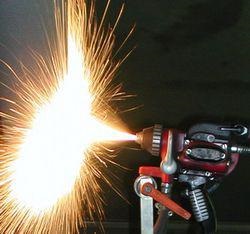
Газотермічне напилення - це комплекс сучасних, добре відпрацьованих методів нанесення функціональних, відновлювальних і декоративних покриттів з найширшого спектру матеріалів.
Область їх застосування надзвичайно широка - від реактивних двигунів і колінчастих валів до медичних імплантантів і ободів велосипедних коліс.
Під газотермічним напиленням (Thermal Spray Coating) розуміють сукупність процесів, при яких напилюваний матеріал розплавляється, диспергується (розпорошується) і переноситься на оброблювану поверхню за допомогою газового струменя. При ударі об поверхню, частка напилюваного матеріалу миттєво охолоджується (швидкості охолодження можуть сягати мільйона градусів в секунду) і деформується, щільно зчеплені з нею. Через це, газотермічні покриття мають стрічкову або планарную ультрадрібнозернистих мікроструктуру. Покриття також може містити пори, а в разі напилення металів - частинки їх оксидів і нітридів.
Напилювана можуть як метали і сплави, так і неметалеві сполуки, карбіди, оксиди, скла, кераміки і полімери, а також композиційні матеріали. В принципі, таким способом можна напилити будь-який матеріал, який не розкладається при нагріванні до температури плавлення. У ролі підкладки можуть виступати метали, кераміки, деревина або пластмаси.
Нанесення газотермических покриттів практикується в промисловості близько 100 років, проте за останні 20 років в даній області відбулися істотні зміни, які висунули ці технології на новий рівень можливостей. Подібні зміни були викликані удосконаленням технологічного обладнання і технології виробництва вихідних матеріалів для напилення, впровадженням новітніх систем автоматизації та контролю якості.
Винахідником газотермического методу напилення був Макс Ульріх Шооп. Розпорошуючи свинець за допомогою стаціонарної тигельної установки, він отримував покриття на різних матеріалах. На основі його технології в Цюріху в 1909 р був відкритий завод з металізації. У 1913 р Ульріх Шооп удосконалив і запатентував конструкцію газопламенного розпилювача, де матеріал для розпилення подавався в полум'я газового пальника у вигляді дроту. Щільність покриттів, отриманих Шоопом становила 85-90% щільності компактного матеріалу. У 1918 р він з співробітниками розробив електродугової розпилювач, що дозволяє ефективно наносити покриття з металу. Метод нанесення покриттів через розпорошення стали назвали по імені винахідника технології шоопирования. У 1921 р Ульріх Шооп запатентував технологію металлопорошкових газопламенного розпилення.
Процеси газотермічного напилення прийнято класифікувати за природою джерела теплової енергії (див. Рис.) В установках газопламенного, високошвидкісного і детонаційного напилення, джерелом енергії є тепло, що виділяється при хімічній реакції горіння паливного газу. У процесах електродугового і плазмового напилення, джерелом енергії є електрична дуга. Розглянемо докладніше кожен з методів газотермічного напилення.
Газоплазмове напилення (Combustion Flame Spraying)
Газополум'яне напилення здійснюється за допомогою спеціального пальника, в яку вдувається повітря (або кисень) і горючий газ (ацетилен, пропан, водень або ін.) У зону горіння подається напилюваний матеріал, який розплавляється полум'ям пальника, розпорошується і переноситься газовим струменем на оброблювану поверхню. Процеси газопламенного напилення створюють покриття з відносно високою пористістю (5-12%) і невисокою адгезією до підкладки. Це обумовлено малою швидкістю газового струменя (близько 50 м / с). Температура полум'я обмежує спектр матеріалів, які можуть бути розпорошені газополуменевим способом.
Напилюваний матеріал може подаватися в розпилювач у вигляді стрижня, дроту, порошку або шнура. Металеві матеріали, як правило, використовуються у вигляді гнучких дротів, що дуже зручно і забезпечує безперервність процесу. Керамічні матеріали - у вигляді порошків або спеціальних спечених прутків. Істотним недоліком при використанні прутків є порушення безперервності процесу.
При використанні для напилення багатокомпонентних порошків, можливе порушення однорідності властивостей покриття, викликане сегрегацією (розшаруванням) порошків. Дана проблема усувається використанням гнучких шнурових матеріалів, що складаються з того ж порошку, що утримується гнучкою зв'язкою. При розпилюванні матеріал зв'язки повністю випаровується і на підкладку осідає тільки матеріал порошку.
Основними достоїнствами газопламенного напилення. що забезпечили йому широке поширення, є простота і надійність обладнання, а також мобільність. Даний метод може використовуватися в польових умовах (на трасі). Технології газопламенного напилення з успіхом застосовуються для ремонту і відновлення геометрії деталей, які не зазнають серйозних навантажень.
Плазмового напилення (Plasma Spraying)
При даному способі напилення, джерелом енергії є електрична дуга, підпалювали між двома електродами. Через область горіння дуги продувається інертний газ (як правило, аргон з добавками азоту або водню), який іонізується і утворює плазму. Температура плазми в області дуги досягає 15000 ° С. В струмінь плазми подається порошок напилюваного матеріалу, який розплавляється і переноситься на оброблювану поверхню. Незважаючи на високі температури в зоні горіння дуги, що обробляється поверхня не відчуває сильного нагріву, так як при виході з області дуги температура різко падає.
Плазмовим напиленням отримують покриття з нікелевих і залізних сплавів, карбідів, нітридів, боридів. Надзвичайно висока температура плазми дозволяє напилюють даними способом вогнетривкі кераміки, що містять оксиди алюмінію і цирконію, і інші тугоплавкі матеріали, що не піддаються розпорошення іншими способами.
До переваг плазмового розпилення відносяться також гнучкість, можливість регулювання фізико-механічних властивостей одержуваного покриття і універсальність, що дозволяє напилюють практично будь-які матеріали та їх поєднання, в тому числі і отримувати багатошарові композиційні покриття.
Устаткування для плазмового напилення складніше, ніж для газопламенного, так як включає в себе газову і електроапаратуру.
В даний час інтенсивно досліджуються і розробляються нові методи плазмового напилення. В особливо відповідальних випадках для досягнення високої адгезії і щільності покриттів, плазмовий процес проводять у вакуумній камері при зниженому тиску або в атмосфері інертного газу. Зменшення тиску призводить до збільшення швидкості частинок, що дозволяє отримувати більш щільні покриття. Проведення процесу в атмосфері інертного газу виключає взаємодію розпорошується матеріалу з киснем, що дає можливість напилювати хімічно активні матеріали, наприклад, дисилицида молібдену, інтерметалліді. Такі покриття можуть володіти високою твердістю і хімічну стійкість при підвищених температурах.
Ще однією перспективною модифікацією плазмового методу є процес, при якому струмінь напилюваного матеріалу оточується струменем інертного газу з метою виключення взаємодії напилюються частинок з киснем. Переваги даного методу ті ж, що і при проведенні процесу в інертному атмосфері.
Детонаційне напилення (Detonation Gun, D-Gun)
Установка для детонаційного напилювання нагадує кулемет, що стріляє порціями розігрітого порошку. У замкнуту камеру згоряння, до якої прикріпляється стовбур, подається суміш кисню і пального газу, стовбур направляють на Напилювана поверхню. Через завантажувальний отвір в камеру подається порошок. Суміш підпалюється електричною іскрою і вибухає. Розпечені частинки разом з продуктами згорання вилітають на оброблювану поверхню. Температура частинок в момент удару досягає 4000 ° С. Частота пострілів - 3-4 в секунду.
Через високу швидкість вильоту частинок, покриття, отримані детонаційними напиленням. мають високу міцність, твердість і зносостійкість. Детонаційними напиленням створюють покриття з металокераміки: карбідів вольфраму, титану і кобальту, нітридів титану і бору, окису алюмінію.
Недоліком методу є неоднорідність одержуваного покриття і складність технологічного обладнання.
Високошвидкісне напилення (High Velocity Oxygen Fuel, HVOF)
Технології високошвидкісного напилення по праву вважаються найбільш сучасними газотермічним методами.
Принципово, методи HVOF нічим не відрізняються від газополуменевих, однак, завдяки особливостям конструкції пальника, в них досягаються дуже високі швидкості розпилення.
Існують різноманітні реалізації ідеї високошвидкісного напилення. Наприклад, один з варіантів включає камеру згоряння і довге циліндричне сопло, охолоджувані водою. У камеру під високим тиском вдуваються кисень і горючий газ. Строго по осі пальника подається порошок напилюваного матеріалу. Суміш розплавлених частинок порошку і продуктів згоряння газів, проходячи через сопло, розганяється до надзвукової швидкості і вилітає в напрямку підкладки. У систем HVOF першого покоління, тиск в камері згоряння становило 0,3-0,5 МПа, швидкість вильоту частинок досягала 450 м / с. Для подальшого прискорення вилітають частинок, тиск в камері підвищують до 1-1,5 МПа, в конструкцію гармати вводять сопло Лаваля. Швидкості вильоту частинок при цьому перевищують 1000 м / с.
Покриття, отримані високошвидкісним методом характеризуються значеннями щільності, що досягають 99% щільності компактного матеріалу, і низьким рівнем залишкових напруг. Оскільки наявність останніх є головним чинником, що обмежує товщину покриття, HVOF-напилення дозволяє отримувати покриття значно більшої товщини в порівнянні з газополуменевим напиленням. За експлуатаційними характеристиками високошвидкісні покриття перевершують покриття, отримані детонаційними напиленням. У ряді програм, процеси HVOF поступово витісняють плазмового напилення.
З огляду на те, що падаючі частинки мають дуже велику кінетичну енергію, для формування високоякісних покриттів не требуетсяО розплавлення, що робить цей процес єдино прийнятним в ряді випадків, наприклад, при напиленні металокераміки.
Технології HVOF-напилення є неперевершеними для відновлення і продовження ресурсів деталей, що зазнають високий корозійно-ерозійний знос, кавітацію, завдяки високій щільності і зносостійкості одержуваних покриттів.
У розвинених країнах, високошвидкісне напилення практично повністю витіснило методи вакуумного напилення і дозволило відмовитися від вкрай неекологічних гальванічних покриттів.
Електродугове напилення (Arc Spraying)
Електродугове напилення - один з найбільш економічних методів напилення покриттів, що характеризується низьким енергоспоживанням і високими швидкостями напилення. Джерелом нагріву, як і в разі плазмового напилення, є електрична дуга. В даному випадку, дуга запалюється між двома дротами з напилюваного матеріалу, які подаються в зону розпилення з постійною скоростью.Температура в зоні дуги може перевищувати 5000 ° С. Диспергирование розплавленого матеріалу і доставка його на оброблювану поверхню виробляється струменем стисненого газу, як правило - повітря.
Так як напилюваний матеріал виступає в ролі електрода, цим методом можна розпорошувати тільки електропровідні матеріали (метали і сплави), тому його іноді називають електродугової металізацією.
Перевагами електродугового напилення є його простота, економічність і висока продуктивність (до 45 кг / год).
Цей процес широко використовується для напилення антикорозійних цинкових і алюмінієвих покриттів, застосовуваних у суднобудуванні, інфраструктурі міст, обладнанні сільськогосподарських підприємств.
Існують також сучасні електродугові гармати, що працюють в інертних атмосферах і використовують в якості розпилювального газу азот або аргон. У цих установках отримують покриття з активних металів, таких як титан і цирконій, для антикорозійного захисту в хімічній промисловості.
Велике значення при нанесенні будь-яких типів газотермических покриттів має попередня обробка напиляемой поверхні, що включає операції мийки, знежирення і абразивної струменевої обробки. Попередня обробка впливає на міцність зчеплення напилюваного покриття з підкладкою. У ряді випадків, газотермічні покриття після напилення піддають додатковій обробці - оплавлення, механічної або фізико-хімічної обробки та ін. Що дозволяє поліпшити адгезію і експлуатаційні характеристики вироби. Хороші результати дає застосування газотермічних покриттів поверх основних наплавлених шарів, що мають, як правило, грубий поверхневий рельєф.
Процеси газотермічного напилення набули широкого поширення завдяки ряду істотних переваг в порівнянні з іншими методами нанесення покриттів. До них відносяться:
- можливість нанесення покриттів на об'єкти практично будь-яких розмірів і форм;
- найширший спектр напилюються матеріалів і підкладок;
- нанесення газотермічних покриттів не викликає значного розігріву оброблюваних поверхонь;
- відсутні температурні деформації напилюються деталей;
- відсутність структурних змін в матеріалі оброблюваної деталі;
- висока економічна ефективність і екологічність.
Безумовно, описані процеси слід віднести до ресурсозберігаючих, оскільки вони продовжують термін експлуатації обладнання, дозволяють відновлювати зношені вузли, а не заміняти їх новими. Застосування функціональних покриттів дає можливість економити дорогі матеріали, виготовляючи основний обсяг деталі з більш дешевого металу. Впровадження у виробництво сучасних автоматизованих процесів газотермічного напилення дозволяє випускати продукцію з високими експлуатаційними властивостями, що відповідають вимогам сучасних технологій.