Винахід відноситься до галузі металургії, зокрема до способів виготовлення тонких листів з жароміцного псевдо-альфа-титанового сплаву. Запропоновано спосіб виготовлення тонких листів із злитка псевдо-альфа-титанового сплаву. Спосіб включає деформацію злитка сплаву Ti-6,5Al-2,5Sn-4Zr-1Nb-0,7Mo-0,15Si в сляб і його механічну обробку. Далі здійснюють нагрів до температури вище температури поліморфного перетворення (ТПП), деформацію і багатопрохідний прокатку на підкат з регламентованою сумарною ступенем деформації та ступенем деформації за прохід. Проводять збірку листів в пакет, прокатку пакета на готовий розмір і багатопрохідний прокатку з регламентованою сумарною деформацією пакету, витяг отриманих листів з пакета і їх ад'юстажную обробку. Отримують мікроструктуру листів, що забезпечує високий і рівномірний рівень міцності і пластичних властивостей. 1 табл. 1 мул.
Винахід відноситься до обробки металів тиском, а саме до способів виготовлення тонких листів з жароміцного псевдо-альфа-титанового сплаву Ti-6,5Al-2,5Sn-4Zr-1Nb-0,7Mo-0,15Si.
Завданням, на вирішення якої спрямовано винахід, є розробка способу виготовлення тонких листів з псевдо-альфа-титанового сплаву Ti-6,5Al-2,5Sn-4Zr-1Nb-0,7Mo-0,15Si, що дозволяє забезпечити отримання тонких листів, що володіють однорідною структурою і механічними властивостями, а також високою якістю поверхні і геометричних параметрів.
Технічним результатом, що досягається при здійсненні винаходу, є отримання мікроструктури листів, що забезпечує високий і рівномірний рівень міцності і пластичних властивостей.
Поставлена задача досягається тим, що в способі виготовлення тонких листів із злитка псевдо-альфа-титанового сплаву, відповідно до винаходу здійснюють деформацію злитка псевдо-альфа-титанового сплаву складу Ti-6,5Al-2,5Sn-4Zr-1Nb-0,7Mo- 0,15Si в сляб, механічну обробку сляба, нагрів до температури на 120 ÷ 200 ° с вище температури поліморфного перетворення (ТПП), деформацію з сумарною ступенем деформації 40 ÷ 80% з подальшим нагріванням до температури на 90 ÷ 150 ° с вище ТПП, деформацію з сумарною ступенем деформації 30 ÷ 60%, багатопрохідний прокатку на підкат з уммарной ступенем деформації 50 ÷ 80% і зі ступенем деформації за прохід 10 ÷ 20% і додатковим нагріванням після досягнення ступеня деформації 10 ÷ 30%, нагрів підкату до температури на 20 ÷ 40 ° С нижче ТПП і багатопрохідний прокатку з сумарною ступенем деформації 10 ÷ 30% і зі ступенем деформації за прохід 5 ÷ 20% з додатковим нагріванням після досягнення ступеня деформації 10 ÷ 30%, збірку листів в пакет з укладанням таким чином, щоб напрямок листів подальшої прокатки було перпендикулярно напрямку листів попередньої прокатки, прокатку пакета на готові й розмір з нагріванням до температури на 20 ÷ 120 ° С нижче ТПП і багатопрохідний прокатку з сумарною деформацією пакету 50 ÷ 85% і ступенем деформації за прохід 5 ÷ 15% з додатковим нагріванням пакета після досягнення ступеня деформації 15 ÷ 25%, витяг отриманих листів з пакету і їх ад'юстажную обробку.
Спосіб реалізується в такий спосіб.
Виплавлений і механічно оброблений злиток нагрівають до температури на 120 ÷ 200 ° С вище ТПП і піддають куванні зі ступенем деформації 40 ÷ 80%, що руйнує литу структуру, усереднює хімічний склад сплаву, ущільнює заготовку, усуваючи такі ливарні дефекти, як порожнечі, раковини і ін. температура нагріву нижче вказаної межі призводить до зниження пластичних характеристик, утруднення деформації і появи поверхневого розтріскування, температура нагріву вище вказаної межі викликає значне збільшення газонасичених го шару, що призводить до поверхневих надриву при деформації, погіршення якості поверхні металу і, відповідно до збільшеного видалення металу з поверхні заготовок. Наступна деформація заготовки зі ступенем 30 ÷ 60% після нагрівання на 90 ÷ 150 ° С вище ТПП дозволяє подрібнити розмір зерна по відношенню до вихідного стану. Для повного видалення поверхневих дефектів отриманий сляб механічно обробляють з усіх боків на глибину не менше 5 мм. Подальша багатопрохідний прокатка сляба на підкат зі ступенем 50 ÷ 80% після нагрівання до температури на 60 ÷ 80 ° С вище ТПП підвищує пластичність металу і обмежує утворення дефектів при подальшій деформації в (α + β) -області. Сляб прокатують зі ступенем деформації за прохід 10 ÷ 20%, і після досягнення ступеня деформації 1 ÷ 30% виробляють додатковий підігрів, що дозволяє поліпшити пластичність металу, зберігати в процесі прокатки задовільну якість поверхні і виключити утворення тріщин гуркоту. Після деформації в β-області здійснюють нагрів підкату до температури на 20 ÷ 40 ° С нижче ТПП і здійснюють багатопрохідний прокатку з сумарною деформацією 10 ÷ 30% і ступенем деформації за прохід 5 ÷ 20% для руйнування большеуглових кордонів зерен і збільшення щільності дислокацій, що дозволяє підготувати задану мікроструктуру для отримання механічних властивостей в поперечному напрямку, щоб при подальшій пакетної прокатки виробляти підготовку мікроструктури для отримання механічних властивостей переважно в поздовжньому напрямках і. Ступінь деформації за прохід 5 ÷ 15% визначається технологічними властивостями сплаву і умовами досягнення мінімальної різнотовщинності листової заготовки перед пакетної прокаткою. На даному етапі після досягнення ступеня деформації 10 ÷ 30% виробляють додатковий підігрів підкату, що дозволяє зберегти задовільну якість поверхні. При відсутності можливості застосування холодної прокатки для отримання тонких листів через низьку пластичності сплаву і високих навантажень на стан через високий опору деформації остаточне деформування листів на готовий розмір здійснюють пакетним способом, для чого підкат розрізають на мірні листові заготовки, при цьому листові заготовки укладають в пакет зі зміною напрямку прокатки таким чином, щоб напрямок подальшої прокатки було перпендикулярно напрямку попередньої прокатки. Зміна напрямку прокатки пакета дозволяє отримати оптимальну кристалографічну текстуру в листах і зменшити анизотропию механічних властивостей. Температурний інтервал нагріву і ступінь деформації на даному етапі дозволяє збільшити рівень подрібнення і коагулирования первинної α-фази, що сприяє отриманню равноосной дрібного мікрозерна, що забезпечує рівномірні показники механічних властивостей у всіх напрямках. Після пакетної прокатки отримані листи витягують з пакета і здійснюють ад'юстажную обробку, випробування листів і їх упаковку.
Промислова придатність підтверджується конкретним прикладом виконання винаходу.
Для отримання листів товщиною 1 мм були виплавлені злитки діаметром 190 мм і довжиною 260 мм. Хімічний склад сплаву наведено в табл.1. Температура поліморфного перетворення 1020 ° С.
Злитки піддавали куванні після нагрівання до 1180 ° С (на 160 ° С вище ТПП) зі ступенем деформації 65% Після чого заготовку нагрівали до температури 1140 ° С (на 120 ° С вище ТПП) і здійснювали деформування зі ступенем 55% на розміри 49 × 190 × 360 мм. Далі викуваний сляб стругали на розміри 39 × 180 × 350 і розрізали на кілька заготовок. Заготовки нагрівали до настановної температури 1090 ° С (на 70 ° С вище ТПП) і здійснювали прокат за 2 проходи зі ступенем деформації в кожному проході відповідно 10,3% і 9,6% на товщину 32 мм, після чого при досягненні загальної деформації за нагрів 18% підкат підігрівали при цій же настановної температури. Потім здійснювали прокатку в 2 проходу зі ступенями деформації 12,5% і 14,3% на товщину 24 мм, і при досягненні загальної деформації за нагрів 25%, повторно підігрівали при настановної температурі. Після чого виробляли прокатку зі ступенем деформації 16% на товщину підкату 19,5 мм. Сумарна ступінь деформації за етап склала 50%. Для поліпшення якості поверхні заготовки стругали на товщину 15 мм. Далі заготовки нагрівали до температури 990 ° С (на 30 ° С нижче ТПП) і виробляли прокатку в 2 проходу на товщину 11,5 мм зі ступенями деформації в кожному проході, відповідно, 13% і 11,5% і, після досягнення накопиченої деформації 24%, здійснювали подальший підігрів при цій же температурі. Потім здійснювали прокатку в 2 проходу на товщину 9 мм зі ступенями деформації в кожному проході, відповідно, 13% і 10% і, після досягнення накопиченої деформації 22%, здійснювали підігрів при цій же температурі. Після чого заготовки здійснювали прокат за 2 проходи на товщину 7 мм зі ступенем деформації в першому і в другому проході відповідно 11,5% і 12,5% і, після досягнення накопиченої деформації 22,2%, здійснювали підігрів при цій же температурі. Потім здійснювали прокат заготовки в 2 проходу на товщину 6 мм зі ступенем деформації в першому проході 9% і ступенем деформації в другому проході 8%, при цьому накопичена деформація за нагрів склала 15%. Після підігріву заготовки здійснювали прокат в два проходи на товщину 5,2 мм зі ступенем деформації 7% в кожному проході і здійснювали підігрів при досягненні накопиченої деформації 13,3%. Далі виробляли прокатку в два проходи на товщину 4,5 мм зі ступенем деформації 7,7% в першому проході і ступенем деформації 6,3% у другому проході. Потім підкат різали на мірні листові заготовки, проводили ад'юстажние операції і збирали пакети, при цьому листові заготовки укладали в пакет таким чином, щоб напрямок подальшої прокатки було перпендикулярно напрямку попередньої прокатки. У пакет укладали по 3 листові заготовки, з урахуванням верхньої і нижньої сталевих обкладок товщина пакета склала 40 мм. Далі здійснювали остаточний етап прокатки пакетним способом, для чого пакети нагрівали до температури 980 ° С (на 40 ° С нижче ТПП) і здійснювали прокат за 1 прохід на товщину 33 мм (ступінь деформації 17%). Потім здійснювали підігрів і прокатку за 2 проходи на товщину пакета 27 мм (ступінь деформації по проходах 9,1% і 10%, загальний рівень деформації 18,2%), після чого виробляли підігрів і прокатку пакета за 2 проходи на товщину пакета 22 мм (ступінь деформації по проходах 11,2% і 8,5%, загальний рівень деформації 18,5%), далі здійснювали підігрів і прокатка за 2 проходи на товщину пакета 18 мм (ступінь деформації по проходах 9,1% і 10%, загальна деформація 18,2%). Потім виконували двопрохідні прокатку на товщину 15 мм (ступінь деформації по проходах 9,5% і 8%, загальний рівень деформації 16,7%), далі виробляли підігрів і прокатку за 2 проходи на товщину 12 мм (ступінь деформації по проходах 10% і 11,2%, загальний рівень деформації 20%). Після чого заготовки підігрівали і здійснювали прокат за 2 проходи на товщину пакета 10 мм (ступінь деформації по проходах 8,4% і 9,1%, загальний рівень деформації 16,7%), виробляли підігрів і прокатку за 2 проходи на товщину пакета 8, 4 мм (ступінь деформації по проходах 10% і 11,2%, загальний рівень деформації 20%). Сумарна ступінь деформації пакета за етап склала 79%. Потім здійснювали розбирання пакетів, в результаті чого були отримані листи розмірами 1,0 ÷ 1,1 × 200 ÷ 210 × 650 ÷ 700 мм. На отриманих листах виробляли ад'юстажную обробку, різання на готовий розмір, відбір зразків та випробування механічних властивостей і дослідження структури. Результати випробувань механічних властивостей листів в стані поставки і після термічної обробки, проведеної на зразках, приведені в табл.2, зображення мікроструктури листів представлені на фіг.1. Якість поверхні листів відповідало всім вимогам нормативної документації, тріщин і розшарувань не зафіксовано.
формула винаходу
Спосіб виготовлення тонких листів із злитка псевдо-альфа-титанового сплаву, який відрізняється тим, що здійснюють деформацію злитка псевдо-альфа-титанового сплаву складу Ti-6,5Al-2,5Sn-4Zr-1Nb-0,7Mo-0,15Si в сляб , механічну обробку сляба, нагрів до температури на 120-200 ° с вище температури поліморфного перетворення (ТПП), деформацію з сумарною ступенем деформації 40-80% з наступним нагріванням до температури на 90-150 ° с вище ТПП, деформацію з сумарною ступенем деформації 30-60%, багатопрохідний прокатку на підкат з сумарною ступенем деформації 50-80% і з ступінь ю деформації за прохід 10-20% і додатковим нагріванням після досягнення ступеня деформації 10-30%, нагрів підкату до температури на 20-40 ° С нижче ТПП і багатопрохідний прокатку з сумарною ступенем деформації 10-30% і зі ступенем деформації за прохід 5 -20% з додатковим нагріванням після досягнення ступеня деформації 10-30%, збірку листів в пакет з укладанням таким чином, щоб напрямок листів подальшої прокатки було перпендикулярно напрямку листів попередньої прокатки, прокатку пакета на готовий розмір з нагріванням до температури на 20-120 ° З нижче Т П і багатопрохідний прокатку з сумарною деформацією пакету 50-85% і ступенем деформації за прохід 5-15% з додатковим нагріванням пакета після досягнення ступеня деформації 15-25%, витяг отриманих листів з пакета і їх ад'юстажную обробку.
Статистика сайту
Всього документів: 589492
Ви можете безкоштовно розмістити інформацію про свій винахід на нашому сайті. Це допоможе потенційним інвесторам дізнатися про вас і зв'язатися з вами.
Хотіли б ви завести сайт-візитку з окремим піддоменом на сайті Банкпатентов.ру?
Так, ця послуга мені цікава
Ні, мене це не цікавить
Всього голосів: 1 593
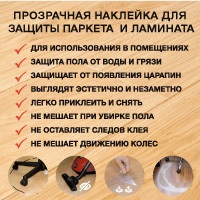