1. Мета та завдання.
Основною метою даної статті є докладний опис процесу виготовлення ручного ріжучого інструменту з обойм підшипників за методом Віктора Івановича. Опис даного методу є на форумі в темі «Мій улюблений саморобний інструмент», в даній статті, виходячи з наявного матеріалу, я вирішив показати виготовлення плоских подборніков різної ширини.
2. ВИХІДНІ МАТЕРІАЛИ ТА ІНСТРУМЕНТИ.
В якості вихідних матеріалів використовувалися обойми підшипників із зовнішнім діаметром 95, 65 і 65 мм, їх ширина становила 25, 12 і 7 мм відповідно, далі по тексту я буду називати їх 1, 2 і 3. Наведені тут розміри можуть дещо відрізнятися від справжніх, оскільки відразу зробити виміри я не спромігся, а потім для визначення діаметрів довелося «малювати - обводити» кола, але якщо я і помилився, то не на багато.
Особливо примітна була найбільша обойма (номер 1), вона мала строго прямокутний перетин. Ймовірно, підшипник був роликовий, причому ролики мали слабку конусність. Далі на фото буде видно блискуча смуга робочої поверхні, по якій вони - ролики «бігали». Обидва інших підшипника були звичайними кульковими однорядними.
З інструменту використовувались: наждак (точило), свердлильний верстат, пальник газовий, пасатижі, молоток, грубий напилок, наждачний (шкурка), шарошка циліндрична (?), Лещата.
3. ХІД РОБОТИ.
Суть методу полягає в доданні частини обойми підшипника певної форми з подальшою «розковуванню - випрямленням» так званого хвостовика при збереженні заводський гарту робочої частини. Під як загнув! Іншими словами обойму треба спочатку розрізати, потім виточити майбутній хвостовик і шляхом нагрівання його до червоного надати йому молотком необхідну пряму форму під потрібним кутом до леза. При нагріванні майбутнє лезо повинно знаходитися в жерстяній банці з мокрим піском, щоб не втратити загартування. На фото 1 показана схема «оброблення» обойми підшипника.
Фото 1.
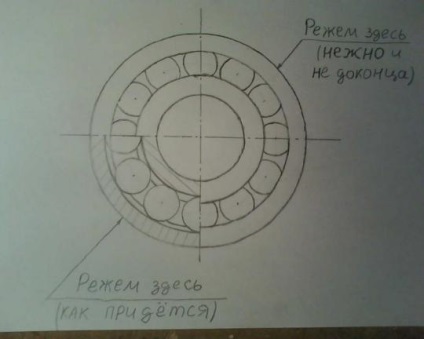
Як показано на схемі, обойму треба різати в двох місцях. При цьому кількість заготовок, які утворюються з однієї обойми, залежить від її розмірів. З обойм 1 і 3 вийшло по дві заготовки, а з 2 тільки одна. Всі три обойми різалися на ребрі точильного кола. Перший «рез» виконувався ніжно, з частим охолодженням і не до кінця. А при другому періодичність охолодження повинна була забезпечити комфортність рукам і тільки ... Мета - економія часу. Після цього обойма акуратно, через алюмінієві або дерев'яні губки зажималась в лещата і ще більш акуратно переламлівалась. ПОБОЮВАТИСЯ осколків! Отримані заготовки, природно, були підсмажені з одного боку. З цієї, смаженої, сторони і виточують хвостовик.
Великим заготівлях з обойми 1 була додана клиноподібна форма, фото 3. Це дозволить підвищити «маневреність» майбутнього інструменту і полегшить процес випрямлення або «кування - гнучкі» хвостовика. Для проведення оного процесу, як уже повідомлялося вище, використовувалася банку з мокрим піском, газовий пальник і пасатижі, фото 5.
Результати процесу представлені на фото 6, 7 і 8.
Всього було отримано п'ять заготовок, три з яких мали внутрішню канавку. Оскільки метою даної роботи було отримання плоских подборніков, то від цих канавок нам необхідно позбутися. Процес «позбавлення - виведення» здійснювався за допомогою циліндричної шарошки Ø 16 мм і висотою 24 мм і дриля, Фото 9 і 10.
Як з'ясувалося справа ця досить трудомістка. Канавку у заготовки з обойми 2 (ширина 12 мм) виводив більше 3 х годин. А на дві заготовки з обойми 3 (ширина 7 мм) пішло приблизно по годині. У всіх перерахованих випадках на самому кінчику майбутнього леза канавку цілком прибрати не вдалося, що не виведені кінці довелося обрізати, фото 11. Температура оброблюваних заготовок контролювалася «вручну», охолодження часте.
Отже, заготовки лез готові. Тепер прийшла пора задуматися про ручках. Їм в даному оповіданні мені хотілося приділити особливу увагу. Останнім часом я роблю ручки з запобіжними металевими кільцями, так мені більше подобається. Не буду сперечатися, що вклеєні на епоксидку лезо буде довго і надійно служити до найповнішого і логічного кінця, але погодьтеся товариші, що колечко надає стамесці більш «естетичний» вид. Воно в якійсь мірі оберігає ручку від випадкових «коцок» об камінь під час заточування - правці, ну і плюс загальне підвищення міцності .
Отже, колечка, їх я робив з внутрішніх обойм підшипників, обточуючи на жорні по всій зовнішній поверхні на конус. Щоб процес обточування йшов акуратно, і поверхня колечка сточуємо рівномірно необхідно підібрати підходящу оправлення. Як оправлення зазвичай використовувався простий болт, але його діаметр повинен бути близький до внутрішнього діаметра кільця, щоб воно вільно оберталося на ньому, але без «бовтанки», Фото 12.
В процесі обточування колечко обертається на оправці, щоб воно не «втекло» його треба чимось притримувати, але тільки не руками. На фото 13 в лівій руці болт з оправкой, а в правій короткий сплющений на кінці пруток (викрутка теж би підійшла), що обмежує переміщення кільця. Точити необхідно до повного зникнення центральної канавки. При роботі СУВОРО СЛІДКУВАТИ через зазори між каменем і упором точила! На фото 14 представлений кінцевий результат.
Матеріалом для ручок зазвичай служили різні елементи «утилізованої» меблів, найчастіше ніжки від стільців і шаф. Матеріал: дуб, бук і якийсь різновид червоного дерева. У держ. установах цього добра свого часу можна було знайти у великих кількостях, головне, щоб домашні не заперечували перетворення житлової площі в складську. На фото 15 показано колишня ніжка від шафи. На торцевій поверхні відзначений внутрішній діаметр насаджують кільця. «Посадочне» місце обробляємо напилком рівномірно з усіх боків з незначною конусностью, головне не перестаратися. Кільце має заходити на посадочне місце досить щільно.
Потім використовуючи лещата в якості гвинтового преса остаточно надягаємо колечко, діяти акуратно без різких рухів, Фото 16. Колечко повинно переміщатися рівномірно без перекосів. При цьому допускається протачивать посадкову поверхня не на всю глибину кільця, головне відсутність зазору між його нижнім краєм і поверхнею дерева. Все одно при вклейці леза торцева поверхня буде затоплена епоксидкой. До речі бук, за моїми спостереженнями, при процедурі «запрессовки» поводиться більш пластично, ніж дуб або червоне дерево, що дозволяє втиснути колечко глибше і прибрати можливі щілинки, викликані нерівномірністю проточки. Після обробки напилком результат виглядав приблизно так, як на фото 17.
Таким чином під кожне лезо була виготовлена своя ручка, як правило їх довжина не перевищувала 110 мм. У кожній ручці був просвердлений отвір під свій хвостовик. І, природно, була проведена операція «вклейки».
При вклейці великих лез, отриманих з обойми 1, використовувався зарубіжний епоксидний клей DoneDeaL DD6573, а в інших випадках наш класичний ЕДП. Іноземний клей мені не сподобався, не дивлячись на зручність дозування - там два шприца з одним поршнем. Занадто легко він відокремився від стінок металевої (!) Ємності, в якій я його перемішував. Як буде працювати покаже час ... Результати моїх праць, після надання ручкам остаточної форми за допомогою напилка і шкурок, показані на фото 18 і 19. Тут 4 з 5 майбутніх подборніков, фото одного широкого не збереглося, вибачайте ...
Як видно на фото, на ручках з'явилися значні тріщини. До цього моменту подібного лиха у мене не траплялося, а обпік я їх вже більше двадцяти штук, причому в опрацюванні ручки були виконані з різних порід дерева і мали різну товщину. Тут же з чотирьох випалюються за один раз ручок потріскалися три (ручки двох широких стамесок з обойми 1 були обпалені окремо і без «пригод», а нижня стамеска на Фото 20 до теми відноситься тільки щодо випалу, ручка 12 міліметрової стамески з обойми 2 була єдиною «вижила»).
Розмірковуючи про причини спіткала мене неприємності, прийшов до висновку, що з великим ступенем ймовірності виною всьому став режим випалу. Газовий пальник засмітилася, і полум'я було значно менше, ніж в минулі рази (це факт). Як-небудь спеціально треба буде перевірити ...
Поміркувавши, вирішив ручки не переробляти, вклейка виявилася досить надійною. На фото 21 представлені остаточні результати після шліфування й полірування руків'я.
Розумію, що для більшої частини аудиторії найцікавіше практичне застосування даного інструменту. Що ж, товариші, постараюся з часом розкрити цю тему. Дякуємо за увагу.
Думаю, так довго оброблялася внутрішня частина через те, що абразив занадто дрібний на занадто твердої зв'язці і кількість обертів завелике. Звідси дуже маленький знімання матеріалу зі значним нагріванням і, відповідно, частим охолодженням. Якщо немає каменю побільше зернистістю, то можна в тому ж болті зробити пропил, вставити в нього стрічку з шкурки Н-50 і справа піде значно швидше на грубій обдирання. Напевно так.
А майстер-клас хороший, подборнікі естетичні вийшли і в якості лез можна бути впевненим. Пам'ятаю, давно ще Віктор Іванович писав про такий же технології, але все не зберуся наробити гнутих ножиків таким способом, вкрай корисні інструменти, виручають, де ні стамескою ні Клюкарзи НЕ підлізти
За це повідомлення сказали спасибі Василь Колишкін +1
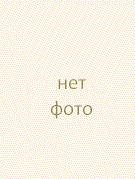
Абразив там стандартний. Що по жорсткості зв'язки, що за розміром зерна. Білий електрокорунд по ШХ15 здатний працювати досить довго без затупления граней або засолювання. АЛЕ. або на досить високих оборотах (порядку декількох тисяч в Пневмомашинка, скоблении), або на дуже низьких, тоді йде режим різання металу. Василь, судячи з усього, вгадав якраз посередині (коли вже й не ріже, але ще толком і не скоблить)
Шарошка дуже давня, родом з радянських часів.
Я її одразу впізнав, у мене таких багато, різних розмірів і саме з тих времен.Інтересно, що розмір зерна, щільність, тип зв'язки і т.п. на всіх, незалежно від розміру, ідентичні. Від 1 см завдовжки і до розміру в половину кулака. Найменші використовую зі 102L наконечником, вклеївши як осі відпрацював своє бор. Н у а там робочі обороти від 0 і до 35000 об / хв. Ті, що побільше - в "Профілі" і низькооборотної жорні. І під мікроскопом особливості обробки дуже добре видно. Якщо точно підібрати швидкість, то цей абразив здатний швидко і якісно знімати не тільки розжарену сталь, а й, наприклад, бронзу. Чи не забиваючись і не перегріваючи її при цьому. Виходить не гірше, ніж фрезою.
А цей свердлильний верстат має можливість регулювання обертів (як мінімум, перебросом ременя). Так що наступного разу є сенс спробувати, може вийти неслабкий виграш за часом і якістю. Якість і зараз відмінний, ось тільки трудовитрати на цей етап роботи.
Якщо керуватися теорією, то швидке затвердіння в масі повинно призводити до утворення тривимірної просторової сітки з великою кількістю "дефектів".
Ось тільки один маленький нюанс: ця шпаклівка - автомобільна. Тобто при наявності купи дефектів вона обсипется зі шпаклювати борту разом з фарбою. В тому і фокус, що умови штатної роботи цієї шпаклівки досить жорсткі. І навантаження вона повинна тримати досить пристойну.
Правда, є одна тонкість, шпаклівку краще брати універсальну, вона не дає усадки при затвердінні (на відміну від фінішної, яка добре працює тільки в тонкому шарі)
За це повідомлення сказали спасибі Василь Колишкін +1