Установка технічних засобів охорони.
Тел. . Телефонуйте!
ГлавнаяМеталлізація розпиленням
Процес осадження розпиленням полягає в расплавлении напилюваного матеріалу, розпиленні його струменем стисненого повітря або газу і осадженні на поверхні виробів шляхом удару і деформації частинок. Залежно від застосовуваного джерела тепла розрізняють газову, електродугову, високочастотну і плазмову металлизацию. Напилюваний матеріал може застосовуватися у вигляді дроту, стрічки або порошку.
Схема розпилювальних головок метал-лизатор представлена на рис. ХП1.1. Найбільшого поширення набули електродугові Металлізатори дротяного твань (рис. XII 1.1, а). Електрична дуга горить між двома електродами в потоці стисненого повітря, який захоплює краплі розплавленого металу, подрібнює їх і направляє на поверхню деталі. Дуга отримує постійний або змінний струм від зварювальних трансформаторів або від перетворювача постійного струму. Електродугові апарати можуть бути вико
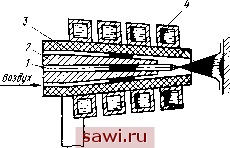
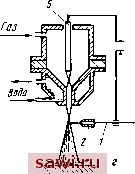
Мал. XIII.1. Схема розпилювальних головок електродугового (а), газового (б), високочастотного (в) н млазменмого (г) металізатора:
i - розпорошується дріт; 2 - наконечники для дроту; 5 - повітряний сопло; 4 -індуктор; 5 - вольфрамовий електрод
вани для напилення матеріалів, температура плавлення яких не перевищує 2800 ° С, і застосовуються для напилення сталей і кольорових металів.
При газовій металізації (рис. XIII 1,6) кінець дроту плавиться в газовому полум'я і частки розплавленого металу захоплюються потоком згорілих частинок. Потрапляючи в струмінь стисненого повітря, частинки металу дробляться і набувають значну швидкість. Найбільш висока температура (3180 ° С) досягається при використанні ацетилено-кисневого полум'я. Газопламенная металлизация застосовується для нанесення покриттів з кераміки, тугоплавких сполук і металів з особливо високою температурою плавлення.
Різновидом газової металізації є реактивна і вибухова металізації, а також металізація з підвищеним тиском горючого газу. У реактивних газових металізатора плавлення і розпилення металу відбуваються в спеціальній камері, куди подаються пропано-кисло-рідна суміш і напилюваний метал у вигляді порошку. В результаті згорання горючих газів з сопла камери згоряння розм'якшені частинки металу разом з продуктами згорання вириваються назовні з великою швидкістю (до 1600 м / с) і направляються яа металізуюча поверхню. Вибухова металлизация заснована на використанні явища детонації (теплової хвилі). Вра-щаюпдійся барабан зі звуконепроникним кожухом має камеру згоряння, куди noj) -ціямі подаються порошок з карбіду вольфраму, ацетилен і кисень. Вибухова суміш при певному тиску запалюється електричною іскрою. В результаті впливу теплової хвилі і тиску розширюються газів температура в камері згоряння підвищується до 3300 ** С. При повороті барабана металеві частинки і горюча суміш зі швидкістю понад 2700 м / с вириваються з камери згоряння. Гази згоряють на повітрі, а метал осідає на поверхні деталі в розм'якшеному стані і зв'язується з основою микросварки. Товщина покриття при цьому способі металізації становить 0,05-0,2 мм.
Реактивну і вибухову металлизацию застосовують для нанесення тугоплавких матеріалів з метою підвищення зносостійкості ріжучих і вимірювальних інструментів, робочих поверхонь формувальних матриць і інших деталей. Металізація за допомогою підвищеного тиску горючого газу також призначена для розпилення порошків твердих і керамічних сплавів (оксидів алюмінію і цирконію). Тут відсутній стиснене повітря. Його роль виконує горючий газ. Завдяки цьому вдається зберегти тепло металевих частинок і донести їх до деталі в розм'якшеному стані. Частинки з підставою зв'язуються микросварки. Як горючий газ застосовують водень або ацетилен. Замість порошку можна використовувати дріт.
При високочастотної металізації (рис. XIII.l, e) розплавлення напилюваного матеріалу здійснюється в індукторі струмами високої частоти від установок типу ЛГПЗ-
30, Л3-37 і ін Метал розпилюють стисненим-повітрям. Цей метод металізації застосовують в основному для напилення стали.
Процес тигельної металізації заснований на розпиленні підігрітим повітрям або газом попередньо розплавленого металу, що надходить в форсунку розпилювального апарату. Застосування цього методу обмежується можливістю нанесення тільки легкоплавких матеріалів, незручністю експлуатації тигельних апаратів, а також неможливістю виконання стельових робіт.
Плазмового напилення (рис. XIII.1, г) є одним з нових прогресивних способів металізації розпиленням. В основі процесу лежать ті ж закономірності, що й при плазмовому наплавленні. Висока температура плазмового струменя дозволяє виробляти розпорошення найбільш тугоплавких матеріалів. Застосування плазмообразующих-щих нейтральних газів запобігає окисленню напилюються матеріалів в процесі нанесення. Плазмового напилення є високопродуктивним процесом; так, продуктивність напилення вольфраму в вигляді дроту досягає 12 кг / год, у вигляді порошку 1,5 кг / год при корисному використанні 60-70% металу.
2. Технологія металізації
Технологічний процес металізації деталей розпиленням складається з послідовного виконання наступних операцій: підготовки поверхні деталей до металізації, власне металізації, механічної обробки після металізації і технічного контролю металізованих виробів.
Підготовка поверхні. Підготовка поверхні полягає в очищенні її від бруду, жирів, вологи, іржі та створенні на ній відповідної шорсткості. Від забруднень поверхню очищають промиванням в бензині або розчинниках, піскоструминної обдування, проточкою на верстатах, випалюванням в печах або нагріванням газовим пальником. Деталі, що були в експлуатації, особливо лиття та чавунні, просочені маслом, не завжди вдається очистити бензином і розчинниками, тому їх очищають нагріванням до температури 300-350 ° С в печах за допомогою газових пальників або паяльних ламп. Випал слід виробляти до повного вигоряння масла і випаровування вологи, т. Е. До припинення виділень диму і пари. Характеристика та область застосування основних способів підготовки поверхні перед металізацією розпиленням представлені в табл. XII 1.1, а їх вплив на зчіплюються-ність напиляного шару з основним металом - в табл. XIII 2.
Видно, що кожен із способів підготовки має свою область застосування. Деякі з них, наприклад спосіб рваною різьблення. насічка зубилом, анодно-механічного-ська обробка, забезпечують високу міцність зчеплення шару з основою, але значно знижують міцність від утоми деталей машин. Їх використовують в тих
Характеристики та області застосування основних способів підготовки поверхні деталей під металізацію
Нарізування рваною різьблення
Нарізування лій різьблення ковзанці
Насічка зубилом з подальшою піскоструминної обробкою
Намотування дроту з наступною піскоструминної обробкою
Обдування поверхні деталей з пістолета в спеціальній камері кварцовим піском з розміром зерен 0,5-2,5 мм під надлишковим тиском повітря 1-6 ат
Після проточки з метою отримання точності форми на токарному верстаті нарізають рвану різьблення з кроком 0,5-1,8 мм і глибиною 0,15-0,7 мм в залежності від діаметру деталі (мінімальні цифри для діаметра 10-20 мм, максимальні для діаметра 200 400 мм). Рвану різьблення отримують при установці різця в різцетримачі з вильотом 100- 150 мм і зміщення його нижче центру від 1 до 4 мм Після проточки на токарному верстаті за допомогою спеціального різця наносять ряд паралельних напівкруглих канавок глибиною 0,6 0,7 мм, розташованих на однаковій відстані одна від одної. Поверхня канавок обкатують роликом для додання форми хвоста. Замість паралельних канавок допускається нарізування круглої різьби з кроком 1,6 мм для сталі і 1,8 мм для чавуну
Насічка зубилом (вручну або механічно) рисок з подальшою піскоструминної обробкою
Дріт діаметром 0,5-1,5 мм намотують в один ряд з кроком намотування від 2 до 5 діаметрів про волоки. Після намотування і закріплення дроту (за допомогою зварювання) виробляють піскоструминну обробку всієї поверхні, яка підлягає металізації Після обробки різанням виробляють обдувку деталі сталевий або чавунної дробом діаметром 0,5-2 мм. Дріб вдаряється об поверхню деталі зі швидкістю 50-70 м / с, здійснює наклеп поверхні і надає їй шорсткість Металевим електродом із застосуванням вібратора на поверхню деталі наноситься метал висотою окремих виступів 0,1- 3 мм
Глибина Язвін (шорсткість) 50-100 мкм. Процес ведуть на грубих обдирних режимах за звичайною схемою
Для деталей складної форми, при закладенні тріщин на чавунних деталях, для деталей з рухомою посадкою, а також при підготовці до нанесення жароміцних і декоративних покриттів при товщині шару від 0,02 до 3 мм Забезпечує найвищу зчіплюваність і може застосовуватися в усіх випадках, де потрібна висока міцність зчеплення при товщині покриття від 0,5 до 20 мм. Недолік способа- значне зниження втомної міцності деталей. Широко використовується при ремонті валів і втулок з м'яких сталей
При нанесенні покриттів товщиною від 0,5 до 20 мм для відновлення розмірів валів, обойм та інших деталей з незагартованої і нецементірованной стали. Може застосовуватися для підготовки внутрішніх циліндричних поверхонь
Найбільш часто застосовується для плоских поверхонь незагартована деталей, рідше для циліндри-чегкіх деталей з товщиною покриття 0,15-4 мм Застосовують для відновлення загартованих важко навантажених деталей при товщині покриття 0,7-20 мм. Діаметр дроту повинен бути менше половини товщини шару
Для обробки внутрішніх і зовнішніх поверхонь будь-якої форми. Втомна міцність деталей при такій обробці не тільки не знижується, а навіть дещо зростає
Застосовується для загартованих сталей, можна обробляти внутрішні і зовнішні поверхні будь-якої форми
Те ж, що і електродугової, втомна міцність знижується на 20-30%