Багато швидкозношувані деталі обладнання мають велику вагу, хоча в роботі бере участь тільки їх тонкий зовнішній шар, вага якого часто не перевищує 10-15% загальної ваги. Такі деталі економічно доцільно відновлювати наплавленням зношених поверхонь електродами і сплавами з по-щення твердістю.
Спеціальні електроди марок ОЗН-250, ОЗН-300, ОЗН-350, ОЗН-400 і У-340 (табл.26) застосовуються для отримання наплавлення середньої твердості деталей з вуглецевих і середньолегованих сталей (цифрові індекси показують середню твердість третього шару наплавлення по Брінеллю).
Табл.26. Електроди для наплавлення середньої твердості
Спроби використовувати вуглець як основний ведучий легуючих ющий елемент (збільшення вмісту його в наплавленні більше 0,3%) приводили до утворення тріщин і пір в наплавленого металу.
Слід зазначити, що вуглецеві стали з С = 0,3-0,7% схильні до утворення гартівних структур, що знижують ін-ність стали, і утворення тріщин при звичайних методах сварок-ки, що застосовуються для маловуглецевих сталей.
Досвід застосування електродів ОЗН і У-340 свідчить про високу якість електродів зі шлакоутворюючих покриттям основного типу (мармур, плавиковий шпат) і з марганцем, вве-денним в якості ведучого легуючого елемента. Основна перевага зазначених електродів полягає в меншій схильності до утворення тріщин.
Зносостійкість загартованого металу, наплавленого елект-родом ОЗН-300, в 1,5 рази вище, ніж загартованої сталі марки 40Х. Електроди ОЗН-300 і ОЗН-250 слід рекомендувати для наплавлення загартованих деталей з середньовуглецевих сталей марок 40 і 45, з хромистих сталей марок 30Х, 35Х, 40Х та ін. Ці елек-Трод застосовні для наплавлення деталей з маловуглецевих сталей і сталей марок 35 і 40.
Метал, наплавлений електродами ОЗН-250, добре обро-розробляються ріжучими інструментами. Твердість металу, наплав-ленного електродом ОЗН-300 і ін. Може бути знижена відпалом при 850 ° і охолодженням разом з піччю.
При загартуванню наплавлений метал досягає твердості НВ 400-460.
Електродами Т-540, Т-590 і Т-620 (див. Табл. 26) для отри-ня високої твердості наплавляют деталі, виготовлені з це-ментіруемих і гартованих сталей, а також деталі робочих ор-ганів дорожніх машин.
Висока твердість металу, наплавленого цими електрода-ми, виходить в результаті введення до складу покриття легуючих-чих елементів: ферохрому, ферротитана, ферробор, карбіду, бору і графіту.
Зважаючи на відсутність первинних карбідів і порівняно Неви-сокой ступеня легування аустеніту хромом і титаном метал, наплавлений електродом Т-540, знижує твердість при відпалі і допускає механічну обробку різанням. Твердість металу, наплавленого електродами Т-540, безпосередньо після на-плавки дорівнює 35-45 HRC; після відпалу при 900-950 ° вона сни-жается до 24-28 HRC, а після гарту при тій же температурі і відпустці при 200-250 ° становить 57-60 HRC. Цим електродом можна наплавляти зношені зуби шестерень.
Зазначеними електродами можна наплавляти щоки і валки камнедробілок, зуби ковшів екскаваторів і ін.
Стійкість щік камнедробілок збільшується після наплавлення електродом Т-590 в 2 рази.
Табл.27. Залізо-хромисті електроди
Сталініт - порошкоподібний сплав, який розплавляє-ся вугільним або сталевим електродом на постійному струмі при прямій полярності і наноситься на деталь шаром 3-4 мм. В якост-стве флюсу застосовується бура.
Сталініт можна замішувати на рідкому склі і у вигляді пасти наносити на поверхню деталі, розплавляючи його т.в.ч.
Через високий вміст вуглецю в наплавленні охолоджувати деталь слід повільно. Незважаючи на це, наплавленого поверх-ність має значну кількість неглибоких тріщин і пор.
Для зменшення утворення тріщин застосовують наплавку шихти сталевим електродом або замінюють порошкоподібну шихту 0,65-0,80 мм, наповнену порошкоподібної сумішшю з феромарганцю, сталініта або ін. Складів.
Внаслідок малого електричного опору трубки весь зварювальний струм практично йде по ній, і дуга збуджується між-ду трубкою і деталлю. Трубка розплавляється від безпосередньо-го дії електричної дуги, а порошкоподібна суміш всередині неї плавиться під впливом випромінюваної теплоти дуги.
Температура плавлення феромарганцю - близько 1 250 °, поет-му порошкоподібна суміш в електроді швидко розплавляється. Трубка на кінці електрода захищає плавиться порошок від окисного дії зовнішнього повітря, що забезпечує вигідне використання легуючих елементів. З порошкооб-різному суміші в наплавку переходять 80-85% марганцю, 90% вугле-роду і 90% хрому.
Інший, більш слабким захистом є електродна зовнішня обмазка товщиною 0,6-0,8 мм, яка іонізує електричні-кую дугу.
Глибокий проварена, необхідний при зварюванні, приносить шкоду при наплавленні, так як викликає зайвий витрата марганцю, хрому та інших легуючих елементів. Для досягнення міцного зв'язку наплавленого шару з деталлю досить мати глибину провару 0,1-0,2 мм, але такий малий проварена отримати важко. Зазвичай при ручному наплавленні трубчастим електродом глибина провару со-ставлять 0,7-1,0 мм.
Наплавлення литих деталей зі сталі марки 13ГЛ (щоки камнедро-Білок, бандажі валкових дробарок, била, облицювання кульових млинів) виробляють трубчастими електродами, виготовленими зі сталевої стрічки товщиною 0,8 мм і наповненими доменним феро-марганцем. Для наплавлення бив молоткових дробарок і деталей дробарок ударної дії в наповнення цих електродів рекоменду-ється додавати нікель в кількості 6-7% від ваги наповнення.
Недоліком високохромисто наплавлення є її мала ударна в'язкість (в 2-3 рази менша, ніж у марганцовистой наплавлення). Нанесення на марганцовістойсталі і чавун високо-хромової наплавлення є скрутним.
Хромомарганцовістие покриття, одержувані наплавленням трубчастими електродами, наповненими сталінітом, містять 2,5-3,0% вуглецю, 5,5-6,0% марганцю і 5,2-7,0% хрому. Та-кая наплавка трубчастими електродами має коефіцієнт зносостійкості 5,5-7,0, міцно утримується на сталі і чавуні і надає високу зносостійкість шнеків, ножів, вальців і інших деталей, які працюють на стирання без ударів або з не-великими ударами. Тому в більшості випадків хромистая наплавка може бути замінена марганцовистой або хромомар-ганцовістой.
Наплавлення трубчастими електродами з ферромарганцем. Рас-смотреніі вище електроди для отримання твердих наплавлень мають в своєму складі такі дефіцитні і дорогі склад-рами елементи як Cr, Ni, Ti, В.
Лабораторія зварювання ВНІІСтройдормаша як основ-ної легирующей складової електродів запропонувала марганець, який є дешевим матеріалом. Твердість складних (комплек-сних) карбідів заліза-марганцю в 1,5-2 рази вище твердості кварцу, який є одним з найбільш твердих абразивів, со-торкаються з робочими органами дорожніх машин. Твер-дость основи марганцовистой наплавлення також висока, а при на-Клепа (нагартовка) стає близькою до твердості кварцу. Мар-ганцовістая наплавка міцно утримується на сталі і чавуні і добре переносить удари. Ці якості марганцевистих наплавлень роблять їх найбільш придатними для захисту швидкозношуваних-трудящих деталей дорожніх машин.
В результаті численних дослідів і перевірки на виробниц-стве встановлено, що найвигіднішим складом марганцовистой наплавлення є той, в якому міститься 1,9-2,3% вуглецю і 19-23% марганцю. При цьому важливо, щоб карбіди займали не менше 20% і не більше 35% від загального обсягу наплавлення.
Крім переваг, марганцевисті наплавлення мають і недо-статок: їх коефіцієнт розширення в 2,5 рази більше, ніж у ма-лоуглеродістой стали. Тому при охолодженні в наплавленні метушні-кают тріщини, які навіть на щоках камнедробілок не щеплена-дять до відшарування наплавки і не відображаються на терміні служби дета-чи. У деяких випадках, наприклад при наплавленні смуг для лез-вий ножів, ці тріщини можна повністю усунути.
Ферохром, так само як і феромарганець, є сировиною, забезпе-чувати зносостійкі покриття. Карбіди хрому мають високу твердість - 1 570 кГУмм 2 і вище. Твердість основи хро-Місті наплавлення - 500-675 кг / мм 2; коефіцієнт ізносостойкос-ти хромистой наплавлення 6,5-6,8. Отже, ця наплавка яв-ляется навіть дещо зносостійкого, ніж марганцовистого, в тих випадках, коли при роботі деталі не відбувається наклепу, що робить її придатною для захисту деталей, що працюють без уларов.
Для відновлення щік камнедробілок застосовують трубчас-ті електроди, наповнені доменним ферромарганцем або доменним ферромарганцем з нікелем. Щоки для дроблення відомого-молодняку або інших порід малої міцності наплавляют трубчастими електродами, наповненими сталінітом.
При наплавленні щік можливо їх викривлення (ріс.74, а) в ре-док великий усадки наплавленого металу. Тому слід одночасно проводити наплавлення 3-4 щік короткими ділянки-ми, поступово переходячи від однієї щоки до іншої, щоб за це вре-мя встигав охолонути ділянку, наплавлений першим (рис. 74 б - цифри на малюнку вказують послідовність наплавлення окремих-них ділянок при одночасній наплавленні трьох щік).
Для зменшення викривлення між наплавленими ділянками ребер слід залишати незаповнені проміжки, заплавлені їх після закінчення наплавлення і повного остигання щоки, але не все підряд, а згідно з цифрами, зазначеними на. Мал. 74 б, щоб щока встигала остигати.
Щоки слід укладати для наплавлення так, щоб їх вага сприяв зменшенню викривлення (рис. 74 в). Однак навіть при дотриманні всіх перерахованих заходів предосторожнос-ти все ж відбувається деяке викривлення, для усунення якого на зворотному боці щоки наплавляют підсилюють ребра (рис. 74 г). Поверхня щік перевіряють лінійками по ребрах і по діагоналях. Товщина шару, що наплавляється па дроблять ребра за один про-хід, не повинна перевищувати 6 мм. При наплавленні кожного дотримуюся-ного шару слід ретельно видаляти шлак.
Форму наплавлених ребер перевіряють шаблоном (рис. 74 д). Ребра неправильної форми, подібно ослабленому ребру, шви-ро зношуються. Неприпустимі западини, які повинні бути обов'язково заплавлені. Необхідно особливо ретельно очі щать від шлаку місця, що підлягають наплавленні.
Унаслідок великої усадки наплавленого шару в ньому образу-ються дрібні тріщини, розташовані поперек ребер.
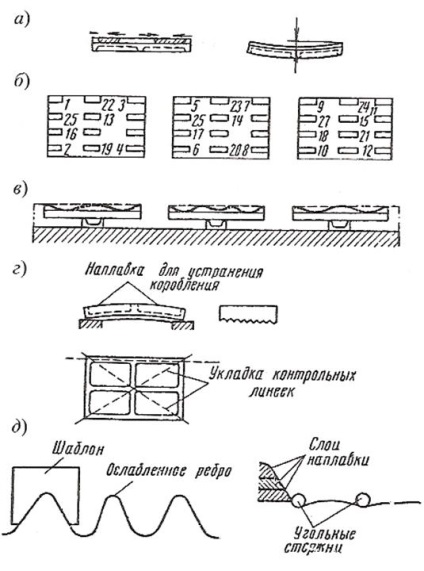
Ріс.74. Наплавлення щік камнедробілок
МЕТОДИ ПІДВИЩЕННЯ ІЗНОСТОСТОЙКОСТІ ДЕТАЛЕЙ ОБЛАДНАННЯ
Зміцнення деталей обкативаніем, розкачування і дробеструйним наклепом
Обкатування і розкочування поверхонь обертання вироб-водиться для підвищення експлуатаційних властивостей деталей і за-міни шліфування незагартована поверхонь після чистового точіння. Ця обробка сприяє поліпшенню навареними по-поверхонь.
Обкатування роликами проводиться на токарних або ре-вольверних верстатах, а розкочування - на токарних, револьвер-них і радіально-свердлильних верстатах в спеціальних приспособ-домлення (рис. 75 і76).
Величина зміни розмірів деталей при обкатуванні і рас-кативаніі залежить від металу деталі, зусилля обкатування, числа проходів, подачі, діаметра ролика і ширини циліндричного паска на ролику. При ширині паска 3 мм і діаметрі ролика 100 мм тиск на ролик в залежності від металу деталі при-ють від 50 до 200 Н при числі проходів від 2 до 4.
Після обкатування висота мікронерівностей зменшується приблизно вдвічі, тобто чистота поверхні підвищується приблизно на один клас.
Мал. 75. Пристосування для обкатування циліндричних поверхонь: а - з одним роликом; б - з трьома роликами
Мал. 76. Ролики для обкатування циліндричної поверхні
Мал. 77. Епюра розподілу напружень металу по перетину при вигині і поверхневому наклеп: 1 - наклепаного шар; 2 - напруження стиску від наклепу; 3 - напруги розтягнення по перетину при вигині; # 916; # 948; - зниження максимальних напружень розтягу
Дробоструминний наклеп застосовують для підвищення втоми-ної міцності деталей, що працюють в умовах змінних на-грузок. На відміну від обкатування цей спосіб обробки примі-ним для деталей різної конфігурації.
В результаті дрібоструминного обробки змінюються фізичні властивості поверхневого шару металу. Для м'яких металів твер-дість підвищується на 20-40%, сприятливіші розподіляються на-напруги в перетині деталі, в результаті чого підвищується втомлено-стная міцність. Епюра розподілу напруги металу по се-ню при вигині і поверхневому наклеп показана на рис. 77.
При обробці сталевих деталей застосовують чавунну і, рідше, сталеву дріб. Розмір дробу повинен бути 0,4x2 мм. Мел-кая дріб застосовується для обробки дрібних деталей, велика - для великих. Глибина наклепу не перевищує 1 мм.
Дробоструминний наклеп деталей виробляють на пневматичних або механічних дробемет. У пневматичних дробемет дріб через форсунку викидається під тиском до 50-60 Н / см 2. У механічних дробемет дріб викидається обертовим з великою швидкістю ротором.
Дробоструминний наклеп застосовують для підвищення втомної міцності ресорних листів, пружин, осей, черв'яків і інших де-талей, які працюють у важких умовах при змінному навантаженні.