Якщо вам цікаво дізнатися, як виробляють двигуни для сучасних літаків, то пропонуємо відправитися на віртуальну екскурсію на завод ВАТ «Уфимське моторобудівне виробниче об'єднання», де виготовляють двигуни для реактивних літаків, в тому числі для сімейства Су (Су-35С, Су-27 і Су-30).
1. Зварювання в населеної камері «Атмосфера-24»
Найцікавішим етапом виробництва двигуна є аргонодуговая зварювання найбільш відповідальних вузлів в населеної камері, що забезпечує повну герметичність і акуратність зварного шва. Спеціально для УМПО ленінградським інститутом «Прометей» в 1981 році створено один з найбільших в Росії дільницю зварювання, що складається з двох установок «Атмосфера-24».
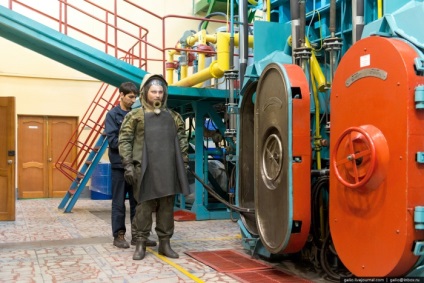
2. За санітарними нормами робітник може проводити в камері не більше 4,5 годин в день. З ранку - перевірка костюмів, медичний контроль, і тільки після цього можна приступати до зварювання.
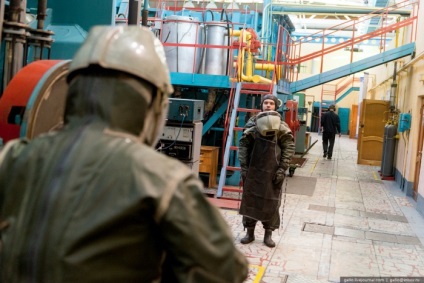
3. Зварювальники відправляються в «Атмосферу-24» в легких космічних скафандрах. Через перші двері шлюзу вони проходять в камеру, їм прикріплюють шланги з повітрям, закривають двері і подають всередину камери аргон. Після того, як він витіснить повітря, зварювальники відкривають другі двері, заходять в камеру і починають працювати.
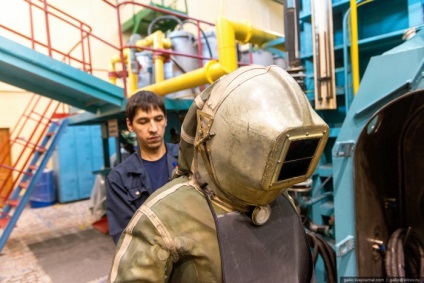
4. У безокисного середовищі чистого аргону починається зварювання конструкцій з титану.
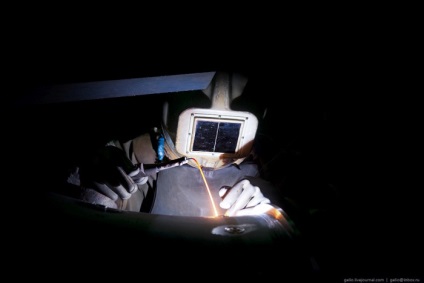
5. Контрольований склад домішок в аргоні дозволяє отримати якісні шви і підвищити міцність від утоми зварних конструкцій, забезпечує можливість подварки в самих важкодоступних місцях за рахунок застосування зварювальних пальників без використання захисного сопла.
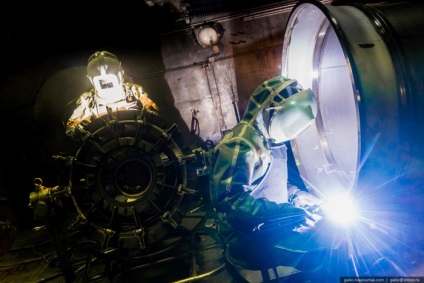
6. У повному обладунку зварювальник, дійсно, схожий на космонавта. Щоб отримати допуск до роботи в населеної камері, робочі проходять курс навчання, спочатку вони в повній екіпіровці тренуються на повітрі. Зазвичай двох тижнів достатньо, щоб зрозуміти, чи годиться людина для такої роботи чи ні - навантаження витримує далеко не кожен.
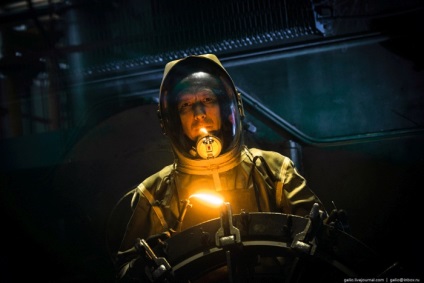
7. Завжди на зв'язку зі зварниками - фахівець, який стежить за тим, що відбувається з пульта управління.
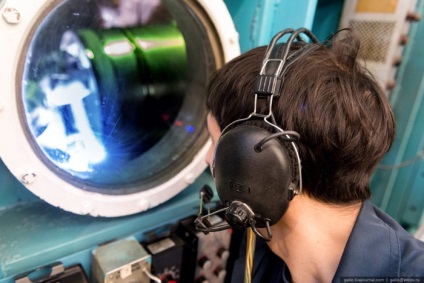
8. Оператор управляє зварювальним струмом, стежить за системою газоанализа і загальним станом камери і працівника.
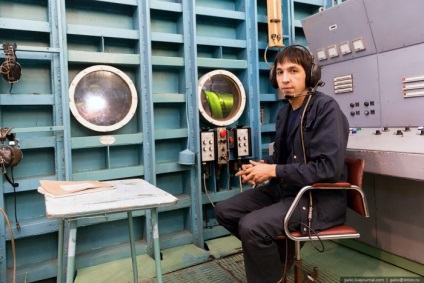
9. Жоден інший спосіб ручного зварювання не дає такого результату, як зварювання в населеної камері. Якість шва говорить сама за себе.
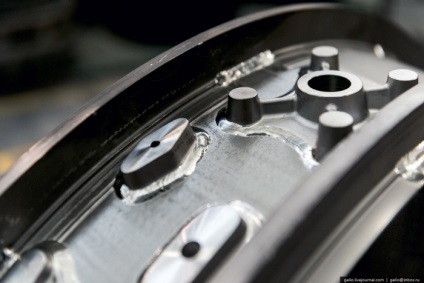
10. Електронно-променеве зварювання.
Електронно-променеве зварювання в вакуумі - повністю автоматизований процес. У УМПО він здійснюється на установках Ebokam. Одночасно зварюється два-три шва, причому з мінімальним рівнем деформації і зміною геометрії деталі.
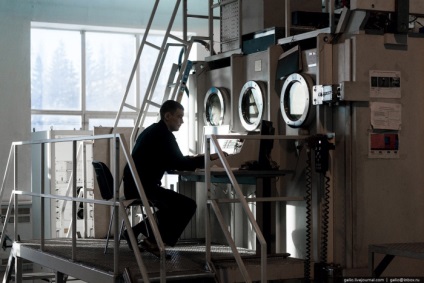
11. Один фахівець працює одночасно на декількох установках електронно-променевого зварювання.
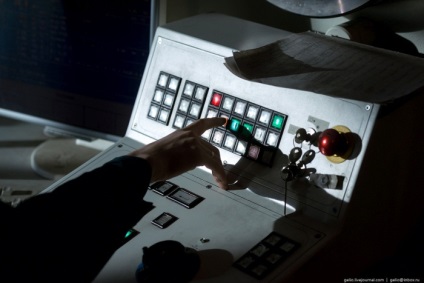
12. Деталі камери згоряння, поворотного сопла і блоків соплових лопаток вимагають нанесення теплозахисних покриттів плазмовим способом. Для цих цілей використовується робототехнічний комплекс ТСЗП-MF-P-1000.
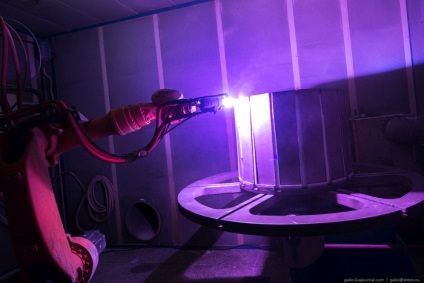
13. Інструментальне виробництво
У складі УМПО 5 інструментальних цехів загальною чисельністю близько 2500 чоловік. Вони займаються виготовленням технологічного оснащення. Тут створюють верстатні пристосування, штампи для гарячої та холодної обробки металів, ріжучий інструмент, вимірювальний інструмент, прес-форми для лиття кольорових і чорних сплавів.
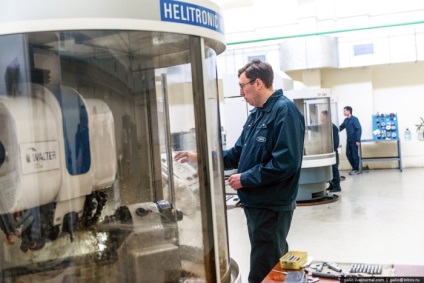
14. Виробництво прес-форм для лопаточного лиття здійснюється на верстатах з ЧПУ.
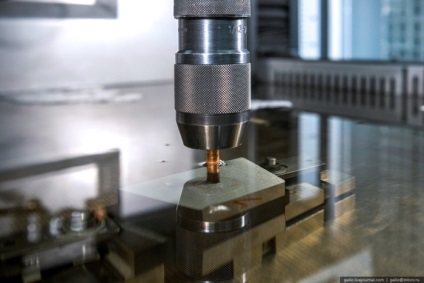
15. Зараз для створення прес-форм потрібно всього два-три місяці, а раніше цей процес займав півроку і довше.
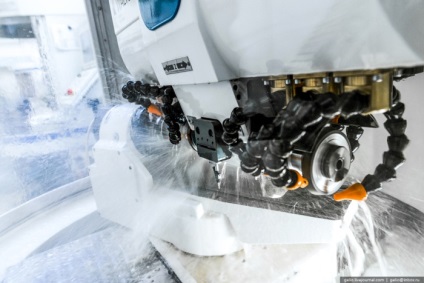
16. Автоматизоване засіб вимірювання вловлює найдрібніші відхилення від норми. Деталі сучасного двигуна та інструменту повинні бути виготовлені з гранично точним дотриманням всіх розмірів.
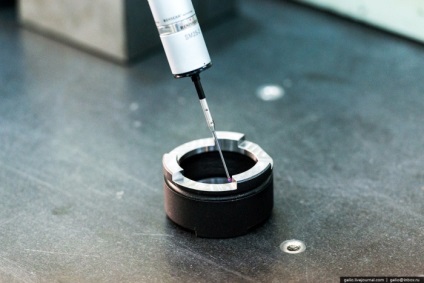
7. Вакуумна цементація.
Автоматизація процесів завжди передбачає зменшення витрат і підвищення якості виконуваних робіт. Це відноситься і до вакуумної цементації. Для цементації - насичення поверхні деталей вуглецем і підвищення їх міцності - використовуються вакуумні печі Ipsen.
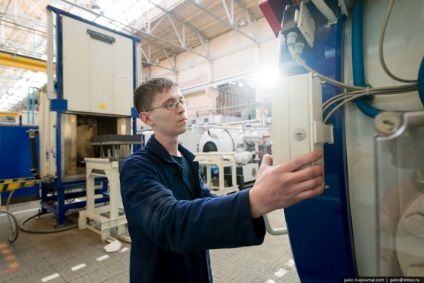
18. Для обслуговування печі досить одного працівника. Деталі проходять хіміко-термічну обробку протягом декількох годин, після чого стають ідеально міцними. Фахівці УМПО створили власну програму, яка дозволяє здійснювати цементування з підвищеною точністю.
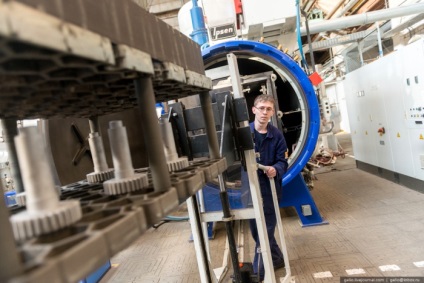
19. Ливарне виробництво
Виробництво в ливарному цеху починається з виготовлення моделей. Зі спеціальної маси пресуються моделі для деталей різних розмірів і конфігурацій з подальшою ручною обробкою.
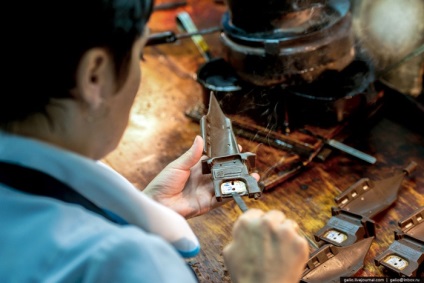
20. На ділянці виготовлення виплавлюваних моделей працюють переважно жінки.
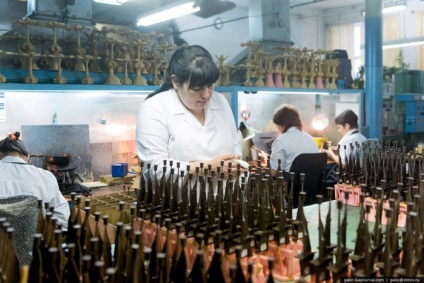
21. Облицювання модельних блоків і отримання керамічних форм - важлива частина технологічного процесу ливарного цеху.
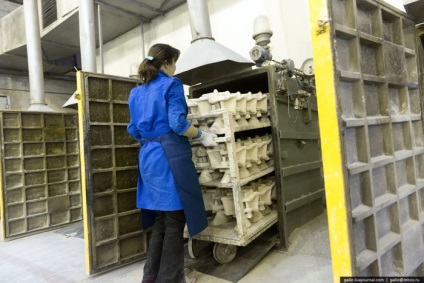
22. Перед заливанням керамічні форми прогартовуються в печах.
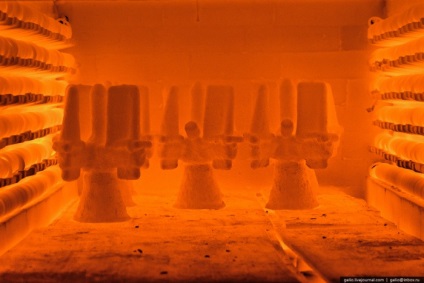
23. Керамічна форма прожарена - далі на неї чекає заливка сплавом.
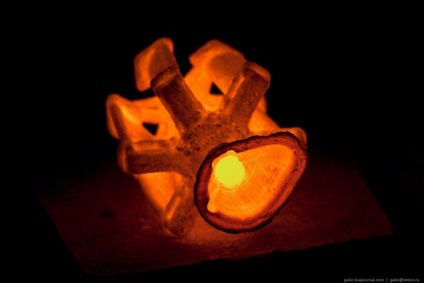
24. Так виглядає залита сплавом керамічна форма.
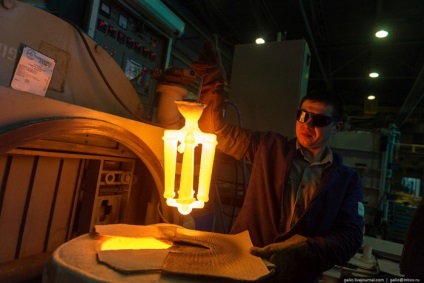
25. «На вагу золота» - це про лопатці з монокристаллической структурою. Технологія виробництва такої лопатки складна, але і працює ця дорога в усіх відношеннях деталь набагато довше. Кожна лопатка «вирощується» з використанням спеціальної затравки з нікелі-вольфрамового сплаву.
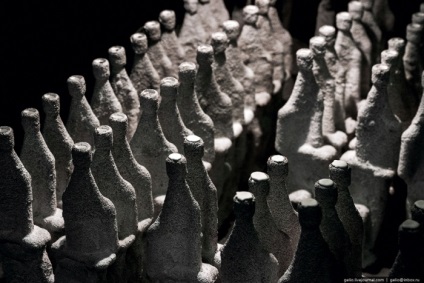
26. Ділянка обробки порожнистої шірокохордной вентиляторної лопатки
Для виробництва порожніх шірокохордних вентиляторних лопаток двигуна
ПД-14 - рушійною установки перспективного цивільного літака МС-21 -
створений спеціальний ділянку, де здійснюється вирізка і механічна обробка заготовок з титанових плит, остаточна механічна обробка замку і профілю пера лопатки, включаючи його механічну шліфування й полірування.
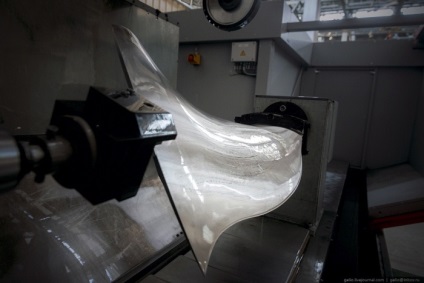
27. На четирёхкоордінатном горизонтальному обробному центрі впроваджено технологію остаточної обробки торця пера лопатки на пристосуванні, спроектованому і виготовленому в УМПО, - ноу-хау підприємства.
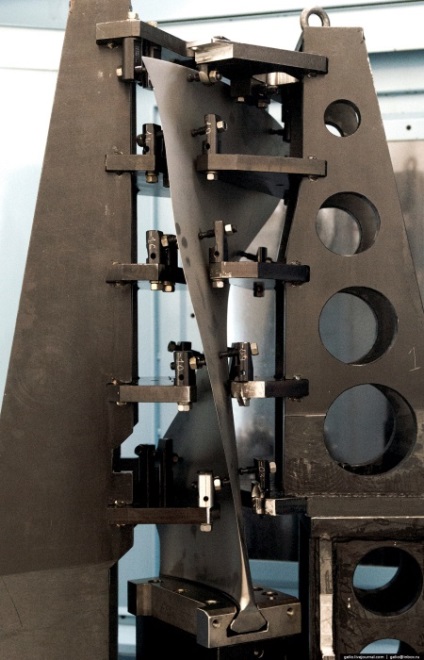
28. Комплекс виробництва роторів турбіни і компресора (КПРТК) - це локалізація наявних потужностей для створення основних складових елементів реактивного приводу.
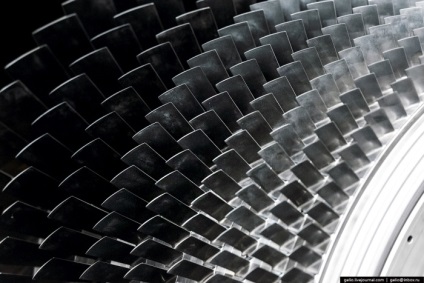
29. Збірка роторів турбіни - трудомісткий процес, що вимагає особливої кваліфікації виконавців. Висока точність обробки з'єднання «вал-диск-носок» - гарантія довгострокової і надійної роботи двигуна.
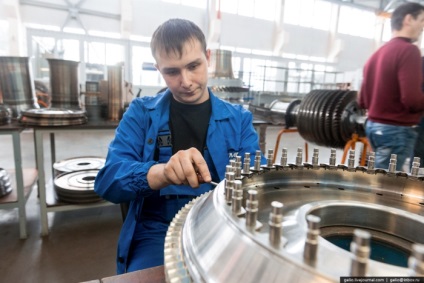
30. Багатоступінчастий ротор збирається в єдине ціле саме в КПРТК.
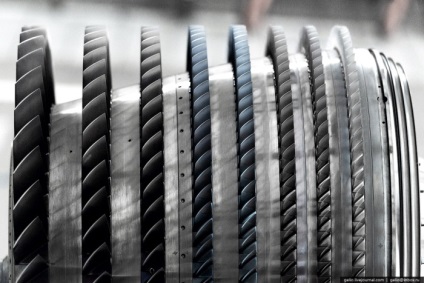
31. Балансування ротора здійснюють представники унікальної професії, якій в повній мірі можна опанувати тільки в заводських стінах.
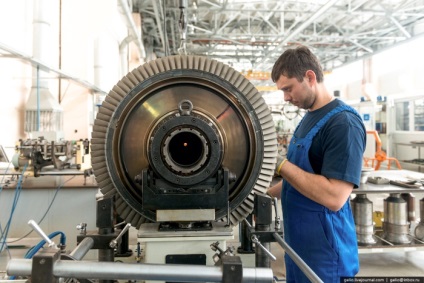
32. Виробництво трубопроводів і трубок
Щоб всі агрегати двигуна злагоджено функціонували - компресор нагнітав, турбіна крутилася, сопло прикривалося або відкривалося, потрібно подавати їм команди. «Кровоносні судини» серця літака вважаються трубопроводи - саме по ним передається найрізноманітніша інформація. У УМПО є цех, який спеціалізується на виготовленні цих «судин» - різнокаліберних трубопроводів і трубок.
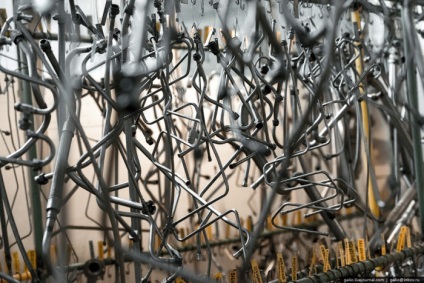
33. На міні-заводі з виробництва трубок потрібно ювелірна ручна робота - деякі деталі є справжніми рукотворними витворами мистецтва.
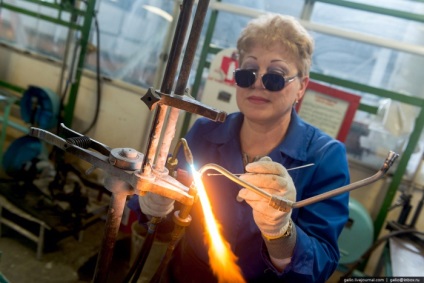
34. Багато операцій по трубогиба виконує і верстат з числовим програмним управлінням Bend Master 42 MRV. Він гне трубки з титану і нержавіючої сталі. Спочатку визначають геометрію труби за безконтактною технологією за допомогою еталона. Отримані дані відправляють на верстат, який виробляє попереднє згинання, або на заводському мовою - гинув. Після проводиться коригування і остаточний гинув трубки.
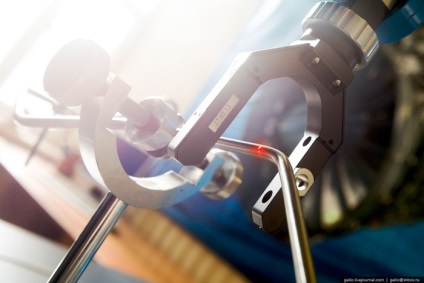
35. Так виглядають трубки вже в складі готового двигуна - вони обплітають його, як павутина, і кожна виконує свою задачу.
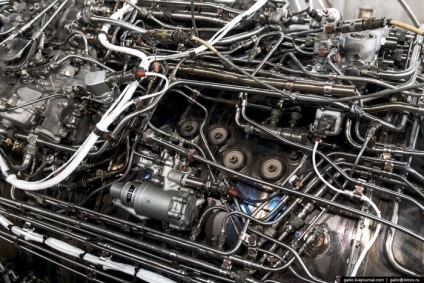
36. Остаточне складання.
У складальному цеху окремі деталі і вузли стають цілим двигуном. Тут працюють слюсарі механоскладальних робіт високої кваліфікації.
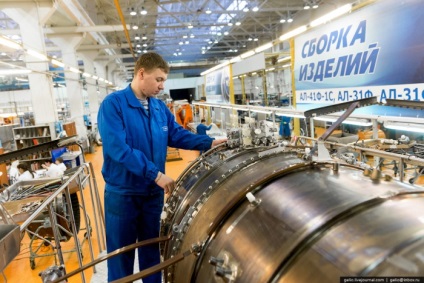
37. Зібрані на різних ділянках цеху великі модулі стикуються збирачами в єдине ціле.
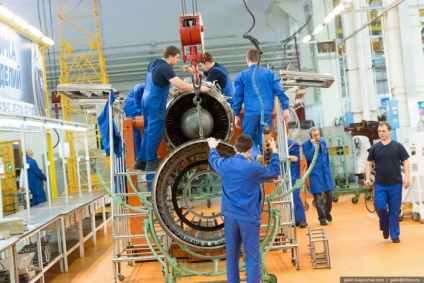
38. Кінцевим етапом складання є установка редукторів з паливно-регулюючими агрегатами, комунікацій та електрообладнання.
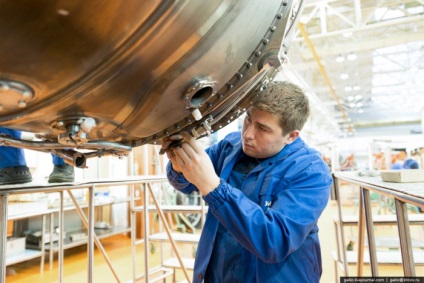
39. Проводиться обов'язкова перевірка на співвісність (для виключення можливої вібрації), центрування, так як всі деталі поставляються з різних цехів.
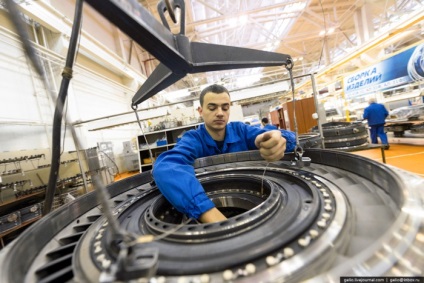
40. Після пред'явницьких випробувань двигун повертається в складальний цех на розбирання, промивання і дефектацию. Спочатку виріб розбирають і промивають бензином. Потім - зовнішній огляд, виміри, спеціальні методи контролю. Частина деталей і складальних одиниць направляється для такого ж огляду в цехи-виробники. Потім двигун збирають знову - на приймально-здавальні випробування.
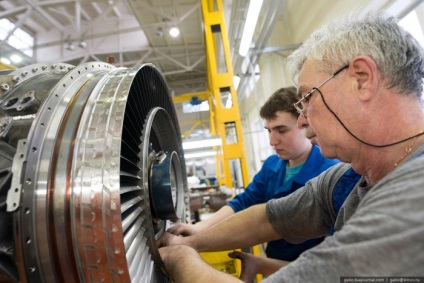
41. Слюсар-складальник збирає великий модуль.
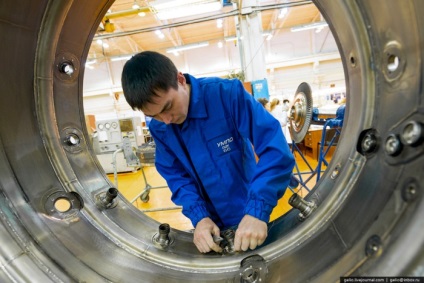
42. Слюсарі МСР виконують збірку найбільшого творіння інженерної думки XX століття - турбореактивного двигуна - вручну, суворо звіряючись з технологією.
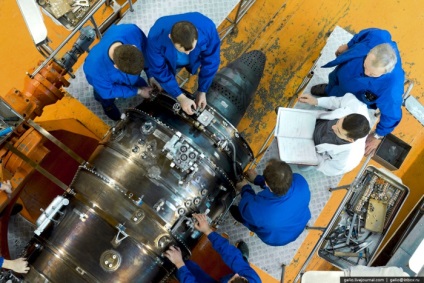
43. Управління технічного контролю відповідає за бездоганну якість всієї продукції. Контролери працюють на всіх ділянках, в тому числі - і в складальному цеху.
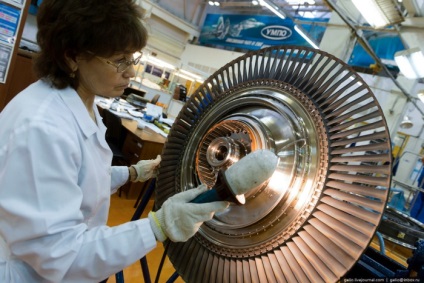
44. На окремій ділянці збирають поворотний реактивне сопло (ПРС) - важливий елемент конструкції, який відрізняє двигун АЛ-31ФП від його попередника АЛ-31Ф.
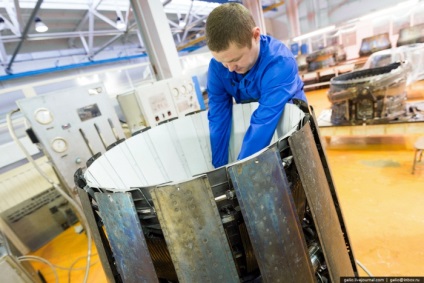
45. Ресурс роботи ПРС - 500 годин, а двигуна - 1000, тому сопел потрібно робити в два рази більше.
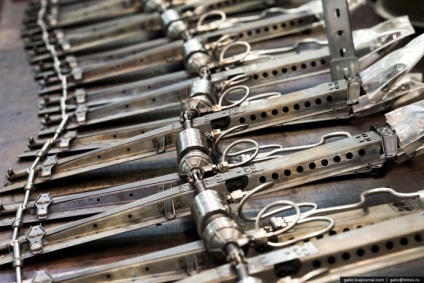