Слідкуйте за нами в ВКонтакте. Facebook 'e і Twitter' e
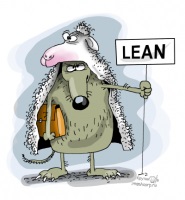
Лін (англ. Lean - пісний, стрункий). Концепція лин (бережливе виробництво, кайдзен) - система простих рішень, що дозволяють ліквідувати витрати і досягти лідерства в ефективності. Лін створена на основі виробничої системи компанії Toyota і за останні десятиліття збагачена досвідом лідерів світової промисловості.
Дотримання концепції лин дозволяє систематично діставати підвищений прибуток, забезпечуючи при цьому кращі на ринку якість, ціну і терміни. Результати, досягнуті завдяки системі бережливого виробництва, компанії утримують десятиліттями (як приклади, крім компанії Toyota, можна згадати таких світових лідерів, як Alcoa, Boeing, Bridgestone, Caterpillar, Ford, General Electric, Nissan, Scania, Xerox). У Росії вже сотні підприємств, в тому числі найбільші ( «АвтоВАЗ», «Газпром нафта», «Група ГАЗ», КамАЗ, «Русал», «Северсталь», УАЗ), стали будувати виробничі системи на основі бережливого виробництва. Однак концепція лин підходить не тільки великому бізнесу. Безліч невеликих підприємств з успіхом впроваджують цю технологію.
1. Непотрібні переміщення робочих
Втрати можуть виникати з таких причин, як:
• нераціональна організація робочих місць (незручне розташування верстатів і т. П.);
• зайві рухи робочого в пошуках необхідного інструменту, оснастки та т. П.
Як порахувати втрати? Проведіть хронометраж переміщень одного робочого протягом зміни. Порахуйте, скільки часу він витрачає на ходьбу до місця зберігання деталей і інструментів, їх пошук, помножте це час на кількість робочих в зміні і на число змін в році. Тепер Ви можете оцінити, які втрати несе Ваше підприємство від непотрібних переміщень робочих.
Приклад усунення втрат. На одній з дільниць підприємства автомобільної галузі інструмент зберігався в загальній шафі. Робочі на початку зміни брали один інструмент, а потім протягом дня міняли його на інший. В результаті оператори витрачали 10-15% часу на безглузді ходіння до шафи і назад. За кожним вирішили закріпити невеликі тумби для інструменту. В результаті переміщення були скорочені, а робоче місце стало більш зручним. Продуктивність праці зросла на 15%.
2. Безпідставна транспортування матеріалів
Йдеться про рух матеріалів, яка не додає цінності кінцевого продукту. Ось причини втрат:
• транспортування матеріалів між цехами, що знаходяться на значній відстані один від одного;
• неефективна планування виробничих приміщень.
Як порахувати втрати? Уявіть заготовку, що прийшла на склад матеріалів. Тепер подумки виконайте весь шлях, який вона проходить на всіх етапах технологічного процесу. Визначте, на скільки метрів її потрібно перемістити, скільки разів її піднімуть і поставлять, скільки ресурсів на це витрачається, скільки цінності при цьому додається і що втрачається (можливо, через переміщень погіршується якість заготовки). Тепер помножте втрати на кількість заготовок, які використовуються на виробництві протягом року.
Приклад усунення втрат. За технологією, прийнятою на одному автомобільному підприємстві, великогабаритну корпусні деталь двічі переміщали на зварювальний ділянку. Корпус зварювали, повертали на попередній ділянку для обробки поверхні, потім знову везли на зварювання (приварювали складальну одиницю) і знову транспортували на вихідне місце. Час витрачалося не тільки на переміщення деталі, але і на очікування навантажувача. Щоб скоротити втрати, було вирішено розмістити зварювальний пост в безпосередній близькості від ділянки механічної обробки і електровізки. Таким чином вдалося виключити транспортування компонента за допомогою автонавантажувача: з'їм і установка деталі, як і раніше, проводиться кран-балкою, а для переміщення корпусу використовують електровізок. Економія часу склала 409 хвилин на місяць, а це рівнозначно часу на виробництво двох корпусів.
3. Непотрібна обробка
Втрати цього виду виникають, якщо будь-які властивості товару виявляються марними для замовника. А саме:
• виготовляється продукція з непотрібними споживачу функціями;
• конструкція виробів необгрунтовано ускладнюється;
• використовується дорога упаковка товару.
Як порахувати втрати? Відвідайте замовника (покупця) і з'ясуйте, як він застосовує поставляється Вами продукцію. Якщо Ваша компанія, наприклад, виробляє деталі, поспостерігайте, як у споживача організований процес монтажу і пов'язані з ним операції. Вам потрібно зрозуміти, які властивості матеріалів або конструктивні елементи виробу він не використовує. Також поцікавтеся у замовника, які властивості продукції він вважає другорядними або зовсім непотрібними. Тепер оцініть, скільки ресурсів Ви щорічно витрачаєте на забезпечення цих непотрібних властивостей.
Приклад усунення втрат. На одному з підприємств, що займаються виробництвом автобусів, забарвлення всіх поверхонь (видних і невидних) проводилася по третьому класу точності. Після опитування споживачів з'ясувалося, що їм це не потрібно. Технічний процес був змінений: знизили клас точності при фарбуванні невидних поверхонь. Витрати скоротилися на сотні тисяч рублів на місяць.
Цей вид втрат викликаний простоєм працівників, машин або обладнання в очікуванні попередньої або наступної операції, матеріалів або інформації. Причини різні:
• перебої з постачанням сировини, напівфабрикатів;
• поломки обладнання;
• відсутність необхідних документів;
• очікування розпоряджень керівництва:
• неполадки з програмним забезпеченням.
Як порахувати втрати? Потрібно хронометрировать всі дії (або бездіяльність) персоналу, а також роботу (простий) обладнання протягом зміни. Порахуйте, яку частину часу простоювали робочі (через неготовність матеріалу, інструменту і т. П.) І наскільки довго залишалася бездіяльною обладнання (через поломки, переналагодження, низьку продуктивність). Тепер помножте час простою робочих і обладнання на кількість робочих, змін в році, одиниць обладнання. Це Ваші втрати.
Приклад усунення втрат. В одному з цехів підприємства з виробництва автомобілів обладнання підлягає простоювало без роботи через поломки. Час простою вдалося скоротити за рахунок організації пункту ремонту та обслуговування безпосередньо в цеху. Якщо верстат виходив з ладу, робочий звертався до ремонтникам і ті усували проблему негайно. Паралельно майстер подавав заявку головному механіку. В результаті простої устаткування і працівників скоротилися на 26 людино-годин на місяць.
5. Приховані втрати від перевиробництва
Це найнебезпечніший вид втрат, тому що веде втрати інших видів. Проте в багатьох компаніях виробляти більше, ніж потрібно замовнику, вважається нормою. Причини втрат від перевиробництва:
• планування повного завантаження устаткування і робочої сили;
• робота з великими партіями;
• виробництво обсягу продукції, що перевищує рівень попиту;
• виготовлення продукції, попит на яку відсутня;
• дублювання роботи.
Приклад усунення втрат. На підприємстві при плануванні виробництва запасних частин для автомобілів і автокомпонентів виходили з чисельності робітників і завантаження устаткування. Техніка працювала на межі можливостей, обсяги росли, але частина виробленого припадала пилом на складах. Вивчивши споживчий попит, а також прибуток від кожного виду продукції, керівництво прийшло до висновку, що вигідніше відмовитися від виробництва деяких товарів, а вивільнені ресурси використовувати для виготовлення деталей, що користуються попитом. В результаті компанії вдалося усунути втрати від перевиробництва і збільшити прибуток на десятки мільйонів рублів.
Надлишки з'являються, якщо сировина і матеріали закуповуються про запас. Через це на підприємстві виникають такі втрати:
• витрати на оренду складських площ;
• витрати на оплату праці співробітників складу;
• погіршення властивостей матеріалів внаслідок їх тривалого зберігання;
• незавершене виробництво.
Як порахувати втрати? Визначте, скільки у Вас зберігається запасів, які будуть затребувані не раніше ніж через тиждень, в яку суму обходиться їх зберігання, скільки на складі матеріалів, які вже не знадобляться в виробництві, і скільки там зіпсованих матеріалів. Тепер Ви можете визначити, які кошти заморожені і у що обійшлися зіпсовані матеріали.
Приклад усунення втрат. На підприємстві з виробництва автобусів незавершене виробництво становило 16 днів. На складальному ділянці одних комплектуючих було в надлишку, а інших постійно не вистачало. Після застосування методів лин вдалося організувати щоденну поставку комплектуючих на ділянку складання в необхідній кількості. В результаті виробництво готової продукції збільшилася, було отримано прибуток у кілька десятків мільйонів рублів, що дозволило закупити новітнє обладнання, збільшити зарплату робітників і поліпшити умови праці.
7. Дефекти та їх усунення
Втрати виникають через переробок продукції і усунення дефектів, що виникли в ході роботи.
Як порахувати втрати? Порахуйте, скільки бракованих виробів Ваша компанія виробляє в місяць, рік. У яку суму обходиться утилізація? Скільки ресурсів витрачається на переробку дефектної продукції? Пам'ятайте, що замовник ці витрати не несе, він платить Вам лише за придатні вироби.
Приклад усунення втрат. Відсоток дефектної продукції на підприємстві харчової галузі був надто великим: напівфабрикати для тортів не відповідали естетичним вимогам. Були вдосконалені процеси, застосовані методи контролю якості в ході виробництва: в разі неполадок спрацьовує пристрій оповіщення і процес зупиняється. Проблему тепер можна усунути негайно. В результаті кількість бракованих виробів було знижено на 80%.
Втрати творчого потенціалу
Виділяють восьмий вид втрат: незатребуваність ідей, пропозицій працівника, спрямованих на поліпшення діяльності компанії, а також його потенціалу. приклади:
• виконання кваліфікованим фахівцем рутинної роботи;
• неприйняття керівництвом пропонованих корисних змін;
• втрати часу, навичок, можливостей що-небудь удосконалити і набути досвіду через неуважне ставлення до співробітників (керівнику, наприклад, колись їх вислухати).
Показовим є приклад удосконалення, застосованого в зварювальному цеху одного з автозаводів. Молодий фахівець, який прийшов на виробництво, знайшов можливість поліпшити технологію: він запропонував використовувати для переміщення стапеля НЕ кран-балку, а повітряну подушку. Це дозволило б переносити стапель одному робітникові за набагато менший час. Новачок звернувся з ідеєю до майстра, але той не захотів слухати, сказав, щоб фахівець займався своєю справою і не пхав носа в чужі. Повторні звернення до майстра нічого не дали. Через кілька місяців директор заводу, обходив цех, підійшов до нового співробітника і поцікавився, чи є які-небудь труднощі, проблеми. Молода людина розповіла про пропозицію і про опір майстра. Директор дав добро на зміну технології. В результаті було отримано економічний ефект, що перевищував 1 млн руб. на рік.
Слідкуйте за нами в ВКонтакте. Facebook 'e і Twitter' e