Зварювальні роботи в домашніх умовах.
Ручки-баранчики з пластика своїми руками
Давно хотів виготовити ручки-баранчики великого розміру, які завжди можуть стати в нагоді. Для зразка взяв ручку- "ромашку" від струбцин, які йшли в комплекті з циркулярною пилкою.
Хочу відразу показати результат.
Все обладнання робилося для одноразового або дуже рідкісного використання, тому виконано дуже просто, можна сказати, примітивно.
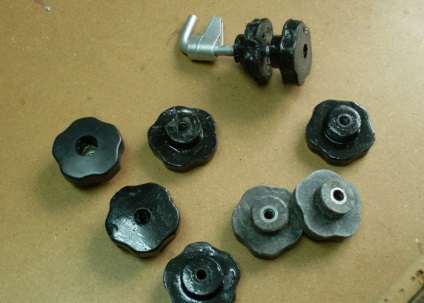
Для виготовлення прес-форми для лиття пластмаси і нагрівача потрібно зовсім небагато матеріалів і інструменту. Якщо немає зварювання, можна застосувати нарізні сполучення або придумати щось ще. Просто зі зварюванням швидше і зручніше.
Прес-форма для лиття пластмаси склеєна з рейок. При діаметрі ручки-зразка 54 мм, зовнішні розміри прес-форми вийшли 100х100 мм, ширина 16мм і висота 22 мм.
Відразу хочу сказати, що висоту прес-форми (товщину майбутньої заливки) треба брати більше. Товщина шару епоксидної смоли над верхньою частиною форми повинна бути не меее 10 мм.
У мене вона була всього 3-4 мм, тому після другої заливки частина "даху" зруйнувалася від сильного тиску.
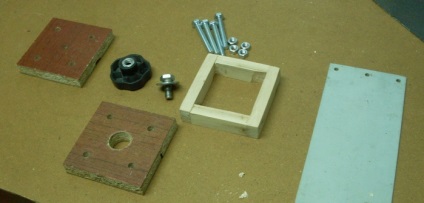
Ручка-модель має виступаючу частину, тому в центрі підстави з ДСП або фанери робимо отвір потрібного діаметру, а по кутах свердлимо отвори діам. 8 мм.
Збираємо конструкцію. Про всяк випадок між підставою і боковинами проклав два шари газети. Знизу закладаємо болти, накручуємо гайки так, щоб вони знаходилися приблизно на 10 мм від основи. Всю внутрішню частину, крім стінок, змащуємо будь-яким машинним маслом.
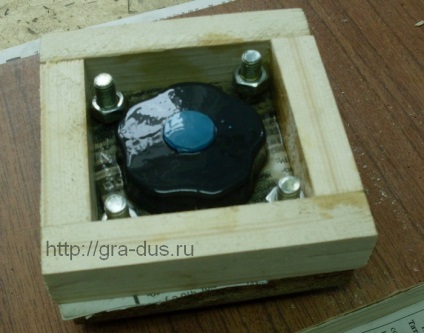
У центрі можна зміцнити трубочку або стрижень - майбутнє заливний отвір. Можна просвердлити його і після заливки. На фото видно, наскільки тонкий шар епоксидної смоли залитий, навіть пробка, що закриває отвір в центрі прес-моделі, просвічує. Треба лити шар товщі.
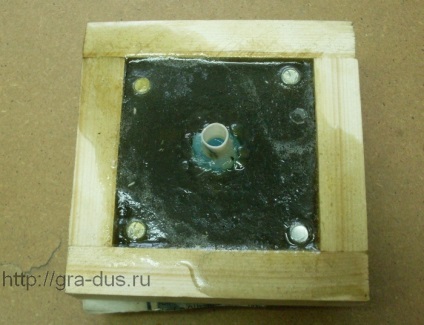
Пімерно через добу епоксидка затвердіє. Викручуємо болти, шліфуємо підставу. Має вийти приблизно так:
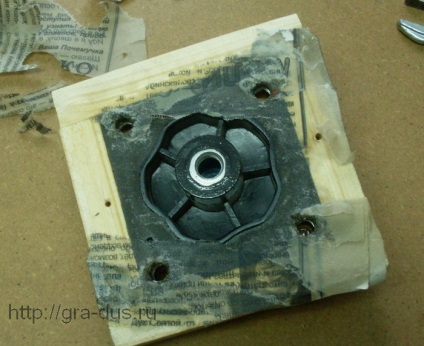
У вже готової прес-формі недалеко від заливного отвору необхідно просвердлити ще одне, діаметром 2-2,5 мм, для виходу повітря під час заливки пластика. У мене спочатку цього отвору зовсім не було.
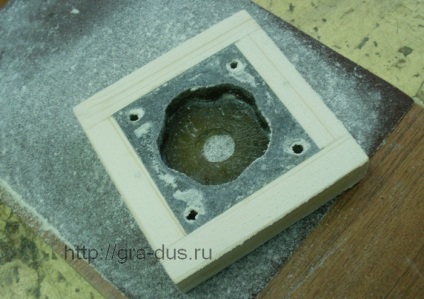
Виготовляємо другу частину форми. Зрозуміло, що в кутах сталевий пластини треба просвердлити збігаються отвори і приварити шайбу.
Поки затвердевал епоксидний клей в прес-формі, я почав виготовляти термопрес для заливки пластика. Ця штуковина схожа на звичайний насос для велосипеда. Використовувалися обрізки труб різного діаметру і підходять за розміром шайби.
Трубу можна взяти діаметром 30-35 мм, довжиною 300-350 мм. Поршень повинен щільно входити в трубу але не заклинювати. Краще нехай частина розігрітого пластику просочиться через поршень, ніж він заклинить під час нагнітання. Зіпсуєте заготовку.
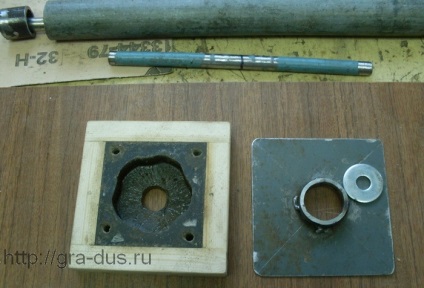
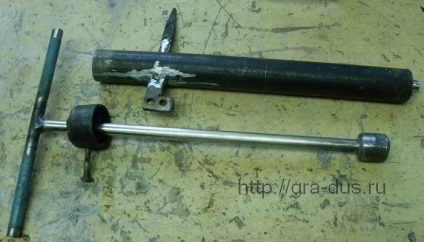
На загострений штир насаджується дерев'яна ручка, до Г-образної платівці прикручується ізолятор з склотекстоліти для кріплення висновків спіралі.
Ці деталі я приварив пізніше, а спочатку була просто труба, на одному кінці якої приварена шайба з внутрішнім діаметром 10 мм, для виходу рідкого пластику.
Перша ручка була відлита взагалі без електропідігріву. У трубу я засинав нарізаний дрібними шматочками пластик. Використовував те, що попалося під руку: шматки від розбитого пластикового відра, лопату для прибирання снігу та інше. Розігрівав на відкритому вогні.
Але це незручно. Пластик при перегріванні періодично запалюється і страшно смердить, труба гаряча і вся чорна від кіптяви, на руку доводиться надягати товсту рукавицю.
Але все-таки вийшло:
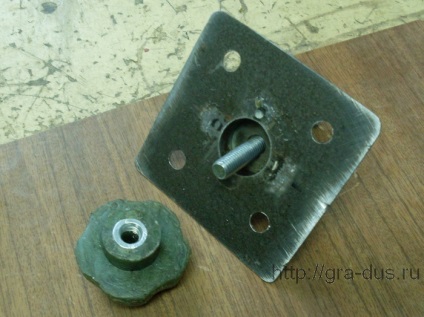
Через брак слюди обмотав трубу фторопластовой стрічкою. Витримує температуру приблизно 450 град. Нагрівач - спіраль від. сам не знаю, від чого. Може, праска, а може старовинна ел. плитка.
Розрізав на три рівні частини, витягнув, випростав, як міг. Трохи скрутив все жили між собою. Довжина спіралі вийшла приблизно 2,5 - 2,8 метра. Згодом зверху обмотав її чимось, схожим на скловату.
Машина не щоденного застосування, тому все спрощено. )
Ходові випробування. Напруга і струм видно на фото. Струм 4,5-5А, напруга близько 30 В. Джерело живлення - старого зарядного пристрою, напруга на виході регулюється. На мультиметри - температура всередині труби.
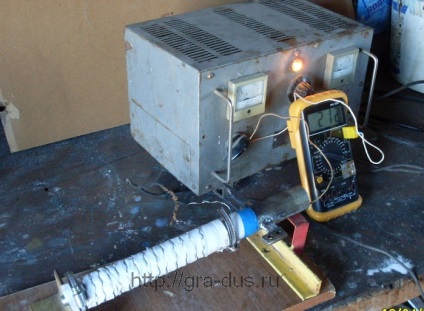
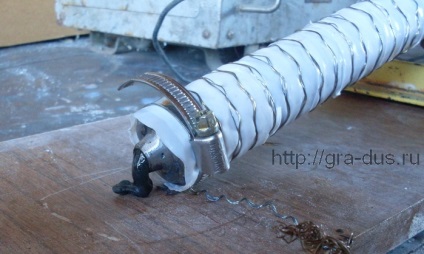
Фторопластова стрічка все-таки не витримала і місцями розплавилася, викликавши коротке замикання і отгоранія частини спіралі.
Намотав іншу. До речі, перед намотуванням нової спіралі її треба отжечь, пропустивши через неї хороший струм, або якимось іншим способом. Після відпалу вона стає м'якою, майже повністю розпрямляється і стає зручною для намотування.
В якості ізоляції застосував гіпсовий бинт з аптеки. Намотав на трубу два шари, потім спіраль і зверху знову кілька шарів гіпсового бинта.
Відлив кілька ручок. Бинт потемнів, але нічого не руйнується, не кришиться. З гіпсового бинта зробив і форму для відливання, але не відчував, так як ручок вже досить.
Так виглядає останній варіант термопистолета.
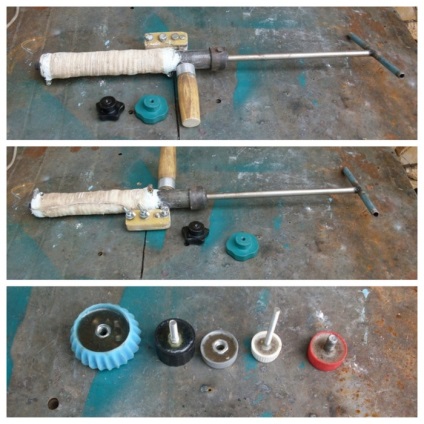
Ручки невеликих розмірів виготовляв, заливаючи епоксидною смолою болт або гайку в пробці відповідних розмірів (нижнє фото).
Лиття пластмаси в домашніх умовах цілком може виконати навіть той, хто не має ніякого досвіду. Основна складність - виготовлення якісної прес-форми.