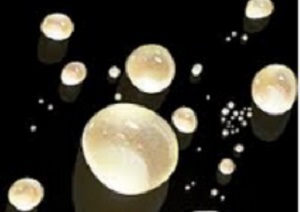
Характеристика сірчистих сполук газоконденсату.
За змістом загальної сірки газоконденсату діляться на 3 групи:
-бессерністие і малосірчисті, що містять не більше 0,05% мас. загальної сірки, ці конденсати не беруть під очищенні від сірчистих сполук;
-сірчисті, що містять від 0,05 до 0,8% мас. загальної сірки, необхідність очищення цих конденсатів вирішується в залежності від вимог до товарних продуктів;
- високосірчисті, що містять більше 0,8% мас. загальної сірки, очищення таких конденсатів практично завжди необхідна.
Сірчисті з'єднання в газових конденсатах представлені різними класами.
У легких дистилятах містяться, в основному, аліфатичні меркаптани C2 - C5 нормального і изостроения, що володіють неприємним запахом.
Їх витягують з конденсатів для отримання одорантов. У більш важких фракціях містяться сульфіди (аліфатичні, циклічні і ароматичні) і тіофену, представлені алкілзаміщених тіофенів, бензотіофенамі, нафтенобензотіофенамі і ін.
Наявність сірчистих сполук в конденсатах призводить до погіршення термічної стабільності вироблюваних з них палив, збільшує їх корозійну агресивність, призводить до викиду в атмосферу при згорянні палива шкідливих речовин, надає палив неприємний запах.
Найбільш агресивними сірчистими сполуками є меркаптани.
Очищення паливних фракцій від меркаптанів
Основними напрямками демеркаптанізаціі газових конденсатів є:
-лужна екстракція меркаптанів з наступним використанням легких меркаптанів в якості одорантов;
-каталітичне окислення меркаптанів до сульфідів;
Лужна екстракція меркаптанів заснована на екстракції меркаптанів водними розчинами гідроксиду натрію з утворенням меркаптіди і зворотної реакції - гідролізу меркаптіди з утворенням вільних меркаптанів і луги:
RSH + NaOH RSNa + H2O
RSNa + H2O RSH + NaOH
Найбільш поширеним процесом каталітичного окислення меркаптанів є процес «Мерокс».
Процес складається з 2 х стадій: екстракція розчинних в лугу меркаптанів розчином їдкого натру, окислення залишилися меркаптанів в дисульфіди киснем повітря.
В якості каталізаторів використовують суміші моно- і дісульфірованних похідних фталоцианина кобальту і ванадію.
Як недоліки процесу слід зазначити: многостадийность, застосування агресивних лужних розчинів, що вимагають використання спеціальних сортів сталі, утворення великих кількостей стічних вод.
Цей процес дозволяє видалити з газоконденсату все класи сірчистих сполук, а також інші гетероатомних сполуки- азот і кисень.
В основі процесу-переклад всіх сірчистих сполук розчинених у конденсаті, в сірководень:
RSH + H2 RH + H2S
RSR '+ H2 RH + RH' + H2S \
Використовують як каталізатори алюмокобальтмолібденовие і алюмонікельмолібденовие, в який іногдадобавляют для міцності 5 7% діоксиду кремнію.
Процес проводять при температурі 310- 370 ОС, тиску 2,7- 4,7 МПа, режимні показники підбирають в залежності від використовуваного каталізатора і сировини.
Очищення від сірчистих сполук ці методом проводиться за допомогою природних і синтетичних твердих сорбентів: бокситів, оксиду алюмінію, силикагелей, цеолітів і ін.
При проведенні адсорбції при підвищених температурах 300- 400 ° С протікають адсорбционно-каталітичні процеси, що призводять до розкладання сероорганических з'єднань або переводу їх в неактивні форми.
Адсорбційну очистку доцільно застосовувати при невеликому вмісті сірки- до 0,2% мас.
Метод заснований на використанні екстрагентів, селективно витягають з газоконденсату сірчисті з'єднання.
Як екстрагентів запропоновані гідроксид натрію, водні розчини етаноламінів, диметилформамід, діетиленгліколь, диметилсульфоксид та ін.
Однак жоден з вживаних в даний час екстрагентів не задовольняє всім необхідним требованіям- високою розчинюючої здатністю по відношенню до сірчистим сполукам, великою щільністю, низькою в'язкістю, доступністю і дешевизною, відсутністю токсичності і корозійних властивостей.
Виробництво автомобільних бензинів з газоконденсату
Бензинові фракції, виділені з газоконденсату, розрізняються по вуглеводневому складу внаслідок різної хімічної природи вихідних конденсатів.
Аналіз фізико-хімічних властивостей і хімічного складу бензинових фракцій, виділених з газоконденсату різних родовищ, дозволив виявити ряд закономірностей.
Бензинові фракції, виділені з конденсатів північних регіонів, містять велику кількість нафтенових вуглеводнів, є порівняно високооктановими внаслідок підвищеного вмісту вуглеводнів изостроения в початкових конденсатах.
Склад отриманих бензинових фракцій обумовлює вибір технології отримання на їх основі товарних бензинів.
В 1 м випадку, досить провести фракціонування з наступним додаванням високооктанових компонентів.
У 2 м випадку, додатково слід застосовувати термічний і каталітичний крекінг, риформінг і депарафінізації.
В цілому існують кілька напрямків облагородження бензинових фракцій, отримання з них товарних композиційних автомобільних бензинів: термічне і каталітичне облагороджування, введення антидетонаційних присадок і високооктанових компонентів, додавання бензинів риформінгу і крекінгу.
Каталітичне облагороджування бензинів не вийшло за рамки лабораторних досліджень.
Термічне облагороджування бензинових фракцій. виділених з газових конденсатів, проводиться в присутності метану (метаріформінг) і дозволяє отримати бензин з октановим числом 72-76 (Шебелинський ГПЗ).
Застосування в якості присадки тетраетилсвинцю звелося до мінімуму з екологічних міркувань.
Найбільш широко застосовуються високооктанові компоненти.
Крім давно застосовуються для цієї мети алкілат і бензинів риформінгу і інших вторинних процесів, все ширше стали застосовуватися кисень з'єднання: спирти, в першу чергу метанол і метилтретбутиловий ефір (МТБЕ).
Виробництво реактивних палив з газоконденсату.
Основою виробництва реактивних палив з газових конденсатів є фракція 135- 230 о С.
Ця фракція задовольняє основним вимогам на реактивні палива.
Розширення фракційного складу фракції призводить до погіршення низькотемпературних характеристик реактивних палив і вимагає проведення депарафінізації.
При розширенні фракційного складу крім палив РТ і ТС-1, можна отримати інші марки: при полегшенні фракційного складу Т-2, при утяжеленіі- Е-1.
В останньому випадку для поліпшення низькотемпературних властивостей палива необхідна депарафінізації.
Виробництво дизельного палива з газоконденсату.
Як дизельні палива для швидкохідних двигунів можуть бути використані фракції газоконденсату, википають вище 160 о С.
Залежно від глибини відбору (температури кінця кипіння) можна отримати ту чи іншу марку палива. Наприклад, фракція з межами википання 150-180- 300 о С відповідає рекомендаціям щодо дизельне паливо зимової марки, а фракція190-200- 310-350 о С - вимогам на дизельне паливо річної марки.
Розширення фракційного складу призводить до погіршення якості палива, для отримання палив, які відповідають сучасним вимогам, необхідно застосування присадок.
Для поліпшення характеристик газоконденсатного дизельного палива широкого фракційного складу застосовують: вязкостниє (протизносні) присадки (АЗНІІ- продукт конденсації нафталіну з холодоагентом), присадки, що підвищують цетанове число, наприклад, кисень з'єднання, що є відходом нафтохімічних виробництв, антиокислювачі.
Газові конденсати є не тільки цінною сировиною для виробництва бензинів, реактивних і дизельних палив, але можуть бути використані для комплексної хімічної переробки з отриманням спиртів, високооктанових компонентів, одоранту, розчинників, ароматичних вуглеводнів, різних інгібіторів і ін.