При відновному ремонті муздрамтеатру силового трансформатора прагнуть зберегти товщину плівки ізоляції пластин. В іншому випадку стрижні можуть виявитися товщі або тонше, ніж вони були, т. Е. Коло, описане навколо фігури стрижня, прийме елліпсовіднимі форму.
При перешіхтовке муздрамтеатру іноді на стару плівку накладають новий шар лакової ізоляції (на кожну пластину або через пластину). В цьому випадку діаметр стрижнів може збільшитися на 1-2%. Це враховують, заздалегідь з'ясовуючи, чи не утруднить таке потовщення стрижнів установку обмоток.
При відновленні ізоляції пластин великої партії стали доцільно застосовувати прийнятий на електромашинобудівних заводах конвеєрний метод лакування і запікання пластин. Цей метод являє собою єдиний і безперервний технологічний процес, при якому забезпечуються висока продуктивність праці і гарна якість лакової плівки.
Багато ремонтні заводи і майстерні мають такі установки, але перевезення пластин стали розібраного муздрамтеатру в майстерні або на заводи спеціально для лакування, особливо на великі відстані, не завжди доцільна. Під час навантаження, розвантаження і перевезення пластин вони неминуче піддаються деформацій, ударам і трясці, що різко погіршує магнітні властивості стали, особливо холоднокатаної текстурованої (гарячекатана сталь зараз для виробництва трансформаторів не застосовується і може зустрітися лише при ремонті старих трансформаторів). У багатьох випадках вигідніше спорудити на місці ремонту просту і дешеву конвеєрну установку.
Зображена на рис. 1 конвеєрна установка сконструйована для роботи в умовах виїзних ремонтів. Основними частинами установки є лакування верстат, т. Е. Два обертових гумових валика 2 (рис. 1, а), які змочуються лаком і між якими пропускають пластини стали, каркас 7 печі, цегляна кладка 9, нагрівальні елементи 6, роликовий ланцюг 4 і зірочки 8 з направляючими і проміжними валиками 5.
Каркас печі зазвичай виготовляють у вигляді двох ящиків з тонколистової сталі. У торцях ящиків передбачають вирізи для ланцюгів конвеєра. Іноді каркас зварюють з куточків у вигляді відкритої рами. Цегляну кладку розміщують в каркасі без зв'язує розчину. Нагрівальні елементи зазвичай виготовляють у вигляді спіралей, навитих з круглою ніхромового дроту діаметром 2 мм і вище. Орієнтовна схема з'єднання спіралей в зірку показана на рис. 1, б. В даному випадку передбачено шість спіралей, розміщених по всій довжині кладки печі. Для гарної якості запікання лаку загальна потужність нагрівачів повинна бути 50-55 кет.
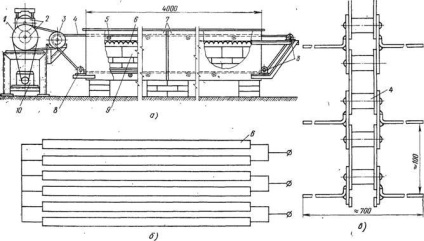
Мал. 1. Конвеєрна установка для лакування та запікання пластин стали: а - загальний вигляд, б-схема з'єднання в зірку спіралей з ніхромового дроту, в - приводний ланцюг; 1 - шків клинопасової передачі 2 - гумові валики, 3 - ведений шків і зірочка ланцюгової передачі, 4 - роликовий ланцюг, 5 - проміжний валик сталевий стрижень з вільно надягнутими відрізками труб), 6 - нагрівальні елементи, 7 - каркас печі, 8 - зірочки ланцюгової передачі, 9 - цегляна кладка, 10 - електродвигун з редуктором
Для конвеєра застосовують будь-які ланцюги і зірочки, наприклад велосипедні, мотоциклетні, від сільськогосподарських машин. У найпростіших установках використовують тільки один ланцюг. Щоб мати широке полотно, до пластин ланцюга приварюють сталеві прутки (рис. 1, в). Для цієї мети часто застосовують відрізки смугової сталі товщиною 1,5-2 мм і шириною 20-25 мм, попередньо зігнувши їх для жорсткості у вигляді швелера.
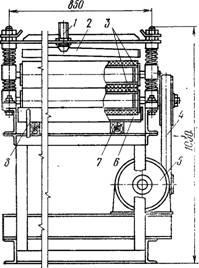
Мал. 2. Лакувальний верстат (вид з боку робочого місця)
1 - патрубок для під'єднання до бачка з лаком, 2 - крапельниця, 3 - різі нові валики, 4 - ремінна передача 5 - електродвигун з редуктором, 6 - ванночка з лаком, 7 - підставка, 8 - трубка для зливу надлишків лаку
При лакування застосовують лак № 302 або № 202, а в якості розчинника - гас або уайт-спірит. Лак, залитий в бачок лакування верстата (рис. 2), самопливом через патрубок 1 потрапляє в крапельницю 2 (трубку з отворами), розташовану вздовж верхнього гумового валика 3. Таким чином відбувається змочування лаком верхнього валика. Надлишок лаку стікає в ванночку 6, розташовану під нижнім валиком, і його нижня частина постійно змочується лаком.
Така конвеєрна установка проста у виготовленні, а також в збірці на місці ремонту муздрамтеатру. Основні елементи конвеєрної установки, наприклад роликові ланцюги, зірочки та спіралі, можуть легко доставлятися на місце ремонту. Приводний валик ланцюгової передачі, а також Кліноременная (ланцюгова) передача повинні бути заздалегідь змонтовані на лакування верстаті який також доставляють на місце ремонту.
З тимчасової конвеєрної установки неминуче будуть виділятися дим і гази, тому її бажано встановлювати в добре вентильованому приміщенні або під тимчасовим навісом, а в теплу погоду - на відкритому повітрі, захистивши її від попадання опадів і пилу. У будь-якому випадку необхідно передбачити вентилятори, щоб відганяти дим і гази в сторону. При роботі на конвеєрній установці необхідно дотримуватися правил техніки безпеки.
Лакування і запікання пластин стали на конвеєрній установці роблять у такий спосіб. Після попереднього прогріву печі протягом 2-3 чу налагодження і регулювання виробляють пробну лакування і запікання дослідних зразків. При досягненні необхідної якості і товщини лакової плівки приступають до масової лакування і запіканню.
Пластини стали, проходячи через валики верстата, автоматично потрапляють на рухому через піч стрічку конвеєра. В кінці конвеєра потік пластин стали із запеченою лакової плівкою сповзає з ланцюгів на спеціально підставлений стелаж (верстак), де пластини укладаються стопкою один на одного. Щоб пластини вкладалися стопкою, необхідно вкладати їх в гумові валики верстата в певному порядку і в одному і тому ж місці валиків.
Час проходження пластин по конвеєру становить 40- 45 сек. За це час запалюється і згорає розчинник (гас) і запікається лакова плівка. Охолоджуються пластини водою (душова установка) або повітрям.
Якщо змонтована конвеєрна установка не забезпечує необхідної якості запікання, змінюють температуру печі, перемикаючи отпайки в спіралях і додатково утеплюючи верхню частину печі, або змінюють швидкість руху ланцюгів конвеєра, підбираючи необхідні діаметри шківів в приводі клинопасової передачі (зірочки в ланцюгової передачі).
В процесі лакування і запікання контролюють товщину лакової плівки. Необхідна товщина плівки забезпечується силою натискання гумових валиків і підбором консистенції лаку. При відновлювальних ремонтів муздрамтеатру товщина плівки повинна бути такою ж, якою вона була в заводському виконанні. На трансформаторних заводах прийнята наступна товщина лакового покриття: при одноразовій лакування 0,005 ± 0,002 мм, при дворазової - 0,011 ± 0,003 мм, при триразовою - 0,016 ± 0,004 мм. Пластини, що мають жаростойкое ізоляційне покриття (типу Карло), допускається додатково не лакувати для магнітопроводів трансформаторів потужністю до 32 000 ква. Для магнітопроводів трансформаторів потужністю вище 32 000 ква застосовують додаткову одно- або дворазову лакування (карлітное покриття замінює одноразову лакування).
Після лакування пластини повинні мати рівномірну за кольором поверхню, гладку, блискучу, без напливів, потовщень і подряпин. Допускається подгара лакової плівки на 5% пластин одного типорозміру; площа подгара плівки не повинна перевищувати 5% площі пластини. При складанні муздрамтеатру підгорілі місця на сусідніх пластинах не повинні збігатися. Допускаються напливи і місцеві потовщення лаку, що не виходять за межі допусків на товщину ізоляційної плівки, допускається видимий слід від конвеєрної ланцюга, але він повинен бути закритий шаром лаку. Після охолодження при натисканні пальцем на лакової плівці не повинен залишатися відбиток.
Контрольне вимірювання товщини лакової плівки виробляють після кожної настройки лакування установки і після зміни режиму її роботи, але не рідше одного разу на зміну. Замір виробляють на п'яти вибірково взятих пластинах. Електричний опір плівки лаку вимірюють за інструкціями трансформаторних заводів після кожних двох годин роботи лакування установки. Вимірювання проводять на трьох пластинах в 3-5 місцях. При тиску електрода на плівку лаку 10 кг / см 2 питомий опір ізоляції однієї пластини має бути не нижче 120 ом / см 2.