Характеристика методів протягування;
Характеристика методів протягування
Протягування є одним з найбільш продуктивних видів обробки металів різанням. Висока продуктивність при протягуванні пояснюється великою сумарною довжиною ріжучих крайок, що одночасно беруть участь в процесі різання.
Протяжка - це багатолезовий ріжучий інструмент, при роботі якого в контакті з простягається деталлю знаходиться одночасно кілька ріжучих лез, що мають велику сумарну довжину. Практично протяжка є інструментальної налагодженням, за один прохід якої проводиться чорнова і чистова обробка. Процес протягування замінює стругання, фрезерування, чорнове шліфування, кругло Різьбонарізання і ін.
Протягання є складним і дорогим спеціальним інструментом, що виготовляється для обробки певних деталей. Тому економічна ефективність від їх застосування в повній мірі виявляється лише при масовому і серійному характері виробництва.
Протягання - вузько спеціалізований інструмент, призначений і розраховується для обробки однієї або декількох певних деталей, і в той же час досить дорогий. Це і обумовлює рентабельність застосування протяжок саме в масовому і великосерійному виробництві.
Однак протягання досить широко застосовуються також і в дрібносерійному виробництві, зокрема, у важкому машинобудуванні, верстатобудуванні, в тих випадках, коли необхідна точність обробки деталі може бути отримана тільки протягуванням, наприклад, при обробці многошліцевих отворів. Довжина протягаються отворів L не повинна перевищувати триразової величини діаметра отвору D, т. Е. L = 3 D і менше. Діаметр протяжок для отворів коливається від 3 до 300 мм.
Протягання мають високу продуктивність, незважаючи на те, що вони працюють при малих швидкостях різання - 3 - 8 м / хв. Причиною цього є велика довжина ріжучих крайок, що одночасно беруть участь в зрізанні шарів металу. Так, наприклад, при обробці протягуванням отвори діаметром 30 мм, якщо в контакті з деталлю буде одночасно перебувати п'ять зубів, сумарна довжина ріжучих крайок, що одночасно беруть участь в зрізанні шарів металу, дорівнює приблизно 470 мм. Якщо та ж деталь буде оброблятися четирехзубие зенкером з припуском 1,5 мм на сто-рону, то сумарна довжина ріжучих крайок, що одночасно беруть участь в різанні, буде тільки близько 7 мм. Тому продуктивність протягання буде значно перевершувати продуктивність зенкера, хоча він працює зі швидкістю різання 20 -30 м / хв.
Висока продуктивність протяжок обумовлена також тим, що кожна протяжка з'єднує в собі чорнові, чистові і калібрів зуби, завдяки чому однією операцією протягування можуть бути замінені дві або три окремі операції. Так, наприклад, протягування може бути застосоване замість наступних трьох операцій: зенкерования, попереднього і остаточного розгортання або замість фрезерування і подальшого шліфування площини.
Крім того, продуктивність протягання зростає внаслідок того, що за період різання кожен зуб знаходиться в контакті з оброблюваної поверхнею, ніж протягування відрізняється, наприклад, від фрезерування і інших переривчастих процесів обробки металів різанням.
Тому в даний час протягування успішно витісняє інші види обробки в масовому і великосерійному виробництві - зенкування і розгортання просвердлених отворів, а також отворів, отриманих куванням і литтям; фрезерування і стругання площин і фасонних поверхонь; довбання різних фігурних наскрізних отворів - многошліцевих, багатогранних, криволінійних і т.п .; нарізування коліс внутрішнього зачеплення, прямозубих конічних коліс, зубчастих рейок, секторів, коліс зовнішнього зачеплення і т.п.
Обробка заготовок на протяжних верстатах
Протягуванням отримують деталі з високою точністю розмірів і малою шорсткістю поверхні. За продуктивністю процес протягування в 5-10 разів вище фрезерування і в 10-15 разів вище растачивания і свердління. Крім того, протяжні верстати нескладні з кінематики і прості в обслуговуванні, так як найчастіше одне головне поступальний рух різання вбудовано в кінематичну схему верстата, а рух подачі закладено в самій конструкції протяжного інструменту.
Обробка поверхонь простяганням проводиться як на звичайних горизонтально і вертикально-протяжних верстатах, так і на спеціалізованому обладнанні.
Протягування внутрішніх і зовнішніх поверхонь набуло широкого застосування на заводах великосерійного і масового виробництва завдяки високій продуктивності і точності обробки. Протягування, як правило, виключає можливість шлюбу за розмірами і чистоті оброблених поверхонь.
Протягування застосовують для обробки симетричних і асиметричних наскрізних отворів різних форм, наскрізних пазів і напіввідкритих отворів, зовнішніх поверхонь: площинних, канавок, тел обертання.
Отвори під протяжку зазвичай попередньо свердлять або розточують. Зовнішні поверхні обробляють протяжками в чорному вигляді без попередньої обробки. Попередньо отримане вихідний отвір далі обробляють протяжкой. Отримані протягуванням отвори показані на рис.23.
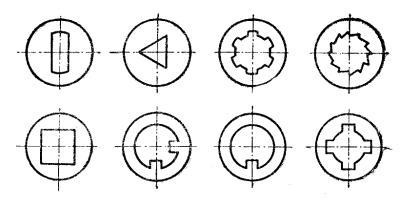
Мал. 23. Різні форми отворів, одержувані протяганням.
Приклад обробки шпоночной канавки дан на рис.24. Напрямна втулка одним кінцем входить в кронштейн, другий її кінець входить в отвір заготовок. Уздовж втулки зроблений проріз, в якій ковзає протяжка. Таким чином, одношпоночная протяжка отримує надійне напрямок при роботі, що забезпечує хорошу якість роботи і високу точність обробки.
Якщо у заготовки один торець не був оброблений, то при протягуванні заготовку необробленим торцем встановлюють на сферичну підкладку. Під дією сили різання заготовка повертається на сферичної підкладці і встановлюється по протяжке. Оброблений торець оберігає зуби протяжки від дії окалини.
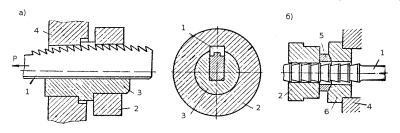
Мал. 24. Протягування отворів: а - шпоночной канавки; б - круглого отвору: 1 протяжка; 2 - заготовка; 3 - напрямна втулка; 4 - завзятий кронштейн станини верстата; 5 - сферична підкладка; 6 - втулка-сідло під сферичну підкладку 5.
Профільна схема протягування площині передбачає попередню обробку цієї площини на строгальном верстаті. Протягування вертикальних площин або поверхні фігурного профілю показано на ріс.25.а. Тут зовнішня протягання 1 обробляє заготовку 2, закріплену в пристосуванні 3. На ріс.25.бпріведен приклад обробки горизонтальній площині зовнішньої протяжкой. Тут в роботі одночасно беруть участь кілька зубців, протяжка рухається зі швидкістю різання V м / хв, подача на зуб Sz є одночасно товщина шару, що зрізається а мм і глибина різання t мм, т. Е. T = а = Sz мм / зуб.
Рис.25. Протягування отворів: а - шпоночной канавки; б - круглого отвору: 1 - протяжка; 2 - заготовка; 3 - напрямна втулка; 4 - завзятий кронштейн станини верстата; 5 - сферична підкладка; 6 - втулка-сідло під сферичну підкладку 5.
З метою підвищення продуктивності праці використовуються схеми безперервного протягування. В цьому випадку заготовки переміщаються відносно нерухомої протягання. Щоб забезпечити прямолінійний рух оброблюваних деталей відносно нерухомої протягання, необхідно використовувати замкнуту ланцюг з рядом пристосувань, які ковзають по напрямних станини (рис. 25.В). Закріплення заготовок у пристроях і їх звільнення після обробки здійснюються автоматично або вручну.
Відносний рух протяжки і деталі може бути обертальним. При цьому заготовки закріплюються на обертовому круглому столі і проходять під протяжкой, прикріпленою до нерухомого кронштейну (рис. 25. г).
При протягуванні тіл обертання плоскими протяжками (рис. 25. д) заготівлі повідомляється головне обертальний рух, а протяжка робить поступальний рух по напрямку дотичної до заготівлі.
На рис. 25.е показаний принцип обробки тіл обертання улиточной протяжкой. Цю протягання можна розглядати як звичайну плоску протяжку для зовнішнього протягування, навернену на циліндр.
Для здійснення процесу зовнішнього протягування равликову протяжками заготовка отримує швидке головне обертальний рух зі швидкістю різання V м / хв, а протяжка - повільне обертальний рух подачі Sк. Крім того, радіальна подача Sz здійснюється за рахунок перевищення одного зубця над іншим на величину:
Схема роботи плоскою протяжкой з профільної схемою представлена на рис. 26. а. Зуби протягання виготовляються з нахилом під кутом # 969; = 10 - 20 °, що полегшує процес протягування. Зубці забезпечені канавками, які розташовуються в шаховому порядку і служать для дроблення стружки на частини. Заготовки, отримані після штампування і кування, обробляють протяжками прогресивної схеми різання (рис. 26. б). У такий протягання немає перевищення Sz між зубцями, але вона встановлюється кілька похило до вертикалі, під кутом # 966 ;. В цьому випадку Sz = tр # Тисячу чотиреста шістьдесят вісім; sin # 966; мм, де tр - крок між зубцями протягання.
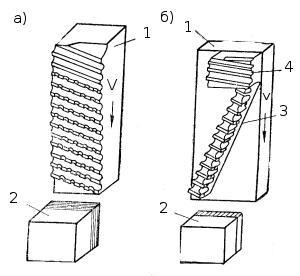
Мал. 26. Обробка плоскими протяжками:
а - робота плоскою протягання з профільної схемою;
б - робота протягання прогресивної схеми різання.