Після зовнішньої мийки вузлів і агрегатів із застосуванням мийного обладнання або вручну деталь надходить на розбирання. Заіржавілі різьбове з'єднання очищають металевою щіткою, змочують спеціальними проникаючими рідинами, можна гальмівний. Ефективне застосування будь-якого рідкого перетворювача іржі або, в крайньому випадку, оцтової кислоти. В останньому випадку деталі нарізного сполучення промиваються водою і змащується. Обірвалася частина болта або шпильки з нарізного отвору видаляють свердлом меншого діаметру. Різьбові отвори під болти і шпильки відновлюють шляхом нарізування різьблення збільшеного (ремонтного) розміру. При необхідності забезпечення різьблення номінального розміру, зношене отвір рассверливают, нарізають в отворі різьблення, вкручують пробку, стопорять її, свердлять отвір і нарізають різьбу номінального розміру.
Різьбові з'єднання класифікуються на три групи, ко-торие наведені в табл.1.
Для розбирання різьбових з'єднань застосовують інструмент ручний і механізований. До ручного інструменту відносяться гайкові ключі наступних видів: з відкритим ротом двусторон-ня; кільцеві двосторонні колінчаті (накладні); торцеві немеханізовані зі змінними головками; спеціальні.
Накладні ключі охоплюють всі грані гайки, що надає їм більшу жорсткість і довговічність. Накладними ключами з 12-гранним зевом можна повертати гайки при отвертиваніі на 30 °, що дуже важливо при роботі в труднодоступних місцях.
Торцеві ключі можна обертати, що не переставляючи з межі на грань, тому скорочується час на відкручування гайки по срав-рівняно з відкритими гайковим ключем.
Зі спеціальних ключів при розбиранні застосовують коловоротні ключі і ключі для круглих гайок. Коловоротні ключі раціональні для отвертиванія болтів і гайок невеликих розмірів. Про-тивність праці може бути підвищена в 2. 5 разів.
Завдання скорочення витрат праці при розбиранні різьбових соеди-нений в основному вирішується застосуванням механізованого інструменту.
Крутний момент отвертиванія гайок і болтів (Н # 903; м) діаметром від 10 до 26 мм визначають за формулою
де - коефіцієнт, що враховує стан нарізного сполучення. Dcp - середній діаметр різьби гайки, мм.
Для викручування шпильок застосовують ексцентрикові, клі-нові, цангові наконечники і спеціальні ключі.
Для з'єднань із значним крутним моментом (до 350 Н # 903; м) використовують Шпильковерти. Так, наприклад, для викручування шпильок всіх діаметрів з блоку циліндрів двига-теля використовується Шпильковерти, який містить механізми для захоплення шпильок і їх звільнення після викручування. В результаті використання цих Шпильковерти виробник-ність праці збільшується на 30. 40%.
Таблиця 1 - Класифікація різьбових з'єднань і значень крутного моменту при розбиранні
Місцезнаходження в автомобілі
Приклади різьбових з'єднань
Різьбові з'єднання забезпечують складання вузлів як за допомогою різьблення, що знаходиться безпосередньо на деталі (свічка запалювання, регулювальні гвинти в механізмі газорозподілу, кульові пальці шарнірів рульового приводу), так і за допомогою кріпильних деталей-болтів, шпильок, гайок спеціального і загального призначення. Спеціальні застосовують у відповідальних вузлах (шатунні болти, шпильки кріплення, головки циліндрів і т.п.) або там де без них технологія збирання - розбирання ускладниться.
Відповідальні кріпильні з'єднання мають невеликий крок різьби і захисне покриття.
До основних несправностей різьбових з'єднань відносяться - ослаблення попереднього затягування, пошкодження та зрив резьби.Самоотворачіваніе відбувається в основному через вібрації, в результаті знижується сила тертя в самій різьбі і на контактному торці гайки або головки болта. Швидкого ослаблення кріплення схильні карданний вал, стартер, паливний насос, генератор.
Основною причиною зриву різьблення при ремонтах є затягування з'єднань із зусиллями, що значно перевищують нормативні. Кріпильні деталі, що використовувалися 10-15 разів, зберігають попередню затяжку в 2-4 рази гірше ніж нові. При невиконанні кріпильних робіт при ТО-2, наприклад, у двигуна, до 80-100 тис. Км його пробігу слабшає затягування майже 15% різьбових з'єднань.
Перед складанням різьблення повинна бути очищена і змазана маслом. Довжина ввертати частини болта для сталевої деталі повинна бути від одного до двох діаметрів різьблення. Збільшувати глибину ввертиванія марно, оскільки основне навантаження сприймають тільки кілька витків різьби, розташованих біля вхідних поверхні деталі. При навертання гайки болт вибирають по довжині таким, щоб він виступав з гайки не більше ніж на два-три витка різьби. З'єднання забезпечують герметичність паливо, повітро, водо- і маслопроводів затягуються плавно. Останні 60-90 0 повороту треба робити без ривків за один прийом. Якщо вузол збирається з розукомплектованих деталей і має ущільнювальну прокладку, то він спочатку обжимается моментом в 1,1 рази більшим ніж за технічними умовами
Потім послаблюють гайки (болти) і вузол повторно затягується необхідним моментом. Ця операція забезпечує рівномірність затягування.
У многоболтових різьбових з'єднань гайки затягують поступово, в два-три прийоми, в певній послідовності, що попереджає деформацію деталі. Якщо сполучаються деталі прямокутної форми, то затягування потрібно починати з середніх гайок, при розташуванні гайок по колу їх слід затягувати хрест-навхрест. На рис. 5. цифри позначають послідовність затягування гайок. Перевищення моменту затягування може пошкодити (зірвати) різьблення або викликати плинність матеріалу стержня болта (шпильки) і ослаблення затяжки. В інструкціях заводів-виготовлювачів, в технологічних картах вказані моменти затяжки для найбільш відповідальних вузлів.
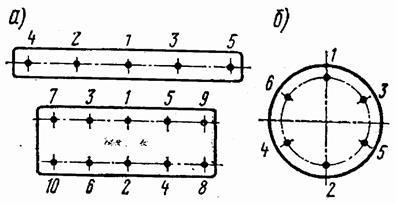
Малюнок 5 - Послідовність затягування гайок на різних поверхнях