Принцип дзидока - зупинити процес заради вбудовування якості
Якщо мова йде про обладнання, ми оснащуємо його пристроями, які виявляють відхилення і зупиняють верстат автоматично. Що стосується людей, їм дано право натиснути на кнопку або смикнути шнур - такі шнури називаються «шнури Андон» - і зупинити складальну лінію. Будь-член команди може зупинити лінію, якщо він помітив відхилення від стандарту. Таким чином, ми покладаємо на членів команди відповідальність за якість. Вони відчувають цю відповідальність і цінують надані їм повноваження. Вони розуміють, що їм довіряють.
Дзидока називають також автономізацією - наділенням обладнання людським інтелектом. Верстат зупиняється, якщо виникає проблема. Набагато ефективніше і дешевше забезпечити якість на місці (не допустити передачу проблеми далі по потоку), ніж займатися перевіркою якості і виправленням дефектів постфактум.
При ощадливому виробництві особливо важливо проводити якісні вироби відразу. Оскільки рівень запасів дуже низький, при проблемах з якістю ви не можете розраховувати на буферний запас. Проблема при виконанні операції А швидко призведе до припинення робіт на операції Б. Коли обладнання зупиняється, прапорці або світлова індикація, супроводжувана музикою або звуковим сигналом тривоги, сповіщає про те, що потрібна допомога. Така сигнальна система називається Андон. Слово «Андон» означає світловий сигнал, що кличе на допомогу.
Хоча ні у кого не викликає сумнівів, що проблеми якості потрібно виявляти і вирішувати якомога швидше, при традиційному масовому виробництві менеджерам і в голову не приходить зупиняти виробництво. Якщо вдається помітити неякісні деталі, їх позначають і відкладають в сторону, щоб, коли буде надана можливість, зайнятися їх виправленням. Такими виправленнями займається вже іншу ділянку. Девіз масового виробництва: «Будь-якою ціною виробляти якомога більше, а проблеми виправимо потім». Президент заводу Toyota в Джорджтауні Гері Конвис сказав мені:
Коли я працював в компанії Ford, того, хто не забезпечував під час своєї зміни 100% вироблення, викликали «на килим». Лінію не зупиняли ніколи. Тут ми не працюємо 100% запланованого часу. Мені здається, сильна сторона Toyota в тому, що вище керівництво розуміє значення системи Андон ... Вони вистраждали цю систему, і вони підтримують її. За роки, які я пропрацював в Toyota, мене жодного разу не дорікнули за те, що, зупинивши виробництво заради безпеки і якості, ми втратили в обсягах випуску продукції. Керівництво цікавило тільки одне - дозволило це виявити першопричини проблеми і чи потрібна нам допомога. Тим, хто працює у нас, я кажу: неприємності чекають вас в двох випадках - перший, якщо ви не з'явитеся на роботу, і другий, якщо, виявивши проблему, ви не смикне за шнур. Для забезпечення якості надзвичайно важливе почуття відповідальності.
Тут ми стикаємося з парадоксом. Керівництво Toyota не вимагає, щоб 100% часу робота велася без зупинки, навіть коли складальна лінія може працювати весь день, але при цьому по продуктивності підприємства Toyota постійно випереджають інші автомобільні компанії. Чому? Тому що в Toyota давно засвоїли: виявлення першоджерела проблем з якістю економить час і гроші. Невпинно виявляючи і вирішуючи проблеми, ви усунете втрати, досягнете значного зростання продуктивності і оберне на порох конкурентів, які змушують складальні лінії працювати на знос і накопичують проблеми.
Коли конкуренти Toyota, в кінці кінців, стали використовувати систему Андон. вони помилково вважали, що, якщо кожне робоче місце оснащене системою зупинки всієї лінії, варто натиснути кнопку - тут же зі скреготом і скрипом встане вся складальна лінія. Однак Андон. який використовується на всіх заводах Toyota по збірці автомобілів і виробництва двигунів, називають також «системою зупинки ділянки лінії». На рис. 11.1 показано, що, коли оператор на робочій позиції 5 натискає кнопку Андон. загоряється жовтий світловий сигнал, але лінія продовжує рух. Лідер команди повинен відреагувати на цей сигнал, перш ніж автомобіль досягне наступного робочого позиції. Якщо він цього не зробить, загориться червоний світловий сигнал і ділянку складальної лінії зупиниться автоматично. На складальних лініях, з яких сходить одна машина в хвилину, у лідера команди є 15-30 секунд. Протягом цього часу він може швидко вирішити проблему або виявити, що її можна вирішити, не зупиняючи лінію і не перешкоджаючи переміщенню автомобіля на наступну робочу позицію. Якщо ні те ні інше неможливо, лідер команди зупиняє лінію. Велика увага приділяється підготовці лідерів команд, які повинні освоїти стандартні процедури, передбачені сигнальною системою Андон.
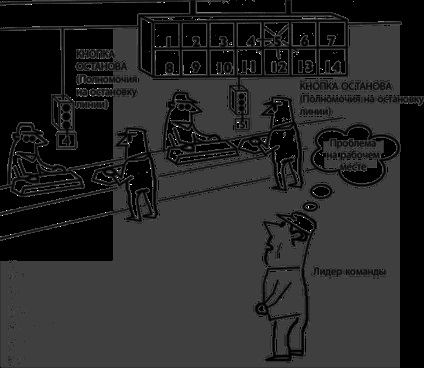
Мал. 11.1. Система Андон на лінії ручної збірки
Складальна лінія ділиться на ділянки з невеликим «буферним запасом» автомобілів між ними (зазвичай від 7 до 10 машин). Такі буфери в разі зупинки ділянки дозволяють наступної ділянки продовжувати працювати протягом 7-10 хвилин, перш ніж він теж буде зупинений, і т. Д. Зупиняти весь завод доводиться рідко. Виходить, що Андон вирішує поставлені перед ним завдання, не ставлячи без необхідності під загрозу виробництво в цілому. Автомобільним компаніям США знадобилися роки, щоб зрозуміти, як застосовувати цей інструмент TPS. Часто робітники і лідери команд не наважувалися зупинити лінію лише тому, що мова дійсно йшла про зупинку всієї лінії!
Вбудовування якості завдяки дзидока було особливо важливо для Toyota при виробництві Lexus, адже власники цієї машини пред'являють до неї надзвичайно високі вимоги. До недавнього часу автомобілі Lexus вироблялися тільки в Японії, де рівень виробничої культури і якості є незаперечним. Потім постало питання: чи можна збирати Lexus в Північній Америці і при цьому дотримати найвищі вимоги до якості, які пред'являє споживач? Відповідь була позитивною, і виробництвом Lexus став займатися завод Toyota в Кембриджі, провінція Онтаріо, Канада. У числі інновацій, які сприяють досягненню досконалості, - ряд технологій і процесів, що дозволяють підняти Андон на новий рівень.
Поділіться на сторінці