Давайте подивимося на сучасний автозавод.
Ваш майбутній автомобіль КІА надходить на завод у вигляді ось таких бобін з листової сталлю.
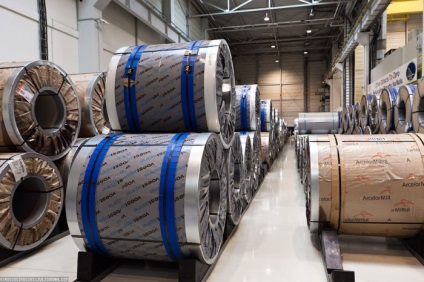
У пресувального цеху двадцятитонні сталеві рулони перетворюються в кузовні деталі майбутніх машин. Цей процес розбитий на кілька етапів. Перший етап включає в себе підготовку «болванки» для подальшої формування деталі. Для цього з листа стали вирізається контур, технологічні отвори і виступи майбутньої деталі.
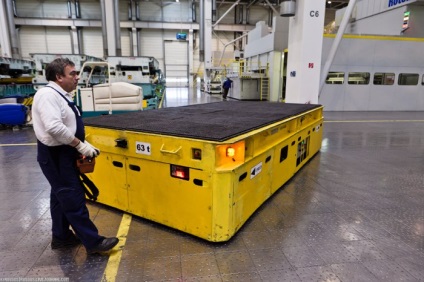
Засіб пересування по цеху.
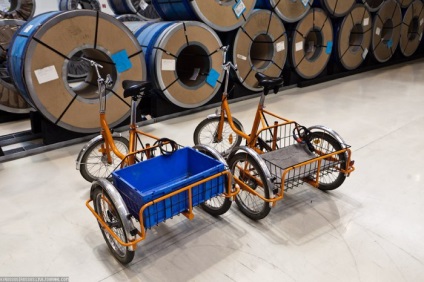
Далі цей продукт складається на металевих стелажах і за допомогою електророхлі потрапляє в прес-машину.
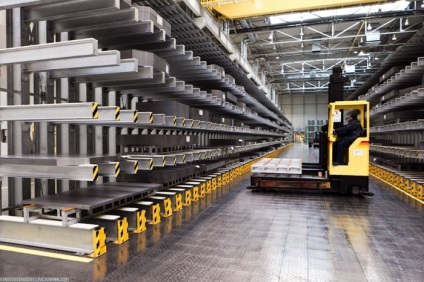
Тимчасові витрати на виробництво однієї деталі складають близько 20 секунд.
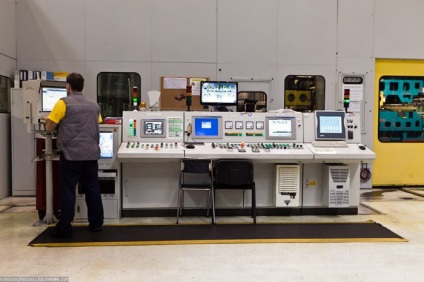
Заміна прес-форм відбувається кожні 30 хвилин.
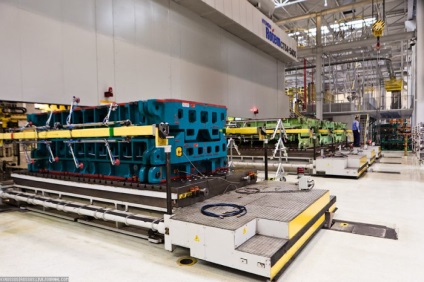
Деталь після штампування.
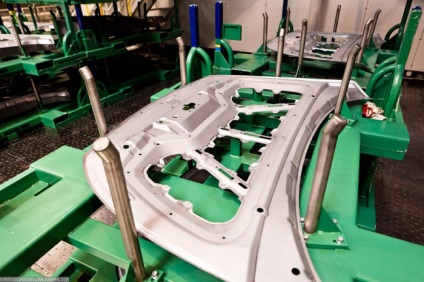
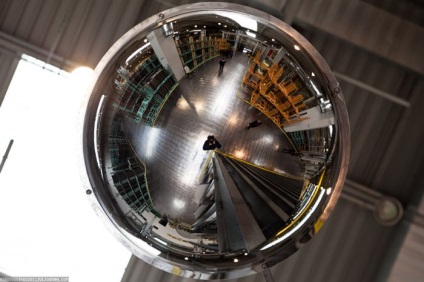
Далі сформовані деталі потрапляють на багатоярусні стелажі і чекають своєї черги в зварювальний цех.
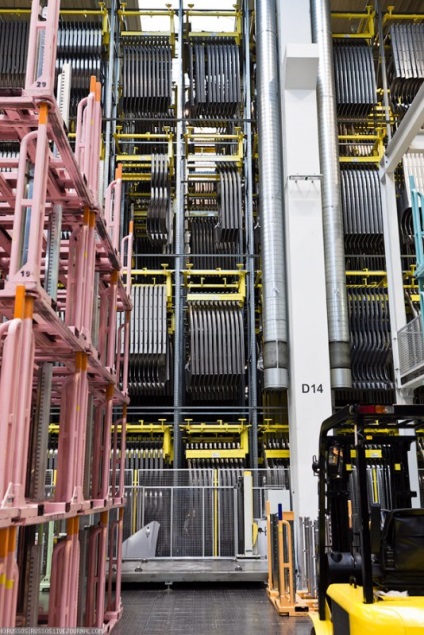
Якщо в прес-цеху є персонал, то склад повністю автоматизований.
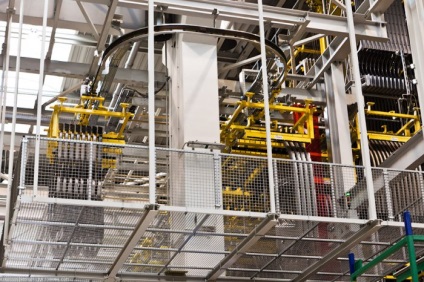
Після складу деталі кузова потрапляють в зварювальний цех, який повністю роботизована.
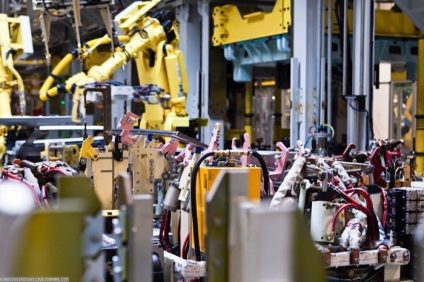
У цеху встановлено близько 400 роботів.
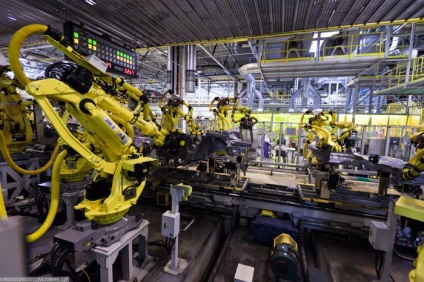
Весь процес відбувається без участі людини, який тільки контролює його.
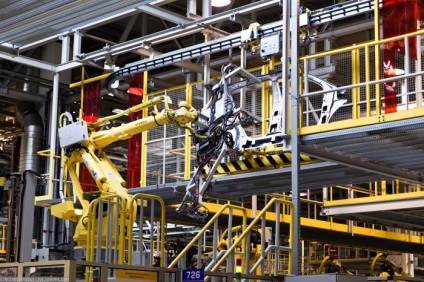
Дивуєшся злагодженій роботі всіх цих механізмів.
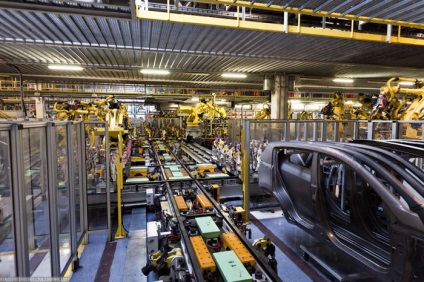
Робот методично забирає з касети елементи кузова і відправляє їх далі на зварювання.
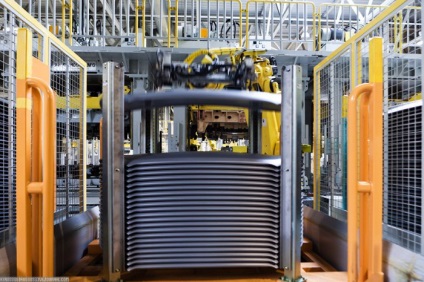
Раптово з процесу «випала» двері, на якій співробітник написав дату і щось ще. Потім вона пірнула назад. Шлюб?
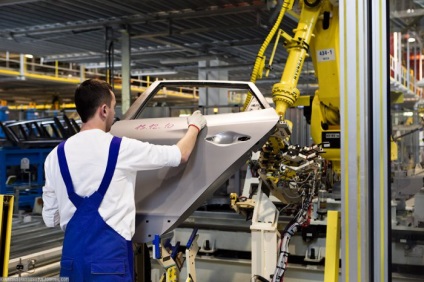
А роботи все продовжували зварювати кузова.
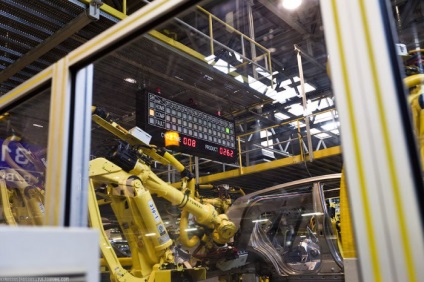
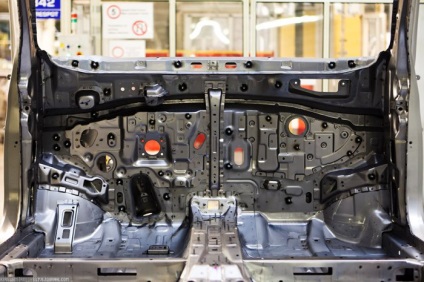
Люди в цьому цеху присутні тільки в Зоні перевірки якості (Quality audit area). При виникненні відхилень в стандартах виробництва деталь або елемент відправляється на доопрацювання. Питанням якості приділяється величезна увага - 10% співробітників працюють саме в цій області, як на різних етапах виробництва, так і на вихідному контролі.
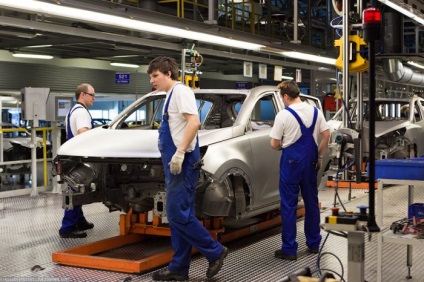
За таким скляним галереям майбутні машини пересуваються між цехами. Через особливого режиму фарбувального цеху нам його не показали, і ми відразу попрямували до складальний конвеєр.
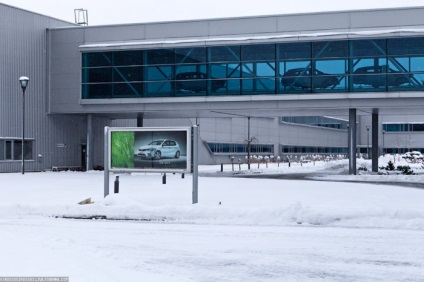
Початок складального конвеєра. 2/3 операцій тут виконують люди.
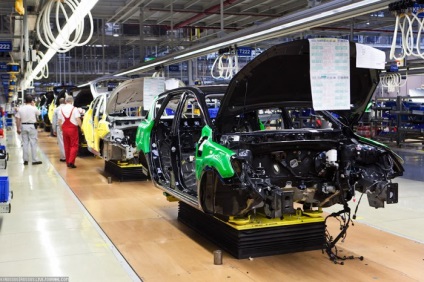
Раптово праворульний Сііда.
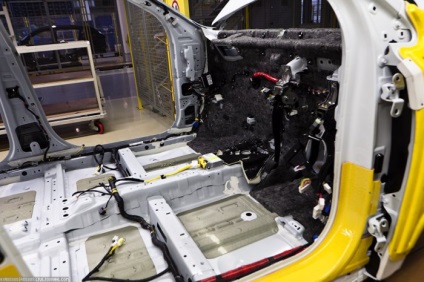
У зміні на збірці працюють близько 500 чоловік.
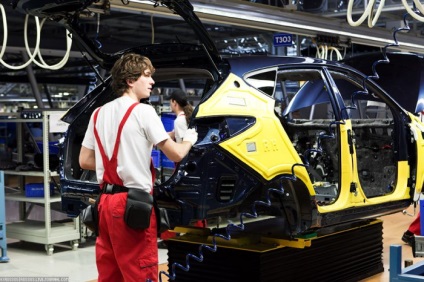
Що мене здивувало - так це відсутність хмарах або незадоволених осіб.
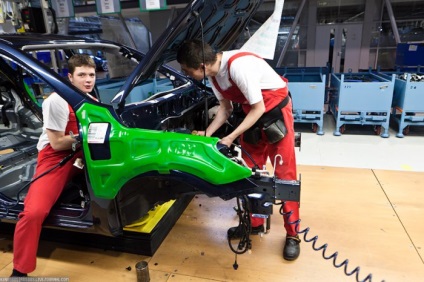
Що мене здивувало ще більше - так це те, що на конвеєрі збираються відразу всі моделі. Для того щоб відрізнити їх один від одного, а так само для захисту ЛКП, на них надягають різнокольорові захисні панелі, де кожен колір відповідає певній моделі.
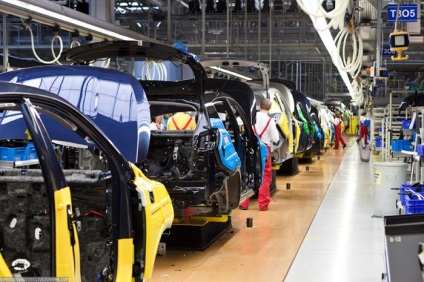
Навіть якщо робота на конвеєрі і нагадує біороботів, то це, напевно, щасливі біоробот.
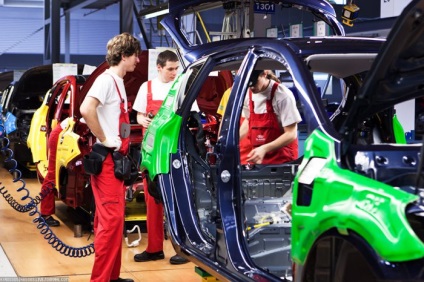
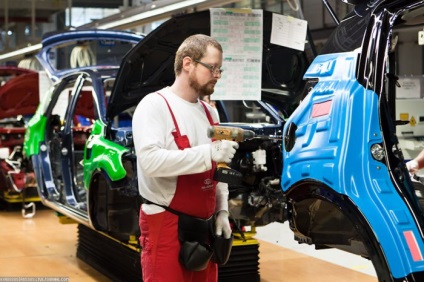
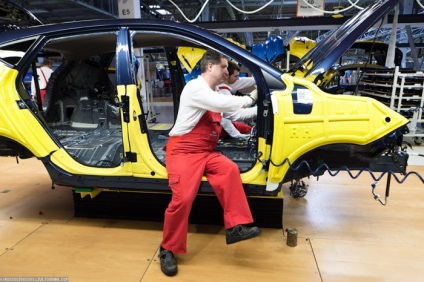
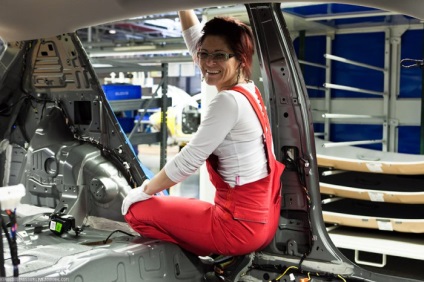
А ось невелике вкраплення роботехніки - установка зібраної торпедо.
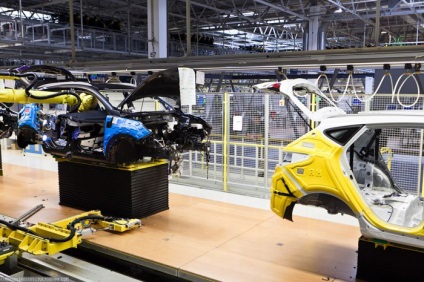
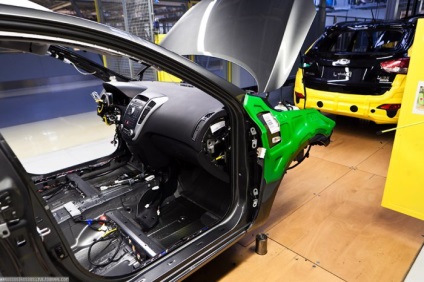
Для завершення збирання потрібно поставити двигун і підвіску на місце.
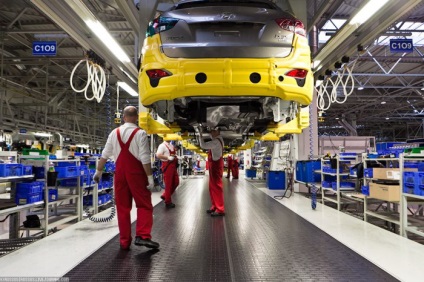
Це все в зборі приїжджає десь збоку на спеціальному візку.
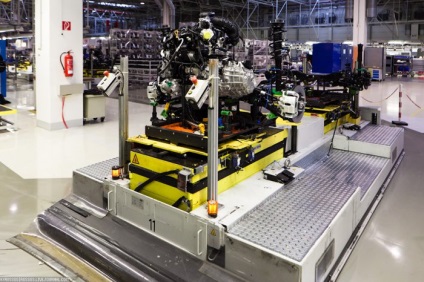
Рухи синхронізуються і ...
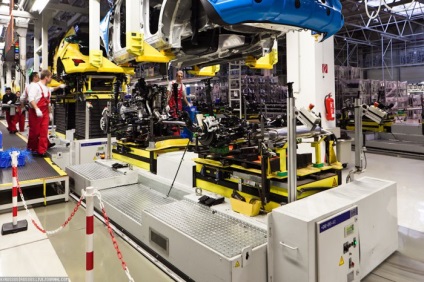
... вжик, одруження (як це називається у них) відбулася.
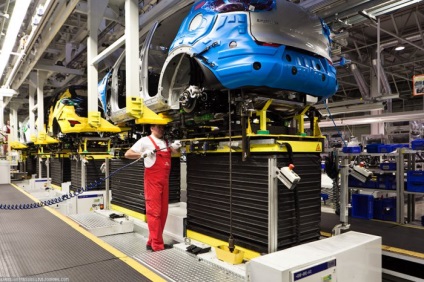
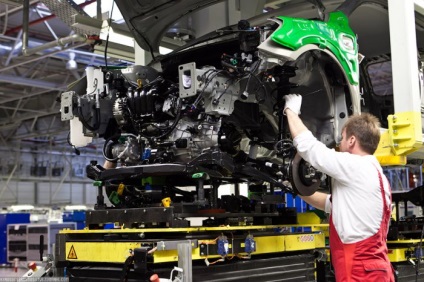
Після цього - фінішна пряма, де щось крутять і приєднують.
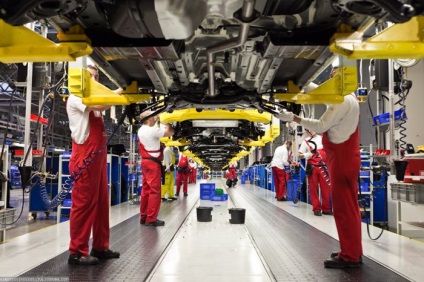
На виході - контроль якості.
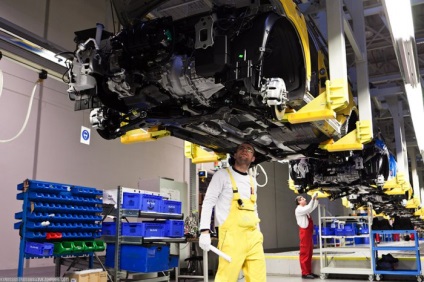
Далі майже готова машина комплектується дзеркалами, стеклами, сидіннями та іншими потрібними речами.
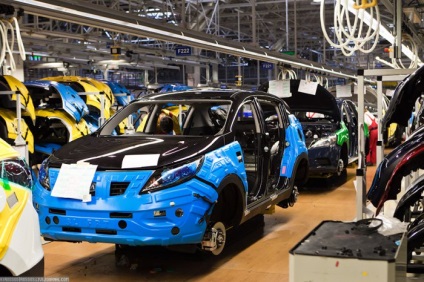
Раз - і лобове скло на місці.
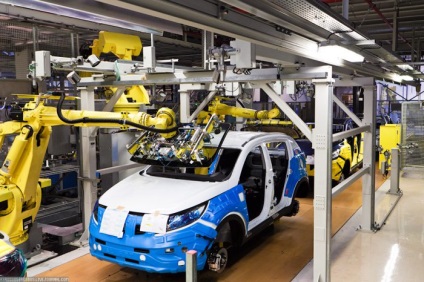
На різних етапах висота машини регулюється підйомником, який знаходиться під майданчиком.
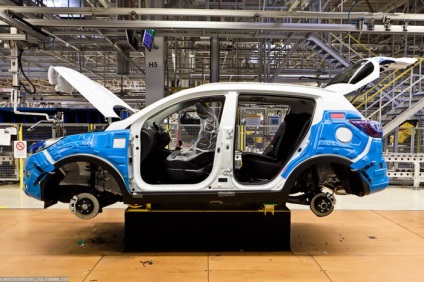
Процес завершується контролем якості і заправкою рідинами, після чого машина їде на випробувальний коло.
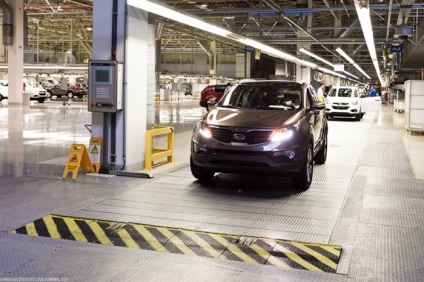
Кільце довжиною в кілька кілометрів. На цій трасі зімітовані різні варіанти покриття дороги, повороти, підйоми і спуски. Тест-пілот може не допустити автомобіль в продаж, якщо, на його думку, в конструкції автомобіля є які-небудь недоліки, або в його роботі є відхилення (брязкіт обшивки, недостатньо чуйне рульове управління, погана робота підвіски і т.д.). Якщо недоліків виявлено не було, то автомобіль потрапляє на стоянку готових авто і чекає своєї відправки.
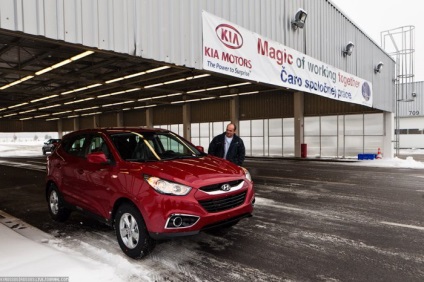