Більшість процесів переробки пластмас у вироби включає в себе три основні операції:
- а) нагрівання і раз-м'якшення полімеру;
- б) власне формування виробів;
- в) охолодження виробів.
Пресування, хоча і є найстарішим методом переробки полімерів у вироби, все ще залишається одним з основних. Технологія процесу полягає в тому, що матеріалу під тиском до 200 МПа надають задану форму. Пресуванням переробн-ють як термореактивні, так і термопластичні полімерні матеріали.
Пресування - зручний спосіб, яким можна отримувати вироби гарної якості з високою точністю розмірів. Однак н аппаратурном оформленні цей метод досить громіздкий і малопродуктивний.
Пряме (компресійне) пресування застосовують головним чином для термореактивних пластмас і гум, хоча в принципі воно може бути застосовано і для переробки термопластів. Але в останньому випадку необхідність охолодження форми перед витягом з неї вироби подовжує цикл, ускладнює процес і часто робить сто нерентабельним.
Подальшим логічним розвитком пресування з попереднім нагріванням полімерних матеріалів є метод литтєвого пресування, при якому порція полімеру розплавляється в камері перед формою, а потім розплав подається в форму, де здійснюють власне пресування під тиском і затвердіння.
Метод лиття під тиском є розвитком процесу литтєвого пресування. За цією технологією полімер розплав-ляется в матеріальному циліндрі литтєвий машини, а потім нприсківается безпосередньо в охолоджену форму. Процес лиття під тиском здійснюється на поршневих і шнекових машинах (рис. 9.2).
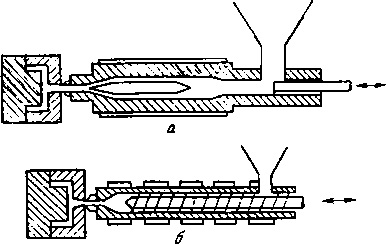
Мал. 9.2. Принципова схема поршневий (а) і шнекової (б) машин для лиття під тиском
Використання шнекового (черв'ячного) пластикатора зі зворотно-поступальним рухом шнека замість плунжера дозволяє не тільки нагріти і пластикують полімер перед уприскуванням, але і поліпшити гомогенізацію розплаву і підвищити точність дозування.
Фактори, що впливають на якість кінцевого продукту при литті під тиском, складні і взаємозалежні.
Екструзія - досить старий і добре відомий технологічний процес. Її застосовують в різних галузях промисловості для переробки найрізноманітніших матеріалів - від виготовлення макаронів до виробництва керамічних труб. Той, хто видавлював зубну пасту з тюбика або користувався м'ясорубкою, відтворював екструзійні процеси. Методом екструзії виготовляють різні погонажні вироби (труби, плівки) і формовані видувні вироби.
На рис. 9.3 показані схеми технологічних процесів виготовлення виробів з полімерів, в основі яких лежить екструзія.
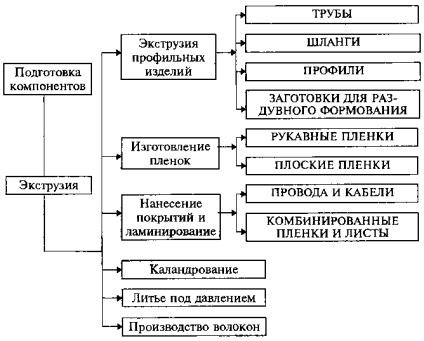
Мал. 9.3. Екструзія і технологічні процеси на її базі
Одна з основних переваг одношнекового екструдера - відносна простота конструкції і, як наслідок цього, низька вартість. У зв'язку з цим Одношнекові екструдери широко використовуються в сучасній хімічній технології.
Одношнековий екструдер зазвичай характеризують основними параметрами шнека - діаметром і співвідношення довжини та діаметру. Продуктивність екструдера залежить від його характеристик і від властивостей матеріалу, що переробляється.
При конструюванні формуючого інструмента необхідно враховувати особливості перебігу розплавів полімерів.
Екструзійно-видувного метод широко застосовують для виготовлення порожнистих (об'ємних) виробів. З його допомогою отримують контейнери різної ємності - від паливних баків до маленьких медичних флаконів (рис. 9.4).
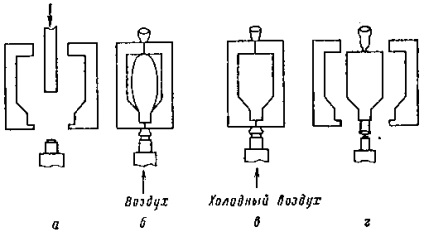
Мал. 9.4. Основні стадії отримання пластмасових бутлів екстра-Зіон-видувним методом
а - подача заготовки; б - видування; в - охолодження вироби; г - видалення вироби з видувний форми
Спочатку екструдують тонкостенную трубу (шланг), яка потім розрізається на відрізки певної довжини. Відрізок труби, званий заготівлею, поміщають між двома частинами порожнистої раздувной форми. Форму замикають, після чого заготовку роздмухують.
Каландрование є одним з методів переробки полі-мерів. В процесі каландрования отримують листи і плівки з пластмас. Каландр складається з трьох або більше нагрітих валянням Проходячи між ними, високов'язка полімерна маса пере-ється в плівку або лист. Маса матеріалу подається в зазор між двома першими валками, звідти вона виходить вже у вигляді плівки. Потім матеріал проходить навколо інших валків, кожен з яких виконує певну функцію.
У звичайному четирехвалковую каландрі є три формуючих (робочих) зазору; перший регулює швидкість подачі матеріалу, другий діє як дозуючий пристрій. Товщину листа визначає зазор між останньою парою валків (рис. 9.5). Ці валки можуть бути глянцевими, матовими або рифленими. Каландрование часто порівнюють з екструзією, розглядаючи останню пару валків як фільєру з обертовими поверхнями.
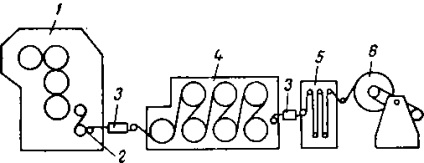
Мал. 9.5. Схема технологічної лінії на базі Ь-образного каланди ра для виробництва листів з пластмас
1 - основний каландр; 2 - гофрують каландр; 3 - регулятор товщини; 4 - система водяного охолодження; 5 - компенсатор; 6 - намотчик
Листи та плівки високої якості можна з однаковим успіхом отримувати як каландруванням, так і екструзією. У загальному випадку нелегко оцінити переваги та недоліки цих процесів, і зазвичай доводиться вирішувати в кожному конкретному випадку, який метод слід вибрати. Можна, однак, констатувати, що плівки і листи з поліетилену, поліпропілену і полістиролу частіше отримують екструзією. Що стосується переробки ПВХ, а також гуми, то для цих цілей майже завжди використовують каландрование, так як при каландрование небезпека деструкції полімеру менше, ніж при екструзії.
Екструдери легше розміщувати і зручніше обслуговувати, ніж ка-Ландри. Однак каландри забезпечують більш високі робочі швидкості, ніж екструдери, що свідчить про перевагу технологічних ліній на базі каландрів, незважаючи на те, що для їх розміщення необхідні великі виробничі площі.
Термоформування виробів з листових і плівкових по-лімерних матеріалів об'єднує три основні методи: ва-Куум-формування, пневмоформування і формування за допомогою сполучених металевих форм. Всіх їх об'єднує те, що при цьому вироби з листових пластиків можна отримувати, притискаючи розм'якшений напівфабрикат до оформляє внутрішньої або зовнішньої порожнини форми.
Найбільшого поширення в промисловості має вакуум-формування (рис. 9.6). У цьому процесі зазвичай використовують листи, які закріплюють в рамі, а потім нагрівають. Після досягнення необхідної температури і стану полімерного листа його нагрівання припиняють і з порожнини між листом і формою відкачують повітря. Атмосферний тиск притискає лист до фор-ме, на якій він охолоджується і твердне, точно відтворюючи її геометрію.
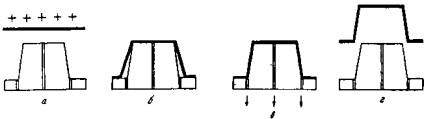
Мал. 9.6. Послідовність операцій при вакуум-формуванні заго-товки з попередньою витяжкою пуансоном
а - нагрівання заготовки; 6 - попередня витяжка матеріалу; в - формування вакуумом; г - видалення відформованої вироби
Одне з основних переваг процесу термоформования полягає в низькій вартості форм. При виготовленні зразків або дослідних партій виробів зазвичай використовують форми з таких матеріалів, як дерево, бетон, пластмаси та металлонаполненние епоксидні смоли. Форми, призначені для тривалої експлуатації, як правило, виконують зі сталі або алюмінієвих сплавів.
Технологія термоформования відносно проста і дешева, при цьому використовується просте обладнання, а вихідними матеріалами служать плівки в рулонах або листи. Недолік цієї технології полягає у великій кількості відходів, що утворюються, яке при формуванні деяких виробів досягають 40%.