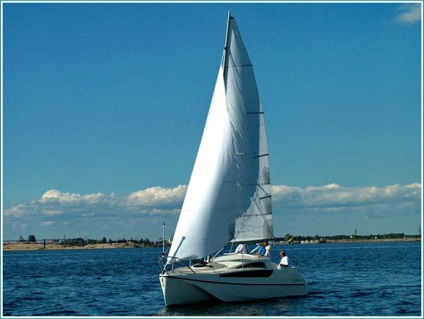
Наповнювачі сьогодні - одні з найважливіших компонентів композитних конструкцій. У яхтобудування їх призначення зводиться в основному до збільшення товщини виклеюють ламінату при одночасному зниженні його маси. В якості додаткових бонусів поліпшені шумо- і теплоізоляція, а також підвищена жорсткість корпусу. Мінуси, правда, теж є: крім збільшення трудомісткості виробництва, наявність сендвіча з двох різнорідних матеріалів з різними модулями упргості і рівнями адгезії до смолі може привести до розшарування (деламінаціі) пластика в процесі експлуатації, вкрай важко піддається ремонту.
До деламінаціі (крім дефектів виготовлення) призводить в першу чергу інший механізм деформації сендвічеве пластика при впливі на нього сильних зосереджених (ударних) впливів. З одного боку, при значній деформації внаслідок сильного удару наповнювач сендвічеве корпусу сприймає на себе частину поперечних навантажень, розвантажуючи зовнішній шар пластику, при цьому внутрішній шар починає працювати на розтягування, що вельми сприятливо для склотканини (і особливо для вуглетканини).
З іншого боку, сильні дотичні напруження, що виникають на кордоні «пластик-наповнювач», призводять до того, що пластикові поверхні сендвічеве корпусу можуть зрушити щодо наповнювача (що супроводжується, природно, розривом клейового шару і втратою загальної цілісності конструкції), хоча зовні на корпусі може не бути абсолютно ніяких дефектів.
Сьогодні застосовуються в основному чотири види наповнювачів: це дерево, полістиролу, що матеріали, пінопласти і стільникові конструкції. Останнім часом популярність також стали набирати синтетичні матеріали, що мають у своїй структурі воздухонаполненнимі мікрокапсули або інші повітряні обсяги і проміжки. У кожного з них - свої достоїнства і недоліки.
Дерево - традиційний наповнювач, що застосовується в пластиковому суднобудуванні з давніх-давен.
Це перш за все бальса, середня щільність якої у висушеному стані коливається від 120 до 150 кг / м. що приблизно в півтора рази легше пробки (і в 3-4 рази - багатьох порід дерева, які ростуть в Росії). Набагато рідше, ніж бальса, застосовується морська фанера; інші ж варіанти дерев'яних наповнювачів не витримали перевірки часом і практично вийшли з ужитку. Переваги дерева цілком очевидні: відносно невисока ціна, простота обробки, хороша доступність.
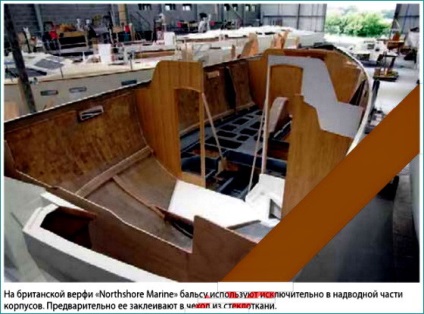
Мінусів, проте, теж чимало. І якщо з схильністю бальси гниття вдалося (або майже вдалося) впоратися спеціальними просоченнями, то інші недоліки дерева поки виглядають трудноустранімимі. Фанеру практично неможливо застосовувати в криволінійних поверхнях (в силу чого її вживання обмежується майже виключно палубами і перегородками), бальса ж дуже сильно вбирає в себе смолу, що збільшує вагу готового композиту і підвищує ризик недостатнього насичення смолою прилеглих до наповнювача шарів тканини.
Щоб уникнути цього, шматки бальсового наповнювача часто заздалегідь монтують на аркуші щільного склотканини, потім обклеюють їх тканиною зовні і вклеюють в ламінований корпус, що збільшує як трудомісткість роботи, так і ризик подальшої деламінаціі. Крім того, бальса (як і практично будь-який інший продукт природного походження) є негомогенних матеріалом, властивості і характеристики якого можуть помітно відрізнятися від зразка до зразка, в зв'язку з чим ряд фірм (особливо при будівництві одиничних зразків яхт) намагаються заздалегідь підбирати бальса по щільності . Ще один недолік дерева - анизотропность, що виражається в розходженні його властивостей в залежності від орієнтації волокон.
Незважаючи на це, ряд відомих фірм (наприклад, «Conyplex») вважає бальса найкращим матеріалом для наповнювача корпусів сучасних пластикових яхт - в чималому ступені через близькість модуля пружності цього дерева до склопластику (що покращує їх спільну роботу) і відмінною міцності на стиск. Тепло- та шумоізолюючі властивості бальси помітно поступаються цим характеристикам сучасних пінопластів. Останнім часом з'явилися композитні наповнювачі на основі бальсового дерева (наприклад, ProBalsa), що мають як високу стабільність, так і поліпшені фізико - механічні якості.
Вспенивающем матеріали (в основному на основі поліуретану), незважаючи на періодично повторювані спроби їх застосування, так і не змогли знайти гідне місце у виготовленні власне склопластикових конструкцій. Їх застосовують більш-менш широко при заливці глухих таранних відсіків, обсягів плавучості (в основному на малих судах), теплоізоляції бойлерів і на інших тому подібних локальних ділянках.
Пінопласти сьогодні є, мабуть, першими за популярністю і значущості наповнювачами. Ринок пропонує дуже велику їх кількість найрізноманітнішої щільності. Однак відразу ж треба зауважити, що переважна більшість сучасних пінопластів, що мають щільність рівну бальса (або нижчу), істотно поступаються їй за характеристиками міцності, особливо по ударної міцності. Основна частка конструкційних пінопластів - це композиції на основі ПВХ з закритими порами, що мають мінімальний рівень водопоглинання і відмінні ізоляційні характеристики.
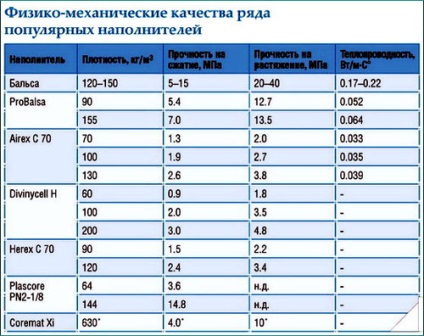
Пінопласти не гниють, багато хто з них мають хорошу вогнестійкість (або не підтримують горіння, або не горять зовсім), їх основні властивості високостабільного від партії до партії. Деякі марки наповнювачів можуть легко згинатися в підігрітому стані, що зручно при викладенні листів пінопласту по криволінійних поверхонь.
Широкому поширенню пінопластів сприяла можливість передовий хімічної індустрії випускати такі матеріали з різними, заздалегідь заданими властивостями. На сучасному ринку нескладно знайти і надлегкі пінопласти, і пінопласти, що володіють підвищеною міцністю на стиснення (що необхідно при використанні вакуумних технологій формування), недавно з'явилися і спецпенопласти, розраховані для «запікання» корпусів в печі.
Проблемами тут до недавнього часу було те, що більшість ПВХ-композицій, по-перше, починають плавитися при порівняно невеликому підвищенні температури, по-друге, мають дуже високий коефіцієнт теплового об'ємного розширення. Це призводить після «запікання» до викривлення корпусу і появи в ньому великих внутрішніх напружень. Порівняно недавно ці проблеми хіміками-технологами були усунені.
На жаль, обсяг даної статті не дозволяє хоча б коротко розглянути весь той найширший перелік пропонованих сьогодні пористих ПВХ-матеріалів, використовуваних в пластиковому суднобудуванні, і до цієї теми ми ще повернемося в окремій статті. Стільникові наповнювачі, що представляють собою вертикально орієнтовані шестикутні стільники з тонкого і міцного матеріалу, закріпленого між двома клейкими поверхнями, застосовуються майже виключно для створення екстремальних спортивних яхт.
Зараз існують наступні варіанти таких конструкцій: з сотами з поліпропілену (виключно легкого пластика) або полікарбонату (досить міцного матеріалу), з номексу або кевлара (при всій своїй хімічній подібності два цих матеріалу досить помітно відрізняються за властивостями і ціною), з металу (щодо поширений лише варіант з алюмінієвими сотами, нержавіючі і титанові різновиди - поки сувора екзотика, яка трапляється лише в авіакосмічній промисловості).
Поліпропіленові стільники в яхтобудування поки майже не застосовуються: мала міцність цього матеріалу дає йому шанс на використання лише при виготовленні деталей меблів або ненавантажених перегородок - там, де потрібна певна товщина, а не особливо висока міцність.
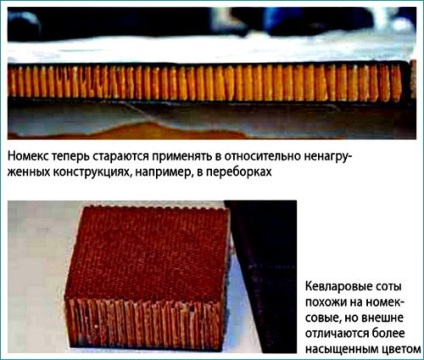
Стільники з номексу широко поширені при будівництві екстремальних многокорпусніков, але недавні численні аварії сильно підірвали реноме цього матеріалу, в силу чого погляди конструкторів звернулися до кевларовим стільниках (наприклад, типу Plascore PN2), які набагато міцніше, але, на жаль, багато дорожче. Алюмінієві стільникові конструкції в яхтобудування поки - дуже велика рідкість.
Навскидку вдається згадати тільки одне судно, побудоване з їх використанням - рекордний катамаран Стіва Фоссета «Playstation / Cheyenne». Матеріал, однак, виявився небезпроблемного: за свідченням учасників кругосвітнього плавання, підводні поверхні корпусів, накопичивши всередині стільникових поверхонь величезний заряд статичної електрики, фактично перетворилися на гігантський конденсатор, в один прекрасний момент розрядився і «погасив» всю бортову електроніку.
Сьогодні застосування алюмінієвих сот в яхтобудування, на думку ряду фахівців, виправдано лише при виготовленні перегородок.
Ще один недолік стільникових конструкцій - їх погана стійкість до пікових ударних навантажень, сконцентрованим на малій площі. У цій ситуації втрата стійкості частині сот, яка веде до різкого падіння несучої здатності матеріалу - дуже частий сценарій. В силу цього в місцях основного зосередження ударних навантажень (райони форштевня / носової скули / днища поблизу кормовій частині) стільники намагаються замінювати суцільним матеріалом типу бальси або пінопластів.
Новітні матеріали з повітряними капсулами або обсягами всередині широко представлені дуже популярним в Росії наповнювачем Polycore (ще відомий під назвою Coremat), що представляє собою нетканий поліефірний матеріал з повітряними мікробаллонамі. Інші матеріали подібного роду (наприклад, «тривимірна» склотканина Parabeam 3D, «Кия» № 201) лише починають знаходити своє застосування в суднобудуванні. Наповнювачі типу Polycore / Сoremat порівняно дешеві, дуже технологічні і прості в обробці, що забезпечило їм популярність, в першу чергу серед виробників масових човнів.
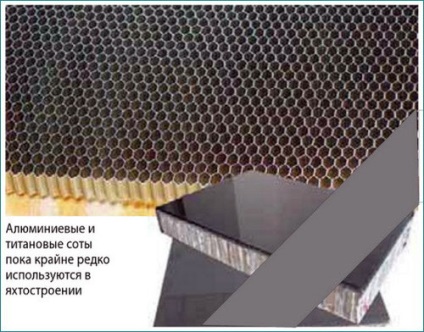
Їх головною відмінністю від більшості раніше розглянутих наповнювачів є те, що вони, будучи пронизані сіткою майже капілярних отворів, просочуються смолою одночасно зі склотканиною, утворюючи практично єдиний з останньої композит, практично не схильний до розшарування (деламінаціі). Ця обставина, без сумніву, виглядає величезним плюсом в очах всіх виробників. Недолік таких матеріалів - досить висока маса виходить (після повного просочення смолою) композиту. Подібні наповнювачі сумісні з усіма типами існуючих смол, але непридатні для роботи з Препреги і в інфузійних процесах.
Поступовий розвиток технологій дозволило привнести в пластикове суднобудування важливе нововведення - технологію укладання скловолокна шляхом напилення (зауважимо, що прімерноо 40 років тому на цей метод покладалися дуже великі надії). Сам метод полягає в подачі через спеціальний пістолет-розпилювач смоли, перемішаної з затверджувачем, укупі з відрізками односпрямованого скловолокна (подається довгий джгут волокна нарізається безпосередньо перед розпиленням на відрізки рівної довжини). З такого пістолета робочий «запилюють» форму, наповнюючи її смолою з відрізками волокна і, на жаль, з численними бульбашками повітря.
В силу останнього механічні якості готового виробу невисокі і сильно поступаються виробам, відформованим з використанням інших технологій. Відсутність довгих цільних «від краю до краю» вироби скловолокна теж не сприяє високій загальній міцності виходить продукту: в ньому немає єдиної цілісної структури, яка забезпечується стеклотканью. Як наслідок, в силу все більш і більш зростаючих вимог до міцності якостям яхт (і до найбільш вигідному співвідношенню «маса / міцність») цей метод формування практично повністю сьогодні вийшов з ужитку, так як його єдиним, по суті, перевагою є лише економія часу .
Втім, часом його застосовують при виготовленні корпусів невеликих човнів або окремих некритичних елементів конструкції. Зауважимо, що деякі відомі в нашій країні яхти, споруджений у 70-х рр. минулого століття (наприклад, польська «Carina») виклеювати саме цим способом. Найбільш же технологічно витонченими і якісними з точки зору отриманих результатів сьогодні є три способи формування пластикових корпусів: з препрегів, вакуумними і інжекційними методами (їх кілька) і в закритій матриці (найскладніший з них).
Артур Гороховський.
Джерело: «Катери і Яхти», №218.