Основними дефектами поршневих пальців є знос робочої поверхні, тріщини, ризики, задираки, викришування цементованої поверхні, ослаблення в місцях посадки (в бобишках поршня). Якщо знос не перевищує норми, палець відновлюють до номінальних розмірів; для цього його хромують, шліфують і полірують. При зносі вище граничного, а також при наявності тріщин або викришування робочої поверхні пальці замінюють новими. Не допускається наявність рисок і забоїн на зовнішніх поверхнях пальців.
Основні дефекти поперечок крейцкопфів - еліптичність і конусність цапф, подряпини, задираки, тріщини в цапфах і вигин. Нерівномірний знос цапф у вигляді еліптичності і конусності, подряпини і задираки усувають проточкою і шліфуванням, а також ручний обпиловкою за калібром. Якщо проточка неприпустима за умовами міцності, цапфи наплавляють електрозварюванням і протачивают. При наявності тріщин і зламів поперечки замінюють новими. Дефекти плазунів, залитих бабітом, у вигляді зносу, відставання і викришування бабіту на робочих поверхнях усувають перезаливка. Після цього повзуни збирають з крейцкопф, і робочі поверхні плазунів обробляють за розміром від осі циліндра до паралелі. Робочі поверхні плазунів шабрують.
Основні дефекти шатунів тронкового двигуна - вигин і скручування стержня шатуна, а також знос втулки під палець. При наявності вигину шатуни правлять на пресі з нагріванням. Скручування усувають шляхом деформації в бік, протилежний скручування. Шатуни, що мають тріщини, замінюють новими. Втулку під поршневий палець замінюють новою.
Обрив шатунних болтів призводить до найбільш серйозних аварій двигуна. Обов'язковій заміні підлягають шатунні болти, що мають такі дефекти: залишкову деформацію (витяжку), пошкодження різьби болта або гайки; забоіни або надриви болта, місцеві Надир, тріщини, скручування, ослаблення посадки гайки на різьбі. Навіть при відсутності вищевказаних дефектів шатунні болти підлягають огляду в терміни, передбачені інструкцією по експлуатації. Для чотиритактних дизелів, крім того, встановлено граничну кількість годин роботи шатунних болтів, після закінчення якого необхідна заміна болтів незалежно від їх стану.
Поршневі штоки при наявності зносу, подряпин і задирів протачивают і шліфують. У разі вигину шток правлять з нагріванням. Викривлення фланця штока (якщо конструкцією передбачено таке з'єднання) усувають проточкою; при наявності тріщин штоки замінюють новими.
У паливних насосів високого тиску дизелів найбільшому зносу і пошкоджень схильні плунжерні пара, всмоктувальні і нагнітальні клапани, а також приводи в вузлах зчленування.
Ремонт паливної апаратури проводиться на спеціальній дільниці дизельного цеху або на спеціалізованому підприємстві. Ремонт плунжерних пар паливних насосів полягає в промиванні і дефектації деталей, механічній обробці плунжеров і втулок, хромуванні плунжеров, обробці після хромування, підборі і взаємної притирання деталей, перевірки щільності пар. Незначні дефекти (ризики, Надір, заїдання) усувають шляхом зачистки, ходіння і притирання. При наявності значних пошкоджень замінюють окремі деталі або цілі комплекти. Притирання плунжеров виробляють на спеціальній доводочной бабці (рис. 112) або на токарному верстаті. Плунжер 3 сухарями 2 затискають в цанзі 1 бабки. Поверхня, що підлягає обробці, покривають шаром притирочное пасти і притирають плунжер розрізним чавунним притиром 5, встановленим в розрізну оправлення 4. Регулюють оправлення таким чином, щоб притир не хитався при переміщенні уздовж плунжера. У міру притирання плунжера поступово підтискають стягнутий болт притиру.
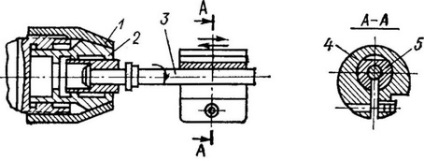
Мал. 112. Пристосування для доведення плунжеров.
Механічну обробку робочої поверхні втулки плунжера виробляють на спеціальному пристосуванні трикулачні головкою 2 (рис. 113), яка погойдується в цапфах 1, розташованих в підшипниках корпусу 3. Втулку 9, що підлягає обробці, встановлюють в направляючої голівці втулки 4, яка по зовнішній поверхні і заплічок може переміщатися в осьовому напрямку на 0,5-2,0 мм завдяки зазору між торцем і притримує планкою 5. Розрізний чавунний притир 8 встановлюють на конічну оправлення 7, яку через шарнір 6 кріплять до шп Заксправ верстата.
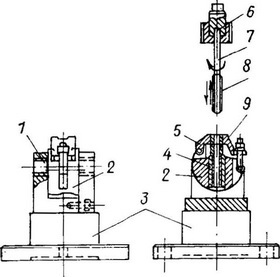
Мал. 113. Пристосування для обробки робочої поверхні плунжерній втулки.
Взаємну пригін плунжера і втулок здійснюють притиранням. Доведення вважають закінченою, якщо плунжер, висунутий з втулки на 40-50 мм, у вертикальному положенні під дією своєї маси плавно опускається до упору в торець втулки. Після цього перевіряють щільність плунжерних пар шляхом опресування сумішшю машинного масла з дизельним паливом пробним тиском при температурі 18-20 ° С (291 - 293 К). Герметичність плунжерній пари вважається задовільною, якщо витік не перевищує 60-70 г / хв.
Ремонт клапанних пар паливних насосів полягає у відновленні конусних поверхонь сідел і клапанів. Нерівномірний знос, ризики, задираки і інші дефекти на цих поверхнях усувають притиранням, користуючись спеціальним пристосуванням. Після ремонту клапанні пари відчувають на щільність. Після ремонту деталей і збірки паливний насос піддають стендовим випробувань.
Ремонт деталей форсунок зазвичай полягає в переукомплектовке прецизійних пар і доводочних операціях. Після цього форсунки оглядають, притиральні поверхні придатних деталей шліфують, деталі проміряють і сортують за розмірами. Розпилювачі підбирають по голок і по корпусу. Невеликі задираки або подряпини на поверхні голки форсунки акуратно виводять притирочное пастою. Пригін посадочних конусів і власника голки здійснюють притиранням із застосуванням тонких притиральних матеріалів і остаточно - чистим маслом. Закінчивши збірку, форсунки піддають стендовим випробувань.
Основним дефектом клапанів механізму газорозподілу є нещільності між тарілкою і гніздом клапана через обгорання, подряпин, забоїн і тріщин. Нещільності усувають шляхом проточки, шліфування та подальшої притирання клапана по гнізду. Операція притирання клапанів полягає в тому, що на притираються поверхню гнізда клапана наносять шар абразивної пасти і тарілці клапана надають зворотно-обертальний рух. Операція притирання вважається закінченою, коли притираються поверхні отримають рівномірний матовий відтінок. Якість притирання перевіряють по олівцевим ризиків: на притерту поверхню тарілки клапана наносять олівцем чотири - шість радіальних рисок і повертають тарілку клапана щодо гнізда приблизно на чверть обороту. Якщо слідів олівцевих рисок не залишається, якість притирання вважається задовільним. Найефективніший спосіб перевірки якості притирання - керосиново-крейдяний проба.
При притирання клапанів застосовують звичайні ручні дрилі або спеціальні пристосування і верстати з механічним приводом.