Основним способом переробки нафти є її пряма перегонка.
Перегонка - дистиляція (стікання краплями) - поділ нафти на різні за складом фракції, засноване на відмінності в температурах кипіння її компонентів.
Фракція - хімічна складова частина нафти з однаковими хімічними або фізичними властивостями (температурою кипіння, щільністю, розмірами), що виділяється при перегонці.
Пряма перегонка - це фізичний спосіб переробки нафти за допомогою атмосферно-вакуумної установки (рис. 1.1), принцип роботи якої полягає в наступному.
В результаті нагрівання нафти в спеціальній трубчастої печі 7 до 330. 350 ° С утворюється суміш парів нафти і випарувався рідкого залишку, що надходить в колону ректифікації 3 з теплообмінниками 2.
У ректифікаційної колоні (рис. 1.2) відбувається поділ нафтових парів на фракції, що становлять різні нафтопродукти. При цьому температура кипіння суміжних груп одержуваних фракцій може відрізнятися всього лише на 5. 8 # 730; С.
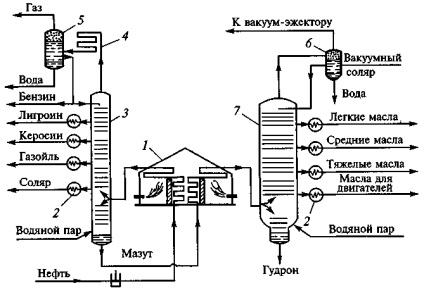
Мал. 1.1. Принципова схема атмосферно-вакуумної установки для
прямий перегонки нафти:
1 - трубчаста піч; 2 - теплообмінники; 3 - колона ректифікації; 4 - конденсатор; 5 - сепаратор; 6 - збірник соляру; 7 - вакуумна колона
Важкі фракції нафти, вступаючи в колону в рідкій фазі, вже в нижній її частині відокремлюються від парів і відводяться з неї у вигляді мазуту.
Залежно від хімічного складу нафти використовують дві схеми отримання палива (рис. 1.3). У першому випадку в інтервалі температур кипіння від 40 до 150 ° С відбирають авіаційні бензини і в інтервалі від 150 до 300 ° С - гас, з якого виготовляють реактивні палива. У другому випадку в інтервалі температур кипіння від 40 до 200 ° С відбирають автомобільні бензини і в інтервалі від 200 до 350 # 730; С - дизельні палива.
Мазут, що залишається після відгону паливних фракцій (60. 80% від початкової маси нафти), використовують для отримання масел і крекінг-бензинів.
Вуглеводні з температурою кипіння нижче 40 ° С (попутні гази) використовують в якості добавок до деяких бензинів і в якості сировини для отримання ряду синтетичних продуктів, а також як паливо для газобалонних автомобілів.
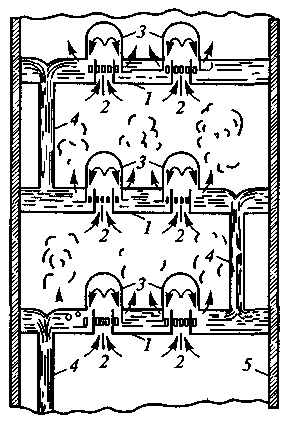
Продуктами прямий перегонки нафти (див. Рис. 1.1) є такі дистиляти: бензин (40. 200 ° С); нафта (110. 230 ° С); гас (140. 300 ° С); газойль (230. 330 ° С) і соляр (280. 350 ° С).
Мал. 1.2. Схема колпачковой ректифікаційної колони:
1 - металеві тарілки; 2 - отвори для проходження парів; 3 - ковпачки; 4 - зливні трубки; 5 - циліндричний корпус
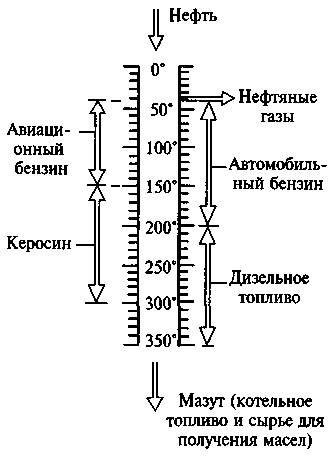
Мал. 1.3. Принципові схеми отримання найважливіших видів палива для двигунів при перегонці нафти
Середній вихід бензинових фракцій, що залежить від властивостей нафти, що видобувається, коливається від 15 до 25%. На частку інших палив доводиться 20. 30%.
Лігроїн, що має трохи більшу щільність, ніж бензин (важкий бензин), використовується як дизельне паливо і як сировину для отримання високооктанових бензинів.
Газойль, який є проміжним продуктом між гасом і мастилами, використовується як паливо для дизелів, а також є сировиною для каталітичного крекінгу.
Продукти, одержувані способом прямої перегонки, мають високу хімічну стабільність, так як в них відсутні ненасичені вуглеводні.
Використання для переробки нафти крекінг-процесів дозволяє збільшити вихід бензинових фракцій.
Крекінг - процес переробки нафти і її фракцій, заснований на розкладанні (розщепленні) молекул складних вуглеводнів в умовах високих температур і тисків.
Вперше крекінг був запропонований російським вченим А. А. Літнім в 1875 р а розроблений - В.Г.Шухова в 1891 р але перша промислова установка була побудована в США.
Існують наступні види крекінгу: термічний, каталітичний, а також гідрокрекінг і каталітичний риформінг.
Термічний крекінг використовують для отримання бензину з мазуту, гасу і дизельного палива.
Наприклад, при нагріванні до 500. 550 ° С під тиском 5 МПа вуглеводень цетан, що входить до складу гасу і дизельного палива, розкладається відповідно на нормальний октан і нормальний октен, які є складовими бензину:
Нові установки для термічного крекінгу в даний час вже не будують, так як одержувані з їх допомогою бензини при зберіганні окислюються з утворенням смол і в них необхідно вводити спеціальні присадки (інгібітори), які різко знижують темп осмоления.
Каталітичний крекінг - це процес отримання бензину, заснований на розщепленні вуглеводнів і зміні їх структури під дією високої температури і каталізатора.
Каталітичний крекінг на заводської установки був вперше здійснений в Росії в 1919 р Н.Д.Зелинский.
В якості сировини при каталітичному крекінгу (рис. 1.4) використовують газойльових і соляровим фракції, одержувані при прямій перегонці нафти, які нагрівають до температури 450. 525 ° С під тиском 0,15 МПа в присутності алюмоселікатного каталізатора, який прискорює процес розщеплення молекул сировини і ізомеризується продукти розпаду, перетворюючи їх в ізопарафінових і ароматичні вуглеводні. При цьому кількість олефінів знижується до 9. 10%, а октанові числа одержуваних бензинів, виміряні по моторному методу, рівні 78. 85.
Продукти каталітичного крекінгу є обов'язковими компонентами при виробництві бензинів марок А-72 і А-76.
Гідрокрекінг - процес переробки нафтопродуктів, що поєднує в собі крекирування і гідрування сировини (газойлів, нафтових залишків та ін.). Такий процес проводиться під тиском водню 15. 20 МПа при температурі 370. 450 ° С в присутності алюмокобальтомолібденового або алюмонікельмолібдено-вого каталізаторів.
Октанові числа бензинових фракцій, одержуваних в результаті гідрокрекінгу, - 85. 88 (по дослідницькому методу вимірювання). Гідрокрекінг підвищує також вихід світлих нафтопродуктів - бензину, дизельного і реактивного палива.
В якості сировини для каталітичного риформінгу зазвичай використовують бензинові фракції первинної перегонки нафти, що википають вже при 85. 180 ° С.
Риформинг проводять в середовищі водневомісний газу (70. 90% водню) при температурі 480. 540 ° С і тиску 2. 4 МПа в присутності молібденового або платинового каталізатора.
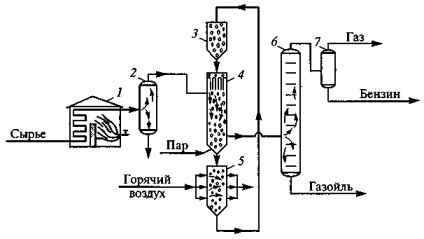
Мал. 1.4. Принципова схема каталітичного крекінгу:
1 - піч для нагрівання сировини; 2 - випарник; 3 - бункер з каталізатором; 4 - реактор; 5 - регенератор; 6 - колона ректифікації; 7 - газосепаратор
Риформинг при використанні молібденового каталізатора називається гидроформинг. а при використанні платинового каталізатора - платформинг. Останній, який є більш простим і безпечним процесом, в даний час застосовується значно частіше.
Каталітичний риформінг використовують для отримання високооктанового компонента автомобільних бензинів (85 по моторному методу вимірювання та 95 - по дослідницькому).
Отримання мастил. Під впливом ідей Д. І. Менделєєва нафтопромисловець В.І.Рогозін в 1876 р побудував близько Нижнього Новгорода перший в світі завод з виробництва масел з мазуту.
За способом виробництва розрізняють дистиляти та залишкові масла.
При отриманні дистилятів масел мазут нагрівають до 420. 430 ° С (див. Рис. 1.1), створюючи у вакуумній колоні розрідження в 50 мм рт. ст.
Вихід дистилятів масел з мазуту становить близько 50%, решта - гудрон.
Залишкові масла - це очищені гудрони. Для їх отримання мазут або напівгудрон змішують із зрідженим пропаном (6. 8 частин пропану на одну частину мазуту) при температурі 40. 60 ° С. Таким чином отримують авіаційні масла МК-22, МС-20 і трансмісійне масло МТ-16. МК-22 рекомендовано і для змащення агрегатів деяких автомобілів, наприклад вантажних автомобілів Мінського автозаводу.
В мастильних маслах, одержуваних з мазуту, крім вуглеводнів обов'язково містяться нафтенові кислоти, сірчисті з'єднання і смолисто-асфальтові речовини, тому їх, як і палива, необхідно очищати.