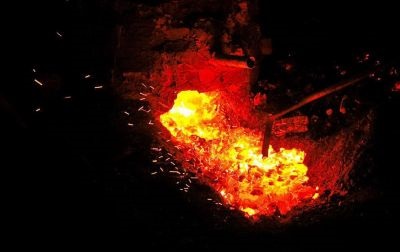
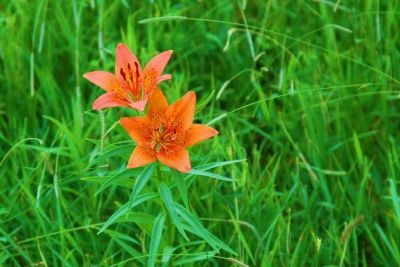
Колись в стародавні часи, наші предки прийшли на цю нову землю і принесли з собою технологію видобутку і виготовлення заліза. Згодом привізна залізо стало доступніше, але не менш цінне. Хороший клинок завжди був вірним супутником будь-якої людини хто жив або приходив в наші краї. Але, як і скрізь, з часом, промисловість витіснила кустарні методи видобутку та обробки металу.
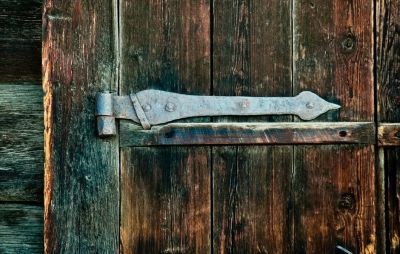
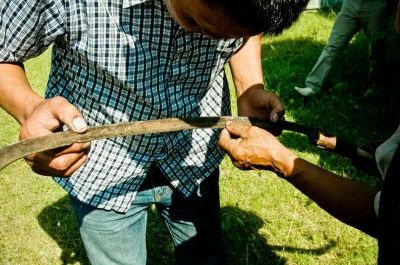
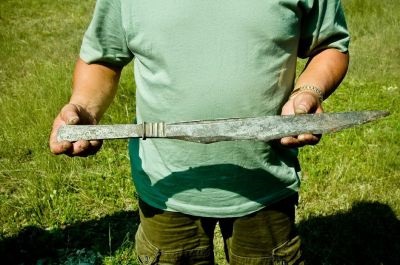
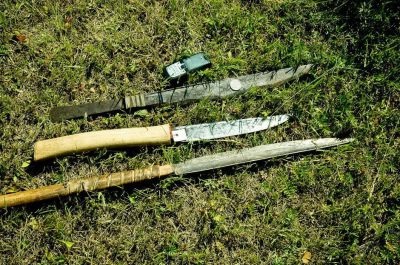
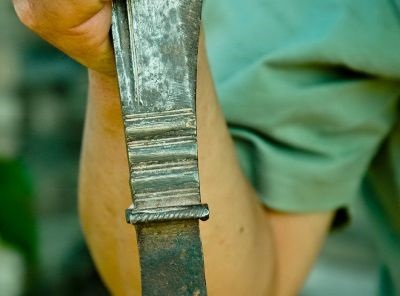
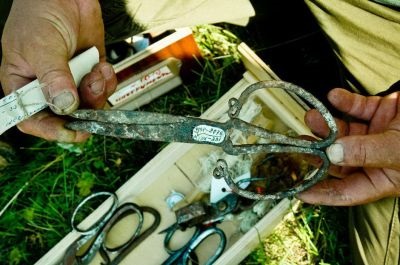
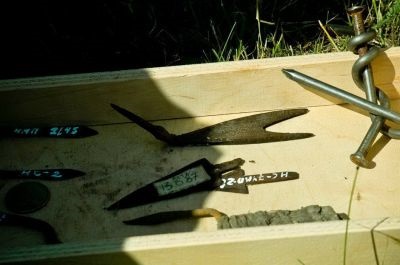
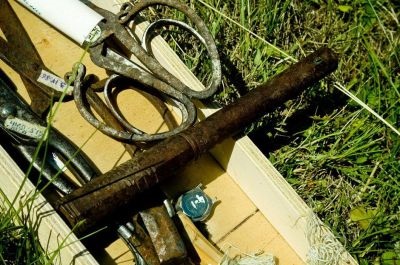
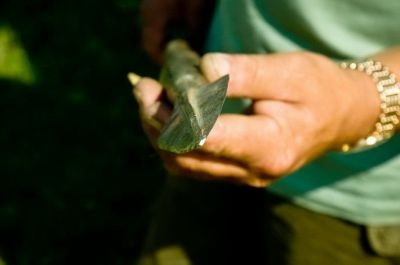
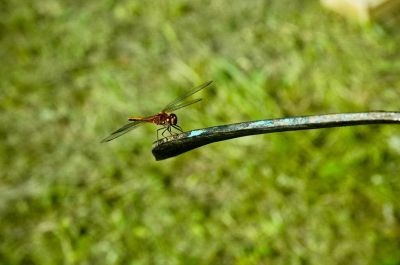
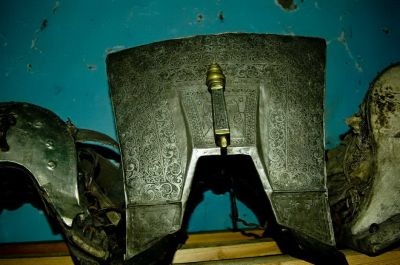
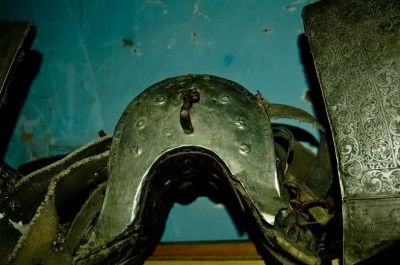
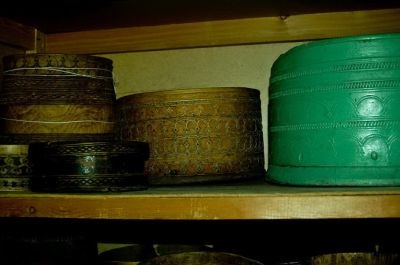
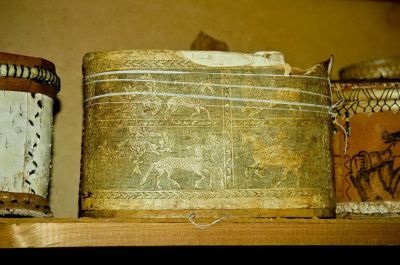
Зараз вже тільки в одиничних місцях Росії і тільки дуже досвідчені майстри займаються власним видобутком заліза. Навіщо і чому вони це роблять, коли зараз набагато простіше купити заготовки з будь-яких сталей від ШХ-8 до VG-10 і можливо ще більш просунутих марок. Напевно це питання з розряду «Навіщо поет пише вірші? Або навіщо мандрівник вирушає в невідомі краї? »Мало хто зможе відповісти, на ці питання, але завжди знайдуться ті, хто гідно оцінить результат.
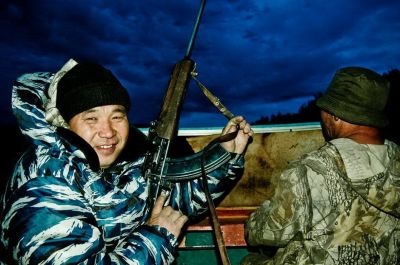
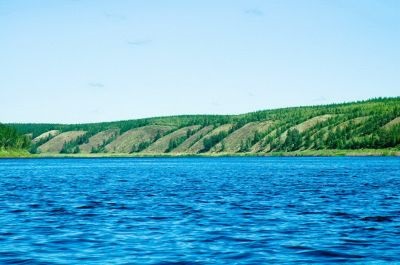
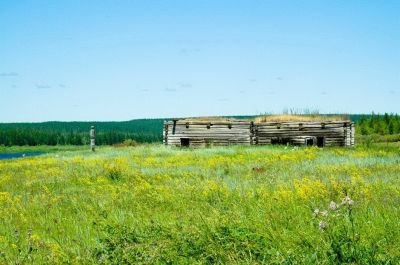
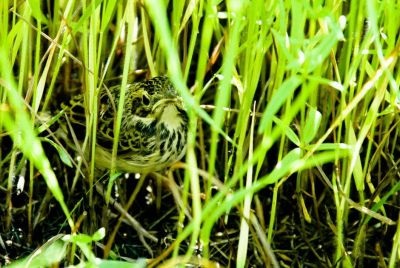
Один якутський майстер, зважився зробити своє залізо. Але не просто заради цікавості і не просто щоб відновити процес видобутку, а зробити це щоб словосполучення "Якутський Ніж" стало нести в собі не закодовані десь і кимось розлиті і пізніше перекувати У-10, ШХ-8 ітд. а наше рідне якутське залізо.
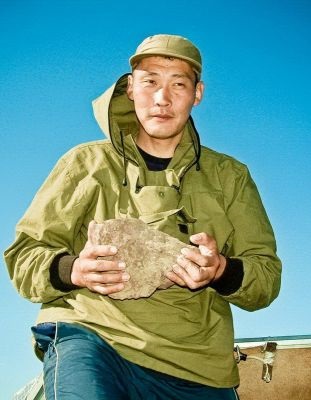
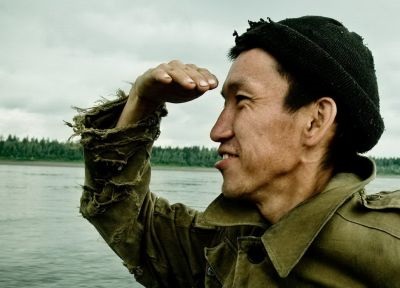
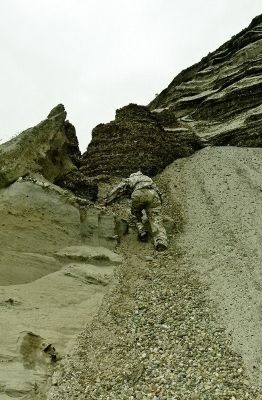
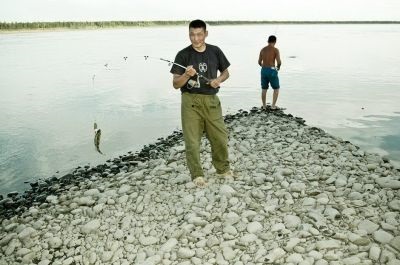
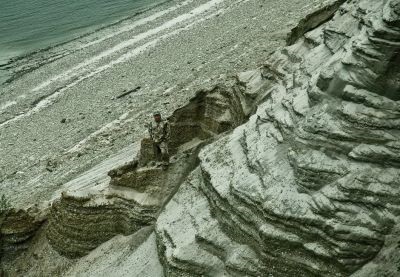
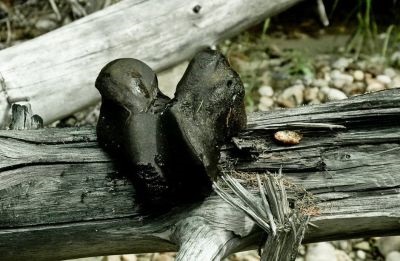
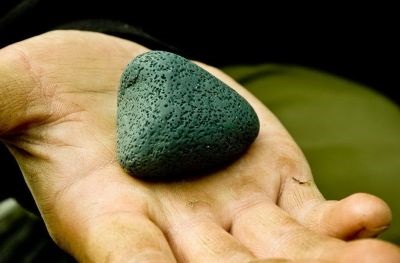
Залізна руда раніше добувалася відкритим способом як підйомний матеріал, на скельних відслоненнях і вимоїнах рудо-містять пластів в заплавах річок Амга і Алдан. Заготівля руди проводилася після закінчення повноводого періоду. На місцях виявлення руда сортувалася і перевозилася до місця безпосередньої плавки.
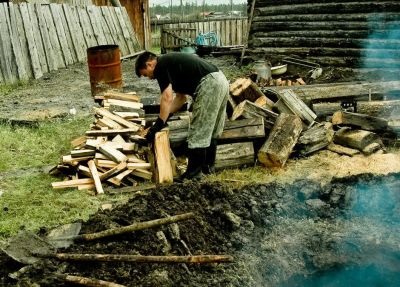
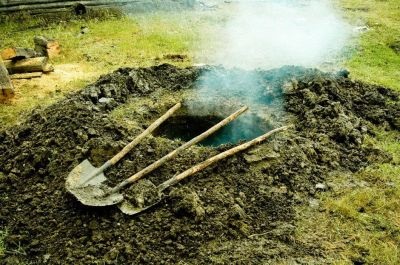
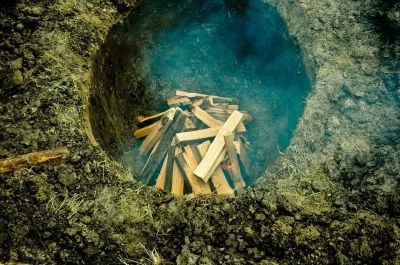
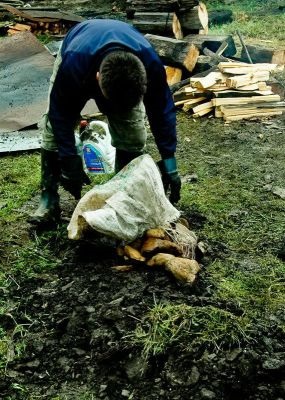
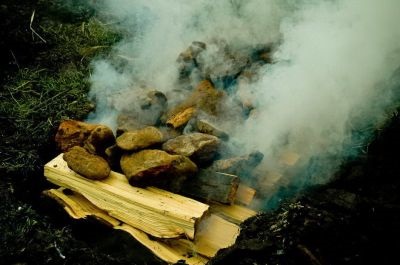
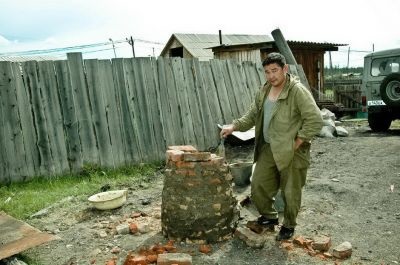
Паливом і основним відновником для сиродутний печі являелся деревне вугілля. Майстер спробував відновити так званий ямний спосіб видобутку вугілля. Ямний спосіб як показав досвід, виявився більш безпечним (в пожежному відношенні) і менш витратним (більше вихід вугілля і менше людської участі).
Заготовлений таким чином деревне вугілля при вилученні з ями завжди засмічений землею, деякою кількістю попелу, а так само дрібними фракціями того ж вугілля. Це погано позначається на якості горіння і отже буде перешкоджати досягненню необхідної температури в печі під час плавки. Щоб уникнути цього вугілля ретельно просівають.
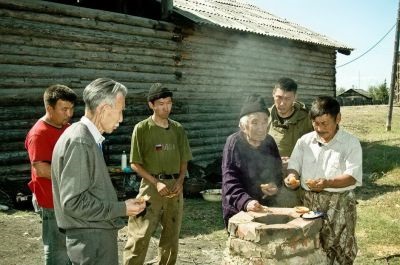
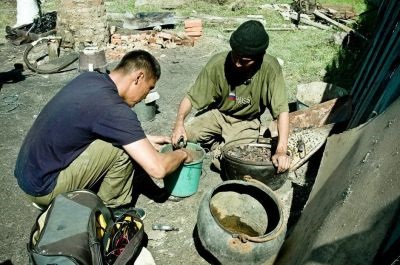
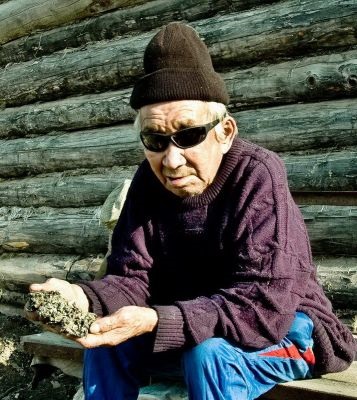
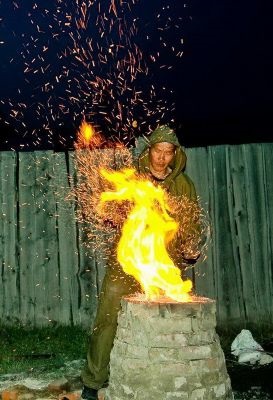
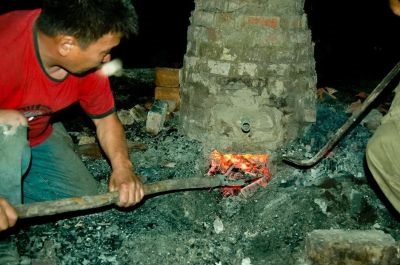
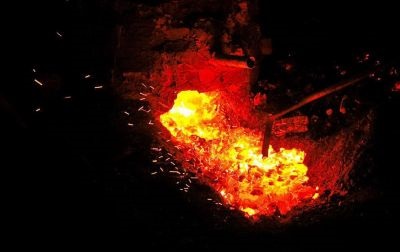
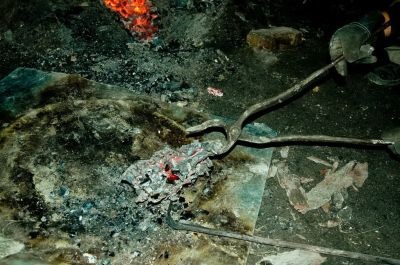
Печі будувалися на заздалегідь підготовленому майданчику бажано на деякій височини (на штучній або природної) від основного рівня поверхні землі. (Пам'ятаєте що кузні завжди були на відшибі і на узвишші? А самі ковалі через це були похмурі і відлюдники). Тулово печі складалося з каменю, як розчин в кладці використовувався глиняний розчин. У нашому випадку камінь був замінений на цеглу. А піддув вирішено було здійснити за допомогою електродвигуна. Для збільшення температури була також встановлена турбіна.
Для прискорення процесу, найбільші шматки руди дробилися. Технологія дроблення досить проста: великі шматки руди прогартовуються (нагріваються до розтріскування) після охолодження руда легко дробиться.
Після кладки печі поки ще сира піч протоплюється сухими дровами при малому Піддув. у міру висихання і прогорання піч заповнюється деревним вугіллям, через деякий час після виходу полум'я назовні засипається перша порція руди, піддув збільшується у міру потреби. Після прогорання першої заправки печі руда опускається, перший етап завершено.
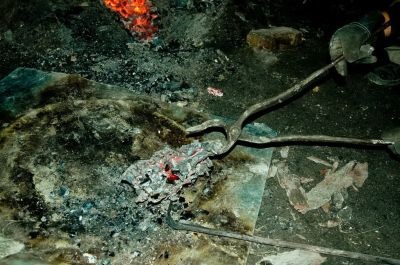
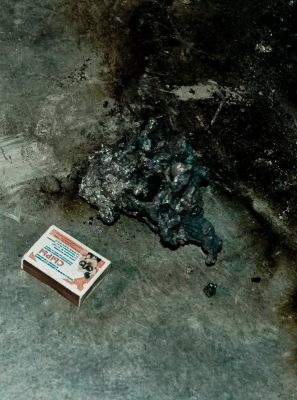
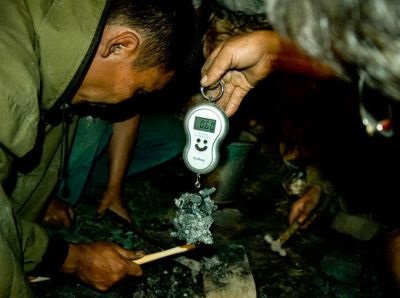
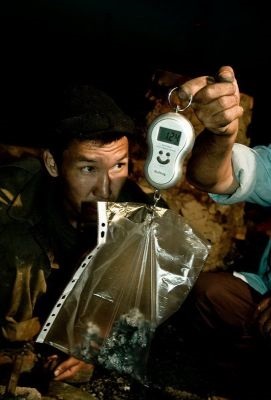
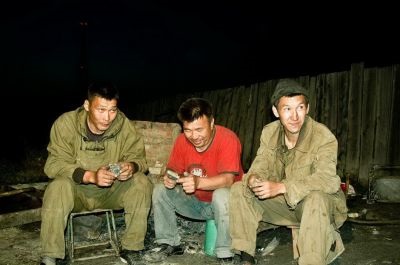
Наступні етапи повторюють перший, кількість етапів визначається
об'ємом майбутньої криці. Після досягнення планованого обсягу залізної криці,
піч ще раз заповнюється вугіллям піддув збільшується до максимального.
При догоранням вугілля пробивається дно печі для виходу розплавлених шлаків.
Частина, що залишилася криця виймається і по можливості проковувати.
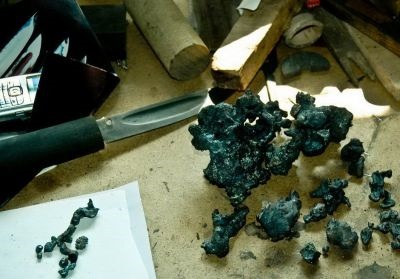
Надалі метал відлитий в форми клинкових заготовок і чушок потупивши в лабораторію на визначення хімічного вмісту, щоб приблизно класифікувати його марку. Поки попередньо сталь за кольором, питомій масі схожа на всім давно відомий булат.
Що з металом буде далі і під що його перетворять руки майстра, в наступному нарисі. Наскільки мені відомо готові попередні ескізи для спеціальних виставкових і колекційних ножів.
за матеріалами Сариала Білюкіна.