Складання деталей під зварювання
Трудомісткість складання деталей під зварювання становить близько 30% від загальної трудомісткості виготовлення виробу. Для зменшення часу складання, а також для підвищення її точності застосовують різні пристосування.
Збірка під зварювання може виконуватися такими способами:
- повне складання вироби з усіх, хто входив в нього деталей з наступним зварюванням всіх швів;
- почергове приєднання деталей до вже звареної частини вироби-при неможливості застосування першого способу;
- попереднє складання вузлів, з яких складається виріб, з наступною збіркою і зварюванням вироби із зібраних вузлів; цей спосіб найбільш раціональний, він застосовується при виготовленні великих і складних конструкцій (суду, вагони, мости та ін.).
Для складання і зварювання колон, балок, стійок складного перетину, а також листових конструкцій зі сталі товщиною більше 8 мм застосовують пристосування, що допускають деяке переміщення елементів конструкції при усадки металу швів.
Пристосування можуть бути призначені тільки для зборки Деталей під зварювання або тільки для зварювання вже зібраних деталей.
Застосовують також і комбіновані складально-зварювальні пристосування.
Для складання листових конструкцій зручні електромагнітні стенди, які фіксують положення кромок зварювальних листів. На електромагнітних стендах може проводитися складання і зварювання листів товщиною до 15 мм. Недолік подібного роду пристосувань - негативний вплив магнітного поля на зварювальну дугу в процесі зварювання.
При масовому виготовленні однакових конструкцій застосовують спеціалізовані складальні кондуктори з механізмами для затиснення деталей. У цих кондукторів здійснюється складання та прихватка деталей, потім виріб звільняється з кондуктора і подається на майданчик або стенд для зварювання.
Перевірка точності збирання проводиться шаблонами і щупами.
Зібрані вузли або деталі з'єднують прихватками. Зварювальні прихватки представляють собою короткі шви з поперечним перерізом до 7% поперечного перерізу повного шва. Довжина прихватки від 20 до 100 мм в залежності від товщини зварювальних листів і довжини шва; відстань між прихватками в залежності від довжини швів - 500-1000 мм. Прихватки виконують тими ж електродами, що і зварювання вироби.
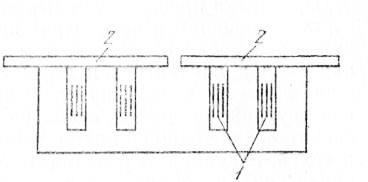
Мал. 1. Магнітний стенд: 1 - електромагніти, 2 - зварюються листи
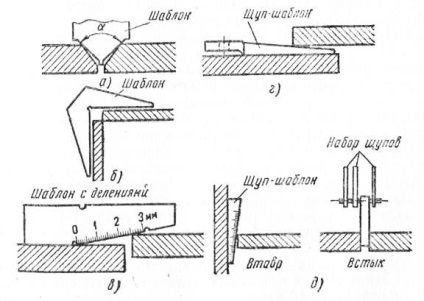
Мал. 2. Інструмент для перевірки якості збірки: а - кута розкриття кромки, б - прямого кута, в - зміщення листів, г -зазора між листами при зварюванні внахлестку, д - зазору при зварюванні втавр і встик
Прихватки перешкоджають переміщенню деталей, що може привести до тріщин в прихватках при охолодженні. Чим більше товщина зварювальних листів, тим більше розтягуються усадочная сила в прихватках і більше можливість утворення тріщин. Тому складання на зварювальних прихватках застосовують для конструкцій з листів невеликої товщини (до 6-8 мм). При значній товщині листів необхідно забезпечити податливість деталей, наприклад, здійснювати збірку на гребінках (еластичні прихватки) і збірку вироби з гнучкими деталями (гратчасті ферми, вузли судів з перегородками і ін.).