Металознавство називається наука, що встановлює зв'язок між складом, структурою і властивостями металів і сплавів і вивчає закономірності їх зміни при теплових, хімічних, механічних, електромагнітних і радіоактивних впливах.
Всі метали і сплави прийнято ділити на дві групи.
Залізо і сплави на його основі (сталь, чавун) називають чорними металами, а решта металів (Be, Mg, Al, Ti, V, Cr, Mn, Co, Ni, Cu, Zn, Zr, Nb, Mo, Ag, Sn , W, Au, Hg, Pbі ін.) і їх сплави - кольоровими.
Сучасне машинобудування характеризують безперервно зростаюча енергонапряженності, а також важкі умови експлуатації машин. Такі умови роботи машин пред'являють до матеріалів особливі вимоги. Для задоволення цих вимог створено багато сплавів на основі різних металів.
У сучасній техніці широко застосовують стали, що забезпечують високу конструктивну міцність, і сплави, які залишаються міцними при високих температурах, в'язкими при температурах, близьких до абсолютного нуля, що володіють високу корозійну стійкість в агресивних середовищах або іншими фізико-хімічними властивостями.
Число нових сплавів безперервно зростає.
У спеціальному машинобудуванні все ширше застосовують так звані композиційні матеріали, сплави з пам'яттю форми і т.д.
За останні роки досягнення матеріалознавства забезпечили небувалий прогрес в розробці конструкційних і інструментальних матеріалів в різних областях техніки. Дослідження реальної структури твердих тіл показали принципову можливість отримання сплавів з міцністю, що наближається до теоретичної, яка визначається міцністю міжатомних зв'язків.
У курсової роботі призначена марка матеріалу для виготовлення-сталь 15Х2НГТА.Ето означає, що в стали міститься 0,15% вуглецю, 2% хрому, 1% нікелю, 1% марганцю, 1% титану, сталь високоякісна, тобто в ній міститься Зменшення кількість домішок фосфору і сірки.
Наявність хрому підвищує міцність, корозійну стійкість, прокаліваемость (при цьому пластичність і в'язкість падають).
У хромистих сталях більшою мірою розвивається проміжне перетворення і при загартуванню з охолодженням в маслі, виконуваної після цементації, серцевина вироби має бейнітне будова. Внаслідок цього хромисті сталі в порівнянні з вуглецевими володіють більш високими властивостями міцності при дещо меншою пластичності в серцевині
Нікель знаходиться тільки в твердому розчині і підвищує корозійні властивості сталей, а також міцність і в'язкість.
Марганець і нікель є аустенізаторамі, тобто розчиняючись в залозі, розширює область аустеніту.
Метод зміцнення (термообробки): цементація (газова).
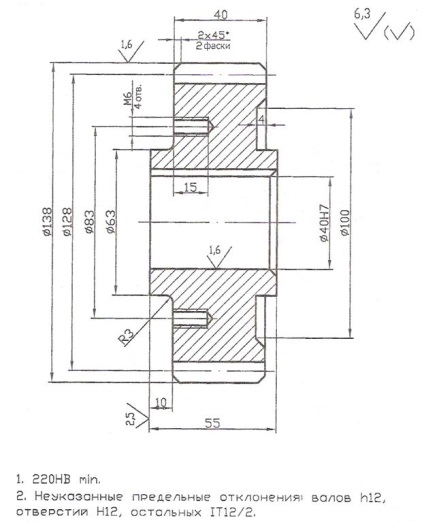
Як спосіб термічної обробки зубів приймаємо газову цементацію з наступним загартуванням і низьким відпусткою.
Цементацією називається процес насичення поверхневого шару стали вуглецем. Розрізняють два основних види цементації: твердими Углеродосодержащий сумішами (карбюризаторами) і газову. Метою цементації є отримання твердої і зносостійкого поверхні, що досягається збагаченням поверхневого шару вуглецем до концентрації 0,8 ÷ 1,2% і подальшим гартом з низьким відпусткою. Цементація і подальша термічна обробка одночасно підвищують і межа витривалості.
Для цементації деталі надходять після механічної обробки нерідко з припуском на шліфування 0,05 ÷ 0,10 мм. У багатьох випадках цементації піддається лише частина деталі; тоді ділянки, які не підлягають зміцнення, захищають тонким шаром міді (0,02 ÷ 0,04 мм), яку наносять електролітичним способом або ізолюють спеціальними обмазками, що складаються з суміші вогнетривкої глини, піску і азбесту, замішаних на рідкому склі, і ін.
Цементацію проводять при температурах 920 ÷ 950 ° С, коли стійкий аустенит, що розчиняє в великих кількостях вуглець. При цементації стали атоми вуглецю дифундують в грати # 947; -заліза. Після досягнення межі насичення аустеніту вуглецем, що визначається лінією SE на діаграмі Fe-Fe3 C, на поверхні може утворитися суцільний шар цементиту.
В реальних умовах цементації освіту на поверхні шару цементиту спостерігається вкрай рідко. Зазвичай при температурі цементації 920 ÷ 950 ° С дифузний шар складається тільки з аустеніту, а після повільного охолодження - з продуктів його розпаду - фериту і цементиту.
Цементовий шар має змінну концентрацію вуглецю по глибині, спадної від поверхні до серцевини деталі. У зв'язку з цим після повільного охолодження в структурі цементованного шару можна розрізнити (від поверхні до серцевини) три зони: заевтектоідних, що складається з перліту і вторинного цементиту і утворить сітку по колишньому зерну аустеніту; евтектоїдних, що складається з одного пластинчастого перліту, і доевтектоїдної зону, що складається з перліту і фериту. Кількість фериту в цій зоні безперервно зростає в міру наближення до серцевини.
За технічну (ефективну) товщину цементованного шару зазвичай приймають суму заевтектоідной, евтектоїдной і половини перехідною (доевтектоїдної) зон або глибину до твердості HRC50 або HV500 ÷ 600 після гарту.
Досвід показує, що товщина цементованного шару для деталей, виготовлених зі сталі з ≤ 0,17% С, становить 15% від найменшої товщини або діаметра цементуемие перетину. При утриманні в стали> 0,17% С товщину шару зменшують до 5 ÷ 9%, а для виробів, що працюють на знос, що не випробовують великих питомих навантажень, до 3 ÷ 4% від найменшої товщини або діаметра цементуемие перетину. Найчастіше товщина шару 0,5 ÷ 2,0 мм.
2.2 Характеристика газової цементації
Під цементацією прийнято розуміти процес високотемпературного насичення поверхневого шару стали вуглецем. Так як вуглець в # 945; -фазі практично не розчиняється, то процес цементації здійснюється в інтервалі температур 930-950 ° С - т. Е. Вище # 945; → # 947; -перетворення. Структура поверхневого шару цементованного вироби являє собою структуру заевтектоідной стали (перліт і цементит вторинний), тому для додання стали остаточних - експлуатаційних - властивостей після процесу цементації необхідно виконати режим термічної обробки, що складається в загартуванні і низькому відпустці; температурно-часові параметри режиму термічної обробки призначаються в залежності від хімічного складу стали, відповідальності, призначення і геометричних розмірів цементованного вироби. Зазвичай застосовується гарт з температури цементації безпосередньо після завершення процесу хіміко-термічної обробки або після подстуживания до 800-850 ° С і повторного нагріву вище точки АС3 центральної (нецементованной) частини виробу. Після гарту слід відпустку при температурах 160-180 ° С.
Цементація проводиться в углероднасищенних твердих, рідких або газоподібних середовищах, званих карбюризаторами, основні склади яких наведено в табл. 1, а в табл. 2 і 3 дані рекомендації по режимам термічної обробки цементованних виробів.
При твердофазной цементації процес ведуть у такий спосіб. Цементуемие деталі упаковуються в цементаційні ящики таким чином, щоб їх обсяг, в залежності від складності конструкції деталі, займав від 15 до 30% обсягу цементаційна ящика. Ящики завантажують в піч, нагріту до температур від 600-700 ° С і нагрівають до температури цементації - 930-950 ° С. Після закінчення процесу цементації ящики виймаються з печі - охолодження деталей ведеться всередині цементаційних ящиків на повітрі. До числа недоліків цементації в твердих карбюризаторів відносяться: неможливість регулювання ступеня насичення і неможливість проведення загартування безпосередньо після цементації, додатковий непродуктивний витрата енергії на прогрів цементаційних ящиків і т. П. Однак простота методу, можливість проводити процес на стандартному пічному обладнанні без установки додаткових пристроїв роблять цей метод досить поширеним в умовах дрібносерійного виробництва в ремонтних цехах і на ділянках великих підприємств.
Остаточні властивості цементованних виробів досягаються в результаті термічної обробки, виконуваної після цементації. Цією обробкою можна виправити структуру і подрібнити зерно серцевини і цементованного шару, неминуче збільшуються під час тривалої витримки при високій температурі цементації, отримати високу твердість в цементованном шарі і хороші механічні властивості серцевини; усунути карбідну сітку в цементованном шарі, яка може виникнути при насиченні його вуглецем до заевтектоідной концентрації.
2.3.1 Характеристика загартування
Загартування полягає в нагріванні стали на 30 ÷ 50 ° С вище АС3 для доевтектоїдних сталей або АС1 для заевтектоідних сталей, витримці для завершення фазових перетворень і подальшому охолодженні зі швидкістю вище критичної. Для вуглецевих сталей це охолодження проводять частіше в воді, а для легованих - в маслі або в інших середовищах. Загартування не є остаточною операцією термічної обробки. Щоб зменшити крихкість і напруги, викликані гартом, і отримати необхідні механічні властивості, сталь після гарту обов'язково піддають відпустці.
Інструментальну сталь в основному піддають гарту і відпустки для підвищення твердості, зносостійкості і міцності, а конструкційну сталь - для підвищення міцності, твердості, отримання досить високої пластичності і в'язкості; для ряду деталей також і високої зносостійкості.
У більшості випадків після цементації застосовують загартування вище точки АС1 (серцевини) при 820 ÷ 850 ° С.
Після газової цементації застосовують загартування без повторного нагріву, а безпосередньо з цементаціонной печі після подстуживания виробів до 840 ÷ 860 ° С. Така обробка не виправляє структури цементованного шару і серцевини. Тому безпосередню загартування застосовують тільки в разі, коли вироби виготовлені з спадково дрібнозернистої сталі. Для зменшення деформації цементованних виробів виконують також ступінчасту загартування в гарячому маслі 160 ÷ 180 ° С.
Іноді термічна обробка складається з подвійної гарту і відпустки. Першу загартування (або нормалізацію) з нагріванням до 880 ÷ 900 ° С призначають для виправлення структури серцевини. Крім того, при нагріванні в поверхневому шарі в аустените розчиняється цементітная сітка, яка при швидкому охолодженні знову не утвориться. Другу загартування проводять з нагріванням до 760 ÷ 780 ° С для усунення перегріву цементованного шару і надання йому високої твердості. Недолік такої термічної обробки полягає в складності технологічного процесу, підвищеному викривленні, що виникає у виробах складної форми, і можливості окислення і зневуглецювання.
Відпустка полягає в нагріванні загартованої сталі до температури нижче АС1. витримці при заданій температурі і наступному охолодженні з певною швидкістю. Відпустка є остаточною операцією термічної обробки, в результаті якого сталь отримує необхідні механічні властивості. Крім того, відпустку повністю або частково усуває внутрішні напруги, що виникають при загартуванню. Ці напруги знімаються тим повніше, чим вище температура відпустки.
Найбільш інтенсивно напруги знижуються в результаті витримки при 550 ° С протягом 15 ÷ 30 хв. Після витримки протягом 1,5 год напруги знижуються до мінімальної величини, яка може бути досягнута відпусткою при даній температурі.
Швидкість охолодження після відпустки також дуже впливає на величину залишкових напруг. Чим повільніше охолодження, тим менше залишкові напруги. Швидке охолодження в воді від 600 ° С створює нові теплові напруги. Охолодження після відпустки на повітрі дає напруги на поверхні в 7 разів менше, а охолодження в маслі в 2,5 рази менше в порівнянні з напруженнями при охолодженні у воді. З цієї причини вироби складної форми, щоб уникнути їх викривлення після відпустки при високих температурах слід охолоджувати повільно, а вироби з легованих сталей, схильних до оборотної відпускної крихкості, після відпустки при 500 ÷ 650 ° С у всіх випадках слід охолоджувати швидко.
Низькому відпуску піддають тому різальний і вимірювальний інструмент з вуглецевих і низьколегованих сталей, а також деталі, які зазнали поверхневу загартування, цементацию, ціанування або нітроцементації. Тривалість відпустки зазвичай 1 ÷ 2,5 ч, а для виробів великих перерізів і вимірювальних інструментів призначають більш тривалу відпустку.
Твердість поверхневого шару для вуглецевої сталі складає HRC60 ÷ 64; а для легованої HRC58 ÷ 61; зниження твердості пояснюється утворенням підвищеної кількості залишкового аустеніту.
Цементація з наступною термічною обробкою підвищує межу витривалості сталевих виробів і різко знижує чутливість до концентраторів напружень за умови безперервної протяжності зміцненого шару по всій поверхні деталі. Додатково межа витривалості цементованних виробів може бути підвищений дробеструйним наклепом.
2.4 Технологічний процес термічної обробки зубів
Перед початком термічної обробки ділянки, які не підлягають зміцнення, ізолюємо спеціальної обмазкою, що складається з суміші вогнетривкої глини, піску і азбесту, замішаних на рідкому склі.
Цементацію проводимо в твердому карбюризаторі з використанням печі Ц - 105А або СШЦ. Вироби, що піддаються цементації в твердому карбюризаторі, поміщають в вогнетривкий ящик і засипають цементаціонной сумішшю, що складається з активованого вугілля і вуглекислої солі (К2СО3, Na2CO3 або ВаСОз). Ящик ставлять в піч і витримують при 900. 950 ° С протягом 5 G ч. При цьому вуглекисла сіль дисоціює з виділенням СО який реагує з розпеченим вугіллям і утворює оксид вуглецю (L + CO = CO). При зіткненні з поверхнею стали оксид вуглецю розкладається (2СО -) - СО2 + С) і вуглець в атомарному-активному стані дифундує в кристалічну решітку y: Fe, утворюючи твердий розчин (аустеніт). При подальшій витримці в печі виріб науглероживается на деяку глибину (1. 2 мм).
Потім виробляємо перевірку твердості методом Роквелла за шкалою С. Вона повинна бути дорівнює HRC60 ÷ 65.
3 Лахтин Ю.М. Металознавство і термічна обробка металів. - 2-е вид. перераб. і доп. - М. Металургія, 1979.
5 «Матеріалознавство» Москва «Машинобудування», 1986р