з'єднань з надмірно великий за площею ущільнювальної поверхнею фланців. Очевидно, що при проектуванні таких з'єднань не враховувалося співвідношення можливостей кріпильних елементів (сумарно створювана сила затягування), площі прокладки і параметрів робочого середовища. В результаті на прокладці з надмірно великою шириною поля ущільнення НЕ створюється необхідного за розрахунком контактного тиску. Фахівці ремонтники при заміні такий прокладки просто заміряють розміри ущільнюваної поверхні фланців і переносять ці розміри на креслення замовляється прокладки. Хоча в даному випадку, буває достатньо зменшити зовнішній або внутрішній діаметр прокладки з тим, щоб збільшити величину контактного тиску.
Зусилля попереднього затягування фланцевого з'єднання - це, мабуть, ключовий етап герметизації. Тут завжди два лиха: чи не дотягли (що трапляється частіше) або перетягнули (що трапляється рідше). В інструкціях по збірці фланцевих з'єднань (які взагалі-то, часом і «вдень з вогнем» годі й шукати), як правило, рекомендації по затягуванню кріпильних елементів містять розрахунковий крутний момент на ключі. Але, по-перше, зустріти на ремонтному виробництві фахівця з динамометричним ключем, це велика рідкість (на відміну від автомобільної майстерні). По-друге, занадто багато факторів впливає на істинний момент на ключі, занадто багато помилок. Іноді, справжнє значення виходить в два рази нижче розрахункового через великі втрат на тертя в кріпильних елементах, або внаслідок дефектів з'єднання. По-третє, самі ключі вимагають регулярної повірки та ретельного догляду. Коректне зусилля затяжки - це не вся проблема. Сам по собі режим затягування з'єднання має велике значення. В принципі, завжди доцільно здійснювати одночасну затяжку, як мінімум, чотирьох шпильок за один крок. Але у фахівців, які здійснюють монтажні роботи, практично ніколи немає під рукою необхідного оснащення. Найкращий спосіб - виконати контроль деформації прокладки. Але тоді ми повинні мати діаграму осьового стиснення для прокладки даного виконання. Але знайти коректну діаграму це дуже велика рідкість, так як розробники і виробники листових матеріалів (особливо це стосується дешевої продукції) часто не здатні підтримувати задані механічні характеристики в кожному аркуші. Єдиний вихід - зробити з листа зразки (як мінімум, три зразки) і провести їх випробування на осьовий стиск, на підставі отриманих даних можна сформувати діаграму стиснення для даного матеріалу. Потім при складанні з'єднання треба або виготовити обмежувальні плитки, або задіяти інший, але щодо коректний метод виміру величини стиснення прокладки.
Інший важливий фактор, який часом не враховується - режими експлуатації обладнання. Нерідкі випадки, коли прокладки виходять з ладу через, наприклад, не регламентованих різких гідравлічних і теплових навантажень або сильній вібрації.
На завершення хотілося б відзначити, що в реальному житті, особливо в умовах сучасної російської дійсності, коли підрядні організації, що відповідають за ремонт обладнання, намагаються наймати на роботу дешевий (а значить і некваліфікований) персонал, ситуація ускладнюється. Тому актуальності набувають питання оцінки економічних втрат компаній в зв'язку з низькою надійністю роботи фланцевих з'єднань, зниження аварійності на потенційно небезпечних виробництвах, екологічного збитку навколишньому середовищу від несанкціонованих витоків небезпечних робочих середовищ, енергозбереження та навчання ремонтного персоналу основам роботи з ущільненнями.