Різка нержавіючої стала широко застосовуватися у виробництві - без неї неможливе створення жодної металевої деталі.
Існує кілька способів різання металу, однак, на якому б верстаті не провадилась робота, головною умовою є якість - різання повинна бути виконана чітко по заданих параметрах і не деформувати матеріал під час роботи.
У статті ми розберемо основні способи, як обробляти сплави металу шляхом різання, і докладно опишемо процес, як це відбувається.
Токарний спосіб обробки
Токарська різання стали включає кілька кроків по обробці, мета яких - зробити виріб потрібної форми і розміру, щоб воно відповідало кресленнями.
Вся робота з різання в цьому випадку здійснюється на токарному верстаті. Спосіб обробки матеріалу на токарному верстаті досить простий: він полягає в проникненні в оброблювану деталь, наприклад, труб, гострих ножів, здатних розкроїти її на частини потрібного розміру.
Токарська різання може здійснюватися цілим рядом інструментів: розгорненнями і свердлами, різцями і плашками, зенкерами, фасонними інструментами і т.д.
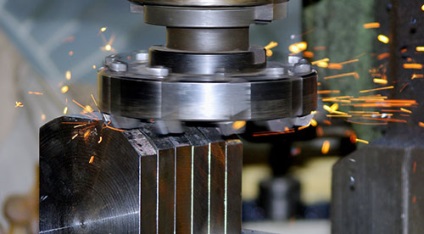
Самий же популярний інструмент, який використовують для різання - токарний різець. З його допомогою здійснюється механічна чорнова і напівчистова обробка деталі з нержавіючої сталі, а також, в деяких випадках, тонка обробка кульками.
Токарний різець використовується при створенні деталей зі сталі, а також різьблення на інших деталях, до складу яких входять сплави зі сталі, наприклад, труб.
Тверді різці на токарному верстаті мають різні призначення, і, виходячи з цього, діляться на 7 класифікацій.
Перший тип різців призначений для обробки циліндричних поверхонь, вони бувають відігнутими або прямими.
Другий тип потрібен для обробки торцевих деталей з нержавіючої сталі, щоб зробити в деталі отвір, використовують розточувальні різці, а для створення зовнішньої і внутрішньої різьби на об'єкті необхідні різьбонарізні різці.
Для того щоб обробляти на токарному верстаті тверді деталі з нержавіючої сталі, будуть потрібні фасонні різці.
Останній тип різців - інструменти контурного точіння. Вони також підходять для роботи на різних типах верстатів.
Різці на токарному верстаті можуть бути як чистовими, так і чорновими, а також тонкими. Стосовно деталі вони можуть бути встановлені радіально або тангенціально і працювати від подачі руху зліва, або справа.
Тверді різці можуть мати пряму, вигнуту, відігнуту або відтягнуту головку. За типом поперечного перерізу різці бувають прямокутними, кульками, або квадратними.
За типом виробництва зустрічаються різці збірних або цільних типів, а також ті, в основі яких лежать сплави стали, кераміки та інших елементів.
Сплави нержавіючої сталі, наприклад, деталі гофрованих труб, токарної різкою або автогеном обробляють рідко, оскільки існує більш ефективне обладнання для цього процесу.
З його допомогою можна знизити витрати на різання, а також значно прискорити цей процес і зробити його більш якісним.
різка плазмою
Плазмова різка - одна з найбільш затребуваних на сьогоднішній день, оскільки вона повністю механічна і забезпечує швидку і чітку роботу в повній відповідності необхідним кресленнями.
Особливості цього процесу в тому, що плазмова різка обробляє деталь труб або інших виробів з нержавійки з допомогою теплоти, яка стискається плазмовою дугою на верстаті.
Після розрізання деталі, струмінь плазми ефективно видаляє ОПЛАН, а також зайві елементи із зони роботи.
Сама плазма складається з іонізованого газу, що знаходиться під високою температурою. Він є хорошим провідником електрики, і тому здатний розрізати навіть складну в роботі нержавіючу сталь.
Плазмова дуга створюється за допомогою стислої звичайної дуги, до складу якої після нагрівання додається плазмообразующий газ.
Для плазмового різання нержавійки використовується ряд з'єднань: повітря з азотом, чистий азот, азотоводородной і аргоно-водневі суміші - все це необхідно, щоб створити якісну плазму, здатну розрізати металеві сплави.
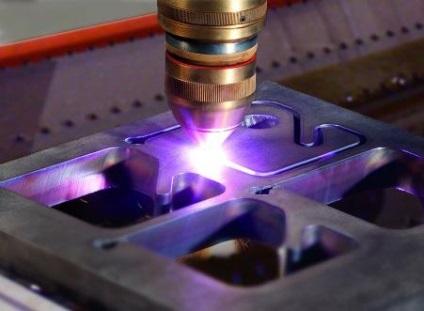
Існує також режим повітряно-плазмового різання кульками, при якому робота верстата виглядає так само, як при різанні стали низьколегованого або низкоуглеродистого типу.
Щоб поверхні зрізу деталі мали мінімум шорсткості, при роботі використовують вплив азотно-водневої суміші, або різання в повітряному середовищі.
Чим вище температура плазми при роботі, тим більш якісною буде різка металевої поверхні труб. Це відбувається через те, що, відчуваючи вплив високої температури, вода, що накопичується в каналах сопла, випаровується швидше, а потім дисоціюють.
Завдяки цьому вплив плазмової дуги стає щільніше, і енергії на деталь надходить більше, а також поліпшується якість видалення шлаків і інших елементів, що виникають в ході обробки труб і інших деталей з нержавіючої сталі.
Середу азоту, азотоводородной або аргоно-водневу суміш використовують рідше, тому що якість обробки в ній нижче.
Тверді сплави обробляють таким чином тільки в тому випадку, якщо при роботі на них впливають високі температури, або робота проходить в агресивному середовищі.
Плазмова різка має ряд переваг перед обробкою газом, тому в більшості випадків для замовника буде вигідно вибрати саме її.
Плазмова обробка стали відрізняється безпекою, мінімальною кількістю викидів, що забруднюють атмосферу, а також швидкістю і високою якістю роботи.
За рахунок того, що різка плазмою відбувається дуже швидко, для замовника це обійдеться дешевше. Крім того, за допомогою плазмового різання можна робити деталі з нержавіючої сталі будь-яких форм, розмірів і складності.
Після плазмового різання додаткова обробка кромок часто не потрібно, оскільки місця розрізу виходять рівними і не мають вад.
Деталі, створені за допомогою плазмового різання, готові для зварювання. При цьому працювати можна не тільки з металевими, а й зі скляними поверхнями.
Для зварювання після різання також можна використовувати плазмовий спосіб, оскільки, процес зварювання за допомогою електродів, хоча і буде простіше, але не зможе створити якісного з'єднання швів, через що конструкція буде недовговічною.
Найчастіше для зварювання нержавійки використовують середу захисних газів - у неї є свої особливості, і при такому способі якість зварювання деталей буде набагато вище.
різка лазером
Лазерне різання нержавійки, так само, як і плазмова - сучасний і вигідний спосіб обробки деталей.
Для різання поверхні з нержавіючої сталі страж-лазером потрібен спеціальний верстат - лазерна установка, здатна створювати і задавати напрямок лазерному променю, який при цьому типі різання виступає як різак.
Лазерне різання - повністю механічна, що значно знижує витрати на її використання. Тому, обробка деталей цим способом вигідна як замовникам, так і тим, хто здійснює роботу.
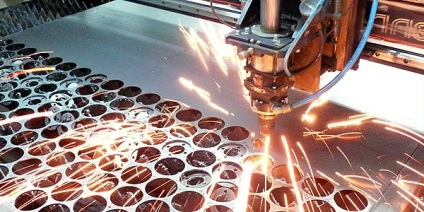
Лазерне різання нержавіючої сталі працює точно за кресленнями, тому можливість невідповідності заданих форм і розмірів кінцевої деталі практично відсутня.
Лазерне різання поверхні проводиться дуже швидко, за рахунок чого можна обробляти велику кількість деталей в короткий термін.
Завдяки тому, що різка поверхні проводиться під впливом високої температури, цей процес дуже швидкий, тому тверді сплави, але вони не попадають в зону різання, залишаються недоторканими, і якість оброблюваної деталі, а також шва, залишається високим.
Лазер, яким обробляється деталь нержавійки, має три важливих вузла, які забезпечують його роботу.
Перший вузол - джерело енергії, який забезпечує роботу, другий - робоче тіло, яке створює випромінювання і третій - оптичний резонатор, який посилює роботу тіла і направляє його в потрібному напрямку, а також дозволяє регулювати силу впливу страж-лазера на робочі поверхні деталі.
Існує два типи лазерів, які широко використовуються у виробництві.
Перший тип - твердотільний страж-лазер, а другий - газовий. Газовий лазер має щілинну, або поперечну прокачування газу, також зустрічається третій тип - газодинамический.
Лазерне різання може обробляти поверхні з будь-якого контуру, найголовніше - правильно задати параметри для роботи.
Оскільки різка поверхні відбувається за допомогою лазера, а не шляхом механічного впливу, деформування листа стали, а також кромки розрізу не відбувається.
За допомогою лазерного різання можна обробляти поверхні будь-якого розміру, і вирізати як зовсім маленькі, так і великі виробничі деталі.
Найменший діаметр отвору, який можна зробити за допомогою лазерного різання - 0.5 мм. При обробці легко можна змінювати потужність випромінювання, роблячи її більше або менше в залежності від необхідності - це значно полегшує роботу з інструментом.
Дуже часто шляхом лазерної та плазмової різки вирізують деталі для гофрованих труб різного розміру. Після цього шляхом зварювання деталі гофрованих труб з'єднують, і вони готові до випуску та встановлення.
Крім того, лазерна різка дозволяє обробляти найрізноманітніші тверді поверхні і сплави металів, також працювати зі скляними виробами.
Якість роботи лазерної установки зі скляними поверхнями, як правило, значно вище, ніж якщо користуватися автогеном, склорізом і іншим більш простим устаткуванням.
Після різання лазером додаткова обробка деталей зазвичай не потрібно, тому можна відразу передавати деталі до місця зварювання.
Завдяки високій якості швів після лазерного різання, процес зварювання протікає легко, і конструкція виходить міцною і довговічною.